Magnesium oxide (MgO) is an important functional raw material in ceramic glazes. It can significantly improve the quality of the glaze layer by adjusting the melting behavior, expansion matching, optical properties and mechanical strength. In practical applications, it is necessary to combine the characteristics of the body, the firing process and the target effect, and scientifically design the formula to achieve the best balance. Its application is mainly reflected in the following aspects:
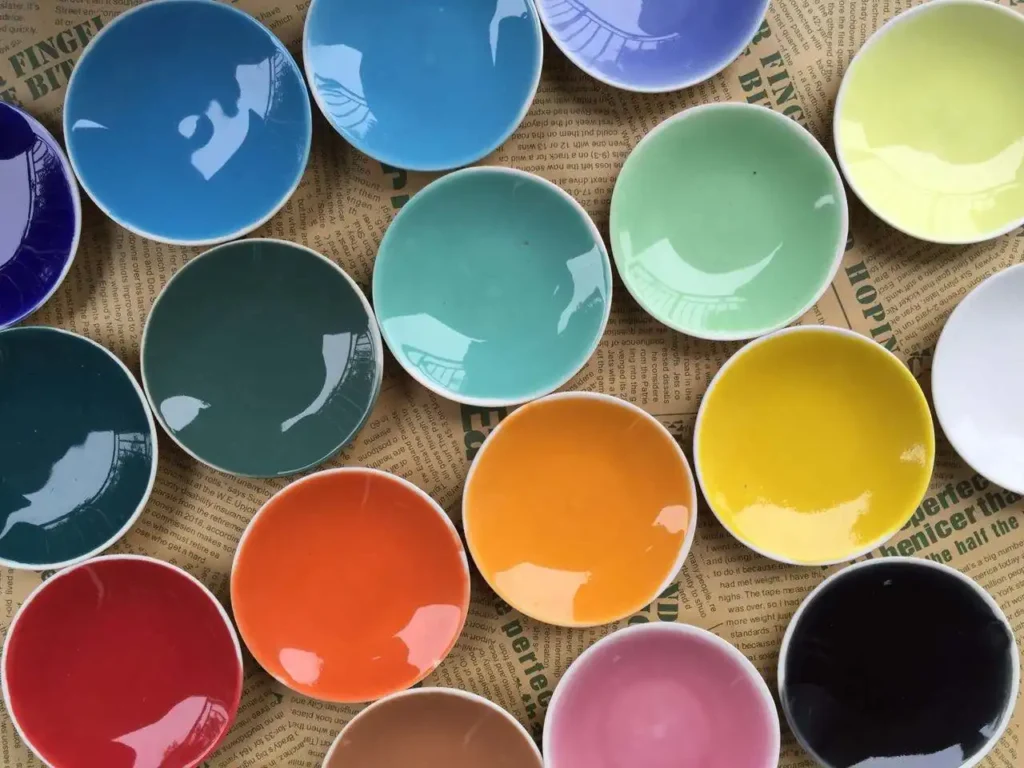
1. Adjust the melting temperature and fluidity of the glaze
Lower the melting temperature: As an alkaline oxide, magnesium oxide reacts with silicon dioxide (SiO₂) at high temperature to form magnesium silicate, which reduces the melting temperature of the glaze and promotes uniform melting of the glaze layer.
Improve fluidity: Adding an appropriate amount can reduce the viscosity of the glaze, enhance high-temperature fluidity, make the glaze smoother and cover more evenly.
2. Adjust the thermal expansion coefficient of the glaze layer
Match the body and glaze combination: The thermal expansion coefficient of magnesium oxide is low (about 13.5×10/℃). Adding it to the glaze can reduce the overall expansion coefficient and reduce cracks (such as cracking or peeling) caused by the expansion difference between the glaze layer and the body.
3. Influence on the optical properties of glaze
Opacification effect: At high temperature, magnesium oxide can form magnesium aluminum spinel (MgAl₂O₄) with aluminum oxide (Al₂O₃), producing an opacification effect and enhancing the opacity of the glaze layer (such as commonly used in white glaze).
