Abstract: Magnesium oxide inhibits the flow of polyhalide lithium salt electrolyte at high temperatures to ensure the safety of thermal batteries. The physical properties of different kinds of magnesium oxide materials are comparatively studied, and their adsorption performance on lithium salt electrolyte is analyzed by overflow experiments. The results show that the magnesium oxide material with small vibrational density and large specific surface area exhibits optimal adsorption performance.
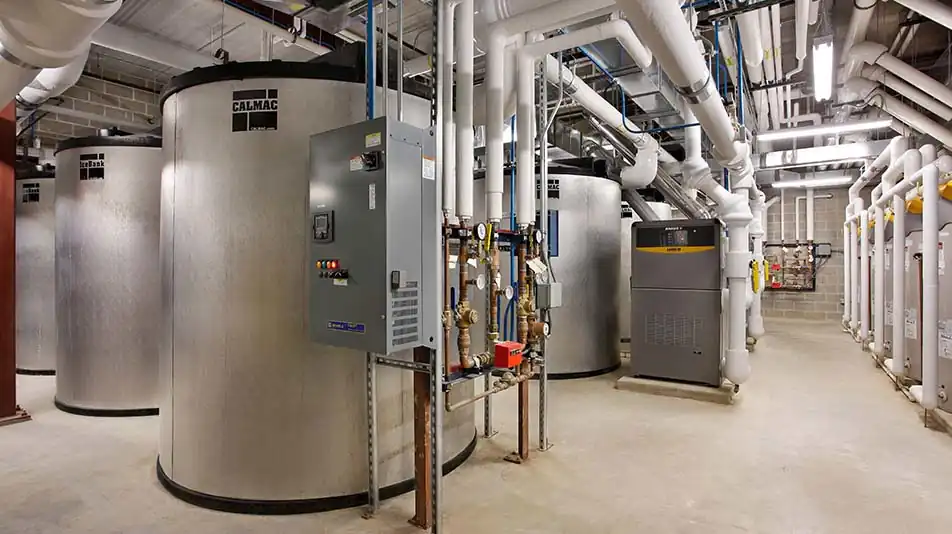
Keywords: thermal battery; magnesium oxide material; adsorption performance
As a kind of storage power source, the thermal battery transforms the salt electrolyte, which is non-conductive at room temperature, into an ionic conductor and enters into the working state through its own heating system. Thermal batteries are widely used in the field of artillery, missiles and other weapons and equipment because of their long storage life, good environmental adaptability, short activation time, high output power, wide range of operating temperatures and compact structure [1-2].
The single pole of thermal battery consists of heating material, positive pole, electrolyte and negative pole, etc. When the battery is activated, the heating material is ignited and starts to provide heat for the battery, and when the internal temperature of the battery is higher than the melting point of the electrolyte, the electrolyte melts, and forms an ionic path between the positive and negative electrodes, and starts to discharge when the external circuit is loaded with a load. However, due to the fluidity of the electrolyte in the molten state, it is easy to cause electrolyte leakage, accelerate self-discharge, and in serious cases, cause internal short circuit, laying a hidden safety hazard for the battery [3]. In order to inhibit the flow of electrolyte in the discharge process, the chemically inert adsorbent material is usually added to the electrolyte layer, and magnesium oxide, as the most commonly used flow inhibitor in the field of lithium thermal batteries, mainly through the capillary adsorption effect of the material itself, the molten state of the electrolyte is immobilized in the pore space of magnesium oxide material. The electrolyte flow inhibition effect will be enhanced with the increase of the addition ratio of magnesium oxide material, but when the magnesium oxide addition is too high, it will lead to the increase of the internal resistance of the thermal battery and the weakening of the pulse performance. Therefore, reducing the addition ratio of magnesium oxide material while achieving good electrolyte flow inhibition is a hot and difficult point in the study of flow inhibitors for thermal batteries, which puts higher requirements on various physicochemical properties of magnesium oxide materials.
