Hebei Messi Biology Co., Ltd. stated that my country’s flue gas desulfurization began in the 1970s, and the limestone-gypsum desulfurization process is the main one. Because flue gas desulfurization costs a lot of money, its development has been slow. As my country’s economic strength increases and environmental protection regulations become increasingly perfect, flue gas desulfurization is imperative.
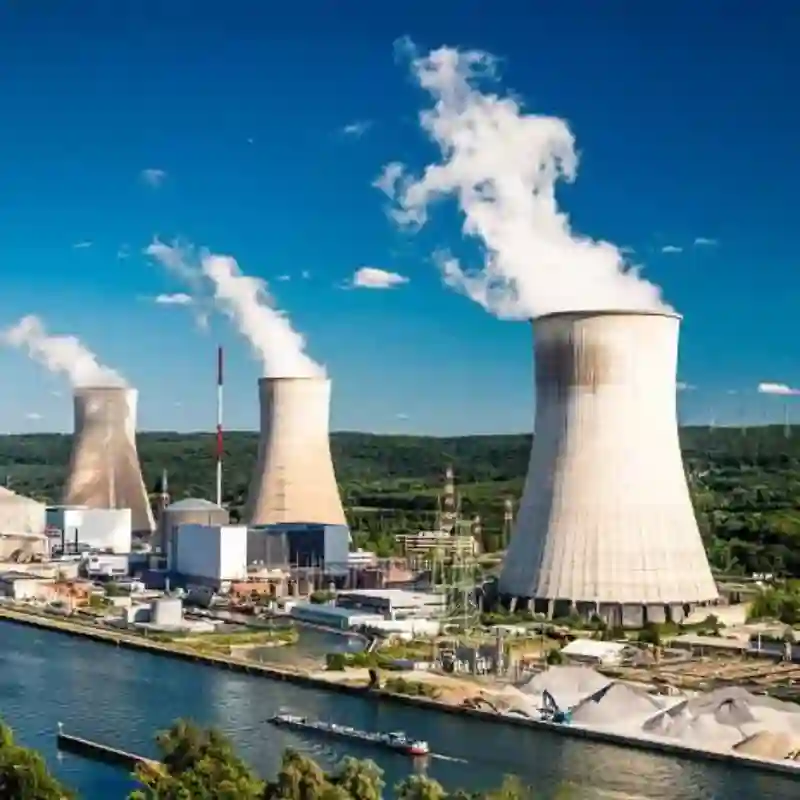
Japan was the first to use magnesium compounds in the flue gas desulfurization process. Then it started to be applied in European and American countries. Magnesium hydroxide desulfurization method uses magnesium hydroxide as an alkaline desulfurizer to absorb sulfur dioxide in the flue gas and generate magnesium sulfite. Part of it is recycled, and the other part is oxidized with air to generate magnesium sulfate. Liquid magnesium sulfate can be reprocessed and reused. The reaction mechanism is that sulfur dioxide first contacts water to generate sulfurous acid, which then reacts with magnesium sulfite in the circulating fluid to generate magnesium bisulfite. Magnesium bisulfite reacts with magnesium hydroxide to obtain magnesium sulfite, which is then oxidized by air to produce magnesium sulfate. The reaction formula is as follows:
SO2+H2O=H2SO3
H2SO3+2MgSO3=Mg(HSO3)2
Mg(HSO3)2+Mg(OH)2=2MgSO3+2H2O
2MgSO3+O2=2MgSO4
Magnesium sulfite in the circulating fluid becomes the main body of the reaction. Although magnesium hydroxide has poor solubility, magnesium sulfate and magnesium sulfite have good solubility. The above-mentioned desulfurization reaction takes advantage of their solubility properties and the fact that magnesium salts are easily oxidized. As long as the pH value of the solution is controlled within the range of 6 to 6.5 (not <5), and conditions such as magnesium sulfite concentration and circulating liquid volume are controlled at the same time, the operation can be stable, scale formation and pipeline clogging can be avoided, and the desulfurization rate can reach about 95%.
The magnesium hydroxide desulfurization process consists of four processes: cooling, dust removal and absorption, oxidation and filtration. Compared with other desulfurization methods, the use of magnesium hydroxide for desulfurization has the advantages of high efficiency, easy operation, relatively simple industrial process, recyclable by-products and high economic benefits.