In hydrometallurgical processes, the precipitation of nickel (Ni) and cobalt (Co) from solution typically involves adjusting the pH to induce their precipitation as hydroxides. Magnesium oxide is a commonly used precipitant that can raise the solution’s pH and assist in the precipitation of metal ions. Its purity directly affects the effectiveness of the precipitation reaction, impurity control, and the quality of the final product.
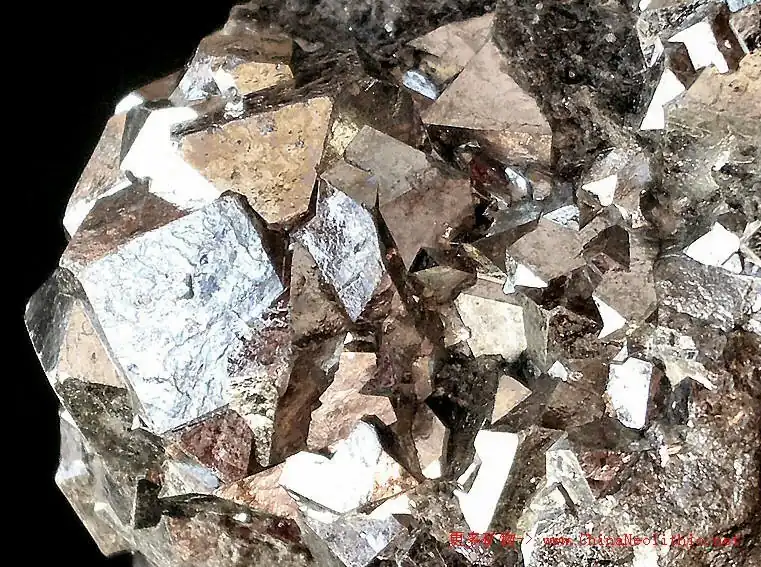
1. Impact of Impurities on the Reaction
Low-purity magnesium oxide often contains impurities such as CaO, Fe₂O₃, Al₂O₃, SiO₂, etc. These impurities may react with metal ions in the solution or form colloids, leading to co-precipitation or incomplete precipitation reactions.
High-purity magnesium oxide can significantly reduce the introduction of impurities, improving the selectivity and purity of nickel and cobalt hydroxide precipitation.
2. Differences in pH Control Capability
Impure magnesium oxide (especially those containing CaO) will release more OH⁻ during hydrolysis, potentially causing excessively high local pH. This can lead to rapid precipitation or clumping of the precipitate, reducing recovery efficiency.
High-purity magnesium oxide has a more controllable dissolution rate and provides more stable pH regulation, which helps in forming precipitates with a reasonable particle size distribution that are easy to filter.
3. Comparison of Precipitate Quality
When using low-purity magnesium oxide, the precipitate tends to have a loose structure and high impurity content due to the interference of impurities. This affects the quality of subsequent calcination or electrolysis products.
Ni(OH)₂/Co(OH)₂ crystals precipitated using high-purity magnesium oxide have a more regular crystal structure, which is beneficial for subsequent process treatments.