Messi Biology stated that the production of electric heating elements affects the quality of electric heating tubes due to various factors, including the process technology of the electric heating tube itself, and various materials for manufacturing electric heating tubes, especially the various indicators of electrical grade magnesium oxide, which will have various effects on the quality of electric heating tubes. The following is a brief introduction to the impact of the main technical indicators of electrical grade magnesium oxide on the quality of electric heating tubes:
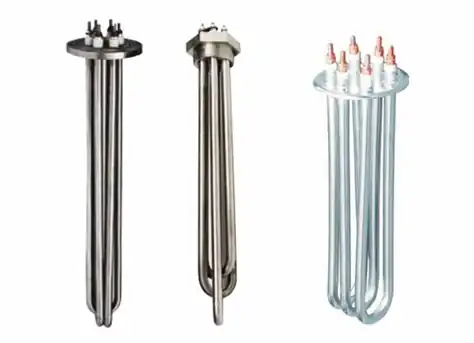
I. The impact of the chemical composition of magnesium oxide powder used in electric heating tubes:
1. Chemical composition of magnesium powder from foreign manufacturers: see the table below
Name | Specification | LOS | Si02 | AL203 | Fe203 | Ca0 | Mg0 | BppM | SppM | CPPM | Magnetic Material PPM | PPPM |
USA | High temperature | ≤0.02 | ≤4.5 | ≤1.2 | ≤0.2 | ≤1.7 | ≥92 | ≤50 | ≤50 | ≤100 | ≤50 | —- |
Medium temperature | ≤0.025 | ≤5.0 | ≤0.8 | ≤0.2 | ≤1.1 | ≥90 | ≤60 | ≤50 | ≤100 | ≤100 | —- | |
Low temperature | ≤0.25 | ≤8.0 | ≤1.0 | ≤0.2 | ≤1.1 | ≥76 | ≤60 | ≤50 | ≤100 | ≤150 | —- | |
Japan | High temperature | —- | ≤1.5 | ≤0.6 | ≤0.5 | ≤1.0 | ≥97 | —- | —- | —- | —- | —- |
Medium temperature | —- | ≤2.0 | ≤2.0 | ≤0.6 | ≤1.5 | ≥94 | —- | —- | —- | —- | —- | |
Low temperature | —- | ≤2.0 | ≤0.6 | ≤0.7 | ≤1.5 | ≥94 | —- | —- | —- | —- | —- | |
Germany | High temperature | —- | —- | —- | ≤0.2 | —- | ≥95 | —- | ≤ 20 | ≤100 | ≤100 | ≤50 |
Medium to high temperature | —- | —- | —- | ≤0.55 | —- | ≥95 | —- | ≤100 | ≤500 | ≤300 | ≤500 |
2. The impact of chemical indicators of magnesium oxide powder used in electric heating tubes on the quality of electric heating tubes
A. Loss on ignition: refers to the moisture in electrical grade magnesium oxide and other objects lost under high temperature;
For high temperature powder and general powder, it mainly refers to moisture; for modified powder, it refers to moisture plus modifier components. For modified powder, the leakage current peak is too large when power is turned on, and for high temperature powder, the tube will cause bubbling after passing through the furnace.
B.SIO2: The ratio of SIO2 to CaO is controlled at 1:1, preferably 2:1.
C.Fe2O3: The amount of iron oxide directly affects the life of the electric heating tube. For electrical grade magnesium oxide, the lower the Fe2O3 content, the better. However, for my country’s current magnesium ore resources, magnesium ore with a content of ≤0.2Fe2O3 is very rare. Most magnesium ore has a Fe2O3 content of ≤0.5% when it is burned into fused magnesium. On the other hand, my country has not yet found iron removal technology that can remove Fe2O3 during the smelting of fused magnesium and control its content to ≤0.1.
D.Al2O3: In fused magnesium, the Al2O3 content is between 0.1-0.5. When its index content is high, it is related to the addition of additives in production.
E.Ca0 content: Ca0 is lime, which easily absorbs water to produce Ca(0H)2. When the silicon content is high, during the electrofusion process, Ca0 reacts with SiO2 to generate CaSiO3, CaO+Si0-CaSi03 (high temperature).
F.Mg0: In electrofused magnesium oxide, the Mg0 content is between 96 and 98. Generally speaking, the higher the Mg0, the fewer impurities, and the better the performance. The MgO content is 98-99% for large crystals. The crystal shape of large crystals is needle-shaped and flake-shaped, so the physical and electrical properties are not as good as electrofused magnesium oxide.
If you want good electrical performance and Mg0 content ≥98%, and other impurities such as Fe2O3 ≤0.2%, you have to use seawater magnesium to achieve this.
G. Other trace impurities: B, S, P, and C are the main impurities; the presence of B will reduce the melting point of MgO (the melting point of magnesium oxide is 2800℃). After the high-temperature powder is made into a tube, the electric heating tube needs to be furnaced at 1050-1080℃ for 15-40 minutes. Excessive B content will cause MgO to sinter after passing through the furnace. When bending the tube, the elbow part will produce hair-like cracks, as shown in Figure (1), which will reduce the withstand voltage of the electric heating tube. In severe cases, the withstand voltage cannot be restored after the elbow is oil-pressurized. The presence of S and P will shorten the life of the electric heating wire. The presence of C ≥1OOPPM will increase the leakage current, reduce the withstand voltage, and reduce the insulation.
