The preparation of silicon steel grade magnesium oxide by the brine ammonia method is currently the most widely used preparation method in China. The principle of this method is to react magnesium ions in brine with ammonia to form basic magnesium carbonate precipitate, and then undergo calcination, pickling, water washing, drying and other processes to obtain silicon steel grade magnesium oxide.
The process flow of preparing silicon steel grade magnesium oxide by brine ammonia method is as follows:
① Raw material preparation: After preprocessing raw materials such as seawater brine or Glauber’s salt, brine of a certain concentration is obtained.
② Basic magnesium carbonate precipitation: Brine and ammonia solution are reacted under certain conditions to generate basic magnesium carbonate precipitation.
③ Calcination of basic magnesium carbonate: Precipitate basic magnesium carbonate and calcine it at a certain temperature to generate magnesium hydroxide.
④ Magnesium hydroxide pickling: Pickling magnesium hydroxide with hydrochloric acid solution to remove impurities.
⑤ Magnesium hydroxide water washing: Wash the pickled magnesium hydroxide with water to remove acidic impurities.
⑥ Magnesium hydroxide drying: Dry the washed magnesium hydroxide at a certain temperature to obtain silicon steel grade magnesium oxide.
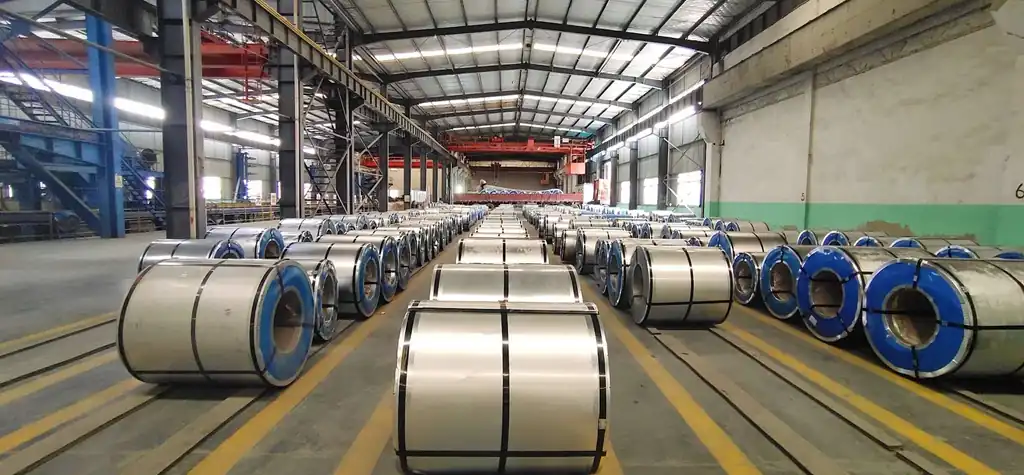
The process parameters for preparing silicon steel grade magnesium oxide by brine ammonia method mainly include:
① Brine concentration: Brine concentration has an impact on the yield and quality of basic magnesium carbonate precipitation. Generally speaking, when the brine concentration is between 20% and 30%, the yield and quality of basic magnesium carbonate precipitation are higher.
② Ammonia concentration: Ammonia concentration also affects the yield and quality of basic magnesium carbonate precipitation. Generally, when the ammonia concentration is between 10% and 20%, the yield and quality of basic magnesium carbonate precipitation are higher.
③ Reaction temperature: The reaction temperature also affects the yield and quality of basic magnesium carbonate precipitation. Generally, when the reaction temperature is between 60°C and 80°C, the yield and quality of basic magnesium carbonate precipitation are higher.
④ Reaction time: Reaction time also affects the yield and quality of basic magnesium carbonate precipitation. Generally, when the reaction time is between 1 and 2 hours, the yield and quality of basic magnesium carbonate precipitation are higher.
The product quality of silicon steel grade magnesia prepared by brine ammonia method mainly includes chemical purity, hydration rate, viscosity and particle size.
① Chemical purity: The chemical purity of silicon steel grade magnesium oxide is generally required to be above 98%.
② Hydration rate: The hydration rate of silicon steel grade magnesium oxide is generally required to be below 2%.
③ Viscosity: The viscosity of silicon steel grade magnesium oxide is generally required to be between 40 and 80cp.
④ Particle size: The particle size of silicon steel grade magnesium oxide is generally required to be between 10 and 30 μm.
The preparation of silicon steel grade magnesium oxide by brine ammonia method has the following advantages:
① The sources of raw materials are wide and the cost is low.
②The process flow is shorter and the production cycle is shorter.
③ Product quality is stable and easy to control.
However, this method also has the following shortcomings:
① The precipitation of basic magnesium carbonate is easy to agglomerate, which affects dehydration and calcination.
② Waste acid is easily produced during the pickling process, causing environmental pollution.
③ Wastewater is easily produced during the washing process, resulting in a waste of resources.
In order to overcome the shortcomings of preparing silicon steel grade magnesium oxide by the brine ammonia method, domestic and foreign scholars have conducted a lot of research and proposed the following improvement measures:
① Adopt efficient dehydration and calcination processes to reduce basic magnesium carbonate agglomeration.
② Use an efficient pickling process to reduce the generation of waste acid.
③ Adopt efficient water washing process to reduce the generation of waste water.
The implementation of these improvement measures can improve the production efficiency and product quality of silicon steel grade magnesium oxide and reduce environmental pollution.