Abstract: The hydrolysis of ethyl silicate was carried out on the surface of magnesium carbonate particles by using sol-gel method with ethyl orthosilicate as the raw material, and the silicate generated was encapsulated on the surface of magnesium carbonate particles, then dried to form a silica film on the surface of magnesium carbonate particles. Orthogonal experiments were conducted to study the effect of different conditions on the encapsulation effect, and the encapsulated surface of magnesium carbonate was subjected to XRD analysis. The results showed that the surface of magnesium carbonate was coated with a layer of silica, the decomposition rate of magnesium carbonate was reduced after the coating of silica, and the coated magnesium carbonate can be used as a foaming agent for the preparation of metal foam.
Keywords: ethyl orthosilicate; hydrolysis; silicon dioxide; magnesium carbonate; foaming agent
Carbonate has the property of releasing carbon dioxide by thermal decomposition, so it can be chosen as the foaming agent for the preparation of foamed metal, CaCO3 has been used as a blowing agent in the preparation of aluminum foam [ 1 – 2 ]; however, due to the poor wettability of carbonate with the metal melt, it is necessary to carry out a surface treatment of carbonate in order to be better dispersed in the metal melt. A layer of oxide or metal on the surface of the particles can play a good wetting effect, at the same time, due to the fast decomposition of magnesium carbonate, after a layer of silicon dioxide, the carbon dioxide generated through the surface of the outward diffusion of the speed is slowed down, prolonging the decomposition of magnesium carbonate reaction speed, magnesium carbonate can be stabilized decomposition in the process of foaming, which is conducive to the formation of the foam body.
The surface of the particles for the coating technology are mainly chemical plating, chemical vapor deposition, plasma spraying method, metal liquid treatment method, etc., due to the SiO2 and metal melt has a good wettability, and the use of ethyl orthosilicate sol-gel can be on the surface of the solid coating layer of SiO2 membrane [ 3 – 5 ]. In this experiment, sol-gel was used to coat SiO2 film on the surface of magnesium carbonate particles, and the coated magnesium carbonate could be dispersed uniformly in the metal melts such as Al and Mg. The sol-gel method was firstly used to develop glass and ceramic powders [ 6 – 7 ], the basic process is: some easily hydrolyzed metal compounds (inorganic salts or metal alcohol salts) in the solvent and water reaction, through the process of hydrolysis and condensation and gradually gel, and then after drying, sintering and other post-processing processes. In recent years, this method has become a promising method of material preparation due to its low process temperature, uniform product composition, high purity, dense microstructure and other advantages [ 8 – 10 ].
1 Experimental design
1.1 Experimental method
Ethyl silicate and water hydrolyzed under certain conditions into silicic acid and ethanol, and silanol has a strong tendency to polymerization, in the hydrolysis reaction at the same time, the polymerization of ethoxysilanol, polymerization of silicone polymers with a three-dimensional mesh structure. In drying, the polymer is further condensed into a reticulated polymer with silicone-oxygen bonds (SiO2) [ 7 ]. If this condensation reaction is induced on the surface of magnesium carbonate particles, a layer of silicic acid is formed on the surface of the particles, and a SiO2 film is produced after sintering.
Since ethyl silicate is not soluble in water, it is usually hydrolyzed by dissolving ethyl silicate in ethanol and adding water. In this experiment, the hydrolysis was carried out without adding ethanol. First weigh a certain amount of ethyl silicate, then add a certain amount of magnesium carbonate into the ethyl silicate and mix well, so that the surface of magnesium carbonate coated with a layer of ethyl silicate, and then add a certain concentration of hydrochloric acid, mix well, and then add water to make the hydrolysis of ethyl silicate. Because the particle size of magnesium carbonate powder is 75~150μm, the ethyl silicate is covered on the surface of the particles to increase the contact area with water, so that the reaction can be carried out uniformly in the whole volume.
1.2 Orthogonal experimental design
The main factors affecting the hydrolysis reaction are: A, the mass ratio of ethyl silicate to magnesium carbonate; B, the mass ratio of ethyl silicate to water; C, the concentration of hydrochloric acid. In the experiment, the decomposition time of magnesium carbonate was used as the standard to measure the effect of coating, the longer the decomposition time of magnesium carbonate, the better the effect as a foaming agent.
