The copper and cobalt belt in Zambia and the Democratic Republic of the Congo (DRC) is the world’s third largest copper belt after the Andes in South America (Chile, Peru and Argentina) and the southwestern United States of America and Mexico, and cobalt reserves are highly concentrated in the DRC, which is the largest in the world. At present, the copper ore used in DRC is mainly surface oxidized copper and cobalt polymetallic ores, therefore, the copper mining mostly adopts the wet process, and in 2013, the output of wet copper refining in DRC has reached 940,000 tons. In recent years, with the investment of domestic and foreign mining and metallurgical enterprises in the DRC further increased, the production of wet copper refining has a tendency of further substantial growth.
DRC (DRC) copper wet production process is generally “ore leaching (heap leaching or stirring leaching〉extraction and electrowinning”, leaching of copper in the process of using sulfur dioxide or sodium sulfite as a reductant to leach cobalt, cobalt-containing copper and cobalt sulfuric acid solution through the copper extracted electrowinning production of cathode copper, extracted residual liquid after neutralization and decontamination of cobalt after precipitation. As the local industrial base of DRC is very weak, basically all industrial auxiliary materials need to be imported except for part of sulfuric acid, in order to save cost, the cobalt products produced locally are mostly made into crude cobalt compounds by the above mentioned process of simple removal of impurities, and the most common crude cobalt compounds are cobalt carbonate precipitation using sodium carbonate to produce cobalt carbonate.
However, the grade of cobalt in crude cobalt carbonate is low, mostly around 25%, which increases the transportation cost and other expenses, and the liquid after sodium carbonate cobalt precipitation contains a large number of sodium salts that are difficult to be treated, which will cause environmental pollution if directly discharged, and if recycled for a long time in the system, it will result in a large number of sodium ions enriched in the solution, which will seriously affect the production of copper. With the local environmental protection policy gradually strict, a number of enterprises began to study more economical, environmentally friendly cobalt production process, magnesium oxide cobalt precipitation process is one of the directions.
Aiming at a local wet smelting plant in the Democratic Republic of the Congo (DRC) cobalt-containing copper extracted liquid neutralization, removal of impurities after the liquid, the study of the effect of magnesium oxide cobalt precipitation under different conditions, came to the conclusion that at a temperature of about 5 ℃, the reaction time of 4h, the end point of the pH value of 8.0, magnesium oxide slurry for the cobalt precipitation of the best effect, the resulting cobalt grade of cobalt hydroxide is higher than 36%, the cobalt recovery rate of more than 99%, the magnesium oxide utilization rate of up to 91%.
Recovery of cobalt metal from cobalt sulfate solution system is generally taken to add magnesium oxide slurry production of cobalt hydroxide products. Whether the concentration of magnesium oxide slurry is kept stable or not is crucial to the quality of the products obtained from cobalt sinking industrial production, the high concentration of magnesium oxide slurry will cause the impurity magnesium content of cobalt products to rise, affecting the quality of the products, and the low concentration of magnesium oxide slurry will cause the reduction of cobalt recovery rate.
1. Test part
Test principle: adding magnesium oxide into the cobalt precipitation pre-liquid (the main component is CoS04 solution) has the following reaction.
MgO+H20→Mg(OH)2↓
Mg(OH)2→Mg2++2(OH)–
Mg(OH)2+CoSO4→Co(OH)2↓+MgSO4
Magnesium hydroxide produced by the hydrolysis of magnesium oxide can be ionized in water to produce OH–. At room temperature magnesium hydroxide lgKsp = -11.5, Co(OH)2 lgKsp = -14.2, due to the solubility product of Mg(OH)2 and Co(OH)2 is very much different, Co2+ in the solution will react with 0H– produced by the ionization of Mg(OH)2 and precipitate as Co(OH)2, which promotes the reaction in the positive direction, so that the MgO continues to dissolve and Co(OH )2is constantly precipitated out.