This experiment compares and explores the differences between different kinds of magnesium oxide materials in terms of stacking density, particle size distribution, specific surface area, microscopic morphology, etc., and uses different kinds of magnesium oxide materials to prepare isolation powder for the overflow rate test of electrolyte, evaluates the adsorption effect of different magnesium oxide materials on electrolyte, and ultimately screens out the magnesium oxide materials with the best adsorption effect, in order to satisfy the application requirements of thermal batteries.
1 Experimental part
1.1 Physical property test of magnesium oxide material
This experiment selects four kinds of magnesium oxide materials prepared and synthesized by different precursor materials for comparative experimental investigation, the number of different kinds of magnesium oxide materials is 1#~4# in order. Biotek BT-303 vibration density tester was used to test the vibration density of magnesium oxide materials; Hitachi S-4700 scanning electron microscope (SEM) was used to analyze the micro morphology of magnesium oxide materials; Malvern Mastersizer 300 laser diffraction particle size analyzer was used to analyze the particle size of magnesium oxide materials; and Malvern Mastersizer 300 laser diffraction particle size analyzer was used to analyze the particle size of magnesium oxide materials. Malvern’s Mastersizer 300 laser diffraction particle size analyzer was used to characterize the particle size distribution of MgO materials; the specific surface area and pore volume of MgO materials were analyzed using the K100 Specific Surface Area Test System of Kreuz.
1.2 Electrolyte overflow experiment
