Description
A method for preparing nano-grade high-purity light magnesium carbonate
Technical field
The present invention relates to a process for preparing nano-grade high-purity light magnesium carbonate from industrial-grade magnesium hydroxide coarse powder, belonging to the field of fine chemicals.
Background technology
Light magnesium carbonate is a white monoclinic crystal or amorphous powder, non-toxic, odorless, and stable in the air. It has the characteristics of non-combustion and light texture, and can be used for heat insulation, high-temperature resistant fireproof and heat preservation materials. Asbestos-grade light magnesium carbonate is an excellent insulating material, used in shipbuilding and boiler manufacturing and other departments, and can also be used to manufacture high-grade glass products, magnesium salts, pigments, paints, flame-retardant coatings, printing inks, ceramics, cosmetics, toothpaste and other daily chemicals and pharmaceutical products. Food-grade light magnesium carbonate can be used as a flour additive, and can also be used as a desiccant, color preservative, carrier, anti-caking agent, etc.
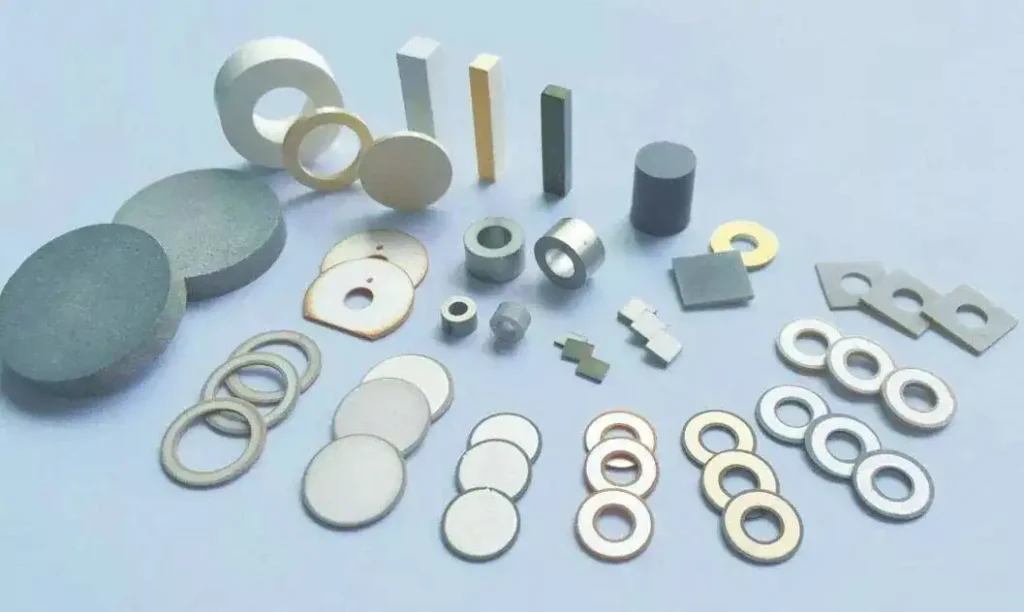
At present, my country mainly uses magnesium ore to prepare light magnesium carbonate. Due to the problems of low ore grade, high cost, poor environment, high impurity content and wide particle size distribution of the product, it has become a bottleneck for the development of enterprises. The brine soda ash method and the brine ammonium carbonate method are used to prepare light magnesium carbonate. The brine purification process has high requirements and requires more equipment. The product contains high content of Na+, Cl-, etc. The mother liquor contains a small amount of ammonium chloride, which needs to be recovered through evaporation, crystallization and other processes. It has high energy consumption and high cost. If it is directly discharged, it will cause pollution to the environment. The domestically produced light magnesium carbonate products are of low grade, with few special and functional products. They mainly occupy the low-end market share, and high-end fine magnesium chemical products still need to be imported.
Using industrial-grade magnesium hydroxide coarse powder as raw material, firstly, magnesium hydroxide is made into nano-scale suspension slurry by liquid phase grinding, and then ammonium carbonate solution is slowly added to the nano-scale magnesium hydroxide slurry for reaction. At the same time, carbon dioxide is introduced as a balance promoter for the reverse reaction of ammonium bicarbonate double hydrolysis until all magnesium hydroxide is converted into magnesium carbonate precipitate. Then the solid precipitate is filtered and separated, and nano-scale high-purity magnesium carbonate powder is obtained by drying. This method greatly improves the nano-uniformity of the raw materials during the reaction process and reduces the nano-size of the light magnesium carbonate product.