Test raw materials: the use of Congo (DRC), a local wet smelting enterprise copper extraction after the extraction of residual liquid by sulfur dioxide / air, quicklime neutralization and removal of impurities version of sodium carbonate cobalt precipitation before the liquid as raw materials. The composition of the material liquid is shown in the following table:
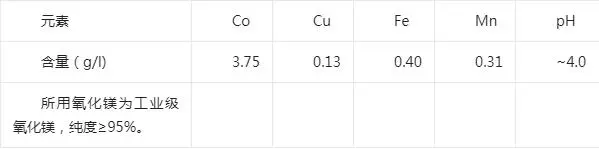
Cobalt precipitation liquid composition
Test method: accurately measure the cobalt precipitation material into the beaker, start stirring, the same stirring speed throughout the test, add magnesium oxide to start recording the reaction time, and realize the constant temperature in the electrothermal thermostatic water bath. During the process of cobalt precipitation, the pH value of the solution was detected online, and after the reaction was completed according to the test conditions, the cobalt slag was filtered, washed sufficiently and dried. The content of cobalt and other impurity elements in the slag were analyzed, and the recovery rate and the unit consumption of magnesium oxide were calculated.
2. Results and discussion
2.1 Charging mode on cobalt precipitation effect test
Magnesium oxide charging method has two kinds of charging: direct dry powder charging and charging after slurry mixing. This test examines the effect of different charging methods on the cobalt grade in the slag. Two groups of cobalt precipitation test, a group of magnesium oxide powder charging, a group of magnesium oxide slurry charging, slurry concentration of 10%, the test ph value of 8.0, the temperature of 50 ℃, stirring time of 5 h. The test results are shown in the table:
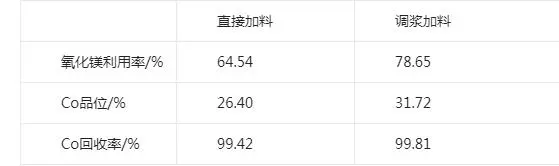
Test results of different dosing conditions
As can be seen from the table, the cobalt recovery of the two charging methods is close to, but the slurrying can make the charging more uniform, avoiding the local magnesium oxide excess, magnesium oxide adjusting slurry charging can obviously improve the cobalt grade. The cobalt grade in the slag obtained from direct dry powder dosing is 26.4%, and the cobalt grade in the slag obtained from slurry dosing is 31.7%, therefore, the subsequent tests all adopt magnesium oxide slurry dosing, and the concentration of slurry dosing is fixed at about 10%.
2.2 Cobalt precipitation endpoint pH value test
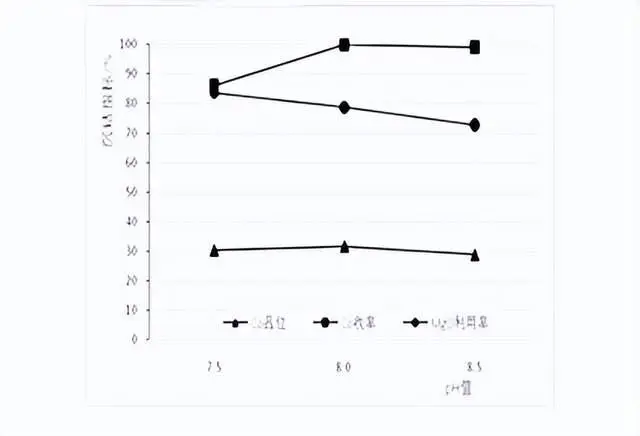
Cobalt precipitation results of different pH conditions
End point ph value setting: in order to facilitate the actual production control, to 0.5 interval selected ph value, respectively, 7.5, 8.0, 8.5. test temperature 50 ℃, stirring time of 5h, the test results are shown in the figure above.
From the figure, it can be seen that in the range of pH 7.58.5, with the increase of pH, the Co grade in the slag firstly increases and then decreases, the utilization rate of magnesium oxide decreases, and the Co recovery rate increases.
At pH 7.5, the slag containing Co is 30.4%, the MgO utilization rate is high, but the Co recovery rate is only 86.1%; at pH 8.0, the slag containing Co is 31.7%, the Co recovery rate is 99.8%, and the MgO utilization rate is 78.7%; at pH 8.5 at 8.5, the slag containing Co is only 28.8%, the Co recovery rate is 99.1%, but the MgO utilization rate is low at 72.8%. Therefore, the subsequent cobalt precipitation test was carried out after selecting the ph value of 8.0.
