Abstract
The present invention discloses a production process of magnesium oxide for petroleum catalysts, including the following steps: to anhydrous magnesium chloride dissolved in water for removing impurities to remove calcium, sulfate, iron, manganese, and then add the extractant to combine with H+ ions in an acidic medium, followed by the passage of high-purity carbon dioxide, the formation of magnesium bicarbonate pyrolysis under low temperature conditions and ultrasonic assisted pulverization to generate 8MgCO3– Mg(OH)2-2H2O, and finally filtering and washing, the generated filter cake is calcined in a lock-type kiln and maintains a certain heating curve to obtain the catalyst-specific magnesium oxide. Beneficial effect: the magnesium oxide produced by this invention meets the following conditions: the content of magnesium oxide is more than 98%, the content of calcium oxide is less than 0.5%, the content of iron is less than 3 ppm, manganese is less than 3 ppm, Cl– is less than 0.01%, SO42- is less than 0.01%, the product particle size of D50<3 micron, D90 <12 microns, particle size distribution double wave peaks, the product’s morphology is characterized by hexahedron, citric acid value in 200 seconds to 250 seconds.
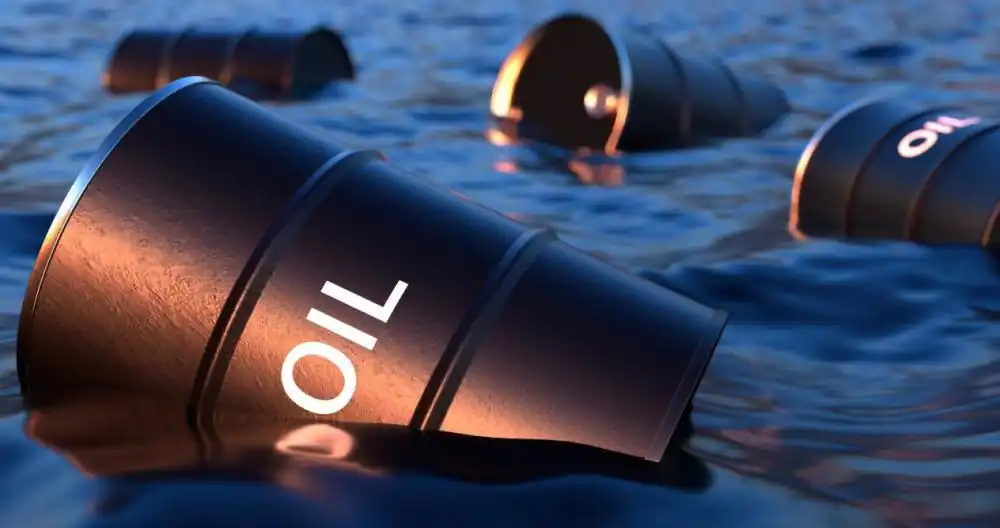
Description
A Production Process of Magnesium Oxide for Petroleum Catalysts
Technical Field
The present invention relates to the field of petroleum catalysts, and more specifically, it relates to a production process of magnesium oxide for petroleum catalysts.
Background Technology
In the production process of petroleum catalyst, it is necessary to add magnesium oxide as a catalyst carrier to increase the adsorption performance of the catalyst. The specific reaction process is as follows: acidic water is stirred with thin alumina for 20 minutes, then 31-36% hydrochloric acid is added and stirred for 30 minutes, and then magnesium oxide is added and stirred. The concentration of hydrotalcite was 10% solid, and the ratio of hydrochloric acid (31-36%) to hydrotalcite was 0.35. The magnesium oxide slurry was 25% solid. The performance index of magnesium oxide in the reaction process of precursor directly affects the reaction process and the quality of the final catalyst.
The purity of magnesium oxide is lower than 97%, so the content of magnesium oxide is greater than 97%. If the activity of magnesium oxide added during the stirring reaction is too high, some small particles are easy to be formed in the reaction slurry. If the citric acid value of magnesium oxide is controlled at 200 seconds-250 seconds, this problem can be solved well, and the generated slurry is uniform and no particles are formed.
When magnesium oxide is added to the acidic slurry of the proposed thin hydrotalcite, the slurry becomes very viscous at the beginning of the reaction, and then gradually becomes thinner. This makes the power of the reaction equipment increase a lot. And there are a large number of semi-finished products stained on the wall of the reaction tank, resulting in cleaning difficulties, seriously affecting the normal production. In order to solve this problem, the particle size of magnesium oxide is controlled at D50<3 micron, D90<12 micron. And particle size distribution double wave peak. Can be a good solution to this problem. When adding magnesium oxide at the end of the slurry has been kept in a diluted state and will not be suddenly thickened.
In the finished product of the catalyst in order to increase the friction coefficient of the product and the hardness and adsorption ability of the product, it is necessary to make the crystal shape of magnesium oxide into hexahedron.
