In order to recover cobalt and copper from the copper extraction residue of a wet process copper refinery in DRC and to realize the recycling of the residue, iron removal – copper precipitation – the first section of cobalt precipitation – the second section of cobalt precipitation process was used to treat cobalt-containing copper extraction residue. The results show that the process was used to obtain iron slag, copper slag, crude cobalt hydroxide and the second cobalt slag, the calcium content of iron slag is 26.79%, the copper content is 0.05%, cobalt content is 0.12%, and the loss rate of copper and cobalt in the process of removing iron is 4.64% and 3.14%, respectively; the copper slag contains copper of 3.74% and cobalt of 2.06%; the cobalt content of crude cobalt hydroxide is 32.83%; the second cobalt slag contains cobalt of 7.14%; the total cobalt content of cobalt is 7.14%, and the total cobalt content of cobalt is 7.14%. 7.14%; the total recovery rate of cobalt is more than 95%. Iron slag is used for building materials, copper slag is returned to the leaching system to recover copper and cobalt, crude cobalt hydroxide can be sold directly, the second cobalt slag by extracting the residual liquid slurry to return to the iron removal process, the second cobalt precipitation solution is used back as a refill of water for milling, valuable metals and waste water after treatment have been utilized as resources. Tested by production practice, the treatment process has good economic, environmental and social benefits.
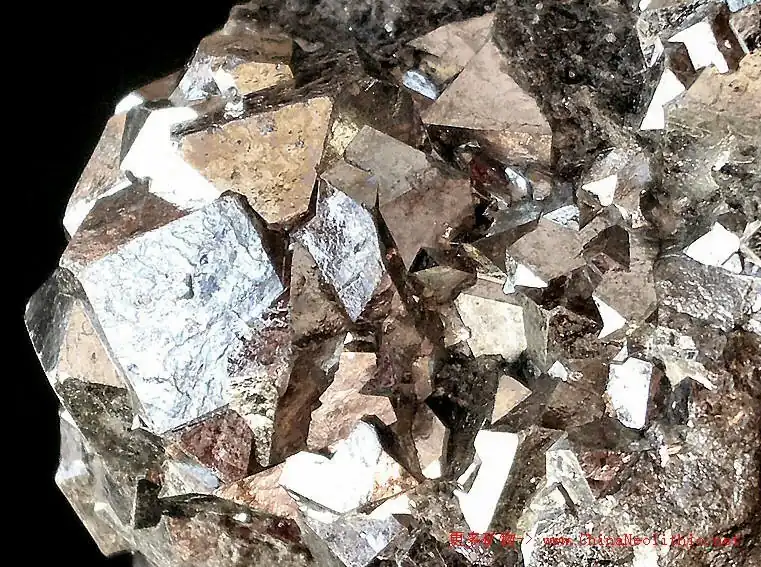
The copper and cobalt ores now developed in DRC are mainly oxidized ores, and the treatment methods mainly include fire method and wet method. In the process of wet leaching of copper from oxidized copper and cobalt ores, it is necessary to add a certain amount of reductant to reduce the cobalt in the leaching, and after the leach solution extracts the copper, the residual solution usually contains a certain concentration of copper, cobalt, nickel, iron, calcium, magnesium, manganese, silica and H2SO4, etc. Most of the local cobalt recoveries are made from the cobalt in the leaching process. Most of the local cobalt recovery enterprises recover cobalt from the extracted liquid by part of the open-circuit process, that is, after removing impurities and using one or two-stage cobalt precipitation process to recover cobalt, after precipitating cobalt solution precipitation of magnesium, the defects of the process is that the copper is not precipitated, and copper into the cobalt product is not counted in the sale of copper, which results in copper loss; precipitation of cobalt solution to add a large amount of lime precipitation of magnesium, magnesium precipitation solution with a high pH value, before discharging into the tailing pond or reuse to be consumed before the consumption of a large amount of acid, the cost of treatment is high. High cost of treatment. In a wet copper refinery in Congo (DRC), the cobalt ion concentration in the copper extraction residue is low (generally around 1g/L), the impurity manganese content is high, the acidity is high ( H2SO4 mass concentration 18-20g/L), iron mainly exists in Fe3+, and Fe2+ content is very small. In view of the current low cobalt concentration of copper extractive residue treatment process problems, this paper studies the copper extractive residue by removing iron and then precipitation of copper, the use of two-stage precipitation method to recover cobalt, cobalt precipitation after the second section of the solution does not go through the lime magnesium precipitation, and directly return to the grinding process of the new process to improve the total recovery of cobalt, and has achieved good economic, environmental and social benefits.
