Magnesium hydroxide is white amorphous powder or colorless hexagonal column crystal. It is soluble in dilute acid and ammonium salt solution, almost insoluble in water and alcohol. Easily absorb carbon dioxide in humid environment. Becomes hexagonal crystal system crystallization when heated above 200℃ in alkaline solution. Decomposed into magnesium oxide and water at 230℃. Above 500℃, it loses water and transforms into magnesium oxide. The aqueous solution is alkaline, pH 9.5~10.5.
As an inorganic weak alkali product, magnesium hydroxide is called “green neutralizer”, “environmentally friendly flame retardant” and “the third alkali” because of its strong buffering properties, high activity and adsorption capacity, as well as non-corrosive, non-toxic, harmless and many other unique properties. Therefore, it is called “green neutralizer”, “environmentally friendly flame retardant” and “the third kind of alkali”, and it is one of the favored and respected products in the process of implementing sustainable development strategy, protecting the environment and beneficial ecological development.
The process of preparing magnesium hydroxide from dolomite mainly includes the following methods:
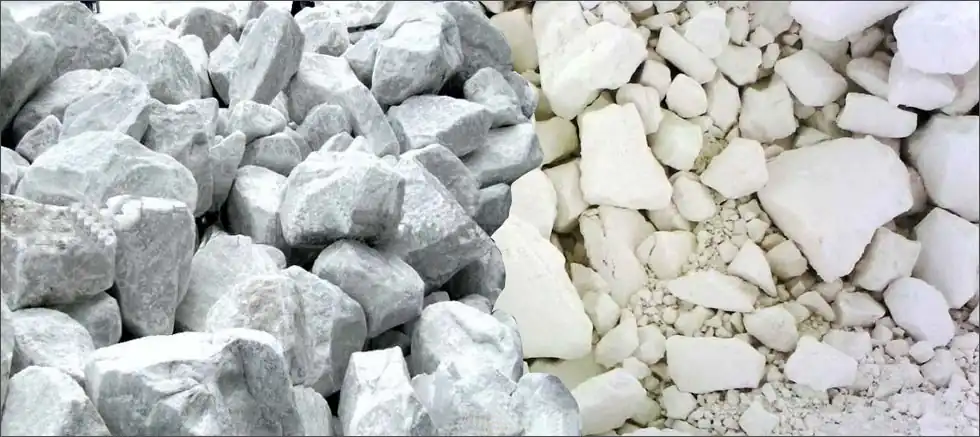
Brine-lime method:
Will be purified and refined treatment of brine and digested to remove slag treatment of lime made of milk of lime in the precipitation tank for precipitation reaction.
Add flocculant to the obtained slurry, mix it thoroughly, and then enter the settling tank for separation, and then filter, wash, dry, and pulverize to produce finished magnesium hydroxide products.
Brine-ammonia method :
Take the brine which has been purified and treated to remove sulfate, carbon dioxide, a small amount of boron and other impurities as the raw material, and use ammonia as the precipitant to carry out the precipitation reaction in the reaction kettle.
Before the reaction, put a certain amount of crystal seeds, fully stirred, the ratio of brine and ammonia is 1: (0.9~0.93), the temperature is controlled at 40 ℃.
Add flocculant after the end of the reaction, the precipitate is filtered, washed, dried and crushed to produce finished magnesium hydroxide.
Dolomite calcination method:
Calcine the dolomite at 950 ℃ for 2.5 hours, digestion ratio 1:40, digestion temperature 70 ℃, digestion time is 50 minutes.
The molar ratio of hydrochloric acid dosage to calcium ions in primary acid leaching was 2:1, and the molar ratio of sulfuric acid dosage to magnesium ions in secondary acid leaching was 1:11.
The pH of the solution in the precipitation process is 11, and the maximum yield of magnesium hydroxide can be obtained under these process conditions, with the total yield reaching more than 85.20%, and flakes of magnesium hydroxide with average purity and dispersion are obtained.
Lightly burned dolomite method:
Dolomite is lightly burned at a lower temperature (not exceeding 700°C) to decompose into calcium oxide and magnesium oxide.
Grinding the dolomite and heating with water and ammonium sulfate, the ammonium sulfate and magnesium oxide react to form ammonia, magnesium sulfate and water.
After filtration, ammonia is added to the filtrate to produce magnesium hydroxide precipitate, which is filtered to obtain magnesium hydroxide solid.
Each of these methods has advantages and disadvantages, and the selection of an appropriate method requires comprehensive consideration based on specific needs and conditions. For example, the brine-lime method and the brine-ammonia method are suitable for large-scale industrial production, while the dolomite calcination method and the lightly burned dolomite method are suitable for the production of magnesium hydroxide requiring high purity or a specific morphology.