Magnesium oxide is a very common alkaline oxide and the main raw material for the production of magnesium hydroxide and magnesium metal. In the application of ceramic materials, magnesium oxide has a melting point as high as 2800°C and has some special and excellent properties. Therefore, it is also quite popular in the field of advanced ceramics. It can be directly sintered into magnesium oxide ceramics or used as an additive.
Magnesium oxide powder preparation
The preparation of magnesium oxide is divided into brine-ammonia precipitation method, dolomite carbonization method, magnesium salt thermal decomposition and rhodolite thermal decomposition method. Preparation, raw materials originated from minerals or seawater, from minerals or seawater to extract MgO, most of the first made of magnesium hydroxide or magnesium carbonate, and then calcined decomposition into MgO, this MgO through further chemical treatment or heat treatment can be obtained from high-purity MgO, if you require a high purity of MgO ceramics, can not be used to add additives to promote the method of sintering and grain growth, but rather the use of activated Sintering method, i.e., Mg(OH)2 calcined at the appropriate temperature to obtain the activated MgO with many lattice defects, used to manufacture sintered magnesium oxide ceramics.
Magnesium oxide ceramics
(1) MgO transparent ceramics
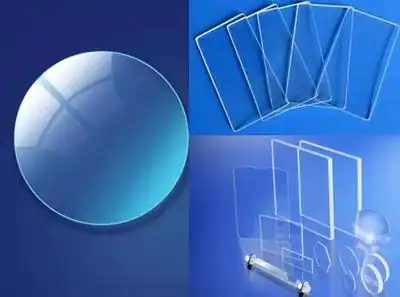
MgO transparent ceramics transparency and infrared transmittance is good, it is a kind of optical isotropic body, has a better resistance to alkali metal vapor corrosion, high melting point, high thermal conductivity, smaller theoretical density, high insulation and high infrared transmittance and other advantages. It has a wide range of applications in the field of visible and infrared transmissive materials, and its performance is better than that of alumina ceramics.
Typical applications: the preparation of spacecraft and rocket missiles infrared window and fairing, high-temperature furnace infrared window, high-temperature infrared optics, optical filters and optical detectors, high-pressure sodium lamps and infrared detector cover the important material.
(2) MgO foam ceramics
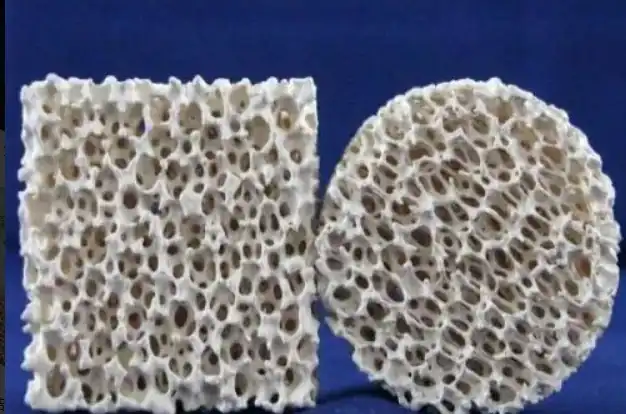
Foam ceramic materials as a new type of ceramic functional materials, its development from the 1970s onwards. MgO foam ceramics have a unique three-dimensional mesh skeleton structure, so that it has 60% -90% of the pore rate, can be efficiently removed from the metal liquid in the large debris and most of the tiny suspended inclusions, with a high degree of refractoriness, high porosity, low thermal conductivity, low cost of manufacturing, preparation, simple process, with good mechanical properties. It has high refractoriness, high porosity, low thermal conductivity, low manufacturing cost, simple preparation process and good mechanical properties. In the domestic Peking University, Li Wenxia et al. to magnesium oxide as aggregate, adding the appropriate amount of ZrO2 prepared magnesium oxide partially stabilized zirconia foam ceramic filters, which in the production of nickel-based alloy single-crystal chip has achieved good results, filling the gaps in the domestic technology.