In a dry environment, the magnesium oxide material was calcined at high temperature, and then the calcined magnesium oxide and the eutectic salt (LiCl-LiF-LiBr) were mixed according to a certain mass ratio, and placed in the powder mixing equipment for full dispersion, and the well-dispersed mixed powders were placed in a muffle furnace for high-temperature sintering, and then after being discharged from the furnace, the isolation powders were prepared by crushing. The isolation powder was pressed into a disk with a diameter of 40.0 mm and a thickness of 0.5 mm at a pressure of 6 MPa. The prepared segregation sheet was placed on the hot pressing equipment and held at a temperature of 500 ℃ for 10 min. After cooling, the mass of the segregation sheet overflow was weighed to determine the degree of electrolyte overflow.
2 Results and discussion
The four different types of magnesium oxide materials selected for this experiment were prepared by two processes, numbered from 1# to 4#, and a comparison of the preparation process and purity and other parameters of the materials are shown in Table 1. From Table 1, it can be seen that the magnesium oxide materials prepared by the brine ammonia method (1# and 2# samples) have higher purity and lower weight loss on scorching.
The vibration density of the magnesium oxide materials was comparatively tested using a vibration density tester, and the test results are shown in Fig. 1. From Fig. 1, it can be seen that the vibrational density of the 2# MgO material sample prepared by the brine ammonia method is the smallest, 0.32 g/cm3; the vibrational density of the 3# MgO material sample prepared by the carbonization calcination method is the largest, 0.51 g/cm3.
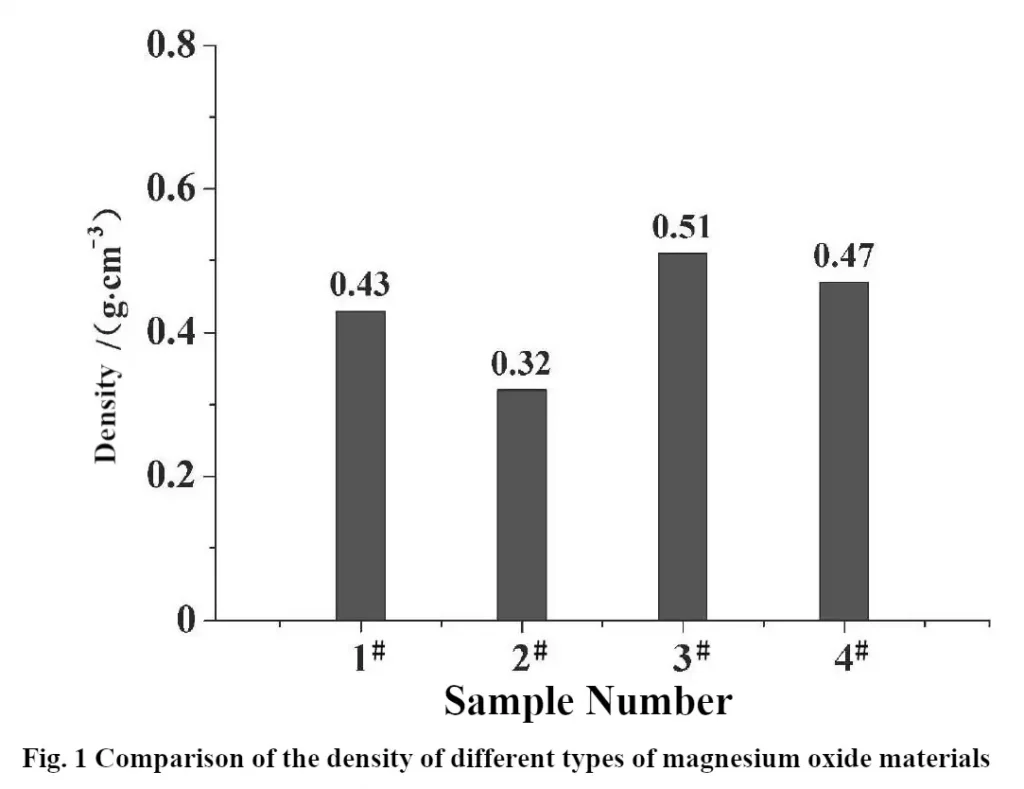
