Magnesium hydroxide has the advantages of being green and environmentally friendly and having low cost in flame retardant applications. However, the flame retardant efficiency is low. In order to achieve the ideal flame retardant effect, the amount of Magnesium hydroxide added is often large, which affects the mechanical properties of the composite material. In addition, MgO produced by the thermal decomposition of Magnesium hydroxide has a certain smoke suppression effect, but the adhesion between MgO is poor, and the protective layer formed after combustion is thin and has poor firmness. Therefore, it is often necessary to add a flame retardant synergist to enhance the carbon layer and add it to the composite material together with Magnesium hydroxide, which can also reduce the amount of Magnesium hydroxide to a certain extent. In order to improve the compatibility between Magnesium hydroxide and the matrix, Magnesium hydroxide needs to be modified by surface grafting or coating to achieve better flame retardant efficiency.
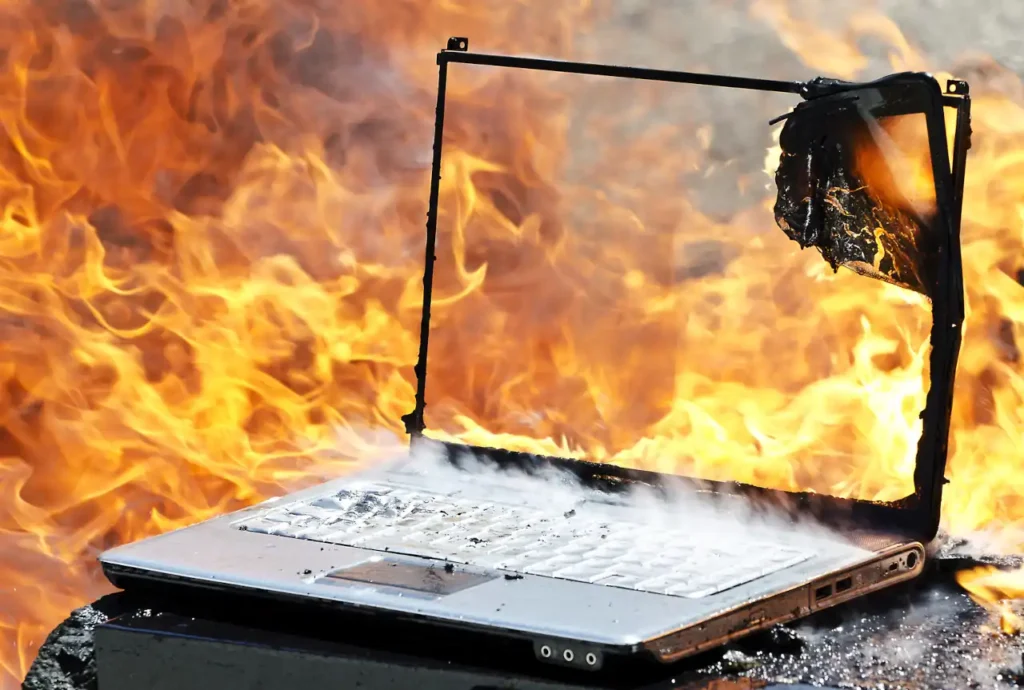
1. Improve mechanical properties
To improve the decrease in mechanical properties of the composite material caused by the large amount of Magnesium hydroxide added, particles with lubricating effect can be added to the matrix together with Magnesium hydroxide, or Magnesium hydroxide can be surface modified. Liguo Shen et al. used Magnesium hydroxide and hexaphenoxycyclotriphosphazene (HPCTP) as flame retardants and blended them with EVA to prepare EVA-Magnesium hydroxide-HPCTP composite materials. The compatibility of the composite materials was significantly improved due to the bridging effect of HPCTP, and it had good processing performance. Lei Ye et al. applied multi-walled carbon nanotubes (MWNT) and Magnesium hydroxide in EVA composite materials to obtain EVA/Magnesium hydroxide/MWNT composite materials. In EVA/Magnesium hydroxide/MWNT composite materials, 2wt% MWNT was used to replace Magnesium hydroxide, and the heat release rate and mass loss rate of MWNT could be significantly reduced by 50-60%, the burning time could be extended by nearly 2 times, and the LOI value could be increased by 5%. The addition of MWNTs can increase the melt viscosity of EVA composite materials during combustion, making the carbon layer harder. The mechanical strength of MWNT and the integrity of the charred layer in EVA/Magnesium hydroxide/MWNT nanocomposites improve the thermal oxidation stability. MWNTs promote the formation of a dense charred layer and play a role in heat insulation.