Hydrolysis of tetraethyl silicate
Si(OC2H5)4 + 4H2O = Si(OH)4 + 4C2H5OH. (1)
From the equation (1), it can be seen that the hydrolysis of tetraethyl silicate is complete when the ratio of tetraethyl silicate to water is 1:4, and the mass ratio is 26:9 (about 3:1) to produce silicic acid. The factorial levels of this experiment are shown in Table 1. The experiment is a 3-factor, 3-level experiment, and an orthogonal table of type L9 (34 ) was used, and the specific orthogonal experimental table is shown in Table 2.
Table 1 Value s of factors and levels | ||
A (ethyl silicate to magnesium carbonate mass ratio) | B (ethyl silicate to water mass ratio ) | C (hydrochloric acid concentration) (mol-L-1) |
2.0 : 1 | 2.5 : 1 | 0.1 |
2.5 : 1 | 3.0 : 1 | 0.2 |
3.0 : 1 | 3.5 : 1 | 0.3 |
2 Analysis of orthogonal experiment results
The data of the orthogonal experimental program are shown in Table 3. From the comparison of the extremes in the table, it can be seen that RB (1.57) > RC (0.83) > RA (0.77), so the influence of the factors should be the primary and secondary BCA, by the selection of the average value of the factors, the selection of the level of the integrated value of the large, so the experiments selected A3B2C3 combination of the experiments, the results obtained by the decomposition of magnesium carbonate time of 7.2 min, which shows that the orthogonal experimental table used in the experiment can be selected as a good choice for the decomposition time of magnesium carbonate. This shows that the positive experimental table used in this experiment can select the optimized experimental combination A3B2C3, and also concluded that the mass ratio of tetraethyl silicate to water is the dominant factor affecting the effect of encapsulation.
Table 2 Orthogonal test results | ||||
experiment number | Horizontal Combination | Laboratory conditions | ||
A | B | C | ||
1 | A1B1C1 | 2.0 : 1 | 2.5 : 1 | 0.1 |
2 | A1B2C2 | 2.0 : 1 | 3.0 : 1 | 0.2 |
3 | A1B3C3 | 2.0 : 1 | 3.5 : 1 | 0.3 |
4 | A2B1C2 | 2.5 : 1 | 2.5 : 1 | 0.2 |
5 | A2B2C3 | 2.5 : 1 | 3.0 : 1 | 0.3 |
6 | A2B3C1 | 2.5 : 1 | 3.5 : 1 | 0.1 |
7 | A3B1C3 | 3.0 : 1 | 2.5 : 1 | 0.3 |
8 | A3B2C1 | 3.0 : 1 | 3.0 : 1 | 0.1 |
9 | A3B3C2 | 3.0 : 1 | 3.5 : 1 | 0.2 |
Table 3 Testing parameters and analysis | |||||
experiment number | A | B | C | D | Decomposition time of magnesium carbonate/min |
1 | 1 | 1 | 1 | 1 | 3.9 |
2 | 1 | 2 | 2 | 2 | 5.2 |
3 | 1 | 3 | 3 | 3 | 4.2 |
4 | 2 | 1 | 2 | 3 | 3.8 |
5 | 2 | 2 | 3 | 1 | 5.3 |
6 | 2 | 3 | 1 | 2 | 4.4 |
7 | 3 | 1 | 3 | 2 | 5.6 |
8 | 3 | 2 | 1 | 3 | 6.4 |
9 | 3 | 3 | 2 | 1 | 3.6 |
Ⅰ | 13.3 | 12.6 | 14.7 | — | — |
Ⅱ | 13.5 | 16.9 | 12.6 | — | — |
Ⅲ | 15.6 | 12.2 | 14.4 | — | — |
K1 | 4.43 | 4.43 | 4.9 | — | — |
K2 | 4.5 | 5.63 | 4.2 | — | — |
K3 | 5.2 | 4.07 | 5.03 | — | — |
R | 0.77 | 1.57 | 0.83 | — | — |
3 Analysis of the effect of magnesium carbonate coating silicon dioxide
The magnesium carbonate particles were analyzed by scanning electron microscope after the coating of silicon dioxide, Fig. 1a is the morphology of magnesium carbonate, from which it can be seen that the magnesium carbonate is a lamellar structure, and the surface is relatively loose. The magnesium carbonate after coating treatment is shown in Fig.1b, it can be seen that the surface of magnesium carbonate particles is much more regular, and denser than that of the uncoated magnesium carbonate particles. Through the XRD analysis of the surface of the particles, it can be seen from Fig. 2, there is silicon dioxide on the surface of magnesium carbonate, so this experiment uses the hydrolysis reaction of ethyl orthosilicate to coat silicon dioxide on the surface of magnesium carbonate.
