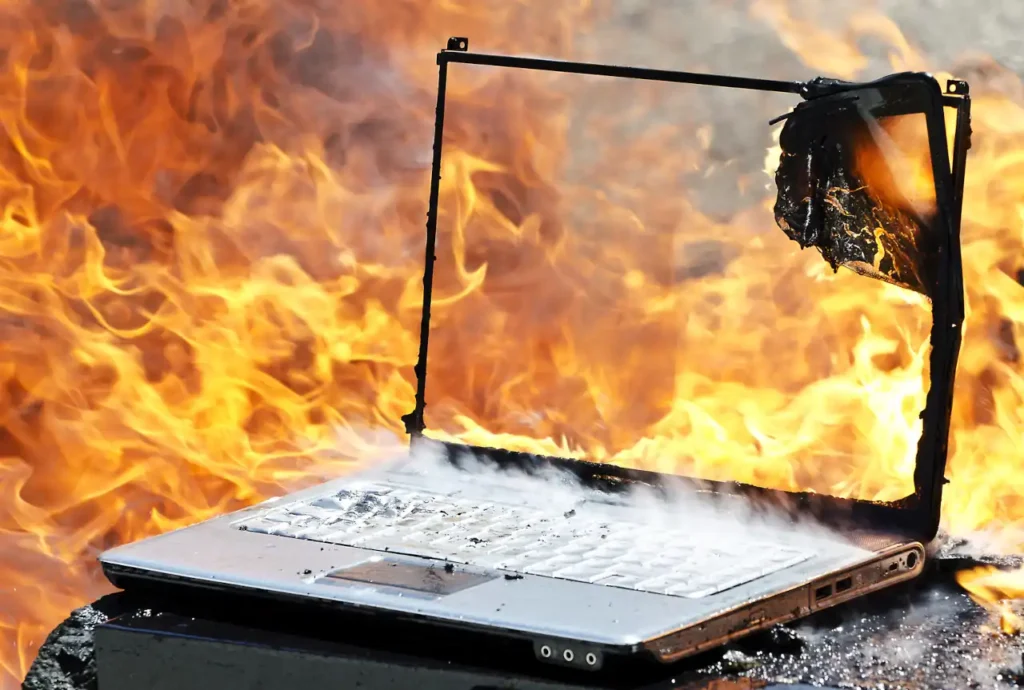
Magnesium hydroxide is an important industrial raw material, which is mainly used in the neutralization treatment of acidic wastewater, flame retardant of organic materials such as plastics and rubber, flue gas desulfurization, food and feed additives, and medicines. Among them, the use of flame retardants is an application field of magnesium hydroxide with high added value. As a flame retardant for polymers such as plastics and rubber, magnesium hydroxide is required to have the characteristics of ultrafine, good dispersibility, and appropriate surface modification treatment, and at the same time, magnesium hydroxide is required to have a high whiteness.
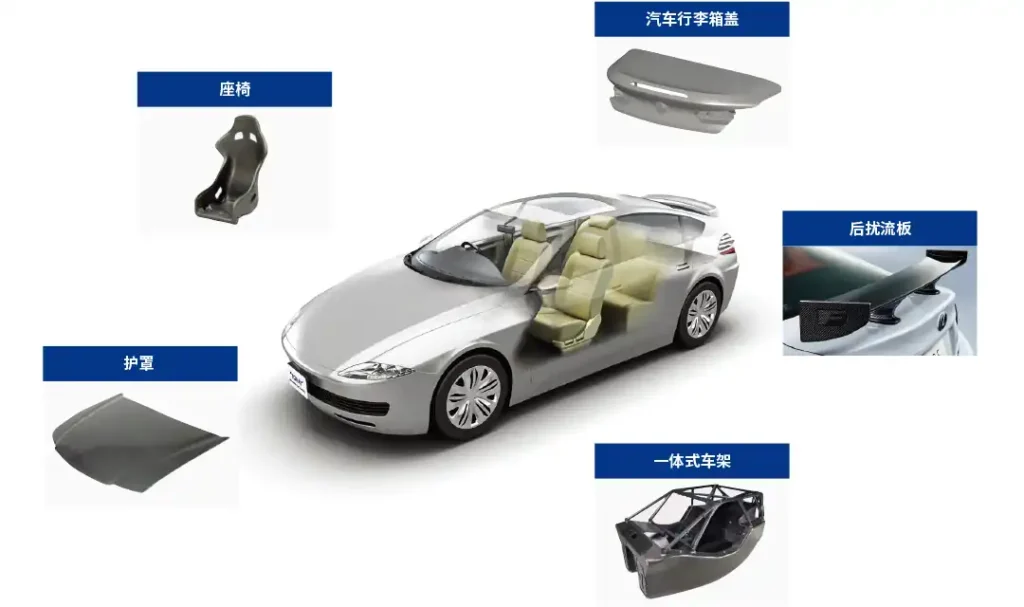
1. Preparation and modification of ultrafine magnesium hydroxide
There are two ways to prepare magnesium hydroxide. One is to grind the natural mineral brucite (the main component is magnesium hydroxide) to a certain fineness, and the other is to use soluble magnesium salts and alkali chemical reactions to make it.