Typical applications.
a, Filter. Utilizing filter cake effect, adsorption effect and rectification effect to filter impurities in magnesium alloy melt and improve filtration efficiency.
b. Energy-saving heat insulation material. It can be used as kiln lining, and in aerospace industry, it can insulate and protect aerospace equipment.
c, sound-absorbing materials. According to research, its noise reduction coefficient is close to that of glass wool, which has good application prospects.
d, catalyst carrier material. Good adsorption capacity, can be widely used as car exhaust purifier carrier.
e, food and pharmaceutical industry. Used in the pharmaceutical industry for enzymes, vaccines, nucleic acids and other physiologically active substances such as concentration, separation, refining, etc., to ensure food safety.
(3) MgO series microwave dielectric ceramics
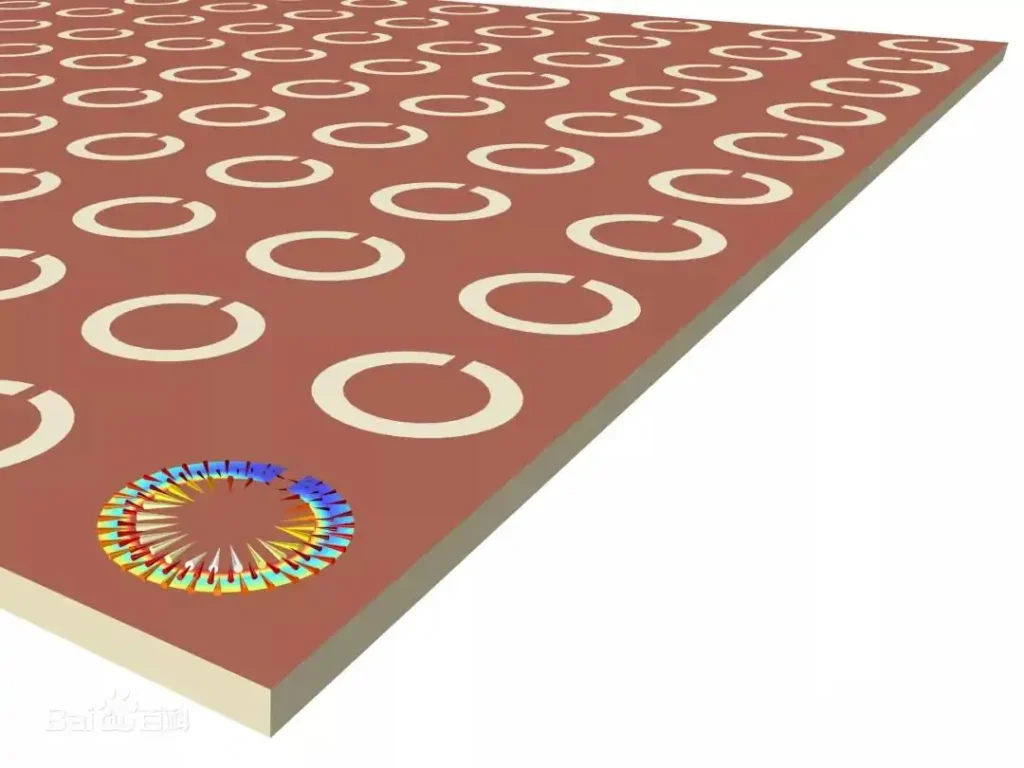
With the mobile communications, satellite communications technology updates, people for the communication time and frequency band requirements are getting higher and higher, so that the low dielectric high Q ceramics have become a research hot spot. On the one hand, MgO ceramics itself has superior dielectric properties (εr=9.1,tanδ<1.6×10-6), is an ideal microwave dielectric substrate material for 5G communication.
MgTiO3-based microwave dielectric ceramics have an ilmenite structure with space group R3, and this material has been investigated and applied to ceramic capacitors and resonators because of its low tanδ and high frequency thermal stability. In addition, MgTiO3 has potential for applications in filters, communication antennas, radar, direct broadcasting satellites, and microwave-frequency global positioning systems.
MgAl2O4 has a spinel-type structure with high hardness, high melting point, high strength, and pure MgAl2O4 is transparent, which can be used in transparent armor, infrared windows, radomes, and other applications. Not only that, MgAl2O4 is also characterized by low εr and can also be used as microwave dielectric ceramics. The comprehensive performance of MgAl2O4 ceramics prepared by microwave sintering is excellent, which can meet the requirements of various fields of use.
