Magnesium carbonate trihydrate (MgCO3·3H2O) crystals are single crystals of magnesium carbonate. During crystallization, the atomic structure is highly ordered, the crystal has few internal defects, the strength value is close to that of an ideal crystal, and the physical and chemical properties are excellent. It is often used as a toughening and reinforcing agent for polymers such as rubber and plastics and an additive for refractory materials such as ceramics. It has extremely high industrial value [1-5]. Because of its high purity and thermodynamically metastable properties, magnesium carbonate trihydrate crystals are often used as intermediate products for the production of stable phase fine magnesium salts such as basic magnesium carbonate, magnesium oxide, and anhydrous magnesium carbonate [6-8].
At present, the common preparation methods of magnesium carbonate trihydrate whiskers include coprecipitation, hydrothermal method, and carbonation method. Botha et al. [9] prepared MgCO3·3H2O by introducing CO2 into a Mg(OH)2 suspension and heating it to investigate the effects of reaction temperature, pH value, and hydrochloric acid on the morphology and structure of MgCO3·3H2O whiskers. Wang et al. [10] used MgCl2·6H2O and (NH4)2CO3 as reactants, strictly controlled the initial concentration of the reactants and the reaction temperature, prepared MgCO3·3H2O whiskers with a length of 40 μm, and calcined the product at 800 °C to obtain high-purity MgO. Gao Yujuan et al. [11] used MgCl2·6H2O and NH4HCO3 as reactants, and obtained rod-shaped, radial and granular MgCO3·3H2O crystals by changing the concentration of ammonium bicarbonate and magnesium ions. Zhao Bin et al. [12] used MgSO4·7H2O and Na2CO3 as raw materials, and synthesized rod-shaped MgCO3·3H2O crystals with good crystallinity when the temperature was 50 °C, the MgSO4 concentration was 1.2 mol/L, the molar ratio of MgSO4 to Na2CO3 was 1:1.2, and the reaction time was 40 min. Shen Rui et al. [13] used pretreated boron mud as raw material, sodium carbonate as precipitant, and disodium hydrogen phosphate (Na2HPO4·12H2O) as additive to prepare magnesium carbonate trihydrate crystals with good dispersibility. Wang Yulian et al. [14] used magnesite as raw material, adopted calcination-hydration-carbonation-pyrolysis method, and used sodium dodecyl sulfate (SDS) as crystal control agent to prepare rod-shaped MgCO3·3H2O crystals with an average aspect ratio of 25. Ou Long et al. [15] used light-burned dolomite powder as raw material, prepared heavy magnesium water precursor solution through digestion and carbonization, and introduced air into the Mg(HCO3)2 solution, and pyrolyzed it at 60 °C to obtain MgCO3·3H2O whiskers. Using industrial magnesium-containing materials such as boron mud, salt lake brine, and natural minerals (magnesite [16-17], dolomite, etc.) as raw materials has certain guiding significance for the industrial production of magnesium carbonate trihydrate, but the process factors are still relatively complicated.
Looking at the research results at home and abroad, the morphology of the prepared magnesium carbonate trihydrate crystals is mainly rod-shaped. In the early stage, the author’s research group used magnesite as raw material, lightly burned to obtain highly active MgO, and hydrated the highly active MgO to obtain Mg(OH)2 suspension, leached the Mg(OH)2 suspension with hydrochloric acid and added a precipitant to synthesize MgCO3·3H2O crystals. Based on the previous work, this paper used chemical reagents MgCl2·6H2O and Na2CO3 as raw materials, and used coprecipitation to prepare MgCO3·3H2O crystals. The effects of reactant concentration, reaction temperature, reaction time, aging time and additive sodium citrate on the phase composition and micromorphology of the crystal product were investigated, and the growth mechanism of rod-shaped magnesium carbonate trihydrate crystals in the MgCl2·6H2O-Na2CO3 system was explored.
1 Experiment
1.1 Main reagent materials
Magnesium chloride (MgCl2·6H2O, analytical grade, Tianjin Damao Chemical Reagent Factory); sodium carbonate (Na2CO3, analytical grade, Tianjin Komeo Chemical Reagent Co., Ltd.); sodium citrate (Na3C6H5O7·2H2O, analytical grade, Shenyang Dongxing Reagent Factory).
