Preparation of nano magnesium hydroxide
Nano magnesium hydroxide is prepared by various methods, including seawater-lime milk method, brine-ammonia method and dolomite calcination method.
Each of these methods has its own advantages and can be selected according to the purity, morphology and production scale of the required magnesium hydroxide. For example, the seawater-lime emulsion method utilizes natural resources and is less costly, while the dolomite calcination method is suitable for applications requiring higher purity.
Surface modification technology
Surface modification of magnesium hydroxide nanoparticles is a key step to improve their dispersion and compatibility in polymer matrix. By introducing surfactants or powder modifiers, the hydrophilicity of magnesium hydroxide can be significantly reduced and its stability in organic media can be enhanced. The modified magnesium hydroxide is more likely to form a homogeneous composite with the polymer matrix, thus improving the overall performance of the material.
Flame retardant performance research
The flame retardant mechanism of nano magnesium hydroxide mainly includes reducing the flammability of polymers, delaying matrix decomposition, heat-absorbing decomposition, and dilution of gas-phase combustibles concentration by the generated water vapor. Application studies in high-density polyethylene (HDPE) and other materials show that nano-magnesium hydroxide can significantly improve the oxygen index and vertical combustion grade of the material, to achieve excellent flame retardant effect.
Application Prospects
With the improvement of environmental protection and safety performance requirements, nano magnesium hydroxide as an environmentally friendly flame retardant, its market demand is growing. Through continuous technological innovation and optimization, the application of nano magnesium hydroxide in flame retardant plastics, rubbers, coatings and other fields is promising.
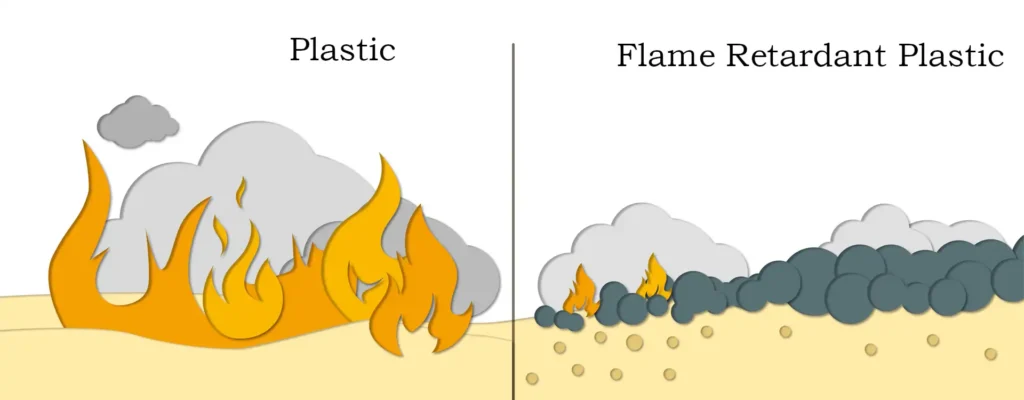
The preparation and modification technology of nano magnesium hydroxide is the key to realize its effective application in polymer materials. By optimizing the production process and modification methods, it can give full play to its flame retardant potential and provide strong support for the development of new environmentally friendly flame retardant materials.
Preparation of heavy magnesium oxide
Everyone for heavy magnesium oxide products have seen, but do you know how heavy magnesium oxide is produced? The following Messi Biology of experts will tell you about the production process of heavy magnesium oxide.
1, raw material preparation: the production of heavy magnesium oxide light burning magnesium oxide powder quality requirements are high. General use of high-quality magnesite production of high-grade powder, must need to pay attention to the magnesium oxide can not let the moisture caking, the index is: magnesium oxide ≥ 93%, calcium oxide ≤ 1.5%, iron ≤ 0.5%, silica ≤ 1%, burning weight loss ≤ 3%, fineness ≥ 325 mesh.
2, water selection in addition to impurities: in the steel tank with agitation, the first water, open the stirrer, in the upper part of the input light burning magnesium oxide powder, fast feeding, to get magnesium oxide slurry, stirring uniformly, open the bottom of the discharge tank, slurry through the centrifugal pump into the cyclone separator, the coarser and the relative density of the mechanical impurities, due to the centrifugal force of the greater, at the bottom will be discharged, which is what we usually say the bottom of the flow, relative density of lighter The magnesium oxide slurry with lighter relative density and smaller particles rises to the upper overflow port and is discharged to the hydration tank.
3, magnesium oxide hydrolysis system of magnesium hydroxide: magnesium oxide hydrolysis with steel square hydration tank, the upper part of the water discharge port. After water selection of magnesium oxide slurry into the hydration tank, after natural settlement for about half an hour, the upper clear liquid discharged through the water discharge port. The remaining magnesium oxide slurry in the hydration tank for about 3 hours or so, began to occur hydration reaction, hydration reaction is an exothermic reaction, the temperature of the slurry will naturally rise to 100 degrees will occur after the violent reaction, generally half an hour to the end of the reaction. At this time the slurry will be thickened, and then after 5 hours, it can be sent to drying and calcination.
Due to the reason of time, this narration can only be up to here. We must pay attention to, in the summer when the temperature is relatively high, the hydration reaction is very fast, from feeding to the water selection operation should be completed within half an hour, placed in the water selection process of hydration reaction. If you still want to know more knowledge, or want to purchase magnesium oxide, then you can directly consult our online customer service, we will have someone to receive you.