Oil absorption value is also called resin adsorption, which indicates the amount of resin absorbed by the filler. It is usually expressed as the amount of linseed oil or dibutyl phthalate required for 100g of filler (ml/100g). It is a physical indicator for testing the performance of inorganic materials. Oil absorption value has important guiding significance for the selection of fillers. Most fillers use oil absorption value as an indicator to roughly predict the demand for resin of fillers. It can characterize the adsorption performance of fillers under different particle sizes and specific surface areas; when the oil absorption value is smaller, the resin adsorption amount is smaller, which means that the filling ratio is higher. In the field of thermal conductive polymer materials, the higher the filling amount of thermal conductive fillers, the higher the thermal conductivity.
Oil absorption value determination method: Taking the oil absorption determination method of magnesium hydroxide as an example, the steps include: accurately weighing the mass of the dropper bottle containing refined linseed oil (accurate to 0.001g) and recording; weighing about 5g of the dried talcum powder sample (accurate to 0.001g) and placing it on a flat plate; adding the refined linseed oil in the dropper bottle to the sample on the flat plate by dripping. The amount of oil added each time should not exceed 10 drops. After adding the oil, use the ink knife to press and grind the oil so that the oil can penetrate into the sample. Continue to add until the oil and the sample can form a mass. From this point on, after adding a drop of oil, it is necessary to fully press and grind with the ink knife to form a uniform consistency, just wet the powder mass, not cracked or broken, and can adhere to the plate. This is the end point; weigh the mass of the dropper and refined linseed oil after the end point (accurate to 0.001g) and record it.
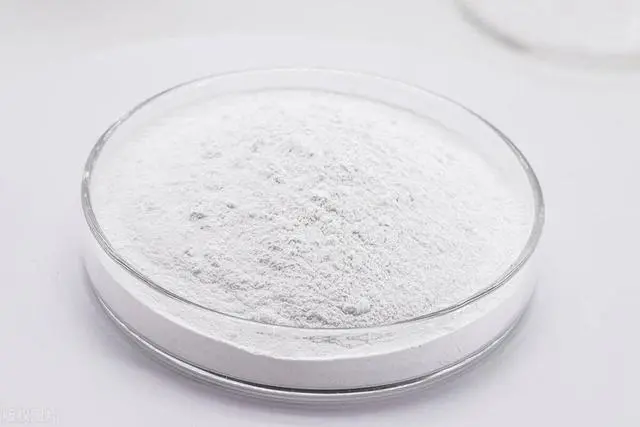
Magnesium hydroxide in the process of modification: The change curve of the oil absorption value of magnesium hydroxide during the pre-hydrolysis time As the hydrolysis time increases, the oil absorption value of the modified magnesium hydroxide powder shows a trend of first decreasing, then increasing, and then decreasing. This is because the silane coupling hydrolysis is incomplete at the beginning, and is accompanied by self-polymerization reaction, resulting in only part of the magnesium hydroxide powder reacting with the modifier, which alleviates the ineffective absorption of dioctyl ester by magnesium hydroxide powder and reduces the oil absorption value to a certain extent. When the pre-hydrolysis time reaches 60min, the oil absorption value reaches the lowest 40.25ml/100g. It can be considered that the coupling agent has been completely hydrolyzed and the degree of self-polymerization reaction is low at this time, so the modification effect of magnesium hydroxide powder is the best. Comprehensive analysis shows that when the hydrolysis time increases to 60min, the activation index of magnesium hydroxide powder also increases, indicating that the degree of hydrolysis of the silane coupling agent is complete, and most of the magnesium hydroxide powder is coated by the modifier, so the activity index is the largest. When the oil absorption value reaches the lowest, the activation index reaches the highest, indicating that the modification effect is optimal.