Abstract
The present invention belongs to the field of high-purity magnesium oxide production, and provides a method for producing high-purity magnesium oxide by reducing and pyrolyzing magnesium sulfate using natural gas. The steps are as follows: 1) Using magnesium sulfate heptahydrate with a purity greater than 99% as a raw material, calcine at 500-600°C for 2-4 hours to obtain anhydrous magnesium sulfate, which is ground for standby use; 2) reducing and pyrolyzing anhydrous magnesium sulfate with natural gas in a reactor, with a conversion rate greater than 99%, to obtain a solid phase product magnesium oxide with a purity greater than 99%, and the gas phase products are mainly carbon dioxide and sulfur dioxide; 3) absorbing the tail gas to obtain valuable by-products (calcium carbonate, sulfuric acid or sodium sulfite or manganese sulfate). The present invention not only realizes the production of high-purity magnesium oxide and improves the pyrolysis efficiency, but also makes full use of the tail gas generated by pyrolysis to produce valuable by-products, avoids environmental pollution, and reduces production costs.
Description
A method for producing high-purity magnesium oxide by reducing and pyrolyzing magnesium sulfate using natural gas
Technical field
The present invention belongs to the field of high-purity magnesium oxide production, and relates to a method for producing high-purity magnesium oxide by reducing and pyrolyzing magnesium sulfate using natural gas
Background technology
High-purity magnesium oxide (magnesium oxide content ≥ 98%) has excellent acid and alkali resistance and electrical insulation at high temperatures, good light transmittance, high thermal conductivity, and large thermal expansion coefficient. It is an important inorganic chemical product and is widely used in medicine, ceramics, electronics, electrical appliances and other industries.
At present, there are several methods for preparing magnesium oxide from magnesium sulfate:
Chai Duoli studied the conditions for preparing high-purity magnesium oxide by calcining the synthesized magnesium hydroxide precursor using industrial magnesium sulfate and sodium hydroxide as raw materials. Under the optimal process conditions, the magnesium sulfate concentration is 2 mol/L, the reaction temperature is 40°C, the reaction time is 35min, and the calcination temperature is 900°C. The purity of the product magnesium oxide reaches more than 99%. Since this method uses sodium hydroxide as a precipitant, it will increase production costs. In addition, the reaction conditions are not easy to control.
Zhang Jingjing studied the process conditions for preparing high-purity magnesium oxide by direct pyrolysis of magnesium sulfate. After dehydration of magnesium sulfate with a particle size of 109 μm, it was pyrolyzed at 1100°C for 1h to obtain magnesium oxide with a purity of 99.8%. Direct pyrolysis has low efficiency and increases production costs.
Liu Haigang studied the preparation of magnesium oxide by reducing and pyrolyzing magnesium sulfate with a solid reducing agent under an inert atmosphere. The results showed that under the optimal conditions, the conversion rate of anhydrous magnesium sulfate was only 90%, which affected the purity of magnesium oxide.
Content of the invention
The purpose of the present invention is to solve the problems of high cost, low pyrolysis efficiency, low purity of the obtained magnesium oxide, many process parameters, difficult to control, and tail gas pollution in the existing methods.
A method for producing high-purity magnesium oxide by reducing and pyrolyzing magnesium sulfate with natural gas comprises the following steps:
(1) calcining magnesium sulfate heptahydrate at 500-600°C for 2-4 hours to obtain anhydrous magnesium sulfate, and then grinding it to 100-200 mesh;
(2) loading the product obtained in step (1) into a reactor, introducing natural gas, and reducing and pyrolyzing it at 800-1100°C, preferably at a temperature of 900-1000°C; the gas-solid (ml/g) ratio is 47:1-50:1. The gas phase reduction products are mainly sulfur dioxide and carbon dioxide, and the solid phase reduction product is magnesium oxide. The main reaction is:
4MgSO4+CH4=4MgO+SO2+CO2+2H2O
(3) The gas phase product produced in step (2) is passed through a sodium hydroxide solution, or a pyrolusite slurry, or a reactor with a vanadium catalyst and absorbed with 98.3% concentrated sulfuric acid to generate sodium sulfite or manganese sulfate or sulfuric acid, and calcium carbonate is generated by absorbing CO2 through lime water to obtain valuable by-products of sodium sulfite or manganese sulfate or sulfuric acid and calcium carbonate.
The process flow of using natural gas to reduce and pyrolyze magnesium sulfate to produce high-purity magnesium oxide is shown in Figure 1. Compared with the prior art, the present invention has a simple process, a short process, easy-to-control reaction conditions, high pyrolysis efficiency, and obtains high-purity magnesium oxide. The tail gas is absorbed, which not only avoids environmental pollution, but also obtains valuable by-products and reduces production costs.
Illustrations
Figure 1 is a process flow chart of using natural gas to reduce and pyrolyze magnesium sulfate to produce high-purity magnesium oxide.

Figure 2 is a schematic diagram of the reaction device. In the figure, 1 is a natural gas cylinder, 2 is a flow meter, 3 is a temperature controller, 4 is a reactor, 5 is a heating furnace, 6 is a magnetic stirrer, 7 is a sodium hydroxide solution SO2 absorption device, 8 is a lime water CO2 absorption device, 9 is a natural gas collection bottle, 10 is a pyrolusite slurry SO2 absorption device, 11 is a reactor equipped with a vanadium catalyst, 12 is a concentrated sulfuric acid SO3 absorption device, and 13 is an oxygen cylinder.