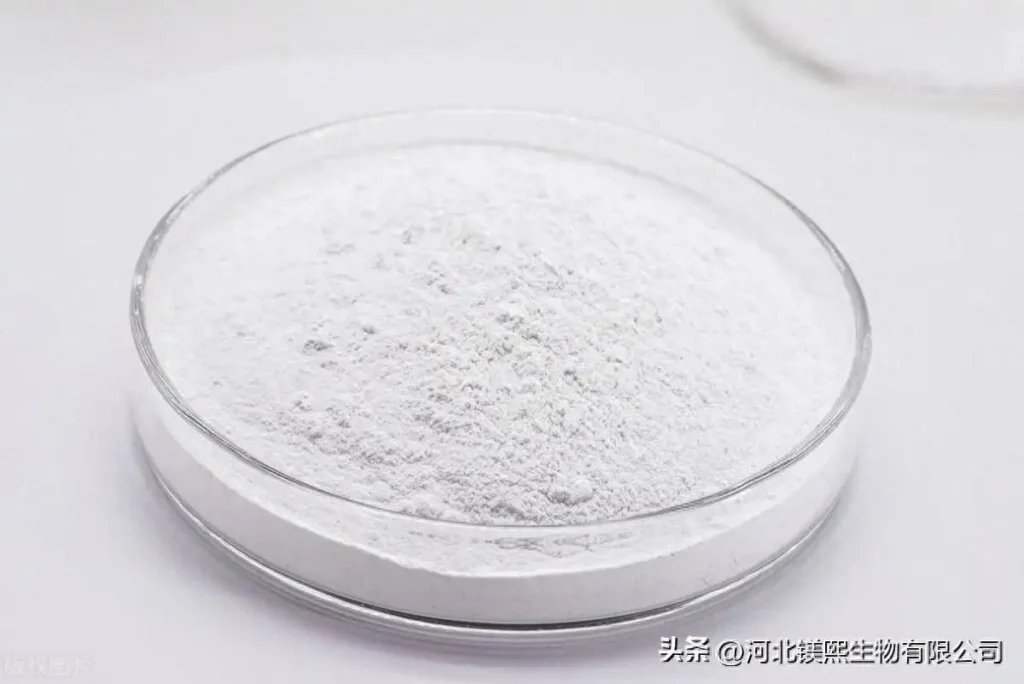
Content of the invention
The purpose of the present invention is to overcome the problems of low quality, wide particle size distribution and high cost in the prior art of preparing nano-scale high-purity light magnesium carbonate, and provide a process for preparing nano-scale high-purity light magnesium carbonate from industrial-grade magnesium hydroxide coarse powder.
In order to achieve the above-mentioned expected purpose, the present invention adopts the following technical scheme:
A method for preparing nano-scale high-purity light magnesium carbonate, characterized in that industrial-grade magnesium hydroxide coarse powder is used as a raw material, firstly, magnesium hydroxide is made into a nano-scale suspension slurry by liquid phase grinding, and then ammonium carbonate solution is slowly added to the nano-scale magnesium hydroxide slurry for reaction, and carbon dioxide is introduced as a balance promoter for the reverse reaction of ammonium bicarbonate double hydrolysis until all magnesium hydroxide is converted into magnesium carbonate precipitate. Then the solid precipitate is filtered and separated, and the nano-scale high-purity magnesium carbonate powder is obtained by drying. The process comprises the following steps:
a. Deionized water, industrial-grade magnesium hydroxide coarse powder and aqueous dispersant are weighed and mixed in a certain proportion;
b. The uniformly mixed solution in step a is placed in a sand mill for wet liquid phase ball milling. The ball milling medium is high-purity yttria-stabilized zirconium oxide ceramic balls. The wet milling mixture is mixed for 2 to 40 hours to obtain a uniformly mixed nano-scale magnesium hydroxide slurry;
c. 1 mol/L ammonium bicarbonate solution is slowly added to the nano-scale magnesium hydroxide slurry obtained in step b for reaction. The temperature is controlled at 60 to 90 ° C, and the pH value is controlled between 8.5 and 9.0. The reaction time is 1 to 6 hours; during the process, carbon dioxide is continuously introduced to perform the reverse reaction of ammonium bicarbonate double hydrolysis until all the magnesium hydroxide is converted into light magnesium carbonate precipitation;
d. The solution obtained in step c is filtered to separate the solid precipitate, and the nano-scale high-purity magnesium carbonate powder is obtained by drying.
