Properties of Active Magnesium Oxide
Active magnesium oxide, also known as light-burned magnesium oxide or caustic magnesium oxide, is magnesium oxide formed by calcining magnesium compounds below 900°C. The chemical activity of magnesium oxide can be expressed by the iodine absorption value (adsorption performance index). The greater the chemical activity and the greater the iodine absorption value, the lighter it is. When the iodine absorption value is 120-180 mg/g, it is called high-activity magnesium oxide, when the iodine absorption value is 50-80 mg/g, it is called medium-activity magnesium oxide, and when the iodine absorption value is 19-43 mg/g, it is called low-activity magnesium oxide.
Active magnesium oxide is generally relative to heavy magnesium oxide. Since the activity of solid substances is proportional to their surface area, some people use the size of their surface area to express activity, so the specific surface area (the surface area per unit mass of substance) is introduced to regard the specific volume (ml/g) as the reciprocal of the bulk density. Generally speaking, highly active magnesium oxide is in the form of ultrafine powder, which refers to particles with a particle size of 10-1000nm. Due to the extremely small particle size of ultrafine particles, they often show special properties that conventional materials do not have in terms of magnetism, electricity, sound, heat and sensitivity. Therefore, it is widely used as a new material. The activity expressed by the citric acid activity value is 12-25. The smaller the value, the higher the activity. The activity expressed by the iodine absorption value is 80-120 (mgI/100gMgO), the specific surface area is between 5-20, and the apparent specific volume is between 6-8.5ml/g. Due to its large specific surface area, it has extremely high chemical activity and physical adsorption capacity, has good sintering performance, does not require the use of sintering aids to achieve low-temperature sintering, and is a preparation of high-functional fine inorganic materials.
Preparation of reactive magnesium oxide
There are many methods for preparing active magnesium oxide, including brine-ammonium carbonate method, dolomite carbonization method and brine-ammonia method. These methods have their own characteristics and application scenarios, which can meet different industrial needs. The following will introduce several main preparation methods of activated magnesium oxide in detail:
Brine-ammonium carbonate method
Chemical reaction process: In this method, ammonium carbonate solution is added to brine, and basic magnesium carbonate precipitation is generated after heating and precipitation. Then, active magnesium oxide is finally obtained by filtering, washing, drying and calcining decomposition.
Advantages: This method has the advantages of easy raw materials and easy reaction control, and is suitable for large-scale production.
Application: It is mainly used in occasions where high-purity active magnesium oxide is required, such as the production of electronic components and high-performance ceramics.
Dolomite carbonization method
Process flow: After calcining dolomite (xMgCO3·yCaCO3) or magnesite (MgCO3), water is added to digest to obtain magnesium hydroxide (Mg(OH)2) and calcium hydroxide (Ca(OH)2). Then carbonize with CO2 to obtain magnesium bicarbonate and by-product calcium carbonate. The mother liquor after treatment to remove calcium carbonate is pyrolyzed to obtain basic magnesium carbonate, and finally calcined at 800℃ for 1 to 2 hours to obtain active magnesium oxide.
Advantages: Natural mineral dolomite can be used as raw material, with low cost and suitable for industrial-scale production.
Application: Widely used as filler and reinforcing agent for materials such as rubber, plastic and paint.
Brine-ammonia method
Process description: Magnesium hydroxide precipitate is generated by introducing ammonia into brine. Then the magnesium hydroxide is filtered, washed, destroyed (crushed), dried, and finally transferred to a rotary calciner for calcination, and calcined at 500℃ for 2 hours to obtain active magnesium oxide.
Advantages: This method can effectively control the particle size and morphology of magnesium hydroxide, which helps to improve the activity of the final product.
Application: Commonly used in the fields of medicine and environmental protection, such as antacids and harmful gas adsorbents.
Magnesite calcination method
Preparation steps: Magnesium ore (main component is MgCO3) is directly calcined to generate magnesium oxide and carbon dioxide. Magnesium oxide with high activity can be obtained by controlling the calcination temperature and time.