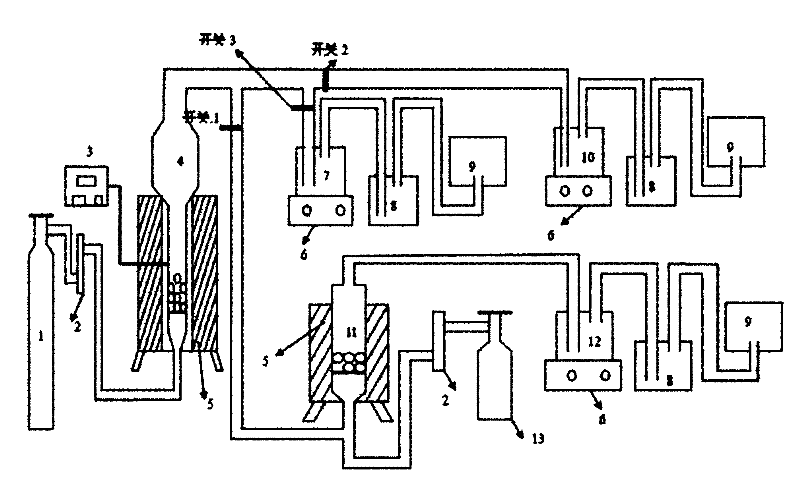
Specific implementation method
Example 1
(1) Dehydrate magnesium sulfate heptahydrate with a purity greater than 99% at 500°C for 4 hours to obtain anhydrous magnesium sulfate, which is then ground and sieved, with -120 mesh accounting for 80%;
(2) 100 g of anhydrous magnesium sulfate prepared in step 1 is loaded into a reactor and heated to 900°C;
(3) Natural gas (methane content greater than 98%) is introduced into a reactor containing anhydrous magnesium sulfate for reduction pyrolysis, and the flow rate of natural gas is controlled to be 160 ml/min, and the reaction time is 0.5 h;
(4) Turn on switch 1, and turn off switches 2 and 3 at the same time, and pass the sulfur dioxide gas produced by the reduction pyrolysis reaction into the reactor 11. At the same time, turn on the switch of the oxygen cylinder, and convert it into sulfur trioxide under the catalytic oxidation of the vanadium catalyst. Pass the sulfur trioxide into the 98.3% concentrated sulfuric acid absorption bottle 12. The concentration of concentrated sulfuric acid can be increased by 0.3%-0.5%. The obtained sulfuric acid can be diluted with water to produce sulfuric acid of different concentrations. The generated carbon dioxide gas is passed into the absorption bottle 8 filled with lime water to obtain calcium carbonate. The excess natural gas Collected in the collection bottle 9;
Reaction formula:
2SO2+O2=2SO3
SO3+H2O=H2SO4
Ca(OH)2+CO2=CaCO3↓+H2O
(5) The solid phase obtained after the reduction pyrolysis reaction
The conversion rate is 99.9%;
Example 2
(1) Magnesium sulfate heptahydrate with a purity greater than 99% is dehydrated at 550°C for 3 hours to obtain anhydrous magnesium sulfate, which is then ground and sieved, with -150 mesh accounting for 80%;
(2) 300% of the anhydrous magnesium sulfate prepared in step 1 is g is loaded into the reactor and heated to 950℃;
(3) natural gas (methane content greater than 98%) is introduced into the reactor containing anhydrous magnesium sulfate, the flow rate of natural gas is controlled to be 480ml/min, and the reaction time is 0.5h;
(4) switch 2 is turned on, and switches 1 and 3 are turned off at the same time, and sulfur dioxide produced by the reduction pyrolysis reaction is introduced into the absorption bottle 10 containing pyrolusite slurry, and the obtained adsorption liquid is subjected to impurity removal, filtration, evaporation crystallization, and drying to obtain manganese sulfate, and the generated carbon dioxide gas is absorbed by lime water, filtered to obtain calcium carbonate, and the excess natural gas is collected in the collection bottle 9;
Reaction formula:
MnO2+ SO2= MnSO4
Ca(OH)2+CO2=CaCO3↓+H2O
(5) After the reduction pyrolysis reaction, the solid phase product obtained is magnesium oxide with a purity of 99.9% and a conversion rate of magnesium sulfate of 99.9%;
Example 3
(1) Dehydrate magnesium sulfate heptahydrate with a purity greater than 99% at 600°C for 2 hours, then grind it and sieve it, with -180 mesh accounting for 80%;
(2) Charge 600g of anhydrous magnesium sulfate prepared in step 1 into the reactor and heat it to 1000°C;
(3) Pass natural gas (methane content greater than 98%) into the reactor, control the flow rate of natural gas to 960ml/min, and the reaction time to 0.5 h;
(4) Turn on switch 3 and close switches 1 and 2 at the same time, and pass the sulfur dioxide produced by the reduction pyrolysis reaction into the absorption bottle 7 containing sodium hydroxide solution to generate sodium sulfite solution. After purifying the sodium sulfite solution, evaporate, crystallize and dry to obtain anhydrous sodium sulfite. The generated carbon dioxide gas is absorbed by lime water and filtered to obtain calcium carbonate. The excess natural gas is collected in the collection bottle 9;
Reaction formula:
2NaOH+SO2=Na2SO3+H2O
Ca(OH)2+CO2=CaCO3↓+H2O
(5) The solid phase product obtained after the reduction pyrolysis reaction is magnesium oxide with a purity of 99.9%, and the conversion rate of magnesium sulfate is 99.9%.