Abstract
The present invention provides a preparation method of surface-modified nano-magnesium oxide material dedicated to SMC thickening, which belongs to the field of functional nanomaterials, in which an appropriate amount of magnesium chloride or magnesium sulfate and polyvinyl alcohol are dissolved in deionized water to form solution A, which is placed in a constant-temperature water bath at 35 ℃; sodium carbonate in the same molar amount is dissolved in quantitatively the same amount of deionized water to obtain the sodium carbonate solution B of the same concentration; it is placed in a constant-temperature water bath at 35 ℃ In a constant temperature water bath at 35 ℃; first quickly half of the sodium carbonate solution to start mechanical stirring; rinse the precipitation with deionized water for 3 to 5 times, and calcine at 450 to 550 ℃ for 120 to 180 minutes; continue to ultrasonically dispersed powder in deionized water, add appropriate amount of stearic acid nanosolutions; after standing, clean it with deionized water, and put it into the microwave drying to obtain the surface modified nano-magnesium oxide material. The modified magnesium oxide material obtained by the present invention has uniform particle size, and the surface-modified nano-magnesium oxide material with controllable thickening rate is obtained, which has important application prospects.
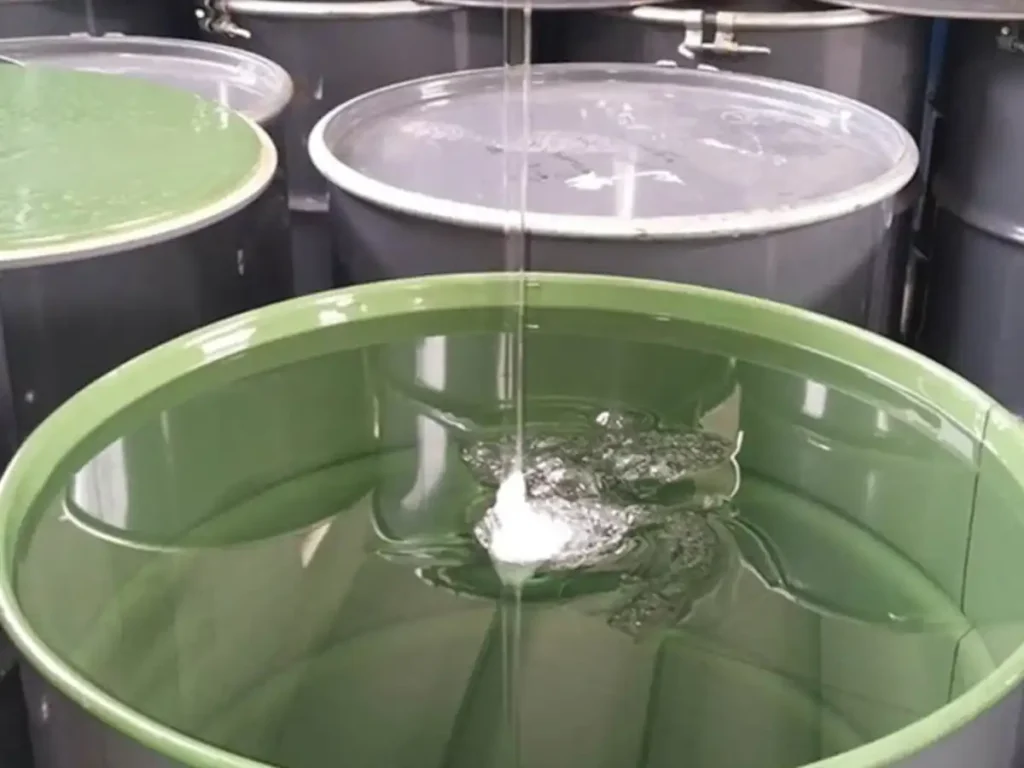
Description
Preparation of a Surface-Modified Nano-Magnesium Oxide Material Specialized in SMC Thickening
Technical Field
The present invention belongs to the field of functional nanomaterials, and specifically relates to the optimization of a surface treatment solution of magnesium oxide dedicated to SMC.
Background Technology
SMC material is composed of SMC-specific yarn, unsaturated resin, low shrinkage additives, thickeners and other fillers. It has a wide range of applications in industries such as transportation vehicles, construction, and electronics/electrical because of its superior electrical properties, corrosion resistance, and high flexibility.