The mass ratio of the deionized water, industrial-grade magnesium hydroxide coarse powder and aqueous dispersant is 50 to 80:10 to 40:1 to 10. The average particle size of the nano-magnesium hydroxide slurry is 50-100 nanometers.
The size of the ball milling medium is 0.1 mm or 0.05 mm.
The drying temperature is 100-180°C, and the drying time is 1-5 hours.
Beneficial effects of the present invention:
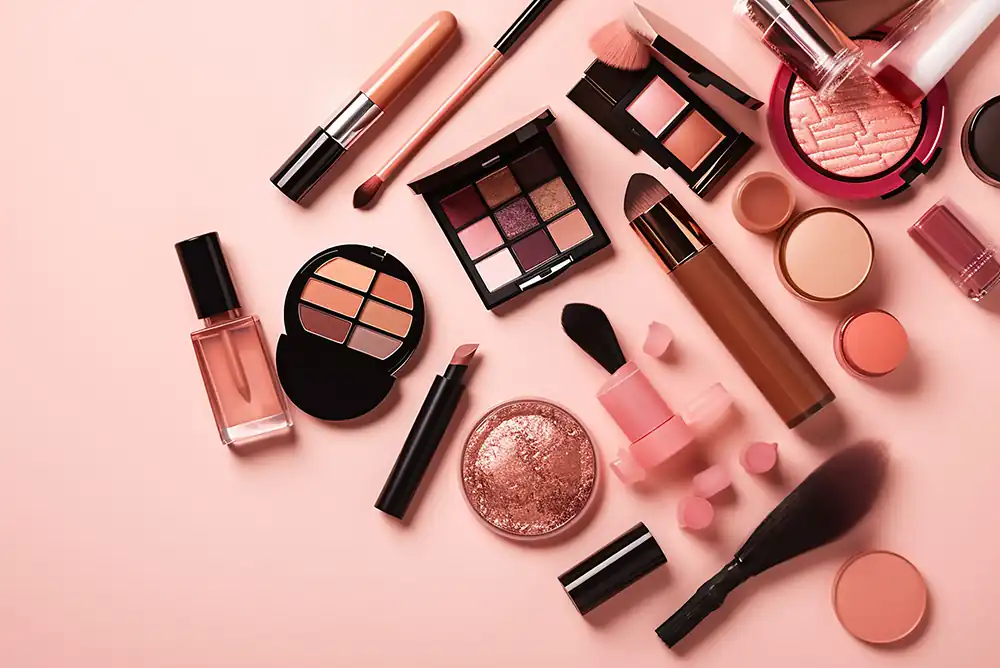
The nano-light magnesium carbonate prepared by the present invention has the characteristics of high purity, low cost, good quality, fine particle size and narrow distribution, and can be used for long-term fire retardant and additives in the fields of food, medicine, cosmetics, rubber, ink, etc. The preparation process of the present invention is stable, efficient, and has a wide range of applications, and is suitable for mass production.
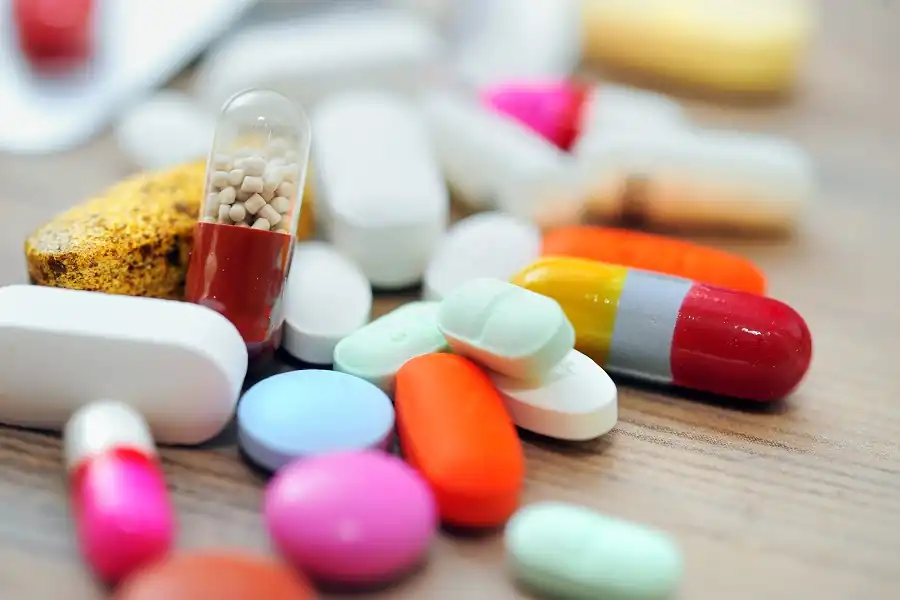
Specific implementation methods
The present invention is described in detail below through specific examples, but the protection scope of the present invention is not limited to these implementation examples.
