In recent years, halogen-free flame retardants such as magnesium hydroxide (MH), aluminum hydroxide (AH) and magnesium aluminum hydroxide (MAH) have been widely studied due to their advantages such as green and pollution-free, and their use has also become a trend.
Among them, MH is an important additive inorganic flame retardant, accounting for a large proportion of the entire flame retardant market and has a clear growth trend. Its advantages are high stability, low volatility, low smoke toxicity and low cost. Its disadvantages are large filling volume, low bonding force with polymers, poor compatibility, and great influence on the processing and mechanical properties of polymers. Therefore, it is very necessary to modify the surface of MH powder to improve its dispersibility in polymers. It has been found that the surface treatment method using low relative molecular weight coupling agents or surfactants is quite effective.
Aluminate coupling agent (ACA) is an important surfactant. They are usually light yellow to white in color, have high surface reactivity, high decomposition temperature, and are environmentally friendly. ACA has two functional groups, hydrophilic and hydrophobic. The hydrophilic group can react chemically with the polar group on the MH powder to graft the hydrophobic group on the powder, thereby greatly reducing the surface energy and improving the compatibility of the MH powder with the polymer.
There have been a lot of reports on the surface modification of MH. Commonly used modifiers include fatty acids and their salts, silane coupling agents and titanate coupling agents. Wang Chen et al. used (3-oxobutyric acid ethyl ester-O1’,O3) di(propanol-2-root) aluminate coupling agent (ACA) to wet-modify the surface of magnesium hydroxide. The results showed that:
1) Infrared spectroscopy, X-ray diffraction, thermogravimetric analysis, scanning electron microscopy, and energy spectrometer characterization results show that the aluminate coupling agent successfully modified the magnesium hydroxide and the modification did not destroy the structure of the magnesium hydroxide crystal, but only acted on the surface of the magnesium hydroxide. At the same time, it was found that the thermal stability of the magnesium hydroxide after modification was improved. Wet-modification of magnesium hydroxide by aluminate coupling agent can improve the lipophilicity and dispersibility of the powder.
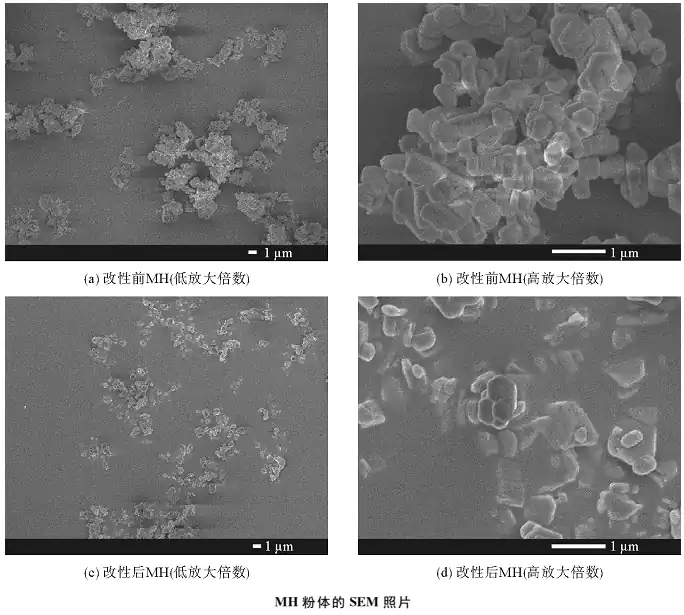
2) Tests such as sedimentation time, oil absorption rate and suspension viscosity show that the dispersibility and compatibility of modified magnesium hydroxide powder in organic solvents are better than those of unmodified magnesium hydroxide powder.
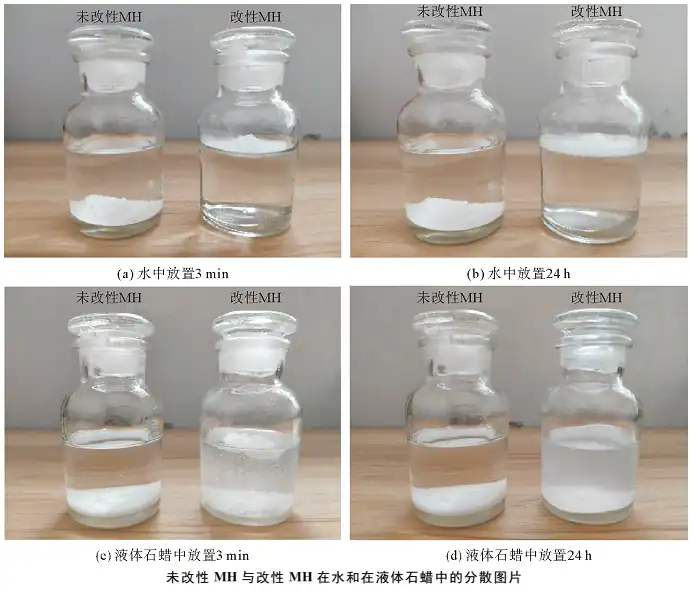
3) The optimal amount of aluminate coupling agent to modify magnesium hydroxide powder is 4% of its mass fraction. When the amount of aluminate coupling agent added is greater than 4%, the modification effect of magnesium hydroxide powder does not improve, and the dispersibility and compatibility of magnesium hydroxide powder in organic solvents cannot be significantly improved.