With the rapid development of the electronics industry, the geometric size of electronic components is getting smaller and small and highly integrated, resulting in the heat generated inside the electronic components cannot be emitted in time, which will affect the performance and service life of electronic components. In addition, the most popular industries such as new energy vehicles and AI are also facing a fatal “heat dissipation” problem.
Polymer materials, also known as polymer materials, have excellent electrical insulation performance, easy processing and molding, low cost, light quality and good corrosion resistance. Therefore application. Generally speaking, the vast majority of polymer materials themselves have poor thermal conductivity, and it is difficult to meet the heat dissipation requirements required in the above areas.
Since most of the artificial polymer materials are very poor in thermal conductivity, it is necessary to produce materials with good thermal conduction characteristics. The most commonly used method is to fill the polymer with high heating rate.
Common heat -conducting fillings can be roughly divided into three categories, first type of metal fillers, the second type of ceramic fillers and the third type of carbon filler.
Although metal particles, carbon materials (such as graphene, single -wall/multi -wall carbon nanotubes, etc.), although it has a high heating rate and is conducive to the improvement of polymer thermal conductivity, these fillers often change the heat conduction performance It has also changed the electrical insulation performance of the polymer. For example, it leads to extremely high conductivity and high dielectric constant without being applied to a polymer base composite material that is both high -thermal conductivity and excellent insulation performance. Therefore, the field of insulation is more concerned about ceramic fillers with a very high heating rate and good insulation performance.
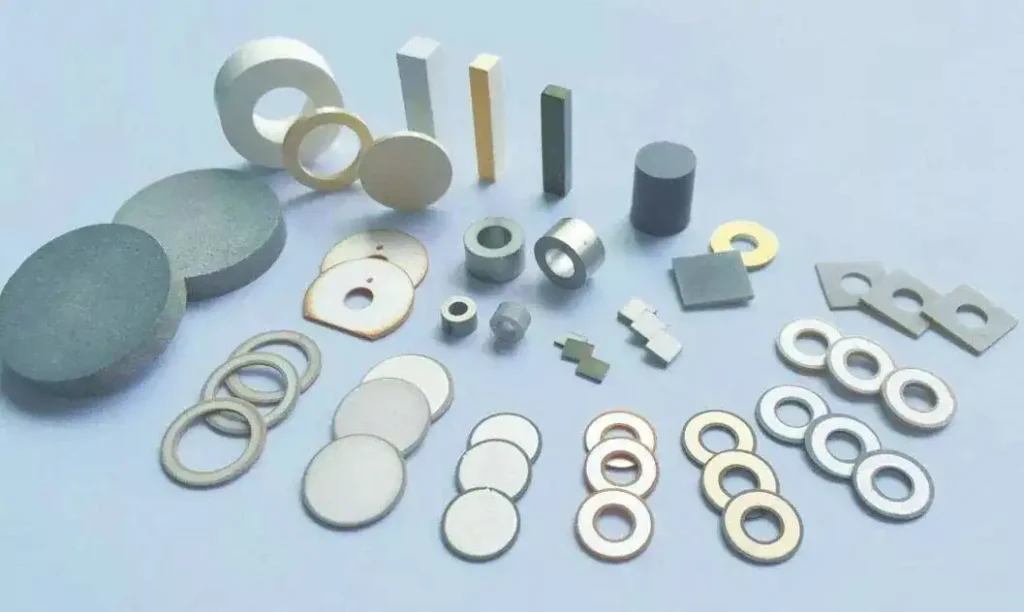
Among all ceramic fillers, boron nitride, alumina and aluminum nitride are applied. The thermal conductivity of boron nitride and aluminum nitride is extremely prominent, but the price is expensive. One alumina has low thermal thermal conductivity than boron nitride and aluminum nitride, but the cost is low, so it is the most widely used. Although the thermal conductivity of magnesium oxide is lower than that of boron nitride and aluminum nitride, it is higher than alumina, 36W/(m · k), and the cost is not high. one.
Magnesium oxide, commonly known as magnesia, also known as lamp powder, magnesium sand, magnesium oxygen, etc. It is a ionic compound that is white solid at room temperature. Its chemical structure is MgO, no smell, no toxicity, belonging to Cube crystal system is a typical NACL crystal structure. Under normal pressure, the pure MgO melting point can reach 2852 ° C, and the boiling point is also very high at about 3600 ° C. At 25 ° C, its relative density is 3.58g/cm3, and it has excellent thermal conductivity. MgO is easily soluble in dilute acid, insoluble in water and water -free ethanol.