Hideko T. Oyama et al. used Magnesium hydroxide and poly (2,6-dimethyl-1,4-phenylene ether) (PPE) to flame retard isotactic polypropylene (iPP). Dodecanoic acid was grafted on the surface of Magnesium hydroxide, and SEBS served as a compatibilizer for iPP and PPE. The two not only had a synergistic effect on the mechanical properties of the composite material, but also had this effect in terms of thermal stability. In order to reduce the amount of Magnesium hydroxide and improve the mechanical and flame retardant properties of the blending system, J.Albite-Ortega et al. combined keratin fibers (KF) extracted from poultry feathers with deoxyribonucleic acid (DNA) in a low-density polyethylene-ethylene-vinyl acetate (LDPE/EVA) blending system for the first time. Mechanical property tests showed that after the addition of DNA, the elongation at break of the composite material was significantly increased, and the torque and viscosity were significantly reduced, indicating that the combination of these additives can improve the mechanical properties and facilitate the processing of composite materials. Most importantly, the combination of these additives reduced the total content of Magnesium hydroxide filler from 55wt% to 20wt%, meeting the flame retardant requirements and improving the mechanical properties. Yaru Yang et al. synthesized a new flame retardant – carbon microspheres coated with Magnesium hydroxide (Mg (OH) 2 @ CMSs). When only 1wt% Mg (0H) 2 @ CMSs was added to the prepared composite material (Mg (OH) 2 @ CMSs / PET), the LOI value was 27.5%, reaching the UL-94V-0 grade. This modification method greatly reduced the amount of Magnesium hydroxide added and weakened the damage of Magnesium hydroxide to the mechanical properties of the composite material.
Weihua Meng et al. synthesized a bio-based Magnesium hydroxide @ phytic acid tin @ tannic acid zinc (Magnesium hydroxide @ PASn @ TAZn) composite material using a layer-by-layer self-assembly method. Adding 10 parts of Magnesium hydroxide @ PASn @ TAZn can effectively improve the flame retardant and smoke suppression properties of polyvinyl chloride (PVC). The LOI value increased to 30.3%, and the second peak heat release rate, second peak smoke release rate and total smoke release of PVC/Magnesium hydroxide@PASn@TAZn composite materials decreased by 40.8%, 72.2% and 35.2%, respectively. The increase in the interfacial contact area of PASn and the enhancement of the interfacial interaction of TAZn significantly improved the tensile strength, elongation at break and impact strength of PVC. Sheng Zhang et al. introduced bis[3-(triethoxysilyl)propyltetrasulfide] on the surface of Magnesium hydroxide, and added Magnesium hydroxide (SMagnesium hydroxide) with a mass fraction of 40wt% to EVA. The LOI increased from 17.9% of pure EVA to 23.3%, and the peak heat release rate decreased to 489kW/M2. The mechanical properties were tested by a tensile machine. When the Magnesium hydroxide content was 40wt%, the elongation at break decreased by nearly 7 times, from 825% of EVA to 124%, while when the SMagnesium hydroxide content was 40wt%, the elongation at break decreased to 74.5%. The morphological observation under scanning electron microscope showed that the dispersibility of SMagnesium hydroxide in EVA was significantly improved. Yunhua Lu et al. grafted titanate polyether coupling agent (eTi4000) on the surface of magnesium hydroxide particles (Magnesium hydroxideP) and magnesium hydroxide whiskers (Magnesium hydroxideW) and applied them in polyvinyl chloride (PVC). The flexural modulus and impact strength of PVC composite materials increased by 217% and 48.2%, respectively, and the total heat release and total smoke release decreased by 66.9% and 88.1%, respectively. Weina Zhang et al. grafted silane coupling agent vinyl triethoxysilane (VTES) on the surface of Magnesium hydroxide to improve the compatibility of Magnesium hydroxide with matrix silicone rubber. However, general surface modifiers such as long-chain silanes will reduce flame retardancy, and it is not possible to have both. Therefore, some work is devoted to the development of surface modifiers with flame retardant elements. Jichun Liu et al. synthesized Magnesium hydroxide and RP co-microcapsules ([Magnesium hydroxide&RP]) by one-step in-situ surface polymerization using 4,40-diphenylmethane diisocyanate and melamine as raw materials, and introduced them into EVA. The results showed that the core-shell co-microcapsules had high thermal stability and thermal oxidation stability, and better dispersibility in EVA.