1.2 Method
1) Sample preparation
Measure a certain volume of MgCl2·6H2O solution with a concentration of 0.05-0.30 mol/L and place it in a beaker, and place the beaker in a constant temperature water bath at 20-50 ℃ for insulation. According to the molar ratio of 1:1, measure the same volume and concentration of Na2CO3 solution and keep it warm at the same temperature, pour it into the beaker containing MgCl2·6H2O solution at one time, stir continuously, stop stirring after the reaction is completed, age for a certain period of time at room temperature, filter, and dry the obtained white precipitate in a constant temperature drying oven at 50 ℃ for 4 h to obtain white powder.
2) Characterization of samples
The microscopic morphology of the product was observed using a MIT500 metallographic microscope produced by Chongqing Aote Optical Instrument Co., Ltd. The sample phase was detected using an Ultima IV X-ray diffractometer produced by Rigaku, Japan. The radiation source was a Cu copper target Kα, λ=0.154 1 nm, a solid detector, a tube voltage of 40 kV, a tube current of 40 mA, a scanning rate of 12 (°)·min-1, and a scanning range of 2θ=5 °~90 °. The morphology of the product after gold spraying treatment was observed using a Hitachi S-3400N scanning electron microscope.
2 Results and discussion
2.1 Effect of reactant concentration
When the reaction temperature was fixed at 50 °C, the stirring rate was 300 r/min, the reaction time was 15 min, the aging time was 0.5 h, and the reactant concentrations were 0.05, 0.10, 0.20 and 0.30 mol/L, respectively, the product morphology obtained was shown in Figure 1. As can be seen from the figure, when the reactant concentration is 0.05 mol/L, the product is mainly irregular agglomerates, and a small amount of rod-shaped crystals can be vaguely seen, as shown in Figure 1 a); when the reactant concentration increases to 0.10 mol/L, needle-shaped crystals begin to precipitate, but the crystal length is short and the yield is low, as shown in Figure 1 b); when the reactant concentration is 0.20 mol/L, the surface of the obtained rod-shaped crystals is rough; some small particle nuclei in the reaction solution gather together to reduce their surface energy, resulting in a small amount of agglomerates, as shown in Figure 1 c); when the reactant concentration increases to 0.30 mol/L, the products are all rod-shaped crystals with smooth appearance and uniform shape, as shown in Figure 1 d).