No effective solution has been proposed for the problems in the related technology.
Contents of the Invention
In view of the problems in the related technology, the present invention proposes a production process of magnesium oxide for petroleum catalysts to overcome the above technical problems existing in the existing related technology.
To this end, the specific technical solution adopted in the present invention is as follows:
A production process of magnesium oxide specializing in petroleum catalysts, comprising the following steps:
Add water to anhydrous magnesium chloride to configure a magnesium chloride solution, add a small amount of magnesium sulfate, filter, and remove calcium ions therein;
To the above solution then add an appropriate amount of barium chloride, and stir and filter to remove the sulfate ions therein;
To the above filtrate add hydrogen peroxide and stir until uniform, then add hydrochloric acid to adjust the PH value, then add a small amount of hydrated alkaline magnesium carbonate and stir until uniform, then stir the static precipitation, and finally filter to remove the iron, manganese and heavy metal impurities therein;
In the magnesium chloride solution, add the extractant organic amine in the acidic medium and hydrogen ions combined with the acid to generate ammonium salts into the organic soluble phase;
To the magnesium chloride solution into high-purity carbon dioxide, the formation of magnesium bicarbonate in solution;
Adjust the pH value of magnesium bicarbonate to 7.5, first add sodium thiosulfate to reduce F3+ to F2+ ions, and then add hydrogen peroxide to oxidize F2+ to F3+ ions, followed by precipitation for two hours, and filtration to remove iron-manganese metal impurities, so that the iron and manganese are reduced to less than 3ppm;
The magnesium carbonate solution was subjected to low-temperature pyrolysis to generate 8MgCO3-Mg(OH)2-2H2O, and at the same time, ultrasonic-assisted pulverization was used and the ultrasonic frequency was adjusted, so that the precursor generated, 8MgCO3-Mg(OH)2-2H2O, had a particle size in accordance with the requirements, and the morphology was hexahedral;
The magnesium carbonate filter cake was washed 4 times with deionized water to remove chloride ions and sulfate ions from it;
Filtering and washing the above solution and calcining it at high temperature in a lock-type kiln and controlling a certain rate of heating, then pushing out the product out of the lock-type kiln and cooling it down to room temperature, so that the citric acid value of the generated product is in the range of 200-500 sec, and the iodine-absorbing value of magnesium oxide is in the range of 6-10 mgI2/gMgO, and then the magnesium oxide specializing for catalysts can be obtained.
Further, the concentration of said magnesium chloride solution is 2 mol/L and the volume of said magnesium chloride solution is 1000 ml.
Further, the mass of said barium chloride added is 20g.
Further, said hydrogen peroxide added is 1 ml, and said hydrated alkaline magnesium carbonate is 2 g. The stirring time is 10 minutes for both, and hydrochloric acid is added to adjust the pH value to 3, and the precipitation is left to settle for 12 hours.
Further, said extractant organic amine is R3,N,R = C7H10-C10H21.
Further, said extraction is an iontophoretic extraction and the extraction system with a concentration of 50% organic amine is selected using phosphate ester as diluent.
Further, said concentration of organic amine 50% is a percentage by volume.
Further, said magnesium carbonate solution is heated by steam.
Further, said heating temperature and pressure during steam heating are 50-60°C and 5.5-6 kg/cm2, respectively.
Further, said high temperature calcination temperature is 1000°C.
The beneficial effect of the present invention is that the magnesium oxide produced by the present invention satisfies the following conditions:
1, the content of magnesium oxide is greater than 98%, the content of calcium oxide is less than 0.5%, the content of iron is less than 3 ppm, manganese is less than 3 ppm, Cl- is less than 0.01%, SO4 2- is less than 0.01%, the particle size of the product is D50 < 3 microns, D90 < 12 microns, the distribution of the particle size is double-wave peaked, and the morphology characteristic of the product is hexahedral, and the value of the citric acid is between 200 seconds and 250 seconds.
2, through the control of magnesium oxide content greater than 98%, so as to effectively avoid the occurrence of bubbles in the reaction process; through the magnesium oxide citrate value control in 200 seconds -250 seconds, so as to effectively avoid the formation of small particles in the reaction slurry due to the addition of magnesium oxide activity is too high, so as to make the generated slurry homogeneous, no particles formed.
3, through the magnesium oxide particle size product particle size control in D50 <3 microns, D90 <12 microns, and particle size distribution of double peaks, so as to make the addition of magnesium oxide slurry has been to maintain a dilute state will not suddenly thicken, which not only effectively reduces the reaction equipment required for the power, but also effectively avoided due to a large number of semi-finished products stained in the reaction tank caused by the difficulty of cleaning, which effectively ensures the normal operation of the production. The production is carried out normally.
4、By making the crystal shape of magnesium oxide into hexahedron, the friction coefficient of the product and the hardness and adsorption capacity of the product are effectively increased.