Magnesium carbonate has a wide range of applications in foamed materials, and its unique properties and advantages make it an important component in various foaming systems. With the continuous advancement of technology and the expanding application fields, the use of magnesium carbonate in foamed materials will become even more extensive and in-depth.
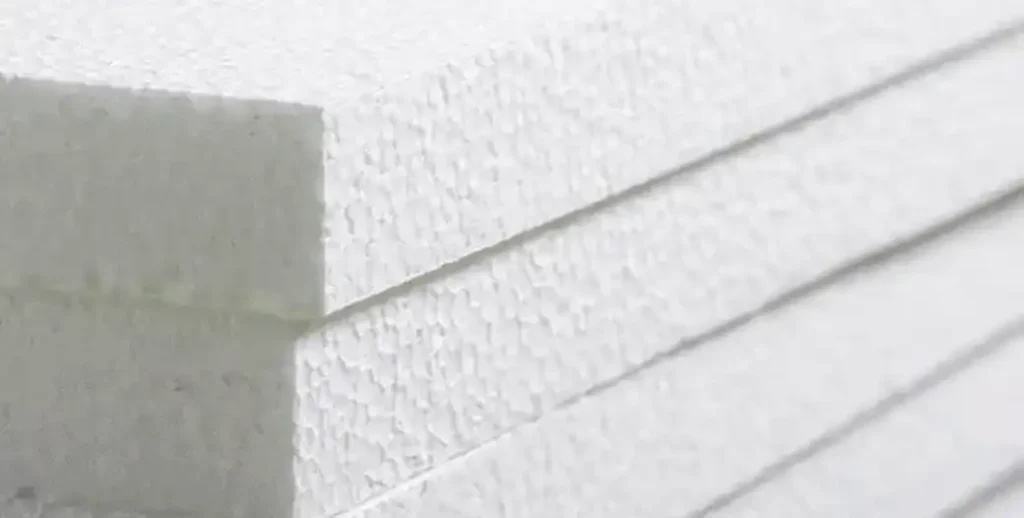
I. Basic Properties of Magnesium Carbonate
Magnesium carbonate (MgCO3) is an important inorganic compound characterized by its non-toxicity, harmlessness, and pollution-free nature. It possesses good anti-scaling and acid-alkali resistance properties, and its gentle physical properties make it a dispersible alkaline powder. These properties enable magnesium carbonate to play a significant role in foamed materials.
II. Applications of Magnesium Carbonate in Foamed Materials
As an Inorganic Foaming Agent
Magnesium carbonate decomposes to produce carbon dioxide (CO2) gas when heated or subjected to other stimuli. These gases form bubbles within the foamed material, causing it to expand and achieve a foamed effect.
The foaming effect of magnesium carbonate depends on its decomposition temperature and gas generation volume. A lower decomposition temperature allows the foaming agent to decompose more easily upon heating, generating bubbles; a larger gas generation volume results in a more pronounced expansion of the foamed material.
Improving the Performance of Foamed Materials
Magnesium carbonate can enhance the stability and heat resistance of foamed materials, allowing them to maintain good foaming effects even in high-temperature environments.
Magnesium carbonate can also interact with other components to form more stable compounds, thereby improving the overall performance of the foamed material.
Reducing Production Costs
Magnesium carbonate is relatively low in cost, and using it as a foaming agent can effectively reduce production costs.
Through reasonable formulation design, the use of magnesium carbonate can also improve product performance, achieving an optimal balance between performance and cost.
III. Specific Application Areas of Magnesium Carbonate in Foamed Materials
Construction Industry
Magnesium carbonate foaming agents are commonly used to prepare lightweight, high-strength building materials such as foamed concrete and foamed gypsum. These materials have excellent thermal insulation, sound insulation, and sound absorption properties and can be used for insulation layers in walls, roofs, and floors.
Packaging Industry
Magnesium carbonate foaming agents are used to produce various packaging materials, such as foam plastics and foam rubber. These materials are lightweight, soft, and shockproof, making them suitable for protecting fragile and valuable items during transportation.
Other Industries
Magnesium carbonate foaming agents can also be used to prepare various other lightweight, high-strength materials, such as foam glass and foam ceramics. These materials have broad application prospects in aerospace, automotive manufacturing, and the electronics and electrical appliance industries.
IV. Advantages of Magnesium Carbonate Foamed Materials
Lightweighting
The foaming characteristics of magnesium carbonate can significantly reduce the density of materials, thereby improving the lightweighting of products. This property is particularly important in the construction and packaging industries, as it can reduce transportation costs and structural burdens.
Thermal Insulation Performance
The foamed structure of magnesium carbonate has good thermal insulation properties, which, when applied in building materials, can effectively reduce energy loss and improve the energy efficiency of buildings.
Enhanced Mechanical Properties
In plastics and rubber, the foaming action of magnesium carbonate can improve the impact resistance and flexibility of the materials, enhancing the durability of products.
Environmental Friendliness
As a non-toxic and harmless inorganic compound, the use of magnesium carbonate meets modern environmental requirements. Its low emission of volatile organic compounds (VOCs) during the foaming process helps to reduce its environmental impact.