(4) MgO ceramic core type
Magnesium oxide high temperature performance is good, with magnesium oxide-based ceramic core foot casting stainless steel castings, even if the pouring temperature up to 1650 ℃, the core material will not react with the alloy, the casting of the internal surface finish is high, and it belongs to the weakly alkaline refractory materials, can be dissolved in phosphoric acid and acetic acid and other organic acid solutions, easy to remove the core, which does not produce thermal cracking defects, magnesium-based ceramic core type of the current research is relatively small, with a great deal of There is a lot of space for development.
Application of magnesium oxide as additive
1. As a sintering agent for alumina
Magnesium oxide, as a common sintering aid, has the following effects on alumina ceramics:
a. Adding an appropriate amount of MgO can reduce the sintering temperature of alumina ceramics, inhibit grain growth, and increase density.
b. Add MgO. Mg accelerates grain boundary diffusion, has a certain refinement effect on grains, and has better density and mechanical properties.
c. An appropriate amount of MgO can inhibit the rapid movement of grain boundaries, making the pores more completely discharged, making the ceramic more dense and with a higher transmittance.
2. As a sintering aid for high-performance ceramic heat dissipation substrates
As high-power electronic devices in the fields of high-speed rail, aerospace and military industry develop towards high temperature, high frequency and high integration, efficient heat dissipation has become an urgent need. High-power devices achieve heat exchange with the outside world through ceramic copper-clad laminates. Currently, there are three mainstream ceramic substrates: Si3N4, AlN and Al2O3, all of which require MgO as a sintering aid. Especially for Si3N4 ceramics with excellent comprehensive properties, in order to avoid the lattice defects caused by Al2O3 as an additive and increase phonon scattering, MgO has become the preferred sintering additive for preparing high thermal conductivity Si3N4 ceramics, and its usage is about 3%.
3. As a sintering aid for ZTA wear-resistant ceramics
Both Al2O3 and ZrO2 have properties such as high temperature resistance, wear resistance and good biocompatibility. Using ZrO2 to toughen Al2O3 to prepare ZTA nanocomposite ceramics can maximize its strengths and avoid weaknesses and give full play to its integration advantages. It has important applications in aerospace, engine wear-resistant parts, and artificial femoral ball heads. The densification and grain refinement mechanism of MgO in ZTA ceramics is similar to that in Al2O3, and its usage is about 2%.
4. As an additive for ferroelectric ceramics
(1) Added to BaTiO3-based ceramics
The uniform precipitation method is used to evenly coat MgO on the surface of BaTiO3-based ceramic powder, which can effectively inhibit the growth of grains and obtain ceramics with uniform grains. This fine-graining effect is due to the inhibitory effect of MgO in the grain boundary region; MgO has Helps form “shell-core” structure grains, reduces and broadens the ε peak of BaTiO3-based ceramics, and increases resistivity and breakdown voltage strength.
(2) Added to barium strontium titanate ceramics
Barium strontium titanate (BST) ferroelectric ceramic material has very good application prospects as a phase shifter in phased arrays and as a tunable device at microwave frequencies due to its high tunability and low dielectric loss.
Since various current ferroelectric materials have certain deficiencies, improving their comprehensive performance through various means has become a key issue that must be solved to achieve large-scale application of barium strontium titanate materials.
In addition to A-site doping substitution with rare earth element ions, adding MgO, MgTiO3, Mg2SiO4 and other compounds to BST ceramics and films can also reduce their dielectric constant and dielectric loss.
5. Doped zinc oxide linear ceramics
ZnO linear ceramic resistors have the advantages of large resistivity change range, large flow density, low nonlinear coefficient, and small temperature coefficient of resistance. They are widely used in power-electronics, transportation, communications, and household appliances. Traditional ZnO composite ceramics still have many problems, such as poor structural uniformity, low industrial production repeatability, poor stability, and insufficient theoretical research.
The addition of MgO helps to improve the temperature resistance coefficient of ZnO ceramic resistors. An appropriate amount of MgO can promote sintering and increase the density of ceramics, but excessive addition will reduce the density of ceramics.