I, Overview
Cobalt is a very widely used metal, there are generally two methods to extract cobalt from nickel and cobalt containing ores, one is pyrometallurgical smelting, and the other is hydrometallurgical smelting. As wet smelting has the advantages of small energy consumption, less pollution, environmental protection, etc., it has been widely used in recent years, especially active magnesium oxide plays an indispensable role in cobalt refining.
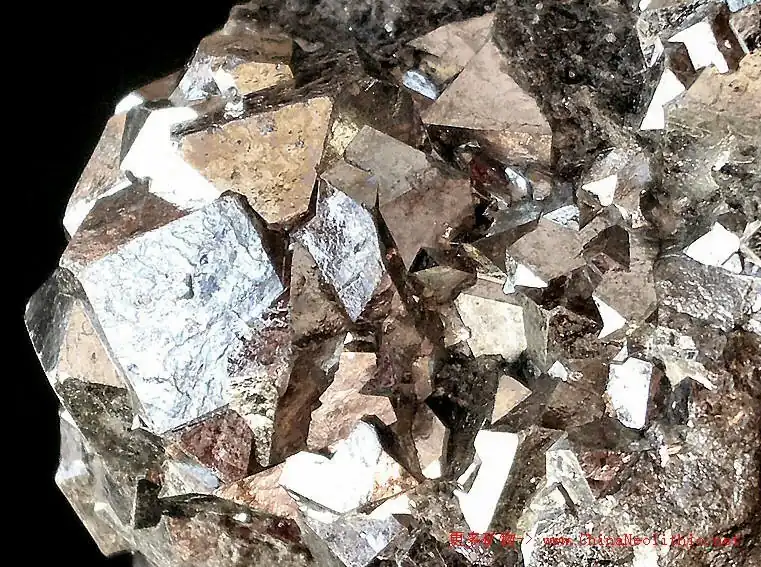
2, two-stage cobalt precipitation process
At present, the DRC cobalt refining process, including nickel and cobalt bearing ores made into slurry, acid leaching, get leaching slurry, using two-stage leaching process. The purpose of doing so is to achieve more leaching rate of copper, nickel and cobalt in the ore, especially the role of magnesium oxide in which can be maximized, the following look at the two-stage cobalt leaching process.
1, a section of cobalt: to the cobalt to add such as the concentration of about 10% of magnesium oxide, control ph value, cobalt sinking reaction for about four hours, after the reaction is completed, the solid-liquid separation, to get cobalt hydroxide products and cobalt sinking liquid.
2, the second section of the cobalt precipitation: to the cobalt precipitation liquid with milk of lime, control the ph value, continue to cobalt precipitation reaction for one to two hours, after the reaction is completed the solid-liquid separation, get the second section of the cobalt precipitation residue and cobalt precipitation, cobalt precipitation liquid discharge after the treatment of the standard.
3, the advantages of magnesium oxide cobalt refining
reactive magnesium oxide cobalt extraction process is a low-grade cobalt ore efficient recovery of cobalt method, the use of two-stage cobalt precipitation process to get qualified cobalt hydroxide, to achieve the use of low-grade cobalt ore resources, the active magnesium oxide cobalt extraction process has the following advantages over the existing technology:
1, the use of two-stage cobalt precipitation slag and fine grinding of low-grade cobalt ore combination of iron removal, on the one hand, to save the cost of iron removal chemicals and recovery of cobalt in the two-stage cobalt precipitation slag, on the other hand, pre-consumption of most of the carbonic acid in the fine grinding of low-grade cobalt ore, so that the iron removal of the neutralized slag back to the first step of the first step of the leaching of cobalt, a substantial reduction in the dosage of sulfuric acid.
2、Adopting special oxidizing agent to remove manganese, which is green, environmentally friendly, with high manganese removal efficiency and will not affect the quality of cobalt hydroxide products.
3、The production line formed by active magnesium oxide cobalt extraction process has the advantages of simple operation, strong adaptability, high cobalt recovery rate, good cobalt product quality, low production cost, environmental protection and so on, which can provide a broad space for the development of low-grade cobalt ore at home and abroad.