Gloss adjustment: Excessive magnesium oxide may lead to a matte effect on the glaze, while adding an appropriate amount can balance the gloss and texture.
4. Improve the mechanical properties of the glaze
Hardness and wear resistance: Magnesium oxide can improve the microhardness and wear resistance of the glaze layer, and is suitable for ceramic products that require wear resistance such as floor tiles and tableware.
Chemical corrosion resistance: The alkaline oxide characteristics can enhance the stability of the glaze to acids and alkalis and extend its service life.
5. Synergistic effect with other ingredients
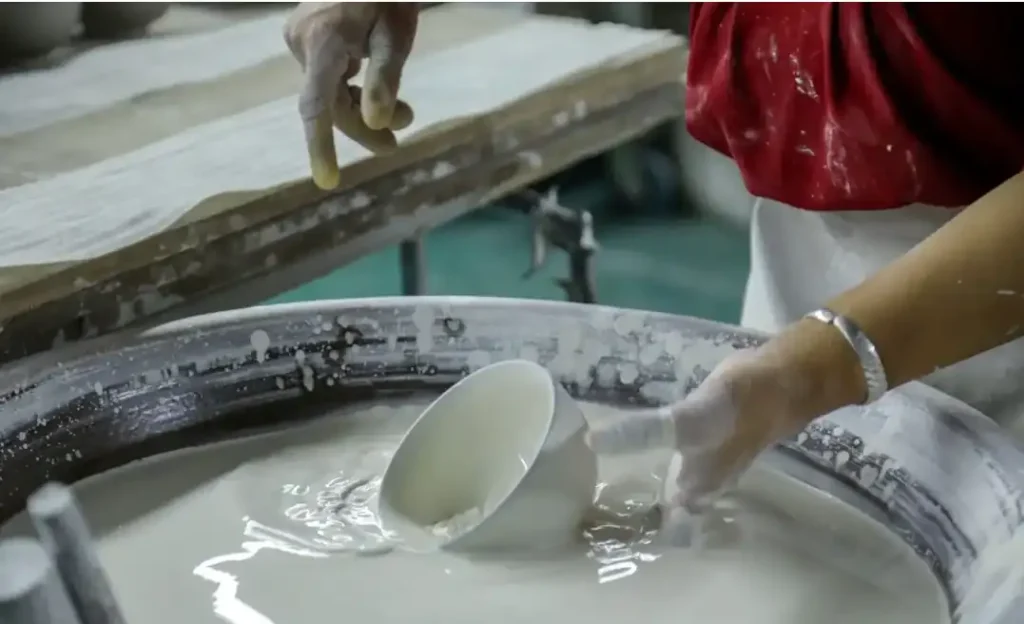
Compared with calcium oxide (CaO): The fluxing effect of magnesium oxide is weaker than that of calcium oxide, but it has better thermal stability and can reduce pinholes and bubbles in the glaze.
Combined with zinc oxide (ZnO): In crystalline glaze, magnesium oxide can promote crystal growth (such as willemite crystals) to form a unique decorative effect.
6. Typical application cases
Architectural ceramics: Add 1-3% MgO to floor tiles and exterior wall tiles to improve wear resistance and frost resistance.
Daily ceramics: Use magnesium oxide to adjust whiteness and light transmittance in bone china glaze.
Art glaze:
① Matt glaze: Add 5-8% MgO, combined with high aluminum formula to form a delicate matte surface.
② Crystalline glaze: Combined with zinc oxide to control the morphology and distribution of crystal flowers.
7. Precautions
Dosage control: Excessive (>5%) can easily lead to rough or cracked glaze surface, and the ratio needs to be optimized through experiments.
Raw material selection: Calcined magnesium oxide or talc (3MgO·4SiO₂·H₂O) is preferred as the magnesium source to ensure uniform dispersion.
Firing system: In an oxidizing atmosphere, 1250-1350℃ firing effect is best, and the formula needs to be adjusted in a reducing atmosphere.