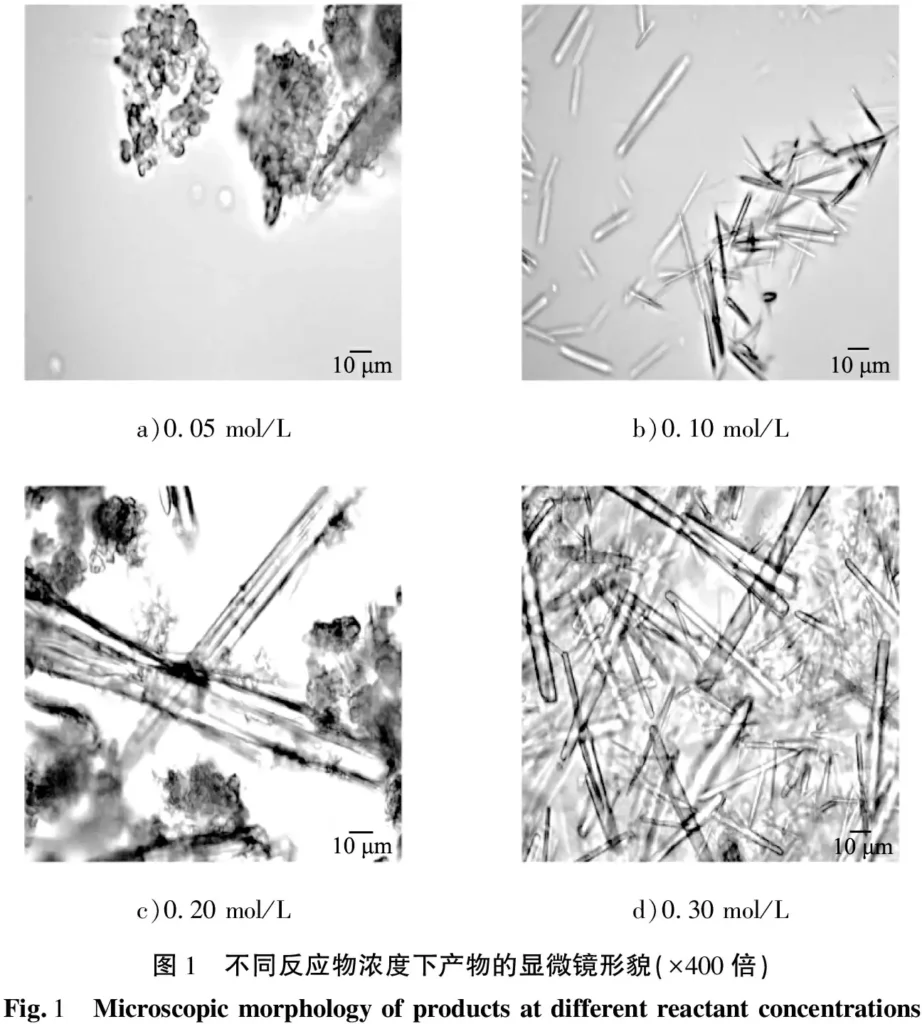
In summary, the growth and morphology of the product are greatly affected by the reactant concentration. When the concentration of the reactant is 0.10 mol/L, the ion concentration in the solution is low, the supersaturation is small, the crystal nucleus growth is incomplete, the number of whiskers obtained is small, and the length is short. Therefore, the appropriate concentration of the reactant is 0.30 mol/L.
Figure 2 is the XRD image of the product obtained when the reactant concentration is 0.30 mol/L. Observation and analysis of the image show that the diffraction peak of the product matches the characteristic peak of MgCO3·3H2O (PDF#70-1433). The diffraction peak is sharp, the base is flat, and there are no other impurity peaks, indicating that the obtained product has high purity and less impurities. Therefore, the appropriate concentration of the reactant is 0.30 mol/L.

2.2 Effect of reaction temperature
The reactant concentration was fixed at 0.30 mol/L, the stirring rate was 300 r/min, the reaction time was 15 min, the aging time was 0.5 h, and the reaction temperature was 20, 30, 40, 45, and 50 ℃, respectively. The product morphology is shown in Figure 3. As can be seen from the figure, when the reaction temperature is 20 ℃, the product can be seen under the 400x objective lens as coarse rod-shaped crystals, as shown in Figure 3 a), but the number is small; when the reaction temperature is increased to 30 ℃, the product is thin rod-shaped crystals, as shown in Figure 3 b); when the reaction temperature is 40 ℃, the obtained crystals are uneven in length and the yield is small, as shown in Figure 3 c); when the temperature is further increased to 50 ℃, longer rod-shaped crystals are obtained, as shown in Figure 3 d). At 20 ℃, the reaction system temperature is low, the reaction rate is slow, and the nucleation is small, resulting in a coarse final product.