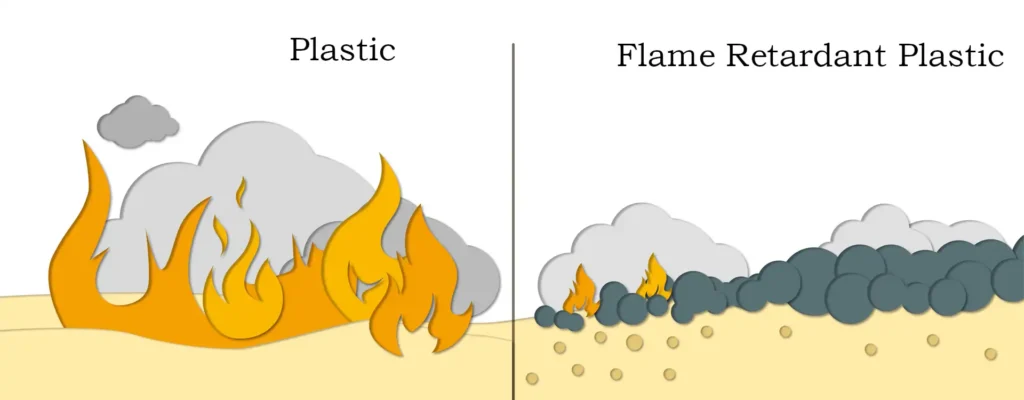
2. Improving smoke suppression
Huan Zou et al. introduced nano-SiO2 and MoO3 into ethylene-vinyl acetate/nitrile rubber (EVA/NBR) blends containing Magnesium hydroxide and RP, further improving the mechanical properties, oil resistance, smoke suppression and flame retardancy of the rubber. The results showed that the addition of nano-SiO2 significantly improved the tensile strength and oil resistance of the material on the one hand. On the other hand, the smoke suppression experiment of EVA/NBR blend samples showed that the addition of nano-SiO2 and MoO3 could significantly reduce the smoke emission.
Natural brucite is a unique mineral with abundant reserves, containing more than 94% Magnesium hydroxide, and can be directly used as a flame retardant (HFFR). Like Magnesium hydroxide, brucite can absorb heat and decompose to release water to cool combustion and dilute the concentration of combustible gases. The generated active MgO layer has heat insulation and smoke suppression effects, inhibiting the entry of combustible volatile organic compounds into the gas phase. However, the disadvantages of brucite are irregular shape, wide particle distribution, and large loading, which are not conducive to the mechanical properties of polymer composites. Yiliang Wang et al. used nickel alginate (NiA), copper alginate (CuA), zinc alginate (ZnA) and 3-aminopropyltriethoxysilane (APTES) to deposit on the surface of brucite for flame retardant EVA, and found that the catalytic graphitization of NiA is efficient and sustainable. In the research process, the catalytic graphitization and carbonization mechanism of alginate on EVA was proposed for the first time, opening up a new field for the application of bio-based materials in polymers. At the same time, the authors simplified the experimental operation and used the electrostatic interaction, dehydration condensation, hydrogen bond and coordination bond between brucite, silane coupling agent APTES, nickel chloride and sodium alginate for self-assembly. The catalytic carbonization of nickel compounds formed more protective carbon layers during the combustion of the composite material, thereby further improving the flame retardant efficiency of the material, reducing the smoke release during the combustion of EVA composite materials and improving the mechanical properties of EVA composite materials. Hongchang Pang et al. used nanoengineering methods to synthesize a flame retardant with brucite as the core and thin SiO2 as the shell. The synthesized CFR was used as a filler material for EVA composites, and the tensile strength (TS) was increased by at least 25%. On this basis, the authors proposed the mechanism of enhanced mechanical properties and flame retardant properties of CFR particles, the main reason of which was the structural synergy between the brucite core and the SiO2 shell.
Xuesong Wang et al. used brucite as the core and dodecylamine polyphosphate as the shell, and synthesized a new type of organic-inorganic hybrid flame retardant using nanoengineering methods. The flame retardant properties and synergistic flame retardant mechanism of core-shell flame retardant (CFR) in EVA blends with brucite and dodecylamine polyphosphate, EVA/physical mixture (PM) with CFR ratio and EVA/brucite blends were compared. At the same filling content (40wt%), the peak heat release rate and smoke generation rate of EVA/CFR blends were significantly reduced, which were 49% and 48% of those of EVA/PM blends, respectively. At the same time, the LOI was increased to 32% (14.3% higher than that of EVA/PM blends), and the UL-94 test could reach V-0 grade. These excellent properties were obtained by nano-engineering the hybrid system of brucite@polyphosphate@amine core/shell structure, which is conducive to the formation of complete and dense palisade structured carbon residues during the combustion of polymer composites. Xinyao Lv et al. prepared a new multifunctional organic-inorganic hybrid flame agent (AM-MEL) using nitrile-trimethyltriphosphonic acid and melamine-modified Magnesium hydroxide nanosheets as raw materials. Then, intrinsic flame retardant epoxy resin (EP) was prepared by covalently adding AM-MEL nanoparticles. At the same time, APP was added to EP to form an intumescent flame retardant system with AM-MEL. Compared with pure EP, EP/AM-MEL/APP containing 5wt% AM-MEL and 15wt% APP reached a limiting oxygen index of 32.0%, no molten droplets fell during the combustion of the specimen, PHRR decreased by 88.0%, THR decreased by 70.0%, total smoke production decreased by 81.5%, and CO yield peak decreased by 87.3%.