There are many types of magnesium oxide products. Among them, magnesium oxide powder with special appearance is a type of material studied by many scholars in recent years. Compared with magnesium oxide in traditional irregular forms, magnesium oxide with special appearance is unique to its unique. The surface nature has a special application. In particular, compared with ordinary magnesium oxide, the heat conduction effect of spherical magnesium oxide is better. After processing, it can improve the thermal conductivity to 40-60W/(m · k). And it can increase the proportion of filling, so it has better cost -effectiveness.
In addition, adding magnesium oxide to plastics In addition to the role of thermal conductivity, it can also play a role in flame retardant. Generally, the flame retardant of plastic is very low, and accidents are prone to occur. For example, in the LED light, if the LED light is used for a long time, the temperature will be very high. If the calories cannot be released in time, it is easy to cause accidents. The general flame retardant is zinc, aluminum and magnesium oxide. The flame retardant effect of borate is the best. It has been accepted by most people, but the reserves of boron are not high, so the price is relatively high, which undoubtedly increases the manufacturing cost, which is very unfavorable for enterprises. It is easier to get alumina and magnesium oxide, but as far as the flame retardant effect of the two kinds of flame retardants is concerned, the flame retardant effect of magnesium oxide is better, but the preparation process of spherical magnesium oxide is backward than the spherical aluminum oxide, so Alumina is now widely used by flame retardant additives. However, the high -performance flame retardant of spherical magnesium oxide makes the industry very optimistic about its prospects.
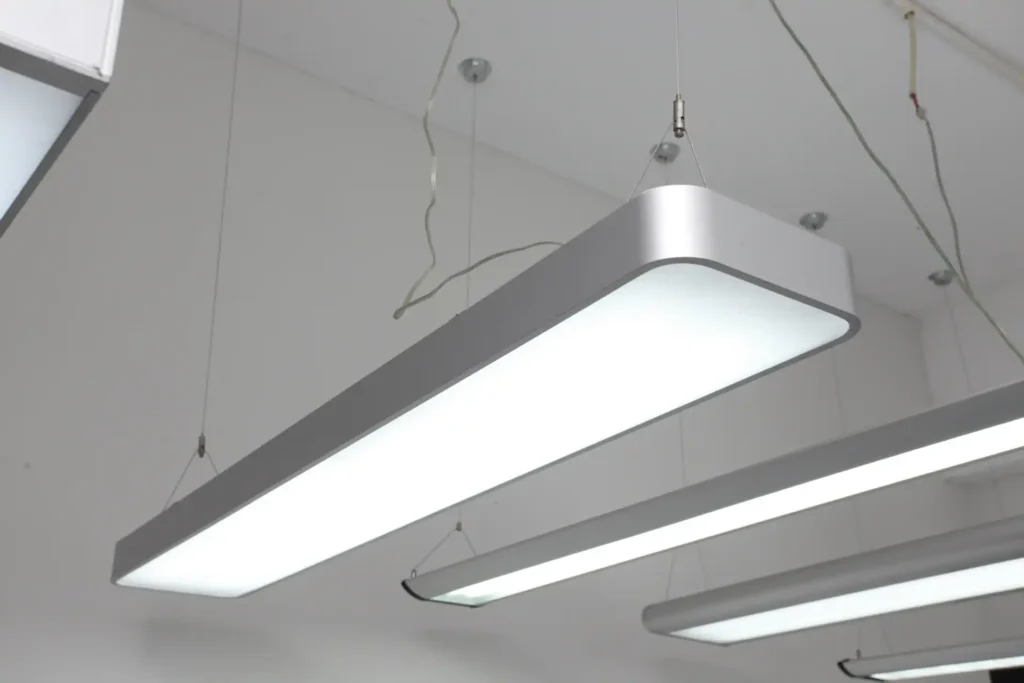
In general, magnesium oxide is a very good thermal padding, which can significantly improve the thermal conductivity of polymer composite materials. Moreover, by changing the shape and size of magnesium oxide, we can further optimize its thermal conductivity to meet the application requirements of different scenarios, such as magnesium oxide. This is of great significance to promote the high value and utilization of my country’s magnesium resources and improve the safe operation of electronic products and new energy vehicles.