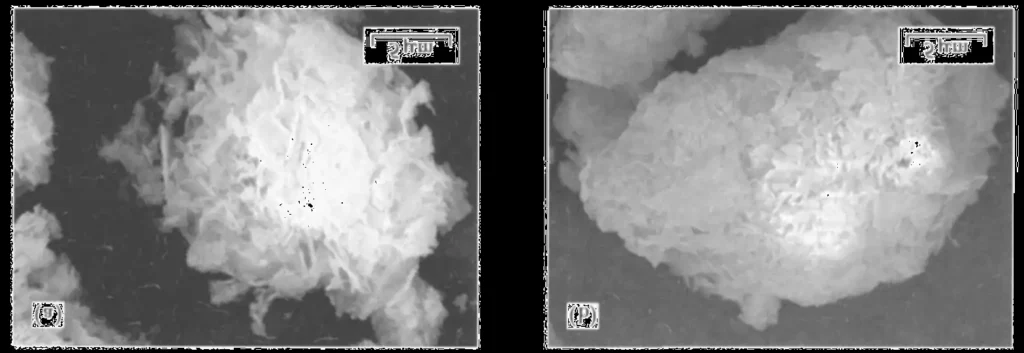
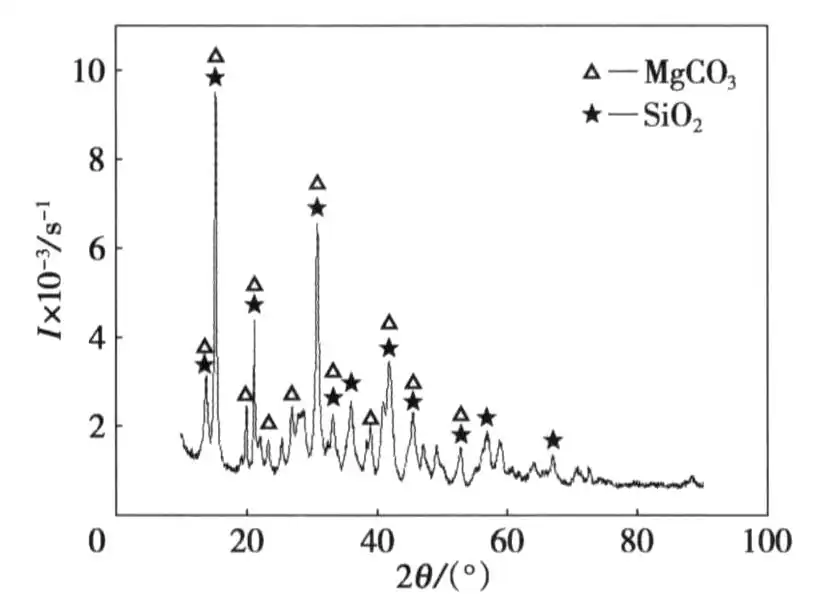
4 After coating silicon dioxide film decomposition kinetic analysis of magnesium carbonate
Magnesium carbonate at high temperature undergoes the following chemical reaction.