2.3 Temperature conditions
The test temperatures were room temperature (local ambient temperature about 30℃), 40℃, 50℃, 60℃, 70℃, test ph value 8.0, stirring time 5h. The results of the temperature conditions are shown in the following figure:
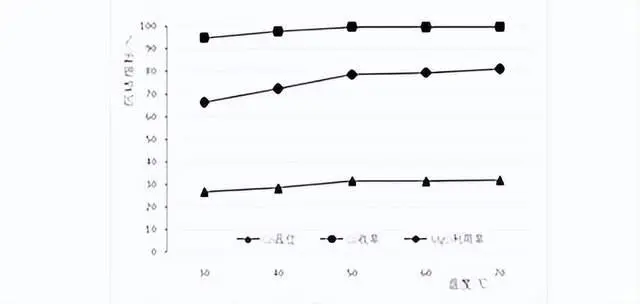
Results of cobalt precipitation under different temperature conditions
As can be seen from the figure, with the increase of temperature, the slag Co content, Co modeling yield, magnesium oxide utilization rate are gradually increased, but when the temperature rose to 50 ℃, the cobalt precipitation indexes did not change much, the slag Co content maintained at about 32%, Co recovery 99.7%, magnesium oxide utilization rate of 80%, therefore, the temperature of 50 ℃ was selected to carry out the subsequent cobalt precipitation test.
2.4 Cobalt precipitation time conditions test
In this test, samples were taken after stirring time of 2h, 3h, 4h and 5h to analyze the solution composition, and the Co recovery rate in each time period and Co content in the slag after 5h. Test ph value 8.0, temperature 50 ℃, test results are shown in the figure below:
As can be seen from the figure, with the increase of stirring time, Co recovery gradually increased, magnesium oxide utilization gradually decreased, when stirring time 4h, Co recovery was 99.7%, basically all the reaction.
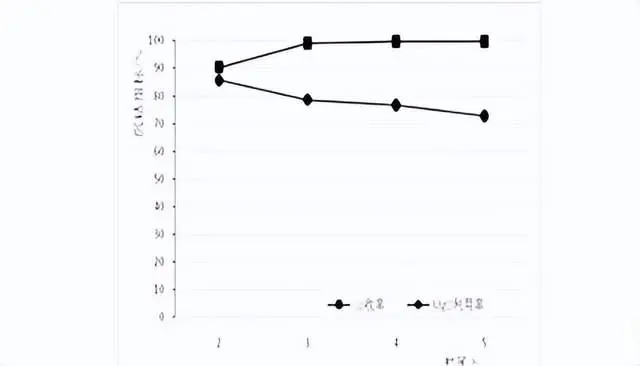
Cobalt precipitation results of different time conditions
2.5 Verification test
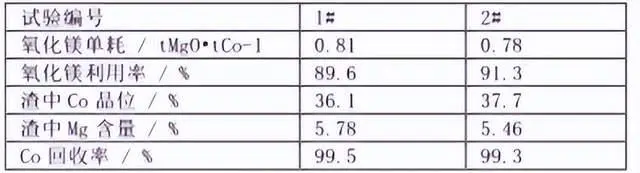
From the above condition test, the optimal process parameters for cobalt precipitation can be concluded as pH 8.0, temperature 50 ℃, stirring time 4h, using slurry magnesium oxide cobalt precipitation. With this optimal process conditions, 2 groups of cobalt precipitation verification tests were carried out, and the results are shown in the table below:
As can be seen from the table, the Co recovery of 1 and 2 groups of tests reached more than 99%, the slag containing Co was 36.1% and 37.7%, and the utilization rate of magnesium oxide was 89.6% and 91.3%, respectively. However, due to the low solubility of magnesium oxide, when generating cobalt hydroxide, the cobalt hydroxide may be wrapped in the surface of undissolved magnesium oxide, which causes further dissolution difficulties, so that the cobalt slag contains a certain amount of magnesium.
3. Conclusion
3.1 The optimum conditions for cobalt precipitation by magnesium oxide were concluded as follows: pH 8.0, temperature 50℃, reaction time 4h, and cobalt precipitation by magnesium oxide slurry.
3.2 in the best process conditions, cobalt recovery rate of more than 99%, Co in the slag of more than 36%, higher than sodium carbonate cobalt precipitation obtained about 25% grade of cobalt carbonate, magnesium oxide unit consumption of 0.8tMg0/tCo or so, the utilization rate of up to 91%.
3.3 there is a certain amount of insoluble magnesium exists in the cobalt hydroxide products.