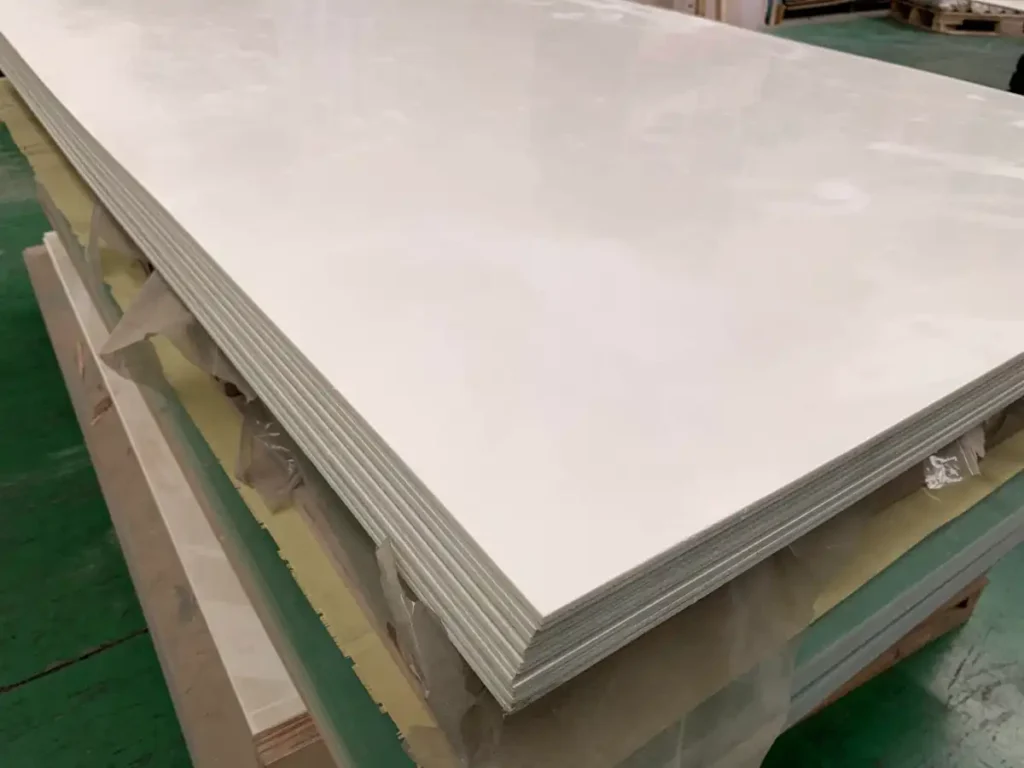
In the SMC preparation process, thickeners have a huge impact on the properties of SMC materials. For chemical thickening of unsaturated polyesters, the most used are alkali metal oxides or hydroxides, such as magnesium oxide, calcium oxide, or barium oxide and the corresponding hydroxides. However, relevant industry experience and research results show that: calcium-related materials are too sensitive to moisture, barium-related thickening materials are too costly, which greatly limits their application as high-quality thickeners in SMC, which makes magnesium-based materials, especially magnesium oxide materials become the most cost-effective SMC thickening materials.
Magnesium oxide material itself is odorless, tasteless and non-toxic, and has strong buffering and efficient chemical adsorption, in metallurgy, environment, construction and other aspects of the application of the research has received widespread attention, and according to the use of the environment purposefully on the surface of the material related to the modification of the research has made great progress, including hydrophilicity modulation, optical, electrical and thermal properties to improve. However, there are relatively few studies on the modification of SMC thickeners, Hu et al. used organic acid as a capping agent to give a method for the preparation of magnesium oxide for unsaturated polyester resin glass fiber reinforced plastic, based on the nano-magnesium oxide material after preparation by spraying, stirring. (A kind of unsaturated polyester resin production of FRP special magnesium oxide and its preparation method CN 103923491A). However, so far, the surface modification of magnesium oxide directly realized in the production process to make it suitable for SMC is still no obvious breakthrough.
Contents of the invention
The purpose of the present invention is to provide a preparation method of surface-modified magnesium oxide nanomaterials dedicated to SMC thickening, which organically combines the preparation process with the surface modification process to obtain magnesium oxide materials that can effectively regulate the thickening speed of SMC. The magnesium oxide material prepared by this solution has controllable thickening performance, good uniformity, simple and controllable cut preparation parameters, easy process amplification, and has obvious application value.