In recent years, researchers have conducted more research on the ultrafine grinding and surface modification of magnesium hydroxide. The process of ultrafine grinding of natural brucite using a medium stirred mill was studied. The results show that when the medium stirred mill is used to ultrafinely grind brucite powder, the effects of several grinding aids are: dispersant μm, dμm.
Many researchers have modified the surface of magnesium hydroxide and added it to organic polymer materials to investigate the effects of surface modification on various properties of the materials.
Magnesium hydroxide was modified with rare earth coupling agents, calcium stearate, etc. and then added to PP. The results showed that the flame retardant level of PP could reach FV-0 level and the oxygen index was close to 30% when Mg(OH)2 accounting for 65% of the total mass of the composite material was added to PP; and the modified Mg(OH)2 could improve the mechanical properties of flame-retardant PP.
The magnesium hydroxide flame-retardant plywood was tested by adding magnesium hydroxide to the adhesive used in the preparation of plywood. The experimental results showed that after magnesium hydroxide flame-retardant plywood was used, the heat release rate, total heat release, and ignition loss of the material during combustion were significantly reduced.
The effect of magnesium hydroxide modified with silane coupling agent on the properties of PP/magnesium hydroxide composites was experimentally studied.
The surface modification of ultrafinely crushed brucite was studied. Ultrafine brucite powder with a d50 of about 1 micron was surface modified by wet and dry methods using modifiers and surfactants such as hydrogen silicone oil, aluminate coupling agent, silane coupling agent, titanate coupling agent and stearic acid, and the effects of various modifiers on magnesium hydroxide modification and the modification process and dosage of the modifier with good modification effect were obtained. The modified powder was added to PP and PVC for flame retardant tests. The results show that the dispersibility of the powder in a dry state and in a polymer matrix can be improved by surface modification of the powder, and the dispersibility and flame retardant properties of the powder in PP can be improved by surface modification. The modification can improve the mechanical properties of PP/magnesium hydroxide composites to varying degrees.
The United States and Japan have done a lot of work on the research of magnesium hydroxide flame retardants and have produced different types of magnesium hydroxide. More than 70% of the particles developed in the United States have a particle size of less than 2μm, which can significantly improve the mechanical properties of polymers when magnesium hydroxide is highly filled. When used in PVC and rubber, it can replace 30% to 50% of aluminum hydroxide to improve the smoke suppression and oxygen index of the material. Magnesium hydroxide with a particle size of 0.9 to 1.1μm produced by American companies can be used for flame retardant polyolefins, PVC and nylon. The content of flame retardant filling in nylon 6 and nylon 66 can reach 50% to 60%, and the flame retardant grade reaches UL94V-0; when used to fill flame retardant LDPE and HDPE, the mechanical properties of the material only decrease slightly.
Related foreign scholars have also studied magnesium hydroxide flame retardant plywood, polymer films, and the influence of magnesium hydroxide particle shape on the performance of composite materials.
At present, the raw materials and processes for preparing magnesium hydroxide mainly include: (1) using sodium hydroxide to react with brine or brine blocks to produce high-purity magnesium hydroxide, but the cost is too high; (2) using calcined dolomite to react with brine or brine blocks to produce magnesium hydroxide, and using lime milk to react with brine or brine blocks to produce magnesium hydroxide. Although the raw material costs of these two process routes are relatively low, the purity of the obtained magnesium hydroxide is not high due to the inevitable introduction of impurity ions into brine, brine blocks, dolomite and lime milk, which limits its application range. (3) using ammonia water to react with brine or brine blocks to produce magnesium hydroxide. This process has the characteristics of relatively low cost, but it requires excess ammonia water (ammonia excess rate of about %) during the reaction, and the remaining ammonia needs to be heated and evaporated. Wastewater treatment becomes a problem because the ammonia evaporation effect cannot make the wastewater meet the discharge standard. Researchers have conducted a large number of experimental studies on various processes.