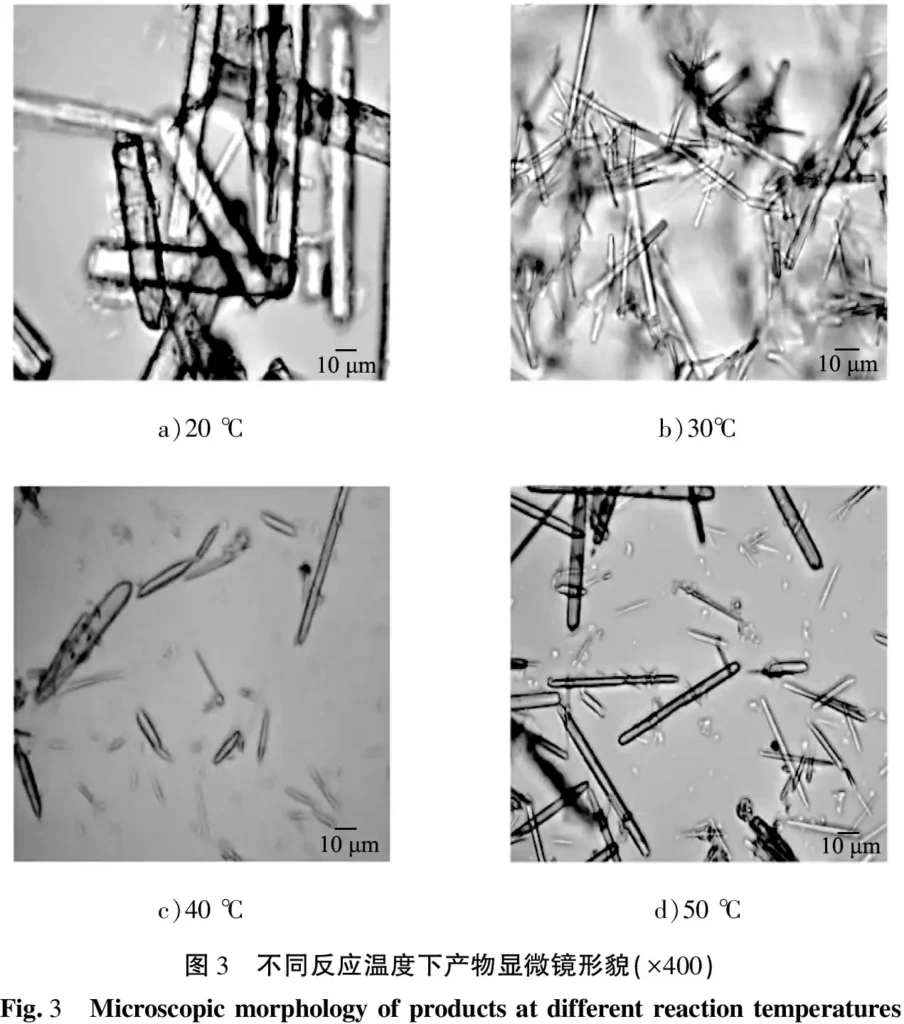
The products obtained at 30 ℃ and 50 ℃ were tested by XRD, and the results are shown in Figure 4. It can be seen from the figure that at 30 ℃, the product diffraction peaks simultaneously contain the characteristic peaks of 4MgCO3·Mg(OH)2·5H2O and MgCO3·3H2O, indicating that the product obtained at this temperature is a mixture of the two. At 50 ℃, the product diffraction peaks all match the characteristic peaks of MgCO3·3H2O, with high peaks and no other impurities, indicating that high-purity and well-crystallized rod-shaped MgCO3·3H2O crystals can be obtained at this temperature, so 50 ℃ is selected as the optimal reaction temperature.
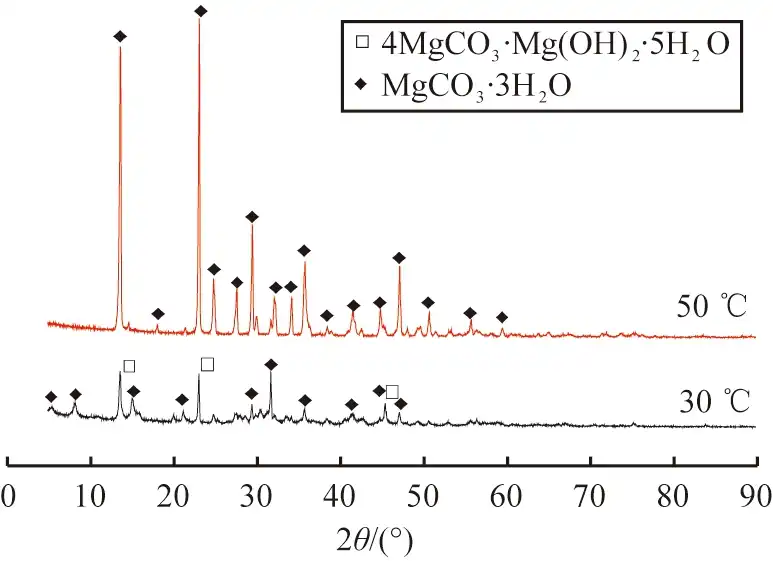
2.3 Effect of reaction time
When the reactant concentration is fixed at 0.30 mol/L, the stirring rate is 300 r/min, the reaction temperature is 50 ℃, the aging time is 0.5 h, and the reaction time is 5, 10, 15, 20, 25 and 40 min, respectively, the XRD pattern of the obtained product is shown in Figure 5. As can be seen from the figure, when the reaction time is between 5 and 15 min, the obtained products are all MgCO3·3H2O. When the reaction time is 15 min, the product XRD image has a smooth base, narrow and sharp peaks, and the diffraction peaks of the product are consistent with the characteristic peaks of MgCO3·3H2O, without other impurity peaks, indicating that the product obtained under this reaction condition has high crystallinity and few impurities; when the reaction time is 20 min, there are two diffraction peaks in the XRD spectrum at the same time, and the obtained product is a mixture of MgCO3·3H2O and 4MgCO3·Mg(OH)2·4H2O. At 25 and 40 min, the characteristic peaks of the product are consistent with the standard peaks of 4MgCO3·Mg(OH)2·4H2O (PDF#70-0361), and the product is basic magnesium carbonate.