Advantages: Easy operation, suitable for industrial applications that do not require particularly high activity.
Application: Widely used in building materials, refractory materials and metallurgical industries.
Serpentine acid leaching method
Extraction process: Serpentine contains rich silicon and magnesium minerals. Magnesium is extracted by acid leaching, and then active magnesium oxide is obtained through precipitation, filtration, drying and calcination.
Advantages: It can effectively extract high-purity magnesium oxide from low-grade ores.
Application: Mainly used for the production of high-purity magnesium oxide and special magnesium oxide materials.
Nanotechnology synthesis method
Technical introduction: Using nanotechnology, by controlling chemical reaction conditions, magnesium oxide with nano-scale particle size is synthesized. This method can obtain magnesium oxide with large specific surface area and extremely high activity.
Advantages: The product has extremely high chemical activity and physical adsorption capacity, and is suitable for cutting-edge technology fields.
Application: Mainly used in the manufacture of catalysts, high-end electronic materials and new composite materials.
External heating rotary kiln method
Production process: Under the condition of external heating treatment, the raw materials are calcined by a rotary kiln to generate active magnesium oxide. This method can be produced continuously with high efficiency.
Advantages: good production continuity, high degree of automation, suitable for large-scale production.
Application: widely used in the demand for magnesium oxide in industrial and agricultural fields.
Summary
As an important inorganic material, the various preparation methods of activated magnesium oxide not only demonstrate rich chemical and physical technologies, but also provide a broad application field. From industrial production to environmental protection, activated magnesium oxide plays an irreplaceable role. Continuing to explore new preparation technologies and improve existing processes will further promote the application prospects and scientific and technological progress of this material.
Applications of Active magnesium oxide
Active magnesium oxide is widely used in luminous parts, gas sensors, various rubber products, fiberglass, fluororubber, catalysts, adsorbents, etc., showing the excellent properties of active magnesium oxide. In recent years, after continuous development and application research and development, active magnesium oxide has been widely used in rubber products, fiberglass, petrochemical industry and other fields.
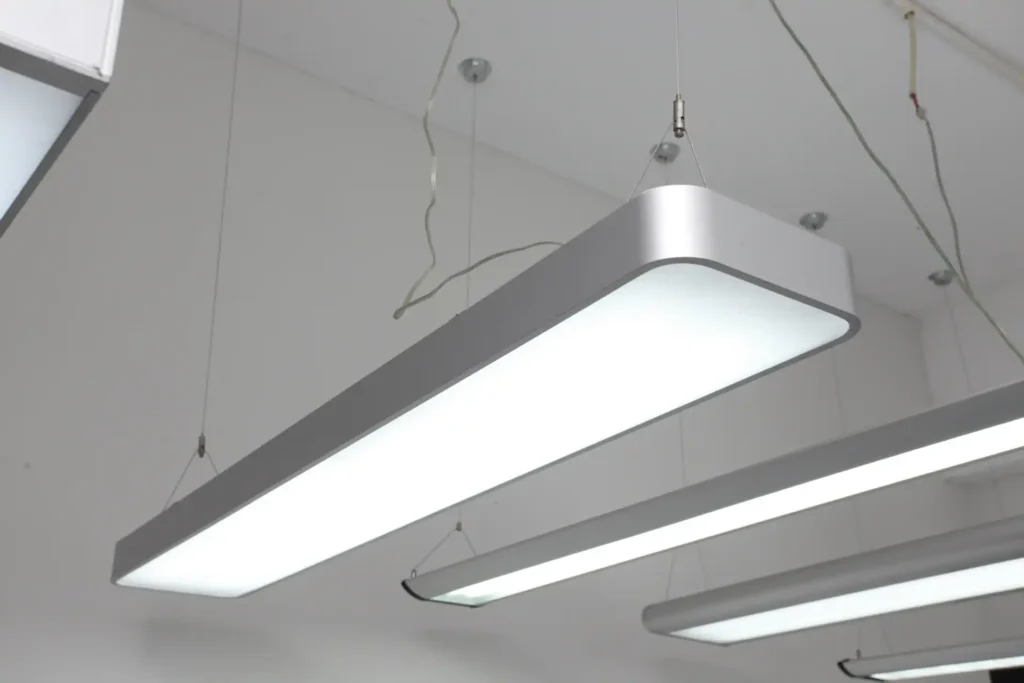
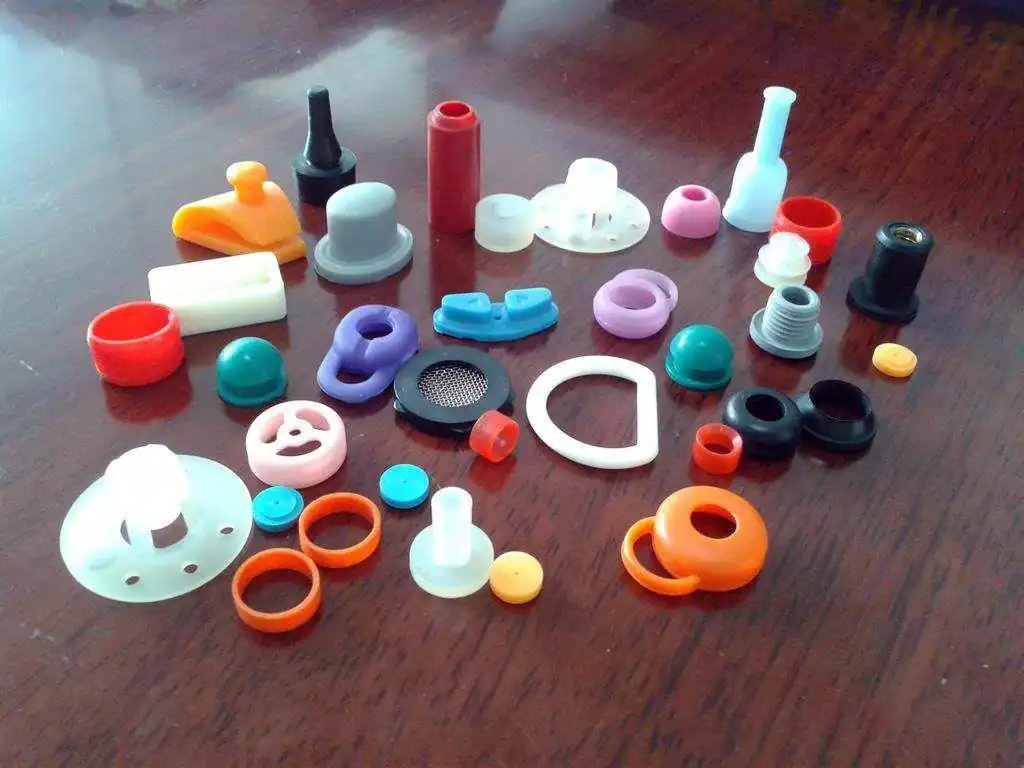
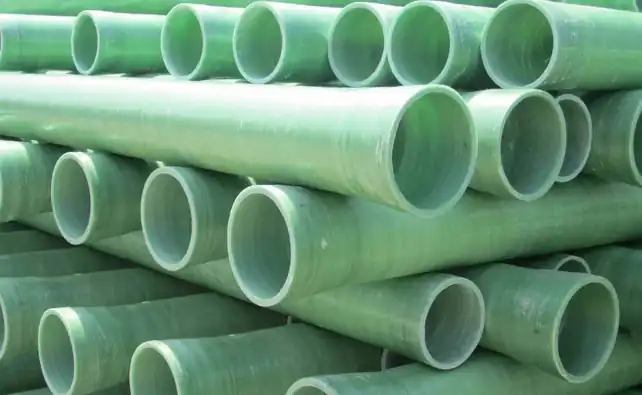