Example 1: Deionized water, industrial-grade magnesium hydroxide coarse powder and aqueous dispersant are weighed in a mass ratio of 50:40:10 and mixed evenly; the mixed solution is placed in a sand mill for wet liquid phase ball milling, the ball milling medium is 0.1mm high-purity yttria-stabilized zirconium oxide ceramic balls, and the mixture is wet milled for 40 hours to obtain a uniformly mixed magnesium hydroxide slurry with an average particle size of 100 nanometers; 1 mol/L ammonium bicarbonate solution is slowly added to the prepared nano-scale magnesium hydroxide slurry for reaction, the temperature is controlled at 90°C, and the pH value is controlled at 9.0, and the reaction time is 6 hours; carbon dioxide is continuously introduced during the process to perform the reverse reaction of ammonium bicarbonate double hydrolysis until all the magnesium hydroxide is converted into light magnesium carbonate precipitate; the prepared solution is filtered to separate the solid precipitate, and dried at 180°C for 5 hours to obtain nano-scale high-purity magnesium carbonate powder.
The mass ratio of deionized water, industrial-grade magnesium hydroxide coarse powder and aqueous dispersant is 50~80:10~40:1~10. The average particle size of the nano-grade magnesium hydroxide slurry is 50~100 nanometers.
The ball milling medium size is 0.1mm or 0.05mm.
The drying temperature is 100~180℃, and the drying time is 1~5 hours.
Example 2: Deionized water, industrial-grade magnesium hydroxide coarse powder and aqueous dispersant were weighed in a mass ratio of 70:29:1 and mixed evenly; the mixed solution was placed in a sand mill for wet liquid phase ball milling, the ball milling medium was 0.1mm high-purity yttria-stabilized zirconium oxide ceramic balls, and the mixture was wet milled for 20 hours to obtain a uniformly mixed magnesium hydroxide slurry with an average particle size of 100 nanometers; 1 mol/L ammonium bicarbonate solution was slowly added to the obtained nano-scale magnesium hydroxide slurry for reaction, the temperature was controlled at 80°C, and the pH value was controlled at 9.0, and the reaction time was 3 hours; carbon dioxide was continuously introduced during the process to perform the reverse reaction of ammonium bicarbonate double hydrolysis until all the magnesium hydroxide was converted into light magnesium carbonate precipitate; the obtained solution was filtered to separate the solid precipitate, and dried at 150°C for 3 hours to obtain nano-scale high-purity magnesium carbonate powder.
Example 3: Deionized water, industrial-grade magnesium hydroxide coarse powder and aqueous dispersant are weighed in a mass ratio of 80:10:10 and mixed evenly; the mixed solution is placed in a sand mill for wet liquid phase ball milling, the ball milling medium is 0.05mm high-purity yttria-stabilized zirconium oxide ceramic balls, and the mixture is wet milled for 2 hours to obtain a uniformly mixed magnesium hydroxide slurry with an average particle size of 50 nanometers; 1 mol/L ammonium bicarbonate solution is slowly added to the prepared nano-scale magnesium hydroxide slurry for reaction, the temperature is controlled at 60°C, and the pH value is controlled at 8.5, and the reaction time is 1 hour; carbon dioxide is continuously introduced during the process to perform the reverse reaction of ammonium bicarbonate double hydrolysis until all the magnesium hydroxide is converted into light magnesium carbonate precipitation; the obtained solution is filtered to separate the solid precipitate, and dried at 120°C for 1 hour to obtain nano-scale high-purity magnesium carbonate powder.
The above is only a preferred embodiment of the present invention and is not intended to limit the present invention. For those skilled in the art, the present invention may have various modifications and changes. Any modifications, equivalent substitutions, improvements, etc. made within the spirit and principles of the present invention should be included in the protection scope of the present invention.