In order to achieve the above-desired purpose, the present invention adopts the following technical program:
The present invention provides a preparation method of a surface-modified nano-magnesium oxide material dedicated to SMC thickening, the specific process steps are:
1) dissolve an appropriate amount of magnesium chloride or magnesium sulfate and polyvinyl alcohol in deionized water to form solution A, and place it in a constant temperature water bath at 35°C;
2) dissolving sodium carbonate of the same molar amount in step 1) in a quantitative amount of deionized water to obtain sodium carbonate solution B of the same concentration; placing it in a constant temperature water bath at 35°C;
3) Pour half of the amount of sodium carbonate solution B in step 2) directly into solution A and start mechanical stirring; add the remaining solution B slowly after a certain time and continue stirring until the reaction is complete to form a precipitate;
4) The precipitate in step 3) is rinsed 3 to 5 times using deionized water, then moistened with an appropriate amount of anhydrous ethanol and filtered, and placed in a microwave for drying;
5) Calcining the dried precipitate in step 4) at 450 to 550°C for 120 to 180 minutes;
6) dispersing the powder obtained in step 5) in deionized water using ultrasonic dispersion, adding stearic acid nanosolution and adjusting the pH to an alkaline range of 9.5 to 10.5 after to a constant temperature water bath environment;
7) The suspension in step 6) is filtered, cleaned with deionized water, and placed in a microwave to dry to obtain the surface-modified nano-magnesium oxide material.
Compared with the existing technology, the beneficial effect of the present invention is: the present invention combines morphological control and surface modification, by controlling the relevant parameters in the reaction process and the method of adding materials, it is possible to obtain surface-modified nano-magnesium oxide materials with controllable thickening rate, with high uniformity and controllability, and it is easy to realize the industrial preparation, and it has an important prospect of application.
Specific embodiments
The following is a detailed description of the embodiments of the present invention, which are implemented on the premise of the technical program of the present invention, and detailed implementation and specific operation process are given, but the protection scope of the present invention is not limited to the following embodiments.
Example 1:
Weigh 19 g of magnesium chloride (0.2 mol) powder and 40 mL of polyvinyl alcohol solution with a mass fraction of 5% into a beaker, add deionized water to 200 mL placed in a constant temperature water bath at 35° C. to become Solution A; weigh 21.2 g of sodium carbonate (0.2 mol) dissolved in 200 mL of deionized water to form Solution B, and place it in the constant temperature water bath; pour 100 mL of Solution B rapidly into the solution A, and begin to carry out the process. Solution A, and start mechanical stirring; 5 minutes later, add the remaining 100mL of Solution B at a speed of 10mL/min, and continue stirring for 20 minutes and then stop; after 30 minutes of standing, the precipitate was rinsed with deionized water for 3 times, added 20mL of anhydrous ethanol for moistening, and put in the microwave drying chamber to dry for 15 minutes; put the dried precipitate in a calcination at 450 ℃ and remove it 180 minutes later; weighed the dried precipitate and put it in a calcine at 450 ℃ and then removed it. 180 minutes after removal; weighing the dried powder 5g into 100mL deionized water, ultrasonic dispersion for 10 minutes; add a mass fraction of 5% hard fatty acid solution 18mL; add the appropriate amount of sodium hydroxide solution will be pH modulation of 9.5 into the 35 ℃ constant temperature water bath reaction for 20 minutes, the resulting suspension filtration, deionized water rinsed 2 to 3 times, placed in a microwave drying chamber The surface modified nano-magnesium oxide material can be obtained by drying for 15 minutes.
