Magnesium oxide (MgO) exhibits significant advantages as an efficient, low-pollution, and mild silica removal material in the preparation of high-purity water. It can precisely address the challenge of removing trace amounts of silica, a difficult-to-eliminate contaminant, providing a more reliable water quality guarantee for industries such as electronics, photovoltaics, and pharmaceuticals.
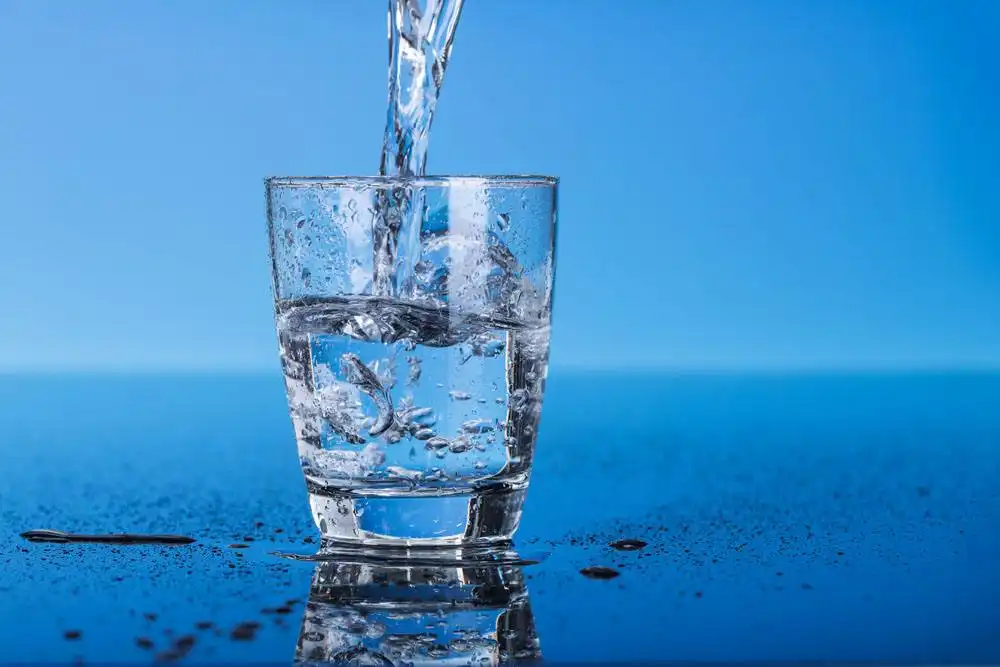
I. Background: The Silica Problem in High-Purity Water
High-purity water, especially electronic-grade ultrapure water (UPW), is widely used in: integrated circuit manufacturing (semiconductor cleaning), the photovoltaic industry (silicon wafer cleaning), precision instrument and medical device rinsing, and laboratory ultraclean reaction systems. In these applications, the content of impurities in the water is extremely demanding, with total organic carbon (TOC), metal ions, dissolved gases, and silicon (Si) requiring control at the ppb (parts per billion) or even ppt (parts per trillion) level.
Among these, silicon (especially soluble or colloidal silicon) is one of the most difficult parameters to control because it:
Easily forms silicic acid colloids, which are not easily removed by traditional filtration.
Can precipitate during heating or drying, forming micro-contamination on wafer or equipment surfaces.
Affects the stability of critical processes such as photolithography and etching.
II. Silica Removal Mechanism and Reaction Pathway of Magnesium Oxide
Magnesium oxide slowly hydrolyzes in water to form magnesium hydroxide. Its weak alkalinity and slow-release properties are well-suited for the mild removal of silicate in ultrapure water pretreatment:
Key Reactions:
Mg2++SiO32−→MgSiO3↓
Or in the metasilicate state:
Mg(OH)2+H2SiO3→MgSiO3↓+2H2O
The generated magnesium silicate precipitate is insoluble in water and can be removed by microfiltration membranes or nanofiltration systems.
III. The Position of Magnesium Oxide Silica Removal in the High-Purity Water Process Chain
High-purity water preparation typically includes the following stages: pretreatment (sand filtration, activated carbon), softening/reverse osmosis (RO), mixed bed/EDI deionization, and polishing treatment (ion exchange, ultraviolet, ultrafiltration).
Magnesium oxide can be used in:
The front end of RO membrane systems: Reducing silica fouling on the membrane surface and extending membrane life.
Before ion exchange/mixed beds: Removing non-ionic silicon species and improving exchange efficiency.
Before the terminal “polishing stage”: In conjunction with fine filtration systems to achieve ppb-level silicon control.
IV. Advantages of Magnesium Oxide in Silica Removal
Simple Dosing and Mild Reaction: Suitable for most pretreatment systems.
No Introduction of Heavy Metal Impurities: The reaction product is a stable precipitate that is easy to filter or adsorb.
No Corrosion to Membrane Materials or Resin Systems: Does not affect subsequent purification processes.
More Environmentally Friendly Compared to Traditional Aluminum and Iron Salts: The generated by-products are easier to manage.