MgCO3=MgO + CO2 ↑. (2)
From equation (2), it can be seen that the decomposition reaction of magnesium carbonate generates solid magnesium oxide and carbon dioxide gas, the magnesium carbonate particles will be gradually surrounded by the magnesium oxide generated by the reaction, and the decomposition of carbon dioxide gas needs to be diffused outward through the magnesium oxide layer, the decomposition reaction of magnesium carbonate is mainly affected by the internal diffusion of carbon dioxide gas in the magnesium oxide layer. Because the magnesium oxide layer is loose structure, so the carbon dioxide gas can quickly diffuse out through the magnesium oxide layer, so the decomposition of magnesium carbonate reaction speed is also very fast. When the surface of magnesium carbonate coated with a layer of silicon dioxide film, carbon dioxide needs to pass through the film to diffuse out, the existence of this film reduces the internal diffusion of carbon dioxide, so that the decomposition of magnesium carbonate reaction rate tends to slow down, the reaction of magnesium carbonate after the coating includes the following three links.
1) the decomposition of magnesium carbonate at the interface of reactants and products (magnesium carbonate – magnesium oxide).
2) The gas product carbon dioxide diffuses first through the internal diffusion of the magnesium oxide layer and then through the internal diffusion of the silicon dioxide film layer.
3) External diffusion of carbon dioxide gas through the silicon dioxide film.
It is also proved by experiment that the decomposition reaction rate of magnesium carbonate is obviously reduced after the coating of silicon dioxide, and the decomposition reaction of magnesium carbonate can be investigated by the shrinkage nucleus model, and magnesium carbonate can be regarded as a spherical particle, and the shrinkage nucleus model of magnesium carbonate can be seen in Fig. 3. Figure 3 can be clearly seen in the reaction of the three links occurring in the region, the inner layer of the large circle is magnesium carbonate, the middle layer of magnesium carbonate reaction of magnesium oxide, the outermost layer of the silicon dioxide layer is encapsulated, due to the presence of silicon dioxide layer, so that the carbon dioxide diffusion of the body to become the reaction of the control stage, encapsulated magnesium carbonate decomposition rate is slow to do a good foaming agent.
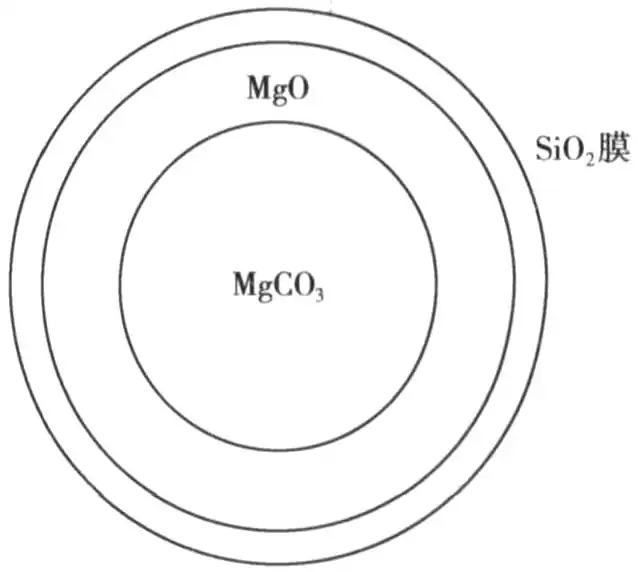
5 Conclusion
1) The hydrolysis reaction of ethyl orthosilicate can be used to coat the silicon dioxide layer on the surface of magnesium carbonate particles, the process in this experiment is hydrolyzed in an alcohol-free environment, in which the ratio of tetraethyl silicate to water is the dominant factor affecting the coating effect.
The optimal process conditions were: ethyl silicate to magnesium carbonate mass ratio 3:1, ethyl silicate to water mass ratio 3:1, hydrochloric acid concentration 0.3 mol/ L. The process was carried out in an alcohol-free environment, in which the ratio of tetraethyl silicate to water was the dominant factor affecting the coating effect.
2) The surface of magnesium carbonate coated with silicon dioxide is regular and the structure is relatively dense. Due to the silicon dioxide coating on the surface of magnesium carbonate, the internal diffusion of carbon dioxide in the reaction process of magnesium carbonate becomes the control stage of the reaction, which reduces the reaction speed of magnesium carbonate at high temperature, so that the coated magnesium carbonate can be used as a good blowing agent for the preparation of foam metal.