Example 2:
Weigh 24g of magnesium sulfate (0.2 mol) powder and mass fraction of 5% of polyvinyl alcohol solution 40mL into a beaker, add deionized water to 200mL placed in a constant temperature water bath at 35 ℃, to become solution A; weigh 21.2g of sodium carbonate (0.2 mol) dissolved in 200mL of deionized water to form a solution B, and placed in a constant temperature water bath; will be 100mL of solution B quickly poured into Solution A, and start mechanical stirring; 5 minutes later at a speed of 10mL/min the remaining 100mL solution B uniformly added, continuous stirring for 20 minutes and then stop; after 30 minutes of resting will be precipitate with deionized water rinse 3 times, add 15mL anhydrous ethanol for infiltration, placed in the microwave drying chamber to dry for 15 minutes; will be placed in the dried precipitates under the condition of 500 ℃ calcination 150 minutes later removed; weighing the dried powder 5g into 100mL deionized water, ultrasonic dispersion 10 minutes later; add a mass fraction of 5% hard fatty acid nano-solution 15mL; add the appropriate amount of sodium hydroxide solution will be adjusted to the pH value of 10 into the 35 ℃ constant temperature water bath reaction for 20 minutes, the resulting suspension filtration, deionized water rinsed 2 ~ 3 times, into the microwave drying chamber drying Surface-modified nano-magnesium oxide material can be obtained in 15 minutes.
Example 3:
Weigh 23.6 g of magnesium chloride hexahydrate (0.2 mol) powder and a mass fraction of 3% of polyvinyl alcohol solution 40 mL into a beaker, add deionized water to 200 mL placed in a constant temperature water bath at 35 ℃, to become solution A; weighing 21.2 g of sodium carbonate (0.1 mo2) dissolved in 200 mL of deionized water to form a solution B, and placed in a constant temperature water bath; will be 100 mL of solution B quickly poured into the solution A, and began to mechanical stirring; after 5 minutes at a speed of 10mL/min to the remaining 100mL solution B uniformly added, continuous stirring for 20 minutes and then stop; after 20 minutes of resting the precipitate with deionized water rinsed 3 times, add 15mL anhydrous ethanol for infiltration, placed in the microwave drying chamber to dry for 15 minutes; dried precipitates placed in a microwave drying chamber at 550 ℃ Calcined at 550 ℃ for 120 minutes and then removed; weighed 5g of dried powder into 100mL of deionized water, ultrasonic dispersion for 10 minutes; add a mass fraction of 5% of hard fatty acid Na solution 12mL; add the appropriate amount of sodium hydroxide solution to adjust the pH value to 10.5 and then put into the 35 ℃ thermostatic water bath reaction for 20 minutes, the suspension will be filtered, rinsed with deionized water for 2-3 times, and then put into the microwave drying chamber for 15 minutes. Microwave drying chamber for 15 minutes to obtain the surface-modified nano-magnesium oxide material.
Example 4:
Weigh 49.2g magnesium sulfate heptahydrate (MgSO4.7H2O) (0.2mol) powder and 40mL of polyvinyl alcohol solution with a mass fraction of 4% into a beaker, add deionized water to 200mL and place in a constant temperature water bath at 35°C. Become solution A; weigh 21.2g (0.2mol) of carbonic acid and dissolve it in 200mL of deionized water to form solution B, and place it in a constant temperature water bath; quickly pour 100mL of solution B into solution A, and start mechanical stirring; after 5 minutes Add the remaining 100 mL of Solution B at a rate of 10 mL/min at a constant speed, and continue stirring for 20 minutes before stopping; after letting it stand for 30 minutes, rinse the precipitate three times with deionized water, add 25 mL of absolute ethanol for infiltration, and dry it in the microwave. Dry in the cavity for 15 minutes; calcine the dried precipitate at 550°C for 120 minutes and then take it out; weigh 5g of the dried powder and put it into 100mL of deionized water, and disperse it with ultrasonic for 10 minutes; add a mass fraction of 5% 15 mL of hard fatty acid sodium solution; add an appropriate amount of sodium hydroxide solution to adjust the pH value to 10.5 and then place it in a 35°C constant temperature water bath to react for 20 minutes. Filter the resulting suspension, rinse it with deionized water 2 to 3 times, and dry it in a microwave After drying in the cavity for 15 minutes, the surface-modified nano-magnesium oxide material can be obtained.
The above description shows and describes the preferred embodiments of the present invention. As mentioned above, it should be understood that the present invention is not limited to the form disclosed herein and should not be regarded as excluding other embodiments, but can be used in various other combinations, modifications and environments, and can be changed through the above teachings or technology or knowledge in related fields within the scope of the inventive concept described herein, and the modifications and changes made by those in the art do not depart from the spirit and scope of the invention, then All should be within the protection scope of the appended claims of the present invention.