Typical Characteristics and Advantages of Magnesium Hydroxide Rubber Masterbatch
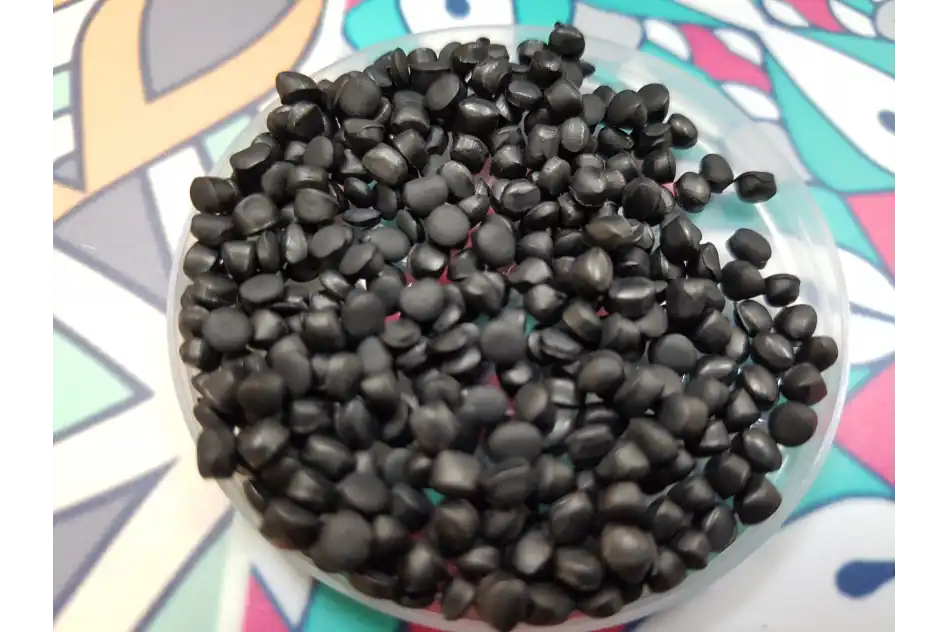
Hebei Messi Biology Co., Ltd. states that magnesium hydroxide rubber masterbatch is a functional masterbatch (concentrate) with a rubber carrier and a high proportion of magnesium hydroxide filler.
Characteristics:
- Flame Retardant: Magnesium hydroxide is one of the most important halogen-free and environmentally friendly flame retardants. In rubber (especially wire and cable sheaths, conveyor belts, seals, etc.), it can exert excellent flame-retardant effects through various mechanisms such as endothermic decomposition, releasing water vapor to dilute oxygen and flammable gases, and forming a carbonized layer.
- Smoke Suppression: The water vapor generated by the decomposition of magnesium hydroxide can significantly dilute smoke and promote the formation of a denser carbon layer, thereby greatly reducing the amount of smoke and smoke toxicity during material combustion. This is a very important advantage.
- Filling and Reinforcement: While meeting flame retardant requirements, it also acts as a filler. Surface-modified magnesium hydroxide can also provide a certain degree of reinforcement.
- Environmental Protection: It replaces halogenated flame retardants (such as brominated compounds) and antimony synergists, meeting increasingly stringent environmental regulations (such as RoHS, REACH, WEEE) and ecological requirements.
Benefits of Masterbatch Form:
- Good Dispersibility: Pre-dispersing a high content of magnesium hydroxide evenly in a rubber carrier solves the problem of agglomeration and poor dispersion that easily occurs when directly adding a large amount of powder, improving the performance and stability of the final product.
- Easy Processing: Simplifies the rubber processing flow (mixing), improves production efficiency, and reduces dust pollution.
- Stable Performance: Ensures stable batch-to-batch quality and reliable flame-retardant effects.
Typical Characteristics and Advantages of Magnesium Hydroxide Rubber Masterbatch
- High-Purity Magnesium Hydroxide: The core filler of the masterbatch is the high-purity magnesium hydroxide (Mg(OH)₂) produced by the company. The content of impurities (such as Cl⁻, SO₄²⁻, heavy metals) is extremely low, which helps to:
- Guarantee excellent flame retardant and smoke suppression effects.
- Avoid negative impacts of impurities on the aging and performance of the rubber matrix (especially silicone rubber, EPDM, etc.).
- Improve the electrical insulation performance of the product (especially important for wires and cables).
- Fine Particle Size and Particle Size Distribution Control: The magnesium hydroxide powder is finely ground and classified to ensure a suitable particle size and a narrow particle size distribution. This is crucial for:
- Obtaining good dispersibility in the masterbatch and the final rubber product.
- Influencing flame retardant efficiency, mechanical properties, and processing fluidity.
- Advanced Surface Modification Technology: This is one of the core competitiveness of Hebei Messi Biology. Surface organic treatment of magnesium hydroxide (such as using silane coupling agents, fatty acid salts, titanates, etc.):
- Significantly improves the compatibility and interfacial adhesion between magnesium hydroxide and the rubber matrix.
- Greatly improves the dispersion uniformity of magnesium hydroxide in rubber.
- Reduces the decline in rubber mechanical properties (such as tensile strength, elongation, tear strength) caused by a large amount of filling, and may even provide a certain degree of reinforcement.
- Improves the processing fluidity of the masterbatch and rubber compounds.
- High Filling Rate: The filling ratio of magnesium hydroxide in the masterbatch can be very high (for example, 60%-85% or higher), ensuring that it can effectively achieve the target flame retardant grade (such as UL94V-0) when added to rubber.
- Carrier Rubber Compatibility: The masterbatch will select different carrier rubbers (such as EPDM, NBR, SBR, NR, silicone rubber, etc.) according to the target application to ensure good compatibility and co-vulcanization with the rubber used in the final product.
- Excellent Flame Retardant and Smoke Suppression Performance: This is the core value of the product. It can help rubber products easily pass flame retardant testing standards such as UL94, LOI, GB/T, etc., and significantly reduce smoke density and toxicity.
- Environmentally Friendly and Non-Toxic: Complies with the halogen-free flame retardant trend and meets green manufacturing requirements.
Main Application Areas:
- Wires and Cables: Sheath materials, insulation materials (requiring halogen-free, low-smoke, flame retardant – WDZ).
- Conveyor Belts: Flame-retardant conveyor belts for underground coal mines, general industrial flame-retardant conveyor belts.
- Sealing Products: Flame-retardant rubber sealing strips, gaskets.
- Rubber Rollers: Occasions requiring flame retardant performance.
- Other Rubber Products: Such as flame-retardant rubber hoses, shock-absorbing pads, floors, and other components that require halogen-free flame retardant and low-smoke, low-toxicity characteristics.
Hebei Messi Biology Co., Ltd., with its technological advantages in the production of high-end magnesium hydroxide (high purity, surface treatment), provides magnesium hydroxide rubber masterbatch, which is a functional additive specifically designed to solve the halogen-free flame retardant, low-smoke, and low-toxicity needs of rubber products (especially wires and cables, conveyor belts, etc.). Its core value lies in solving the dispersion problem of high-filled magnesium hydroxide through the masterbatch form, and combining its surface modification technology to impart excellent flame retardant and smoke suppression properties to rubber while minimizing the negative impact on the mechanical properties and processing performance of the rubber.