In order to further characterize the microscopic morphology of different kinds of magnesium oxide materials, the characterization analysis was carried out using an electron microscope. Figure 2 shows the SEM morphology of different types of magnesium oxide materials, under the same magnification, the micro-morphology of magnesium oxide samples varies significantly. 1# and 2# samples have similar morphology, which is nano-spherical morphology, but there is a certain degree of agglomeration between the particles; 3# samples have a micron-sized flake morphology, but there is a large difference in the size of different flake materials; 4# samples are composed of nano-particles and micron-sized flake material agglomerates, and there are large holes between the particles. The sample #4 is composed of nanoparticles and micron-sized flakes, and there are large pores between the particles.
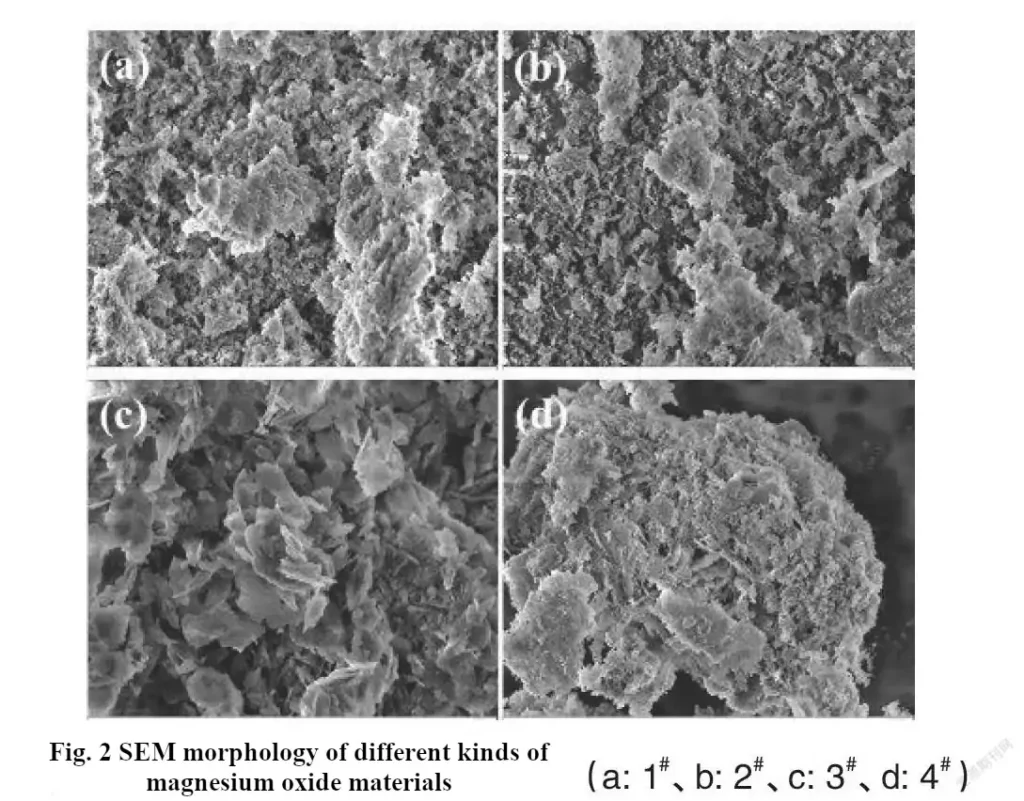
A laser diffraction particle size analyzer was used to characterize the particle size distribution of the magnesium oxide material, and the results are shown in Figure 3. As can be seen from Fig. 3, the particle size distribution of 1# and 2# MgO samples prepared by brine-ammonia method is more concentrated and approximately normally distributed, with the median particle sizes of 9.2 and 12.4 μm, respectively, and the particle size distributions of 3# and 4# MgO samples prepared by carbonization-calcination method are wider, with a D90 of up to 34.3 and 27.6 μm, respectively, and the results are consistent with those of SEM tests, suggesting that the 1# and 2# MgO samples are characterized by a large number of particle sizes, with the D90 reaching up to 34.3 and 27.6 μm, respectively. The results of the particle size distribution test are also consistent with the SEM test results, indicating that 1# and 2# samples have smaller particle sizes and fewer particle agglomerations compared with 3# and 4# samples.
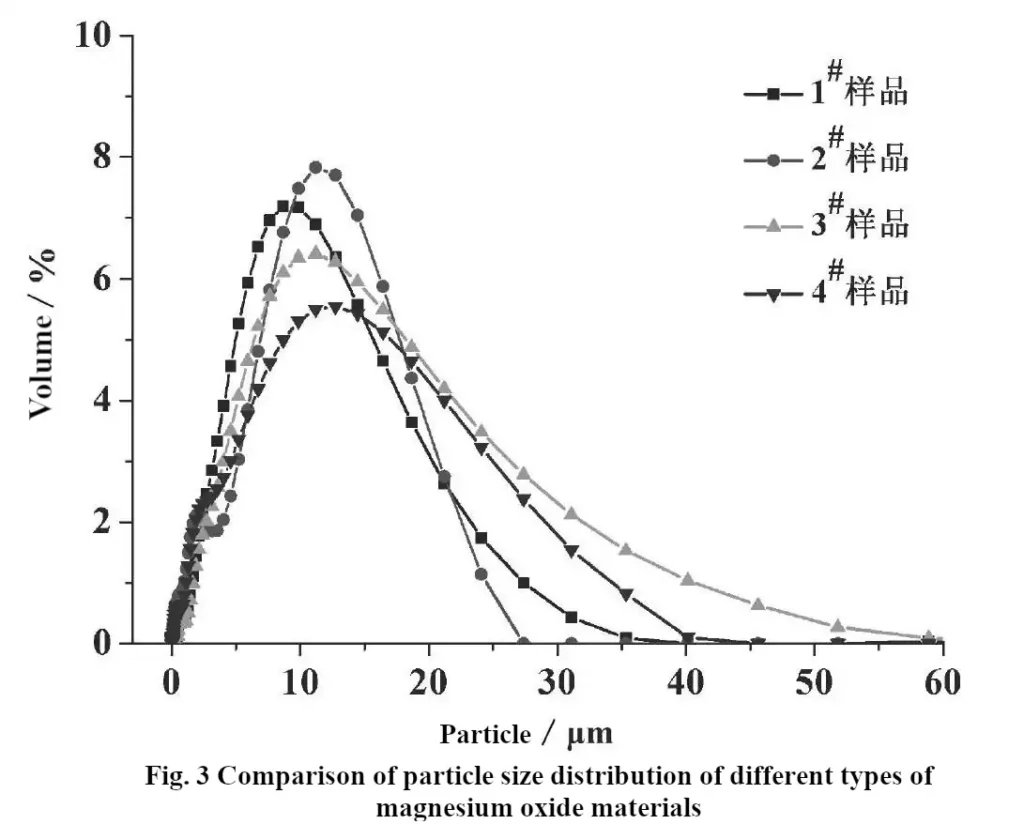