The treatment process of cobalt-containing copper extraction solution is as follows: iron removal – copper precipitation – cobalt precipitation in the first stage – cobalt precipitation in the second stage. Iron removal is to add milk of lime under stirring conditions to adjust the PH value of the solution, and at the same time, air, so that iron in the form of Fe(OH)3 precipitation; precipitation of copper is to add milk of lime under stirring conditions to adjust the pH value of the solution after the removal of iron, copper is removed in the form of Cu(OH)2; the first precipitation of cobalt is the appropriate amount of activated magnesium oxide is slowly added to the solution after the precipitation of copper to control the PH value of the solution, and then filtration after a period of time after the reaction, the slag is dried to obtain the crude hydrogen oxide. The first stage of cobalt precipitation is to slowly add appropriate amount of activated magnesium oxide into the solution after copper precipitation, control the pH value of the solution, filter after a period of reaction, and get crude cobalt hydroxide after drying the filter residue; the second stage of cobalt precipitation is to add lime milk into the solution after cobalt precipitation, control the pH value, so as to make cobalt precipitation in the solution after cobalt precipitation in the first stage complete, and then filter after a certain period of time after the reaction; the second stage of cobalt precipitation is to return to the milling system to investigate its effect on production.
The main reactions of iron removal are as follows:
Ca(OH)2 + H2SO4 → CaSO4 + 2H2O (1)
Fe2(SO4)3+3Ca(OH)2→2Fe(OH)3↓+3CaSO4 (2)
The main reaction of copper precipitation is as follows:
CuSO4 + Ca(OH)2 → Cu(OH)2 ↓ + CaSO4 (3)
The main reaction of cobalt precipitation in the first section is as follows:
The main reaction of the second stage of cobalt precipitation is as follows:
Ca(OH)2 + MnSO4 → Mn(OH)2 ↓ + CaSO4 (7)
Ca(OH)2+CoSO4→Co(OH)2↓ +CaSO4 (8)
The mass concentrations of copper, iron and free sulfuric acid were determined by chemical methods, while cobalt, manganese, calcium and magnesium were determined by atomic absorption spectrometry.
Conclusions and recommendations
(1) It is feasible to adopt the new process of “removing iron, precipitating copper, precipitating cobalt in the first stage, precipitating cobalt in the second stage, and returning the solution after precipitating cobalt in the second stage to the grinding process” to deal with the low cobalt-containing copper extracted liquid, and both copper and cobalt, the valuable metal elements, are obtained. The new process is feasible to treat the low cobalt content copper extract, and the valuable metal elements of copper and cobalt are recovered. The solution after cobalt precipitation in the second section is used as make-up water for grinding, which greatly reduces the amount of new water and alleviates the problem of water expansion in the wet copper refining system. The total cobalt recovery rate is high when this process is used to treat low cobalt concentration copper extracted liquid.
(2) Due to the low cobalt concentration in the extracted liquid, the direct cobalt recovery rate is low, and the cobalt concentration in the extracted liquid can be increased to improve the direct cobalt recovery rate and the output of crude cobalt hydroxide products, and to reduce the cost of production per unit of product.
(3) Adopting the new process of “removing iron, precipitating copper, precipitating cobalt in the first section, precipitating cobalt in the second section, and returning the cobalt precipitation solution to the milling process in the second section” to deal with the low cobalt-containing copper extractive liquor has been proved to have good economic, environmental and social advantages. The new process of treating low cobalt-containing copper extract has been proved to have good economic, environmental and social benefits.