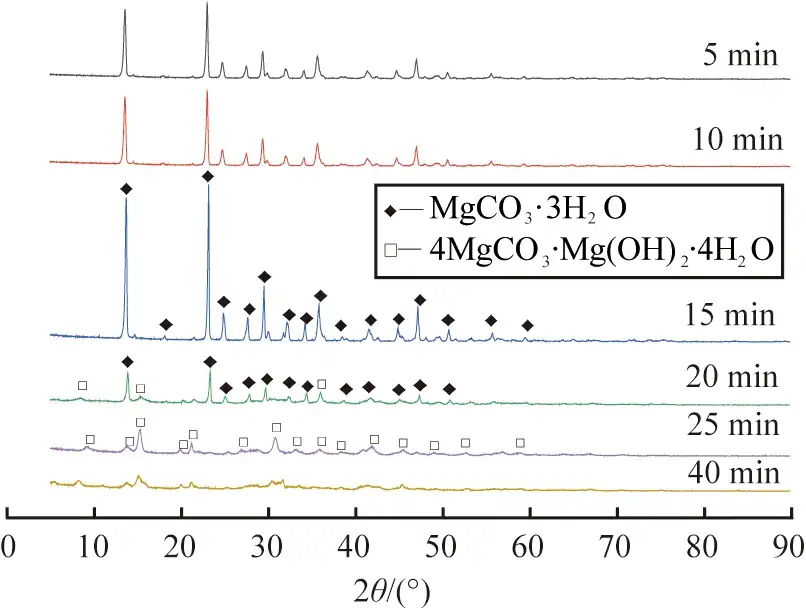
Figure 6 shows the SEM images of the products obtained at different reaction times. As shown in Figure 6 a), when the reaction time is 5 min, the product is mainly short and thick columnar crystals with uneven crystal distribution; when the reaction time is extended to 10 min to 15 min, the product is a rod-shaped crystal with a smooth surface, as shown in Figure 6 b) and c), where the average length of the product obtained at 15 min is about 60 μm; when the reaction time continues to increase to 20 min, floccules begin to appear on the surface of the rod-shaped crystals, which may be caused by the partial dissolution of the rod-shaped crystals, as shown in Figure 6 d); when the reaction time is 25 to 40 min, the rod-shaped crystals continue to dissolve and completely transform into flocculent crystals, as shown in Figure 6 e) and f).