The comparative test results of specific surface area and pore volume of MgO samples from 1# to 4# are shown in Table 2. As can be seen from Table 2, 2# MgO samples have the largest specific surface area up to 55.17 m2/g and the pore volume up to 0.51 cm3/g; while 3# MgO samples have the specific surface area of only 32.62 m2/g and the pore volume of 0.17 cm3/g, which indicates that there are large differences in the specific surface area and the pore volume of the different MgO materials. This test result is also consistent with the results of the vibration density test in Fig. 1, indicating that the smaller the packing density of MgO materials, the fluffier their internal structure and the larger the pore volume. Relevant research literature shows that the specific surface area characteristic parameter of magnesium oxide material has a significant effect on the overflow of the final prepared segregation powder [3], and the 2# magnesium oxide sample has a better adsorption performance due to its maximum specific surface area and pore volume.
In order to further investigate the relationship between the microstructure and adsorption performance of different magnesium oxide materials, the 1# to 4# magnesium oxide samples were respectively subjected to high-temperature calcination treatment in a dry environment, and subsequently, the calcined magnesium oxide and eutectic salts were mixed according to a certain mass ratio, and placed in a powder mixing equipment for full dispersion, and the well-dispersed mixed powders were placed in muffle furnaces for high-temperature sintering, and after being discharged from the furnace The isolated powder was crushed to obtain the isolated powder, and the serial numbers of the isolated powder were still labeled as 1# to 4# in sequence. Subsequently, the isolation powder from 1# to 4# was pressed into a disk with a diameter of 40.0 