Magnesium carbonate exhibits a double-edged effect on the mechanical properties of UV inks. Appropriate usage can enhance adhesion, hardness, and abrasion resistance, while excessive addition may lead to decreased flexibility, impaired adhesion, and even ink film cracking. Its performance is jointly influenced by factors such as particle size, dosage, dispersion state, and the overall formulation structure. Formulators must skillfully navigate these elements to achieve an optimal property balance.
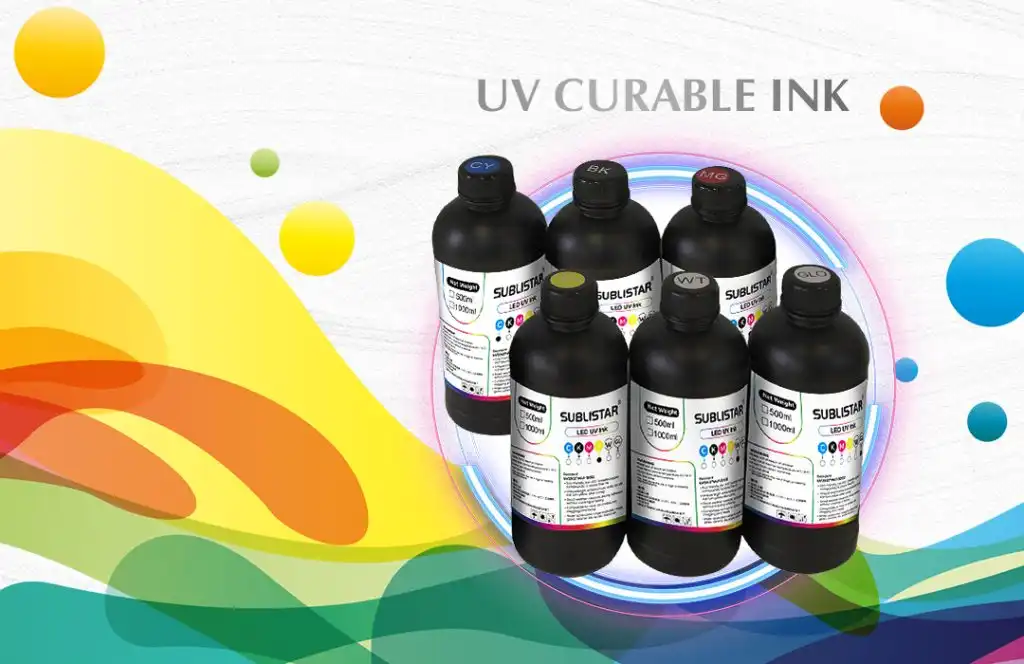
I. Adhesion
With appropriate addition, magnesium carbonate can enhance ink adhesion through mechanical interlocking created by microparticles between the ink film and the substrate. This particulate structure helps the ink film “grip” the surface, especially on rough or poorly receptive substrates. Simultaneously, magnesium carbonate can optimize the ink’s rheology, allowing for a more uniform spread of the ink film, which contributes to the formation of a strong adhesive layer.
However, if magnesium carbonate is added in excess or poorly dispersed, it can easily create micro-voids or weak interfacial layers between the ink and the substrate, thereby reducing adhesion. This is particularly prone to causing delamination or edge lifting issues on low surface energy materials such as plastics and metals.
II. Flexibility
Magnesium carbonate is a rigid particle and lacks flexibility or elasticity. Therefore, incorporating a certain amount of magnesium carbonate into the cured ink film will make the overall film more “hard and brittle,” reducing its flexibility and elongation. For applications requiring flexibility (e.g., flexible packaging, bendable labels, soft plastics), the addition of magnesium carbonate must be strictly controlled.
Nevertheless, under conditions where the resin system itself is relatively soft and possesses strong binding power, a small amount of magnesium carbonate may not cause a significant impact and can even help improve structural stability.
III. Hardness
Magnesium carbonate can effectively increase the surface hardness of UV ink films. As an inorganic mineral powder dispersed within the cured ink film, it essentially “embeds a skeleton” within, making the surface more resistant to pressure and scratching. This has a positive effect on properties such as scratch resistance, fingerprint resistance, and anti-blocking, making it particularly suitable for applications like packaging printing, labels, and decorative films.
However, increasing hardness typically comes at the expense of flexibility. Therefore, in situations requiring a balance between both properties, a comprehensive adjustment of the resin ratio and additive system is necessary.
IV. Abrasion Resistance
Magnesium carbonate itself does not possess self-lubricating properties, but its microstructure helps improve the abrasion resistance of the ink film. By strengthening the surface microstructure, it can reduce the contact area during friction, slowing down the wear rate. The effect is more pronounced with high filler loading or when combined with other reinforcing materials.
However, if the particles are too large or poorly dispersed, magnesium carbonate can instead create rough, easily detached areas on the surface, leading to decreased abrasion resistance. Therefore, controlling particle size distribution and dispersion state is crucial.
V. Impact and Shear Strength
These two properties are mainly related to the overall structural integrity of the ink film. As a non-reactive filler, magnesium carbonate does not form chemical cross-links within the cured network and acts as a “physically embedded” reinforcing agent. When used in appropriate amounts, it can strengthen the ink film structure and improve its resistance to deformation. However, excessive usage or uneven particle distribution can lead to internal structural defects, resulting in brittleness, cracking, and other issues, which are more apparent in thick film applications.