Messi Biology states that magnesium carbonate has complex and multifaceted effects on the processing performance of PVC. Appropriate amounts of magnesium carbonate can improve aspects like the thermal stability, processing flowability, mechanical properties, and surface quality of PVC. However, excessive addition may lead to increased material brittleness or other negative effects. In practical applications, the amount of magnesium carbonate added needs to be reasonably controlled according to the specific requirements of PVC products to achieve optimal processing performance and product quality. Specifically, the impact of magnesium carbonate on PVC processing performance can be discussed from the following aspects:
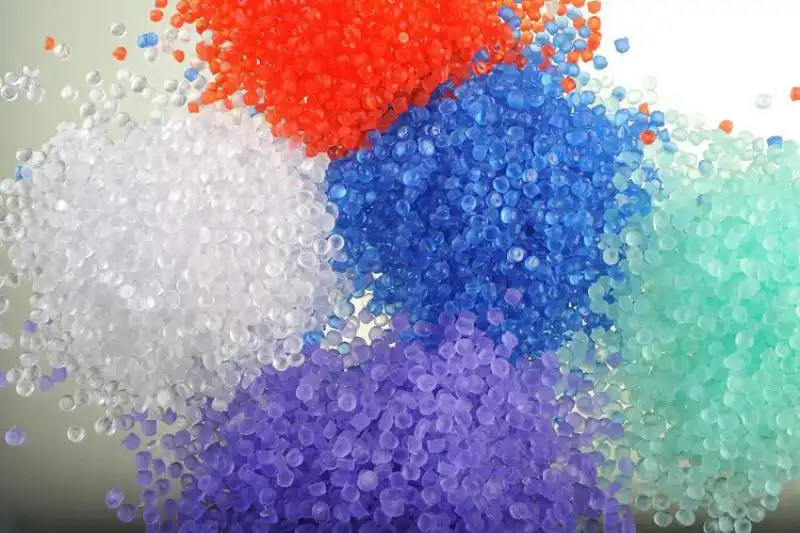
- Improving Processing Stability
Magnesium carbonate, as an inorganic filler, possesses good thermal stability and chemical inertness. It can effectively improve the stability of PVC during processing, especially its thermal stability at high temperatures. The addition of magnesium carbonate can help mitigate thermal decomposition, reduce the degradation of PVC molecular chains, and extend the service life of PVC during processing. - Enhancing Mechanical Properties
When added to PVC as a filler, magnesium carbonate can enhance the material’s rigidity and hardness. Magnesium carbonate itself has certain filling properties and can increase the tensile strength and flexural strength of PVC. However, the increased rigidity may lead to a decrease in the toughness of PVC, especially in low-temperature environments where PVC may become more brittle. Therefore, when selecting the amount of magnesium carbonate to add, it is necessary to balance the relationship between rigidity and toughness. - Improving Flowability and Processability
Magnesium carbonate can improve the flowability of PVC, especially during processing methods like extrusion and injection molding. Because magnesium carbonate particles are fine and have a relatively regular shape, they can form a good dispersion state in PVC, thereby reducing the viscosity of the melt and improving its flowability during processing. This has a positive effect on improving production efficiency and reducing energy consumption during processing. - Reducing Costs
Magnesium carbonate is an inexpensive filler. Its relatively low cost enables it to effectively reduce the production costs of PVC products. By mixing magnesium carbonate with PVC, the use of other high-cost materials (such as plasticizers, antioxidants, etc.) can be reduced, thereby saving production costs. - Improving Surface Quality
Regarding the surface treatment of PVC, the addition of magnesium carbonate can sometimes improve the surface smoothness of the material and reduce the appearance of surface defects. It can also, to some extent, improve the wear resistance and scratch resistance of PVC. Especially for PVC products requiring high durability (such as pipes, window frames, etc.), the use of magnesium carbonate can enhance their surface quality. - Influencing Processing Temperature and Cooling Rate
The addition of magnesium carbonate may have an impact on the processing temperature of PVC. In some cases, magnesium carbonate can help reduce the melt temperature during processing, decrease the risk of thermal decomposition, and thus improve the control of processing temperature. At the same time, the addition of magnesium carbonate may also affect the cooling rate, as it has good thermal conductivity, which helps in the uniform distribution of heat. - Influence on Plasticizers
The application of magnesium carbonate in PVC may affect the selection and amount of plasticizers used. Due to its relatively high specific surface area, magnesium carbonate can sometimes adsorb part of the plasticizer, thereby affecting the flexibility and softening properties of PVC. Therefore, when using magnesium carbonate, it is necessary to adjust the plasticizer formulation appropriately to ensure that the final product performance meets the desired requirements.