In the production and application of phenolic resin foam, magnesium carbonate, as an inorganic compound, is often used to improve the physical and chemical properties of foam. Specifically, the role of magnesium carbonate in phenolic resin foam is mainly reflected in the following aspects:
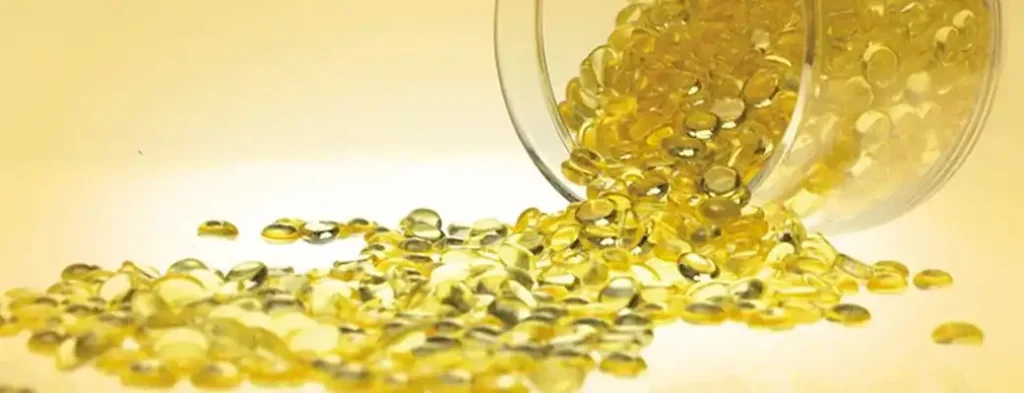
1. As a foaming agent
Magnesium carbonate can be used as a foaming agent and plays an important role in the foaming process of phenolic resin. Foaming is the formation of a foam structure of the resin through the generation of gas, and magnesium carbonate has a certain reactivity. Under high temperature conditions, magnesium carbonate will decompose and release carbon dioxide gas, which will form bubbles in the resin system, thereby prompting the resin to form a foam structure and form a foam with good thermal insulation and shock absorption properties. This role of magnesium carbonate has a direct impact on improving the volume and uniformity of the foam.
2. Adjusting the foam structure and porosity
The addition of magnesium carbonate can adjust the foam structure and porosity of the foam. By adjusting the amount of magnesium carbonate and the reaction conditions, the size, uniformity and distribution of the foam can be controlled, thereby affecting the density and mechanical properties of the final foam. Different porosity will directly affect the thermal insulation, compression resistance and other physical properties of the material.
Generally, a higher magnesium carbonate content may lead to larger pores, but will make the strength and stability of the foamed glue lower. Therefore, in practical applications, it is necessary to accurately control the amount of magnesium carbonate added to obtain an ideal foam structure.
3. Enhance thermal stability
When phenolic resin foamed glue is used in some high temperature environments, it needs to have good thermal stability. As an inorganic filler, magnesium carbonate has high thermal stability, which can effectively improve the high temperature resistance of phenolic resin foamed glue.
Specifically, the decomposition temperature of magnesium carbonate is relatively high, usually above 450°C. When the foamed glue is used at high temperatures, magnesium carbonate can prevent the premature decomposition of the resin, thereby maintaining the stability of the foamed glue. In addition, the magnesium oxide (MgO) formed by magnesium carbonate itself during the decomposition process will enhance the thermal stability of the material.
4. Improve fire resistance
Magnesium carbonate can not only improve the thermal stability of the foamed glue, but also enhance its fire resistance. In the case of high-temperature fire, phenolic resin foam is easy to burn or produce harmful gases, while magnesium carbonate can play a flame retardant role by decomposing and producing carbon dioxide gas. Carbon dioxide gas can form a certain isolation layer between the fire source and the material, reducing the supply of oxygen, thereby reducing the speed of fire spread.
In addition, magnesium oxide (MgO) has a high melting point and can act as a barrier to reduce the damage of fire to the foam structure.
5. Improve mechanical properties
As a filler, magnesium carbonate plays a role in enhancing the mechanical properties of materials in phenolic resin foam. After adding an appropriate amount of magnesium carbonate, the compressive strength and impact resistance of the foam can be improved. This is mainly because the hardness of magnesium carbonate itself is high, which can improve the internal structure of the foam and enhance its anti-deformation ability.
In construction, automobiles and other applications that require high-strength materials, the addition of magnesium carbonate can make phenolic resin foam more resistant to pressure and impact and extend its service life.
6. Improve UV resistance
Ultraviolet (UV) radiation has a destructive effect on many materials, especially on certain organic polymers such as phenolic resin. Phenolic resin may age, turn yellow, and become brittle when exposed to ultraviolet light for a long time. Magnesium carbonate, as an inorganic substance, has good UV resistance and can effectively improve the UV resistance of phenolic resin foam.
By modifying the surface of the resin or adding an appropriate amount of magnesium carbonate, the damage of ultraviolet light to the foam can be significantly reduced, and its appearance and performance can be maintained, especially in outdoor or direct sunlight environments.
7. Improve environmental performance
Magnesium carbonate is a natural inorganic material, and its production process is relatively environmentally friendly. Using magnesium carbonate to replace some organic foaming agents or additives in phenolic resin foam can reduce the use of toxic and harmful substances, thereby improving the environmental protection of the foam. For example, the decomposition process of magnesium carbonate does not produce gases that are harmful to the environment, but produces non-toxic carbon dioxide gas and magnesium oxide.
Therefore, phenolic resin foam using magnesium carbonate is more suitable for green buildings and other fields with high environmental protection requirements.
8. Reduce production costs
Magnesium carbonate is a relatively cheap inorganic material. Compared with other expensive foaming agents or reinforcing materials, the use of magnesium carbonate can effectively reduce the production cost of phenolic resin foam. In addition, a small amount of magnesium carbonate can produce significant effects, so that the foam can meet the performance requirements, reduce the cost of raw materials, and enhance market competitiveness.