Messi Biology states that magnesium hydroxide can be safely added to flexible PVC, primarily serving as a flame retardant and functional filler. However, performance needs to be balanced through formulation optimization (e.g., compounding with plasticizers, surface modification). It is recommended to prioritize high-purity (≥90%) magnesium hydroxide to avoid impurities affecting performance. A recommended addition amount is 30%-50%, with the ratio adjusted based on mechanical performance testing. Attention should be paid to processing temperature control to avoid exceeding the decomposition threshold of magnesium hydroxide (340°C).
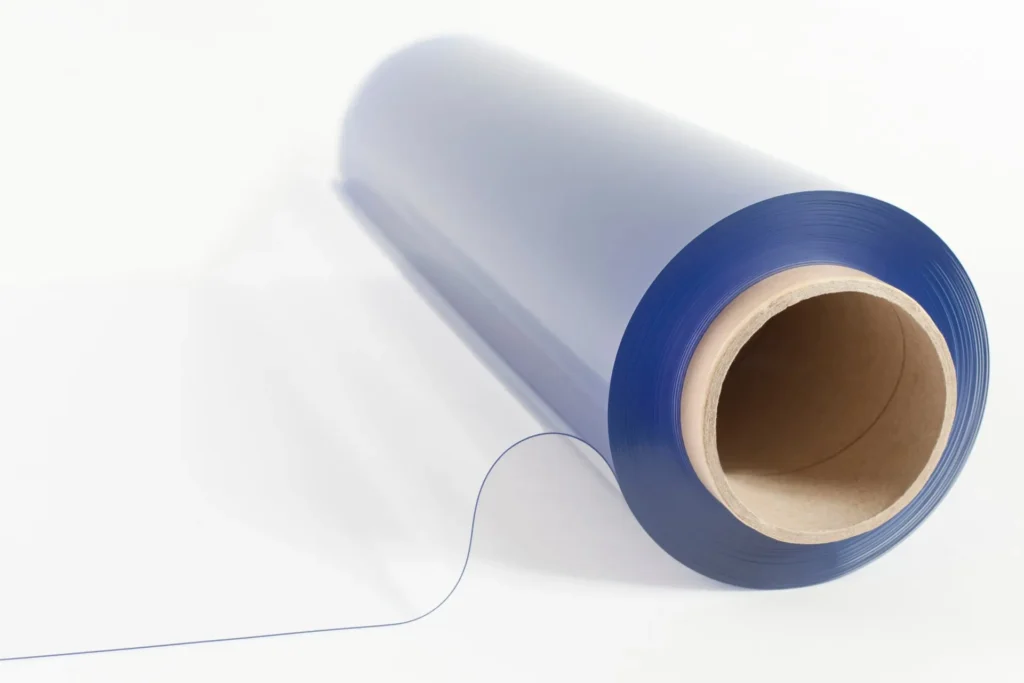
I. Main Functions of Magnesium Hydroxide in Flexible PVC
Enhanced Flame Retardant Performance
Magnesium hydroxide (Mg(OH)₂) is an efficient inorganic flame retardant, whose mechanism includes:
- Endothermic Decomposition: Decomposes into magnesium oxide and water vapor at around 340°C, absorbing a large amount of heat, lowering the material surface temperature, and delaying combustion.
- Reaction Equation: Mg(OH)₂ → MgO + H₂O↑
- Gas Dilution: The released water vapor dilutes flammable gases (such as HCl, alkanes) and oxygen concentration, inhibiting the combustion chain reaction.
- Barrier Formation: The generated magnesium oxide residue covers the material surface, forming a ceramic-like protective layer that insulates heat and oxygen.
- Smoke Suppression Effect: Compared to traditional antimony-based flame retardants, magnesium hydroxide can reduce the release of smoke and toxic gases (such as dioxins).
Enhanced Thermal Stability
- Neutralizes hydrogen chloride (HCl) produced by PVC pyrolysis, delaying material degradation and color change.
- Its endothermic decomposition characteristics can reduce thermal damage during processing, extending product lifespan.
Improved Mechanical Properties
- As a filler, it can improve hardness, abrasion resistance, and impact resistance, particularly suitable for applications like wire and cable sheathing, conveyor belts, etc.
- Surface modification (such as silane treatment) can optimize its compatibility with the PVC matrix, reducing negative impacts on tensile strength.
II. Formulations and Processes in Practical Applications
Typical Addition Ratios
- Flame retardant effect requires higher filler loading (typically 40%-60%), necessitating a balance between flame retardancy and mechanical properties.
- In flexible PVC, it is often used synergistically with plasticizers (such as DOP) and composite stabilizers (such as HL-45).
Modification Techniques
- Ultrafine Treatment: Nano-grade magnesium hydroxide (such as GY-6000) can enhance flame retardancy efficiency and reduce smoke density.
- Surface Activation: Treatment with stearic acid, silane coupling agents can improve dispersion and reduce agglomeration.
III. Advantages and Disadvantages Comparison
Advantages | Disadvantages |
Environmentally friendly and non-toxic, complies with RoHS standard | High addition amounts may reduce material toughness |
Possesses triple functions: flame retardant, smoke suppression, and filling | Requires surface modification to optimize processing performance |
High decomposition temperature (340-490°C) | Poor acid resistance, needs to avoid acidic environments |
IV. Application Cases and Industry Practices
- Wires and Cables: Magnesium hydroxide flame-retardant flexible PVC is used for insulation sheathing, improving fire resistance rating and reducing smoke during fires.
- Conveyor Belts/Films: Compounded with antimony trioxide, partially replacing antimony-based flame retardants to reduce costs and maintain performance.
- Building Materials: Such as flame-retardant tarpaulins, wall panels, etc., meeting fire safety regulations through magnesium hydroxide addition.