The traditional method for preparing magnesium hydroxide is to react brine, brine flakes or brine blocks containing magnesium chloride with sodium hydroxide. Recently, a special method has been adopted at home and abroad to prepare magnesium hydroxide, that is, ammonia water and calcium hydroxide are first used to prepare needle-shaped crystalline basic magnesium chloride with magnesium chloride, and then the basic magnesium chloride is treated with hot water to obtain fibrous crystalline magnesium hydroxide, and finally surface modification is performed. The magnesium hydroxide obtained by this process has the characteristics of easy filtration and high crystallinity. The disadvantage is that the prepared magnesium hydroxide particles are large.
In the preparation process of magnesium hydroxide, the particle size and crystallinity of magnesium hydroxide are closely related to its preparation process. The concentration of reactants, reaction temperature, reaction time, and subsequent treatment, hydrothermal treatment and surface modification after the reaction have an important influence on the particle size of magnesium hydroxide. At the same time, for ultrafine magnesium hydroxide, how to improve the washing efficiency and filtration performance of the slurry is the main problem that plagues the quality and output of magnesium hydroxide products. For these problems, scholars at home and abroad have conducted a lot of experimental research.
From the perspective of reaction kinetics, scholars have shown that in the magnesium hydroxide precipitation reaction, low magnesium hydroxide supersaturation, low magnesium precipitation rate and the addition of magnesium hydroxide seeds are conducive to the growth of magnesium hydroxide crystals, and magnesium hydroxide with better performance can be obtained. However, this condition is inconsistent with actual production, because low supersaturation means reducing the concentration of magnesium ions, which will waste a lot of water, and low magnesium precipitation rate means reducing the recovery rate of magnesium. Therefore, this theory cannot be applied to actual production.
The production process of flame-retardant magnesium hydroxide was studied. Dolomite was used as raw material. After calcination, ammonia water was used as a precipitant. Impurities were first removed, and then various process conditions were controlled for precipitation to obtain needle-shaped magnesium hydroxide powder. After the magnesium hydroxide powder was prepared, it was hydrothermally treated to improve the crystallinity of the magnesium hydroxide powder. The reaction conditions were: precipitation temperature of 50-65℃, and hydrothermal treatment time of 1.2-1.5h. The dispersibility of the powder was improved by surface modification using sodium oleate and sodium stearate.
The preparation technology of flame-retardant magnesium hydroxide was reviewed, and the effects of the crystallization habit of magnesium hydroxide and solution composition on hydrothermal modification in the preparation of magnesium hydroxide were studied. Hydrothermal treatment is a method of chemical reaction at a certain temperature (between the boiling point and critical point of water, i.e., ℃~℃) and pressure (0.1MPa~22MPa) using water or aqueous solution as solvent. Hydrothermal treatment makes the water adsorbed on the surface of the crystal combine, thereby destroying the liquid layer adsorbed on the surface of the crystal, reducing the resistance of the adsorption layer to the growth of the crystal, and promoting the formation of magnesium hydroxide with large grains and small specific surface area and special crystal form. The results show that although the use of water, magnesium chloride, ammonium chloride, and ammonia water as solvents can improve the morphology and agglomeration state of magnesium hydroxide to a certain extent, the effect is not obvious; while sodium hydroxide aqueous solution can change the growth direction of magnesium hydroxide crystals and make the generated magnesium hydroxide crystal structure more stable. The hydrothermal modification of magnesium hydroxide crystals in sodium hydroxide hydrothermal medium belongs to the dissolution-crystallization mechanism, and the growth unit is the octahedron of Mg(OH)64-.
After experimental investigation, it is pointed out that the preparation of special crystal form of magnesium hydroxide and adding it to polymer can improve the mechanical properties of polymer. For example, after the prepared 1nm~10nm magnesium hydroxide is added to the polypropylene matrix, the material has the properties of some steel materials and can replace steel in some application fields. When preparing nano magnesium hydroxide, the main difficulty is the agglomeration problem of magnesium hydroxide.
The experiment on the preparation of nano magnesium hydroxide by full back mixing homogeneous emulsification method was carried out. The experiment used magnesium chloride as the raw material and sodium hydroxide as the precipitant. The effects of reaction temperature, magnesium chloride concentration, rotation speed and other factors on the particle size of magnesium hydroxide were investigated. The experimental results show that with the decrease of magnesium chloride solution concentration and the increase of rotor speed, the particle size of the obtained magnesium hydroxide decreases. The optimal reaction temperature is 40℃~50℃. The particle size of the prepared magnesium hydroxide powder is about 85nm, and the particles are hexagonal flake crystals.