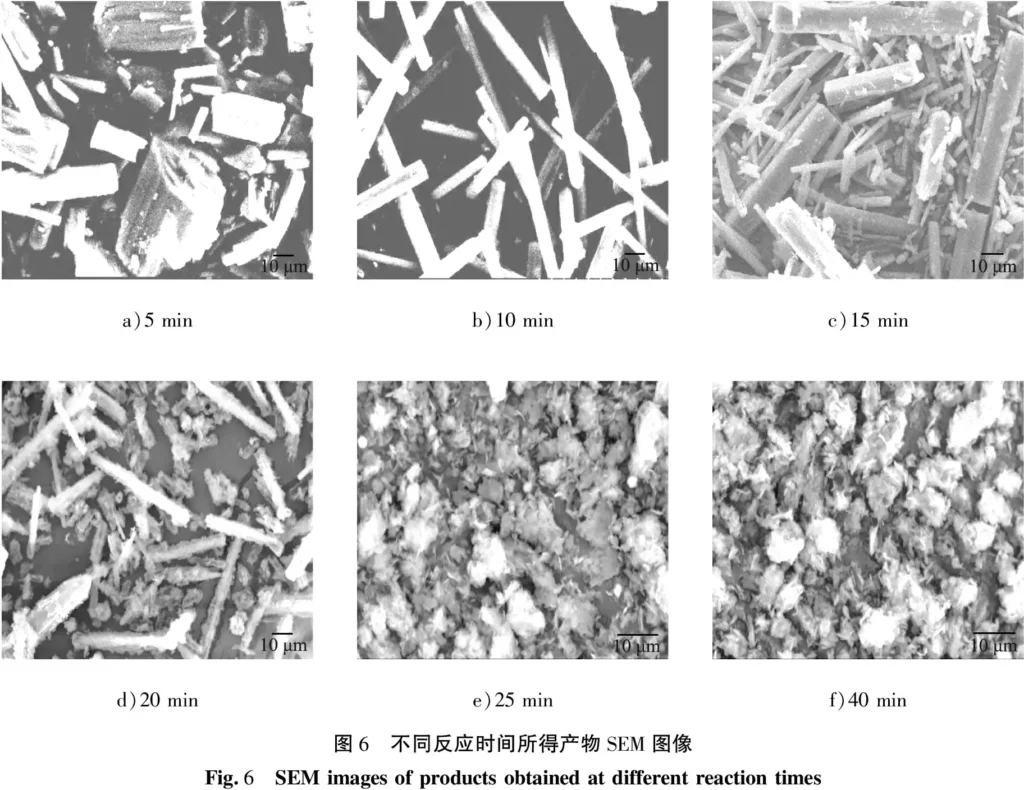
In summary, the reaction time has an important influence on the morphology and phase composition of the product. As the reaction time increases, the product gradually transforms from magnesium carbonate trihydrate to basic magnesium carbonate; combined with the results of XRD and SEM analysis, it is determined that the appropriate reaction time for preparing MgCO3·3H2O whiskers is 15 min.
2.4 Effect of aging time
When the concentration of reactants was fixed at 0.30 mol/L, the stirring rate was 300 r/min, the reaction temperature was 50 ℃, the reaction time was 15 min, and the aging time was 0, 0.5, 1, 3 and 6 h, the morphology of the obtained products is shown in Figure 7. When the aging time is 0 h, the growth time of amorphous particles in the solution is insufficient, and more crystals cannot be formed, resulting in a small number of products. As can be seen from the figure, when the aging time is 0.5 h, the product is a rod-shaped crystal with a smooth surface and uniform length; as the aging time is extended to 1 h, the morphology of the product does not change significantly, and the number of crystals does not increase significantly; when the aging time is further extended to 3-6 h, rod-shaped crystals and flocculent substances exist in the product at the same time. According to the previous research results of the research group [18-20], the flocculent substance is basic magnesium carbonate. This is because magnesium carbonate trihydrate is a metastable hydrated magnesium carbonate. Under certain conditions, it will be converted into a thermodynamically more stable basic magnesium carbonate. Considering factors such as product yield, 0.5 h was determined to be the appropriate aging time.
