Due to the strong polarity of magnesium hydroxide, the surface of the particles is positively charged and is easy to form secondary agglomeration, and its hydrophilicity allows the dried product to still contain moisture. Adding it directly to the polymer is not conducive to dispersion in the polymer material, and it is easy to create gaps at the interface with the polymer, resulting in poor compatibility. In order to increase the surface activity of the particles, thereby improving the dispersion of the powder, improving the compatibility with polymer materials, and improving the flame retardant properties of magnesium hydroxide, it needs to be modified.
Magnesium hydroxide is considered to be an environmentally friendly green flame retardant with great development potential due to its wide source of raw materials, good flame retardant properties, non-toxicity, and non-corrosiveness.
Magnesium hydroxide has high decomposition energy, which is 140°C higher than the thermal decomposition temperature of currently commonly used inorganic flame retardants. It can enable polymer materials to withstand higher processing temperatures, which is beneficial to speeding up extrusion speed and shortening molding time. It also has Helps improve flame retardant efficiency.
Flame retardant mechanism of magnesium hydroxide
The reason why magnesium hydroxide has a flame retardant effect is closely related to its decomposition reaction at high temperatures. When the ambient temperature reaches 340~490°C, Mg(OH)2 begins to thermally decompose, forming magnesium oxide and releasing crystallized H2O. The decomposition equation is:
Mg(OH)2 → MgO+H2O
△G°=-49.8kJ/mol.
The decomposition reaction reaches its peak at 430°C and is completed at 490°C, leaving MgO. Crystallized H2O absorbs a large amount of heat, which will lower the surface temperature of the material in the flame. The released water vapor dilutes the oxygen on the surface, making combustion difficult, and has the effect of inhibiting the decomposition of the polymer and the flammable gas produced by cooling; in addition, decomposition The generated magnesium oxide is also a good refractory material. It forms a carbonized layer on the surface of the material, which isolates the flammable materials in the product from contact with the oxidizing/high-temperature environment and prevents the entry of oxygen and heat. Therefore, when the combustion source disappears, the fire will automatically extinguish, thereby achieving the purpose of flame retardancy.
Research on modification of magnesium hydroxide flame retardant
Since magnesium hydroxide has strong polarity, the surface of the particles is positively charged, and it is easy to form secondary agglomeration, and its hydrophilicity means that the dried product still contains moisture. Adding it directly to the polymer is not conducive to dispersion in the polymer material, and it is easy to create gaps at the interface with the polymer, resulting in poor compatibility. In order to increase the surface activity of the particles, thereby improving the dispersion of the powder, improving the compatibility with polymer materials, and improving the flame retardant properties of magnesium hydroxide, it needs to be modified.
Ultrafine
The ultrafine refinement of magnesium hydroxide is to crush the magnesium hydroxide powder and use appropriate means to reduce the particle size as much as possible, even to the nanometer level, increase the contact area between the flame retardant and the polymer matrix, and strengthen the magnesium hydroxide. Affinity with polymers, improve compatibility between the two, achieve the purpose of reducing dosage and improving flame retardant efficiency. After magnesium hydroxide is ultrafine, it will cause less wear and tear on equipment. It can be widely used in polypropylene, polyethylene, polyvinyl chloride, high-impact polystyrene and ABS resin.
Surface modification
Magnesium hydroxide is very polar, has a positive charge on the surface, is hydrophilic, and is easy to agglomerate. It has poor compatibility with polymer materials. Therefore, magnesium hydroxide must be surface treated. Commonly used methods include the coupling agent method. , anionic surfactant method, microencapsulation method and surface grafting method.
Coupling agent modification
The commonly used surface modifiers for magnesium hydroxide flame retardants are coupling agents. Coupling agents are a class of substances with an amphoteric structure. Part of the groups in their molecules has affinity with organic polymers, and another part has affinity with magnesium hydroxide. These affinities are provided by intermolecular forces and chemical bonds. During the production and processing of polymer materials, hydrophilic magnesium hydroxide is incompatible with polymers, and they can be closely combined through the bridging effect of coupling agents.
Commonly used coupling agents mainly include: silanes, titanates, chromium, zirconium compounds and higher fatty acids, alcohols, esters and other categories.
Mechanism of action of coupling agents: Silane coupling agents are a class of low-molecular organic silicon compounds with special structures, which have a more prominent effect on improving the strength and heat resistance of polymer materials. Since R in silane coupling agents has specific functional groups, different polymers need to select different coupling agents to wrap magnesium hydroxide; titanate coupling agents can give polymer materials better comprehensive properties, that is, good fluidity at processing temperature and high strength and toughness at use temperature, among which the improvement of impact resistance is more significant. Since Mg (OH)2 has strong water absorption and high surface humidity, it is better to select moisture-resistant monoalkoxy pyrophosphate titanate.
Anionic surfactant modification
Anionic surfactants are mainly higher fatty acids and their derivatives. On the one hand, they contain hydrophilic groups that can interact with the hydrocarbon groups on the surface of magnesium hydroxide. Multiple hydrophilic groups are linked to the surface of magnesium hydroxide to improve adsorption fastness; On the other hand, polymers are long-chain molecules, and their polymer chains can act as steric hindrance to reduce the agglomeration of magnesium hydroxide and form particles with smaller particle sizes. Compatible with organic resin matrix, long-term use, and not easy to desorb, anionic surfactants have become a promising modifier and have received more and more attention.
