Magnesium oxide is used instead of ammonia water to be used in ammonium sulfite slurry. The alkaline buffer is made of magnesium oxide, and all indicators of the slurry can reach a level similar to that of the ammonia method. Using magnesium oxide as a buffer, the pulp is easy to bleach, which can promote the effect of delignin during steaming, reduce pollutant emissions and help protect the environment while also reducing costs.
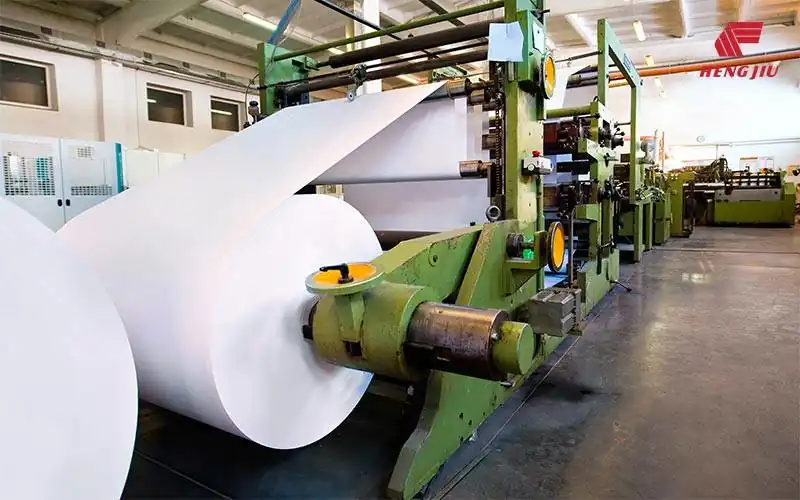
Magnesium oxide can be used when pulp bleaching. Magnesium oxide can replace caustic soda compared to traditional bleaching processes. At the same time, magnesium oxide can improve the viscosity of the slurry, maintain the brightness of the pulp, and reduce the COD content and production costs. In the process of bleaching pulp by hydrogen peroxide, magnesium oxide can replace caustic soda, which can reduce the iron and manganese ions content in the slurry, and can also avoid yellowing due to the presence of excessive iron and improve the quality of the slurry. At the same time, magnesium oxide has a buffering effect and is easy to control pH. It will be better if used in combination with inorganic complexing agents such as phosphate and silicate.
Magnesium oxide can act as a wetting agent to improve pulp deinking operations. The traditional sulfite pulping process has been improved to a magnesium agent sulfite pulping process. After improvement, it can use lower-quality wood as raw materials. The pulp produced can be used to make news printing paper, and the agents used and waste heat can be recycled. In this way, many ecological and economic problems in traditional sulfite pulping operations have been solved for paper mills.