Magnesium hydroxide is an important inorganic chemical with the appearance of white amorphous powder. It occupies an important position in the development of modern economy. It plays an important role in environmental protection (such as flue gas desulfurization, wastewater neutralization, coal-fired sulfur fixation, heavy metal removal, etc.), material processing (such as fine ceramics, coatings, flame retardants, electronic materials), medical care, food processing, etc.
Compared with organic flame retardants, inorganic flame retardants have obvious advantages – they will not produce a large amount of harmful and toxic gases in case of fire, providing convenient conditions for people to escape. In addition, magnesium hydroxide has the advantages of non-toxicity, smoke suppression, high temperature resistance, and low cost. It is a green and environmentally friendly flame retardant. Next, I will introduce its flame retardant mechanism and characteristics:
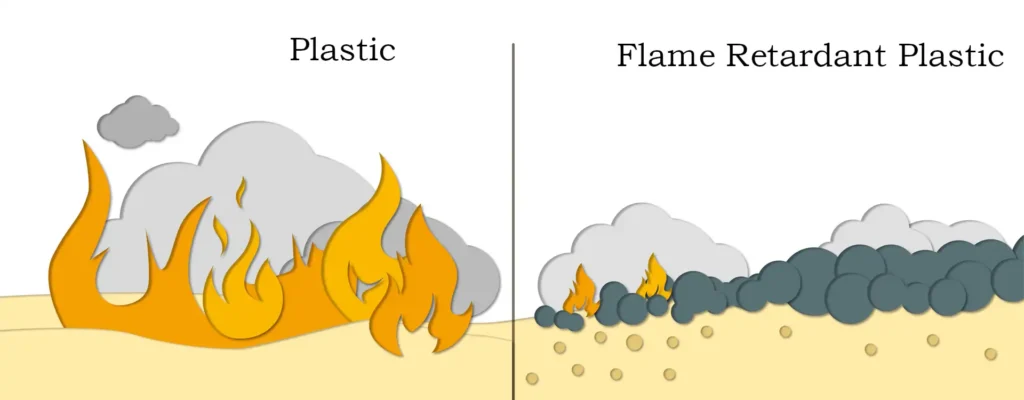
1. Magnesium hydroxide will decompose and produce a large amount of water vapor when heated, thereby diluting the concentration of oxygen and preventing combustion to a certain extent;
2. Magnesium hydroxide has the characteristics of large thermal melting point, which can effectively reduce the absorption of heat energy of polymer substrate during thermal decomposition, thereby delaying the thermal decomposition of the polymer substrate itself;
3. The surface carbonization layer formed by magnesium hydroxide itself has the effect of delaying combustion to a certain extent, and can further inhibit the combustion of gas;
4. Magnesium hydroxide needs to absorb a lot of heat when decomposing, which can reduce the temperature of the flame-retardant material to a certain extent, which is conducive to reducing the decomposition rate of the polymer;
5. Magnesium hydroxide will decompose and generate magnesium oxide when heated. As we all know, magnesium oxide is a high-quality refractory material. Covering the surface of the polymer substrate is conducive to isolating air and blocking combustion.
6. If magnesium hydroxide is used as a flame retardant, a large amount of addition is required to achieve the effect of improving the flame retardancy of the polymer.
As an inorganic additive flame retardant, magnesium hydroxide requires a relatively large amount of addition to achieve a high flame retardant effect. This has brought negative impact on the mechanical properties of materials to some extent. To solve this problem, the research on magnesium hydroxide is mainly carried out from the aspects of surface polarity, low agglomeration, ultrafineness, etc., so as to improve its effect and cost performance.
When ultrafine magnesium hydroxide is not treated, it belongs to thermodynamic metastable state, and its surface has hydrophilic and oleophobic characteristics. It is very easy to agglomerate and it is difficult to achieve uniform dispersion in organic medium, which will reduce certain properties of polymers and make the products unusable. Therefore, the surface of magnesium hydroxide should be modified to improve its hydrophobic properties to improve the dispersibility and compatibility of the two.