Microencapsulation modification
Microcapsule technology is to coat magnesium hydroxide with natural or synthetic polymer compounds to obtain tiny particles. Generally, the particle size is in the millimeter or micron range to form a flame retardant. When the composite material is heated and burned, the capsule wall can melt and rupture immediately. Release the flame retardant to achieve the purpose of flame retardancy, which can improve compatibility and thermal stability.
The surface modification of microcapsule technology can not only improve the compatibility between magnesium hydroxide and polymer materials, but also effectively reduce the performance deterioration caused by the addition of magnesium hydroxide to polymer materials and improve stability. Microcapsule flame retardants are non-toxic and harmless during production and use. They do not produce thick smoke and toxic gases when burned, and have no environmental pollution. Therefore, they have become one of the research hotspots in the field of flame retardancy.
Surface graft modification
Surface graft modification refers to directly connecting one end of the modifier or solubilizer to the polymer material matrix or the surface of the inorganic particles to form a macromolecular modifier, thereby improving the interface properties of inorganic and organic polymers.
Synergy with other flame retardants
Organically combining magnesium hydroxide with other flame retardants or flame retardant synergists through a certain method can significantly increase the flame retardant temperature, increase heat absorption, and reduce the filling amount, thus improving the flame retardant efficiency. exert its comprehensive flame retardant effect. For example, common flame retardant synergists include: aluminum hydroxide, halogen, antimony oxide, organic silicon compounds, red phosphorus and phosphides, metal oxides, metal chelates, zinc borate, graphite, organic soil, etc.
Application of magnesium hydroxide flame retardant
Magnesium hydroxide flame retardant has become a research hotspot in the field of flame retardant materials due to its environmental protection, non-toxicity and high stability. As an inorganic environmentally friendly flame retardant, magnesium hydroxide can release bound water when it is thermally decomposed, absorb a large amount of latent heat, thereby reducing the surface temperature of the material in the flame, inhibiting the decomposition of the polymer and cooling the generated combustible gas. In addition, the decomposed magnesium oxide has good fire resistance and can further improve the fire resistance of the material. Therefore, magnesium hydroxide flame retardant has broad application prospects in the field of flame retardant materials.
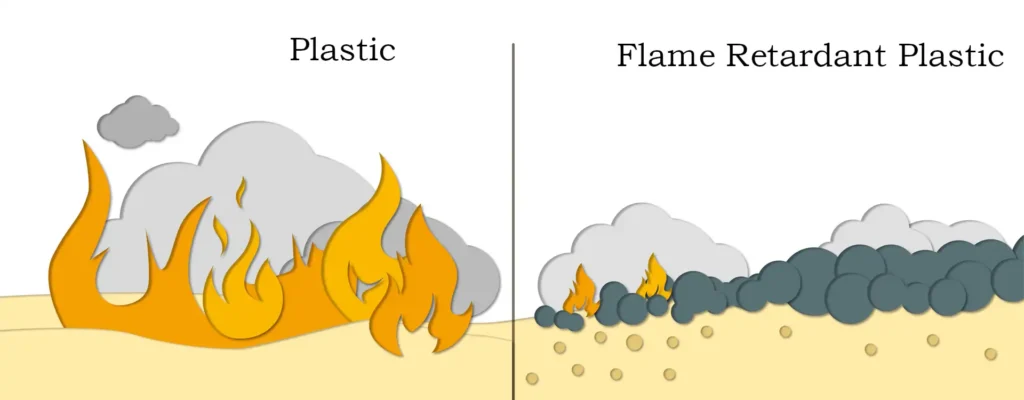
Magnesium hydroxide flame retardant has a wide range of applications, involving plastics, rubber, chemicals, building materials and other industries. In the plastics industry, magnesium hydroxide can be added as a flame retardant or flame retardant filler to polymer materials such as polyethylene and polypropylene to improve the flame retardant properties of plastics. At the same time, magnesium hydroxide can also be used for flame retardant treatment of rubber products to improve the fire resistance and safety of rubber. In addition, magnesium hydroxide flame retardant also plays an important role in the fields of chemical industry, building materials and so on.
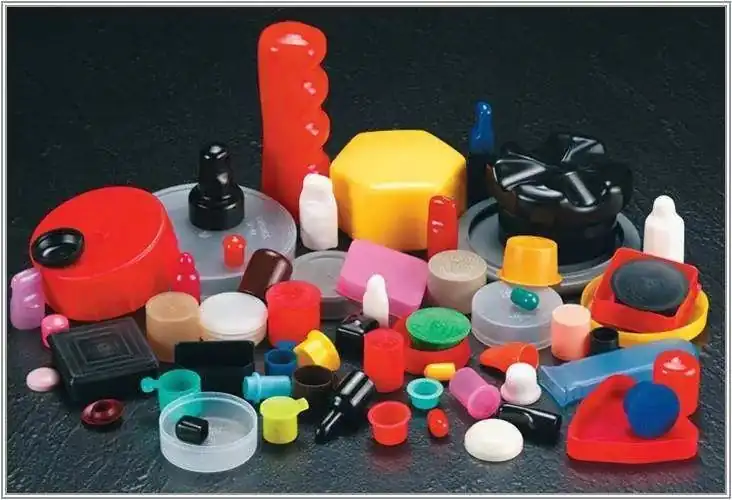
In addition to traditional application areas, magnesium hydroxide flame retardant also shows great potential in new energy, environmental protection and other fields. In the field of new energy, magnesium hydroxide can be used as an additive for battery materials to improve the safety and stability of batteries. In the field of environmental protection, magnesium hydroxide can be used in flue gas desulfurization treatment and other fields, giving full play to its strong adsorption capacity, good buffering performance, heat resistance and other characteristics, and making contributions to environmental protection.