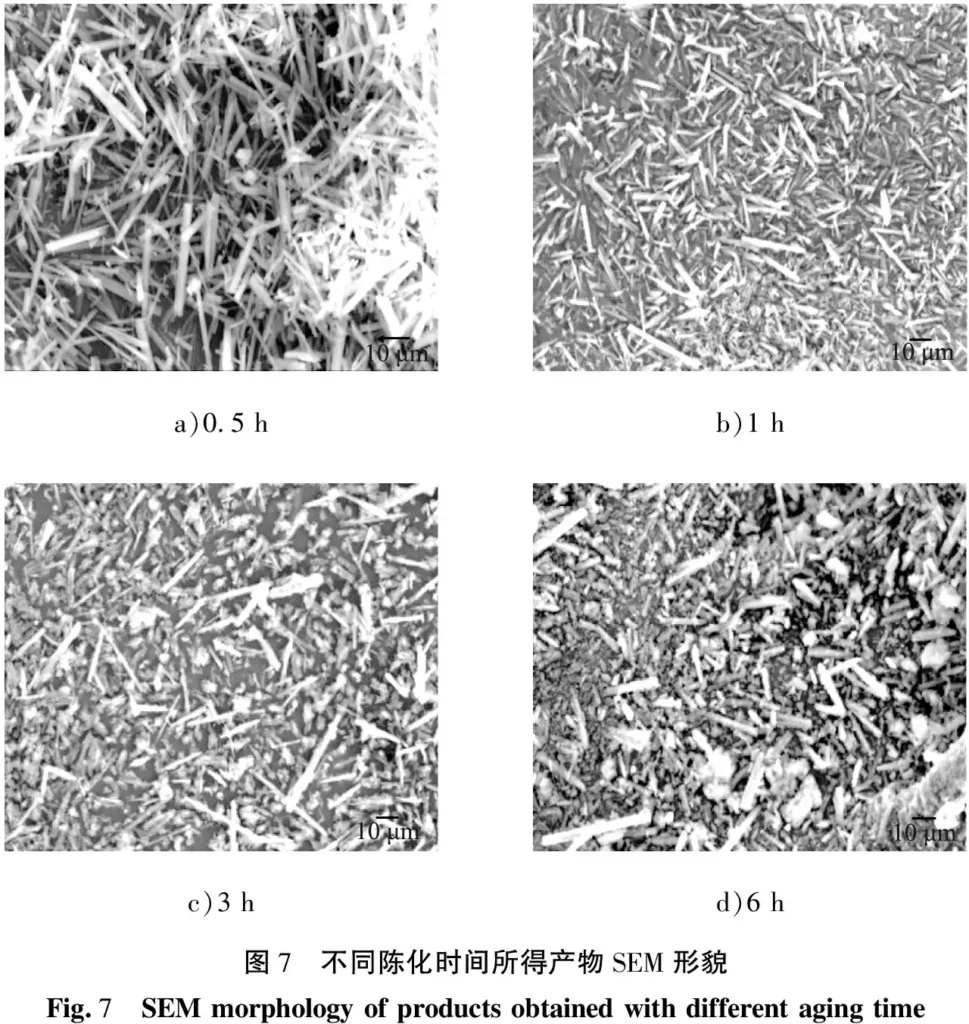
2.5 Effect of adding sodium citrate
The fixed temperature was 50 ℃, the stirring rate was 300 r/min, the aging time was 0.5 h, the addition amount of sodium citrate was 2% (calculated according to the volume fraction of the reaction solution), and the reaction time was 45 min. The effect of sodium citrate on the phase composition and morphology of the product was investigated. The results are shown in Figures 8 and 9. As can be seen from the figure, the morphology of the product obtained after adding sodium citrate is radial, and the base of the product XRD spectrum is flat, the half-width peak is narrow and the intensity is high. The product is still MgCO3·3H2O crystals, indicating that the addition of sodium citrate did not change the phase composition of the product, but had a significant effect on the morphology of the crystal. The reason may be that the selective adsorption of sodium citrate promoted the anisotropic growth of the crystal, causing the magnesium carbonate trihydrate crystal to grow toward several specific crystal faces.
2.6 Whisker growth mechanism
When a Na2CO3 solution of a certain concentration is added to a MgCl2·6H2O solution of the same concentration, the supersaturation of the reaction solution increases rapidly, and a large number of MgCO3·3H2O nuclei precipitate, attract each other, and grow in one dimension along the direction with the lowest solid-liquid interface energy; at the same time, the Na+ that loses extranuclear electrons and the Cl- that gains electrons combine under the action of electrostatic attraction. During the growth of rod-shaped MgCO3·3H2O crystals, the free Mg2+ in the reaction system continuously gathers at the solid-liquid interface to provide growth materials. It is inferred that the growth of MgCO3·3H2O whiskers conforms to the liquid-liquid-solid growth mechanism[21], and its schematic diagram is shown in Figure 10.