The thermodynamics and kinetics of magnesium hydroxide precipitation were analyzed. The analysis results show that the main factors affecting the crystallization performance of magnesium hydroxide are the nucleus wettability and hydration ion radius in the non-uniform nucleation process. To improve the crystallization performance of magnesium hydroxide and produce magnesium hydroxide with good filtration performance, the following measures need to be taken: (1) adding seeds with good wettability; (2) heating to reduce the hydrated ion radius of Mg2+; (3) controlling the concentration of Mg2+.
The effect of reaction temperature on the precipitation of magnesium hydroxide was experimentally studied. The experiment used ammonia water to precipitate magnesium hydroxide. The experiment was carried out at different reaction temperatures. The results showed that the precipitation effect of magnesium hydroxide was best when the reaction temperature was 40℃~50℃.
The use of magnesium chloride to prepare magnesium hydroxide was experimentally studied. The experimental raw material used zinc sulfate electrolysis wastewater. The study found that the residual chlorine in the magnesium hydroxide product was too high. The chlorine content could not be reduced by strengthening washing, controlling the reaction temperature and other process conditions. The product was calcined at a temperature higher than K. After the magnesium hydroxide was calcined into magnesium oxide, the performance of the product met the quality requirements of magnesium oxide.
The crystal form of nano magnesium hydroxide powder prepared in dilute solution was studied. SEM, XRD, nitrogen adsorption and other research methods were used for analysis. The results show that the nature of the reaction raw materials, the type of ions in the solution, the reaction temperature, the hydrothermal treatment and other factors have an important influence on the shape of the crystal.
The growth control of three types of magnesium hydroxide crystals prepared by wet precipitation was tested. The test used magnesium chloride solution and ammonia water to react, and the dispersant was added to the ammonia water in proportion before the reaction. The additives used were surfactants or water-soluble organic dispersants, mainly gelatin powder, lauryl alcohol, polyvinyl alcohol, polyethylene glycol, polysorbate, etc. The effects of various influencing factors in the preparation process, such as additive type, reaction temperature, raw material concentration, addition method, etc., on the crystal form were studied. By controlling the process conditions, nano-magnesium hydroxide with needle-shaped, flake-shaped and rod-shaped crystals were obtained respectively. Finally, the crystals were characterized by using transmission electron microscopy, field emission scanning electron microscopy, and XRD. The results show that when the mass concentration of ammonia water is about 5%, there are more needle-shaped particles in the obtained product, while when the mass concentration of ammonia water is increased to about 25%, there are more flake-shaped particles in the obtained product. The control of crystal shape depends on the type of additives. Because different additives have different adsorption modes on the surface of magnesium hydroxide crystal nuclei. The reaction temperature has an important influence on the crystal form and particle size of magnesium hydroxide; while hydrothermal treatment can improve the regularity of the powder.
Surfactants play a role in dispersing and controlling crystal growth during the preparation process, and nano magnesium hydroxide with needle-shaped, rod-shaped and flake-shaped crystal forms is obtained. Magnesium hydroxide was characterized by scanning electron microscopy, transmission electron microscopy and XRD. Then, after adding it to the EVA material at a mass ratio of 1:1, the oxygen index of the composite material reached 38.3%. Transmission electron microscopy analysis showed that magnesium hydroxide powder formed a monodisperse state in the EVA matrix; scanning electron microscopy analysis showed that after the magnesium hydroxide/EVA composite material was burned, magnesium hydroxide formed a dense magnesium oxide layer on the surface of the material. This is conducive to blocking the contact between air and EVA, thereby improving the flame retardant properties and oxygen index of the material.
The effect of microwave on the product performance in the preparation of nano-sized needle-shaped magnesium hydroxide in dilute solution was experimentally studied. In the experiment, magnesium nitrate solution and sodium hydroxide solution were reacted at room temperature to synthesize needle-shaped magnesium hydroxide nanopowder, and microwave dispersion was applied during the reaction. The diameter of the magnesium hydroxide sample obtained is 20-40nm and the length is 100-150nm.
