Magnesium aluminate spinel (MgAl₂O₄) is widely used in the field of high-temperature materials due to its excellent refractoriness, thermal shock resistance, and corrosion resistance. Meanwhile, magnesium oxide (MgO) plays several important roles in magnesium aluminate spinel-based composites, including serving as a reinforcing phase, a bonding agent, and a key component in regulating the material’s microstructure. The specific roles and influences of magnesium oxide in magnesium aluminate spinel composites are as follows:
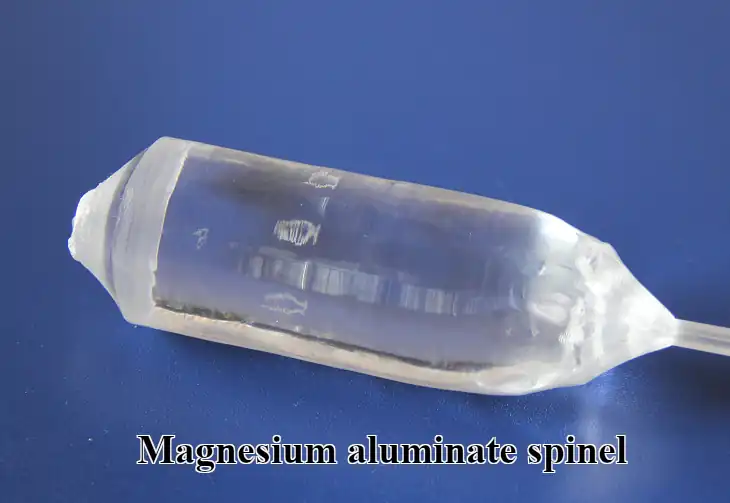
1. As a Reinforcing Phase, Enhancing the High-Temperature Performance of Refractory Materials
In magnesium aluminate spinel-based composites, magnesium oxide can exist as a reinforcing phase, enhancing the material’s high-temperature performance.
- Enhancing Thermal Shock Resistance: The difference in thermal expansion coefficients between magnesium oxide and magnesium aluminate spinel creates a certain microcrack network, which helps absorb thermal stress and improves thermal shock resistance.
- Improving Slag Corrosion Resistance: Magnesium oxide has strong basicity and can react with acidic slag (such as SiO₂, Fe₂O₃, etc.) to form high-melting-point compounds, delaying material erosion.
- Improving High-Temperature Mechanical Strength: At high temperatures, magnesium oxide particles can act as a skeletal structure, increasing the refractoriness under load (RUL) and creep resistance of refractory bricks.
2. As a Bonding Agent, Enhancing Material Density and Strength
Magnesium oxide can also serve as a bonding agent in magnesium aluminate spinel-based composites, increasing the material’s density and mechanical strength.
- Low-Temperature Bonding Action: Highly reactive magnesium oxide can promote the formation of magnesium aluminate spinel during the sintering process, increasing bonding strength.
- Promoting Sintering: Magnesium oxide lowers the sintering temperature by forming a liquid phase or dissolving in magnesium aluminate spinel, making the material denser.
- Improving the Bonding Phase Structure: An appropriate magnesium oxide content can reduce porosity and improve the overall mechanical properties of the material.
3. Influencing Microstructure, Enhancing Wear Resistance and Spalling Resistance
The content of magnesium oxide affects the microstructure of magnesium aluminate spinel composites, thereby influencing their wear resistance and spalling resistance.
- Regulating Grain Growth: Magnesium oxide particles can inhibit excessive grain growth of magnesium aluminate spinel, forming a uniform microstructure and improving spalling resistance.
- Generating MgO-rich Phases, Enhancing Corrosion Resistance: A suitable magnesium oxide content can form MgO-rich phases in the material, improving resistance to alkaline corrosion, especially suitable for steelmaking environments.
- Reducing Thermal Expansion Mismatch, Enhancing Crack Resistance: An appropriate amount of magnesium oxide can adjust the thermal expansion coefficient of magnesium aluminate spinel to make it closer to other refractory materials, reducing the risk of crack formation.
4. Optimized Proportioning in Different Application Scenarios
The specific application of magnesium oxide in magnesium aluminate spinel composites depends on the needs of different industries. For example:
- Steelmaking Industry: The magnesium oxide content is generally controlled at 10%~30% for the lining bricks of converters, electric arc furnaces, RH degassers, etc., to improve slag corrosion resistance.
- Glass Furnaces: An appropriate amount of magnesium oxide can improve resistance to corrosion from Na₂O, SiO₂, etc., making it an important refractory material for glass furnace linings.
- Cement Rotary Kilns: The magnesium oxide content is usually between 5% and 15% to improve the thermal shock resistance of refractory bricks and reduce spalling.