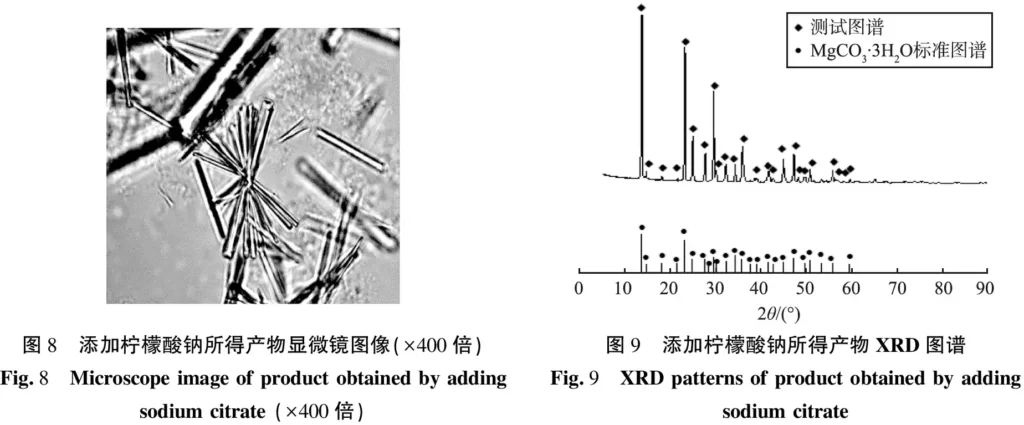
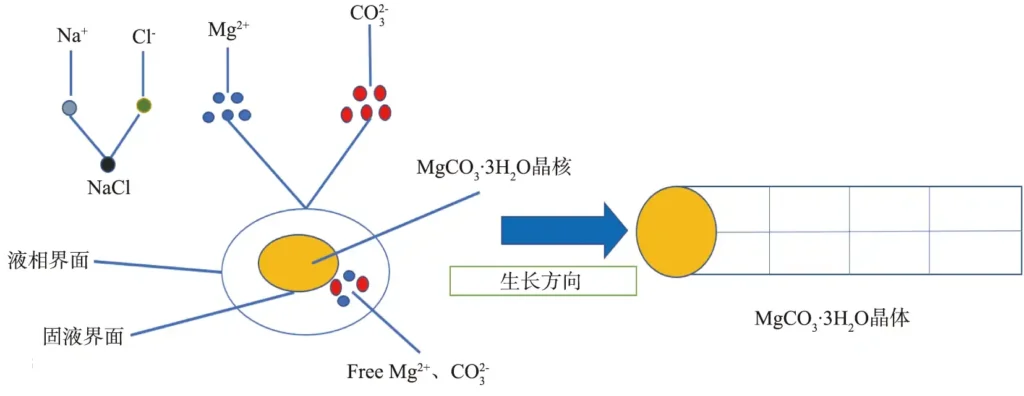
3 Conclusions
1) When the concentration of MgCl2·6H2O was 0.30 mol/L, the concentration of Na2CO3 was 0.30 mol/L, the reaction temperature was 50 ℃, the reaction time was 15 min, the stirring rate was 300 r/min, and the aging time was 0.5 h, rod-shaped MgCO3·3H2O crystals with an average diameter of about 5 μm were obtained.
2) The reaction time has a great influence on the crystal preparation process. When the reaction time is extended (>15 min), the rod-shaped magnesium carbonate trihydrate crystals are transformed into flocculent basic magnesium carbonate.
3) When the addition amount of sodium citrate in the MgCl2·6H2O-Na2CO3 system is 2%, well-crystallized radial MgCO3·3H2O crystals can be obtained.
4) In the MgCl2·6H2O-Na2CO3 system, the MgCO3·3H2O crystals grow one-dimensionally along the direction with the lowest solid-liquid interface energy, which is inferred to be in line with the liquid-liquid-solid growth mechanism.