The surface modification methods for magnesium hydroxide mainly include chemical modification, microencapsulation modification, and surface grafting modification. Among them, the modifiers in the surface chemical modification include coupling agents, composite modifiers and surfactants. The modification technology of microcapsules can keep magnesium hydroxide in good thermal stability, improve the interfacial viscosity of polymer polar bodies and powders, and improve the mechanical properties of its modified materials. The surface grafting modification method refers to grafting the modifier onto the polymer surface to form a macromolecular modifier, which can effectively improve the surface properties of the polymer material. After modification, the properties of magnesium hydroxide itself are also greatly changed, reducing its water absorption rate to 25%-70%, while the hydrophobicity is enhanced.
Coupling agent modification refers to the coupling chemical reaction between the coupling agent and the ultrafine powder, which produces hydrogen bonds, coordination bonds or van der Waals interactions and the combination of covalent bonds and ionic bonds. The coupling agent molecule needs to have two groups: compatibility or reactivity with organic matter and reaction with nano inorganic particles. Through this modification method, low surface energy organic matter and high surface energy nano particles have better affinity. Due to different central atoms, coupling agents can be divided into titanate coupling agents, silane coupling agents, zirconate coupling agents, aluminate coupling agents, aluminum titanium composite coupling agents, zirconium aluminate coupling agents, etc.
Surfactant modification-the molecular structure of this modifier has the characteristics of hydrophilic and hydrophobic groups. There are many types of surfactants, such as cationic, anionic and nonionic, including higher fatty acids, amines, alcohols, etc. One end of this molecule is a long-chain alkyl group, which is similar to the structure of polymer molecules, and the other end is an ether group, amino group, carboxyl group and other groups, which can produce chemical or adsorption reactions with magnesium hydroxide. With the characteristics of surfactants, they can produce affinity with polymers, thereby inhibiting the agglomeration characteristics of magnesium hydroxide itself, so the magnesium hydroxide modified by this method has good dispersibility in plastics and rubbers.
Polymer surface grafting modification is one of the commonly used modification methods. The particle surface of some inorganic powders has the characteristics of free radical reaction. Under appropriate circumstances, active monomers belonging to high molecular polymers can use this characteristic to graft on the surface of its particles, and then initiate polymerization reactions. The long chain of the polymer is grafted on the surface of its powder, and the hydrophilic group in the polymer has a three-dimensional shielding effect in the water medium. This method can reduce the degree of agglomeration after grafting and increase its dispersion stability. The polymer modifiers of this modification method include terpolymers, polyacrylic acid (salt), etc.
There are two methods for evaluating the surface modification of magnesium hydroxide: direct method and indirect method.
The direct method refers to observing the finished product performance of the modified powder, such as the impact strength, oxygen index, tensile strength, flexural strength, elongation, melt rheology, heat deformation temperature and other parameters of the final product. The disadvantage of this method is that the process and route are relatively complicated.
The indirect method refers to using the parameters of the modified material to determine its effect, such as viscosity, contact angle, average particle size, and lipophilicity. Its advantage is that this method reflects its modification effect intuitively and simply. Some advanced testing and analysis methods can also be used for evaluation, such as differential thermal analysis (DTA), infrared spectroscopy, Auger spectroscopy, energy spectrum analysis and scanning electron microscopy (SEM), to analyze the uniformity, structure, chemical element changes and thickness of the surface modification, and use adsorption tests, activation index, Zeta potential, sedimentation properties, etc. to evaluate the effect of its surface modification.
Summary: The surface modification technology of magnesium hydroxide is closely related to many disciplines, including organic chemistry, colloid chemistry, modern instrumental analysis and testing, nanomaterials, crystallography and many other fields. Its modification methods, modification mechanisms and equipment, modification effect characterization technology and many other aspects still need further in-depth research and improvement.