H. Ferromagnetic substances are completely harmful substances. The lower its content is, the better. The US UCM requires ≤50P.P.M. The content of ferromagnetic substances in electrical grade magnesium oxide mainly depends on two conditions:
a. The content of Fe2O3 in the raw material. If the content of Fe2O3 in the raw material is ≤0.5, it can meet the basic requirements.
b. The magnetic separation capacity of the magnesium powder factory: At present, the best magnetic separators in China are water-cooled. If the content of ferromagnetic substances is too high, it will directly affect the normal withstand voltage, which will greatly reduce the performance and life of the electric heating tube.
At present, the general factory indicators in China are controlled below ≤0.03%.
II. The influence of the physical properties of magnesium oxide powder used in electric heating tubes:
The physical indicators of electrical grade magnesium oxide mainly include flow rate (FT), density (TD) and (FR), and mesh distribution.
1. Flow rate (FT): refers to the time for 100 grams of electrical grade Mg0 to flow out through a 4# Ford cup, in seconds. Different powder loading machines have different requirements for flow rate, especially some foreign powder loading machines, such as Kantel, Oaklay, etc., which have higher requirements for flow rate; the main domestic manufacturers produce powder loading machines with lower requirements for flow rate, which are generally available between 38 and 42 seconds. If the flow rate is too slow, the electric heating tube is not fully filled with powder, and the quality of the electric heating tube cannot be guaranteed; it affects the compaction density after the straight tube, and then affects the power and heat conduction. If the flow rate is too fast, it is easy to leak during powder loading, wasting magnesium powder.
2. Density (T.D) and (FR)
The tapping density T·D and flow rate FR refer to the density measured by the AP901122 tapping density meter made in the United States. The method is to put 100 grams of magnesium oxide into the 3# Ford cup of the density meter, and measure the density after the flow time.
It is an important indicator of electrical grade magnesium oxide. Different customers and different metal tubes have different requirements for density. It mainly affects:
A. After powdering, the elongation of the electric heating tube: that is, the length of the electric heating tube after shrinking the tube. The density is high, and the tube is longer after shrinking; the density is low, and the tube is shorter after shrinking;
B. The compaction density after shrinking the tube causes the resistance of the heating wire to change. Affecting the power and thermal conductivity of the electric heating tube. Therefore, when the electric heating tube factory orders magnesium powder, it is best to make requirements to the magnesium powder factory. For example, when producing aluminum tubes and copper tube electric heating tubes, the density of magnesium powder is relatively high, generally 2.36~2.40g/cm³; for Bondi tubes and stainless steel tubes, the T.D is generally controlled between 2.31±0.3g/cm3.
If the density is too high, when the diameter of the electric heating tube is small when bending the tube, the electric heating tube is easy to break; if the density is too low, the tube is not filled with powder, and the electrical performance such as pressure resistance does not meet the requirements.
3. Mesh distribution. The mesh distribution of electrical grade magnesium oxide is determined by the user’s required density, flow rate and size of the electric heating tube. Here are some common mesh distributions: see the table below for details
A. The influence of mesh on electric heating tube: if the mesh is too large, the particle size is small, the surface area per unit weight is large, and it is easy to absorb moisture; if the mesh is too small, the larger the particle size, the more likely it is to damage the heating wire after rolling and affect the life of the electric heating tube;
B. How to choose the mesh according to the diameter of the electric heating tube and the wire pitch of the electric heating wire:
① ≥8mm diameter electric heating tube can choose 40 mesh ~ 325 mesh magnesium powder;
② 6.5mm ~ 8mm direct electric heating tube can choose 50 mesh ~ 325 mesh magnesium powder;
③ ≤6.5mm diameter electric heating tube can choose 60-325 mesh magnesium powder.
C. How to use mesh distribution to adjust density:
To increase the density, you can appropriately increase the amount of particles (such as 60 mesh) and the percentage of 200 mesh. To reduce the density, just reduce it by 200 mesh or less.
4. Other impurities in electrical grade magnesium oxide:
Magnesium oxide is not allowed to contain other impurities, especially organic impurities, such as packaging fragments, ribbons, organic impurities will carbonize when powered on, seriously affecting the performance of the electrical appliance, and in severe cases, pipe explosion will occur.
III. Effect of modifier dosage
The dosage of modifier should be strictly controlled: the addition of modifier is mainly to achieve the following purposes:
(1) Moisture-proof ability in different regions, especially in the rainy weather in the south, the temperature is high and the humidity is high, which requires a higher moisture-proof ability of magnesium oxide;
(2) Select appropriate high temperature resistant modifiers, generally with smaller molecular weight and lower carbon content, the temperature resistance of modifiers will increase;
(3) The dosage of modifier should not be too large, which will reduce the use temperature of magnesium powder, and in severe cases, pipe explosion and pipe explosion will occur.