mm and a thickness of 0.5 mm at a pressure of 6 MPa. The prepared isolation sheet was placed on the hot pressing test equipment and held at 500 ℃ for 10 min. After cooling, the mass of the overflow of the isolation sheet was weighed and the ratio of the overflow to the total mass of the pole piece was calculated to judge the degree of electrolyte overflow. The results of the overflow rate test are shown in Fig. 4. From Fig. 4, it can be seen that 2# isolation powder presents the best thermal stability and has the lowest overflow rate of 2.35% after the hot pressing test; while 3# isolation powder has the highest overflow rate of 5.24% after the hot pressing test. The results of the overflow rate test show that the 2# magnesium oxide material has a strong adsorption performance on the electrolyte [4].
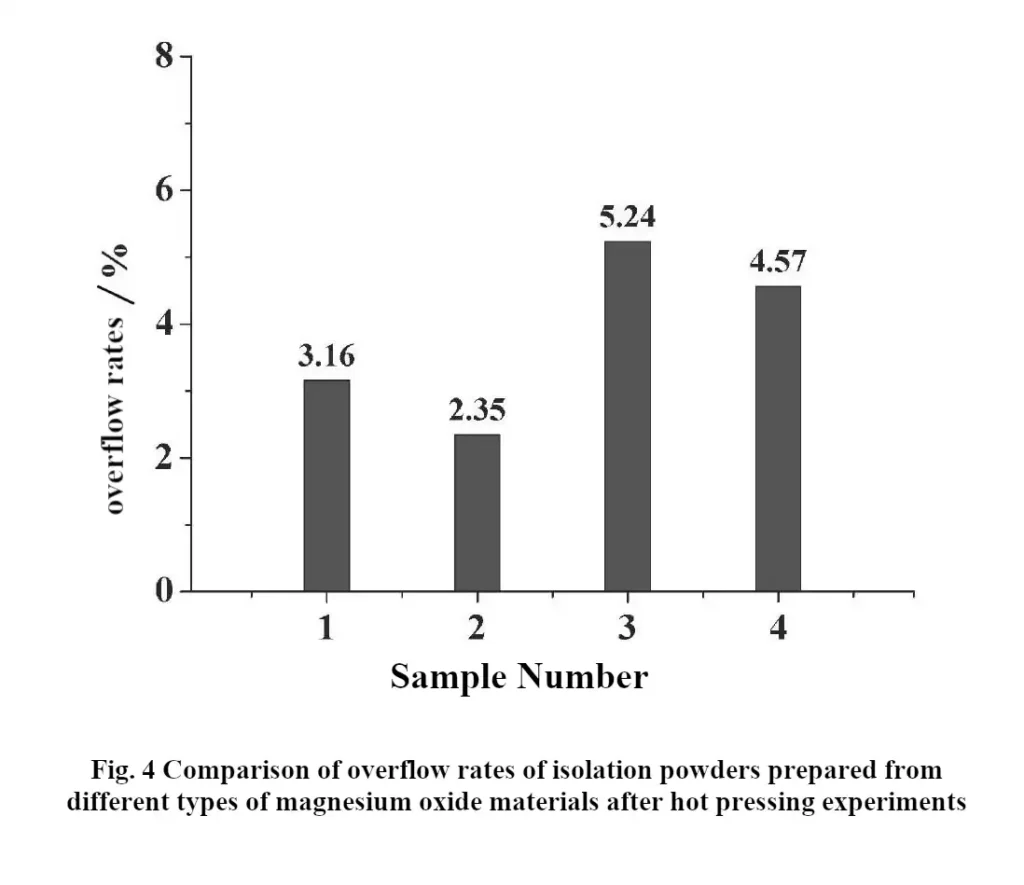
3 Conclusion
The adsorption performance of different kinds of magnesium oxide materials on electrolyte was studied, and the results showed that the magnesium oxide materials with small solid density and large specific surface area had the best adsorption performance on electrolyte. The 2# magnesium oxide sample prepared by hydrochloromagnesite raw material by brine ammonia method has a vibration density of only 0.32 g/cm3, and the micro morphology is nano-spherical, and there is a certain degree of agglomeration between the particles, and the distribution of the particle size is more centralized, and its specific surface area can reach 55.17 m2/g, and the use of this magnesium oxide sample to prepare the isolation powder showed the lowest overflow rate in the hot pressing experiment, which indicates that the isolation powder can meet the hot cell It shows that the isolation powder can meet the application requirements of thermal batteries.
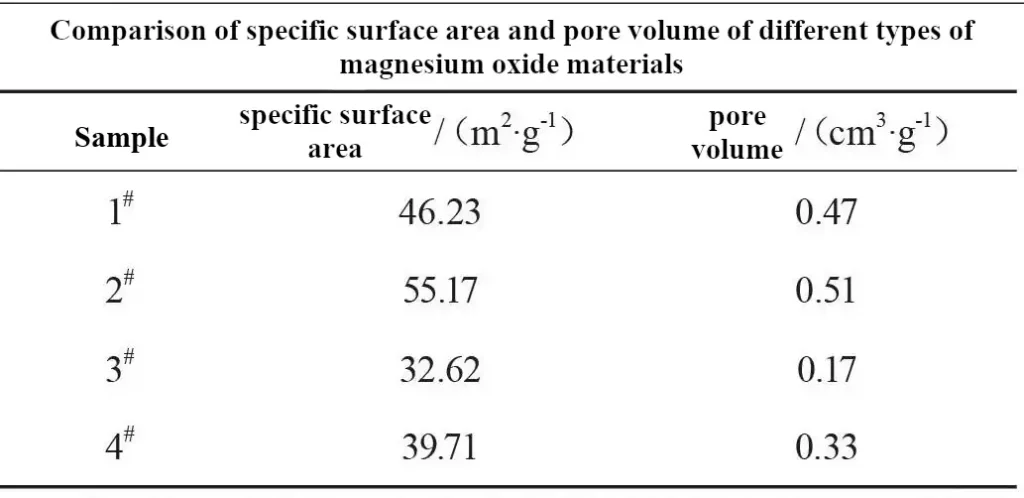