Many patents have been applied for the preparation of magnesium hydroxide. The preparation and surface treatment of high smoke suppression nano magnesium hydroxide were studied. The experiment used the sol-gel method to prepare precipitated magnesium hydroxide. Before precipitation, 0.5%-3.0% sodium dodecylbenzene sulfonate was used as a particle barrier. After preparation, it was calcined at ℃ and then ultrafine ground. Finally, the emulsion polymerization method was used to microencapsulate the magnesium hydroxide powder to make the surface of the magnesium hydroxide powder hydrophobic.
After the magnesium hydroxide powder is prepared, it is a difficult problem to separate it from the mother liquor. That is, if the reaction conditions are not well controlled, the prepared magnesium hydroxide will be difficult to filter and wash; the reason is the formation of colloidal magnesium hydroxide. The research results show that the general solution is to increase the crystallinity of magnesium hydroxide by adding seed crystals, hydrothermal treatment, and reducing the concentration of magnesium ions in the solution during the reaction, and the second is to add a certain flocculant after the reaction to make the magnesium hydroxide particles in the slurry flocculate and settle, so as to achieve the purpose of separation from the liquid phase. Polyacrylamide is commonly used as a flocculant for magnesium hydroxide.
The technology of in-situ preparation of nano magnesium hydroxide using light-burned magnesium (an amorphous refractory material prepared from magnesite or magnesium carbonate) was studied.
In summary, in the preparation process of magnesium hydroxide, high purity, fine particle size, small specific surface area, good dispersibility and easy filtration are the process requirements for preparing magnesium hydroxide. Controlling the type of precipitant, reaction process conditions, hydrothermal treatment, selection of dispersant and appropriate surface modification are the main ways to prepare ultrafine and highly dispersed magnesium hydroxide.
2. Application of ultrafine magnesium hydroxide
Flame retardant refers to an auxiliary agent that can make polymers less likely to catch fire and slow down their burning after catching fire. Flame retardants can be divided into organic flame retardants and inorganic flame retardants. According to the elements contained in the flame retardant, organic flame retardants can be divided into phosphorus flame retardants, halogen flame retardants (including chlorine and bromine) and nitrogen flame retardants; inorganic flame retardants are divided into antimony compounds, red phosphorus and phosphoric acid, boron compounds, aluminum hydroxide and magnesium hydroxide, zirconium compounds and bismuth compounds.
Among the many types of flame retardants, halogen flame retardants are widely used for their good flame retardant effect and no effect on the physical and chemical properties of materials. However, polymers added with halogen flame retardants have a large amount of smoke when burning, and are prone to release corrosive gases (such as HCl, HBr, etc.) and harmful gases, which are easy to cause secondary hazards, and this secondary hazard is often one of the main causes of casualties in fires. Therefore, with the development of science and technology and the improvement of people’s environmental awareness, the research and application of flame retardants in today’s world are moving towards halogen-free direction. Inorganic flame retardants represented by aluminum hydroxide and magnesium hydroxide rely on chemical decomposition to absorb heat and release water to play a flame retardant role when used. They are non-toxic, smoke-inhibiting, and the chemical properties of decomposition products (aluminum oxide, magnesium oxide) are stable, so they do not cause secondary hazards. In recent years, the application of inorganic flame retardants has developed rapidly. Aluminum hydroxide flame retardant is the most widely used and largest-dosage inorganic flame retardant, while magnesium hydroxide flame retardant is the fastest-developing one in application research. In the United States, inorganic additive flame retardants account for about 80% of the total flame retardants, with aluminum hydroxide ranking first, followed by magnesium hydroxide; in Western Europe, inorganic additive flame retardants aluminum hydroxide and magnesium hydroxide account for more than 50% of the total flame retardants.
At present, the sustainable development strategy has become a common goal pursued by countries around the world, environmental protection awareness is increasing, and green projects or environmentally friendly projects are more respected by people. As a weak base, magnesium hydroxide has buffering properties. As a neutralizer for acidic wastewater, it has process advantages over traditional alkaline substances such as calcium hydroxide and sodium hydroxide in many aspects, and can greatly reduce costs in product treatment and discharge. Even if used in excess, the pH value of the solution will not exceed 9.0, which is very easy to control.
Due to its large specific surface area, high activity and strong adsorption capacity, magnesium hydroxide can adsorb and remove heavy metal ions that are harmful to the environment from various industrial emissions, such as Ni2+, Cu2+, Cd2+, Mn2+, Cr3+ and Cr6+. Magnesium hydroxide can also be used as a flue gas desulfurizer. Adding magnesium hydroxide to boiler fuel can reduce the harm of high-aluminum and high-sulfur fuels to boilers and reduce the emission of sulfur dioxide and other harmful gases.