Background and Overview
Magnesium citrate crystals contain different crystal waters. Magnesium salts containing 9 crystal waters are colorless columnar crystals, which become anhydrous salts at 175°C, insoluble in boiling water, and soluble in ammonia and dilute acid. Magnesium salts containing 14 crystal waters are colorless leaf-shaped (scaly) crystals, which become trihydrate salts at 110°C and become anhydrous salts when heated. The solubility in 25°C water is 18g/L. MgHC6H5O7·5H2O is a colorless crystal that dissolves in 5 times the amount of water, is soluble in acid, and is insoluble in ethanol. Magnesium citrate containing 9 crystal waters has a magnesium content of up to 11%, and the magnesium contained is easily absorbed by the human body. Therefore, it is an important source of magnesium nutritional supplements. Magnesium citrate can be used as a medicine, and its most common medical use is as a saline laxative. When magnesium citrate is used for medical purposes, the quality requirements of magnesium citrate are very high.
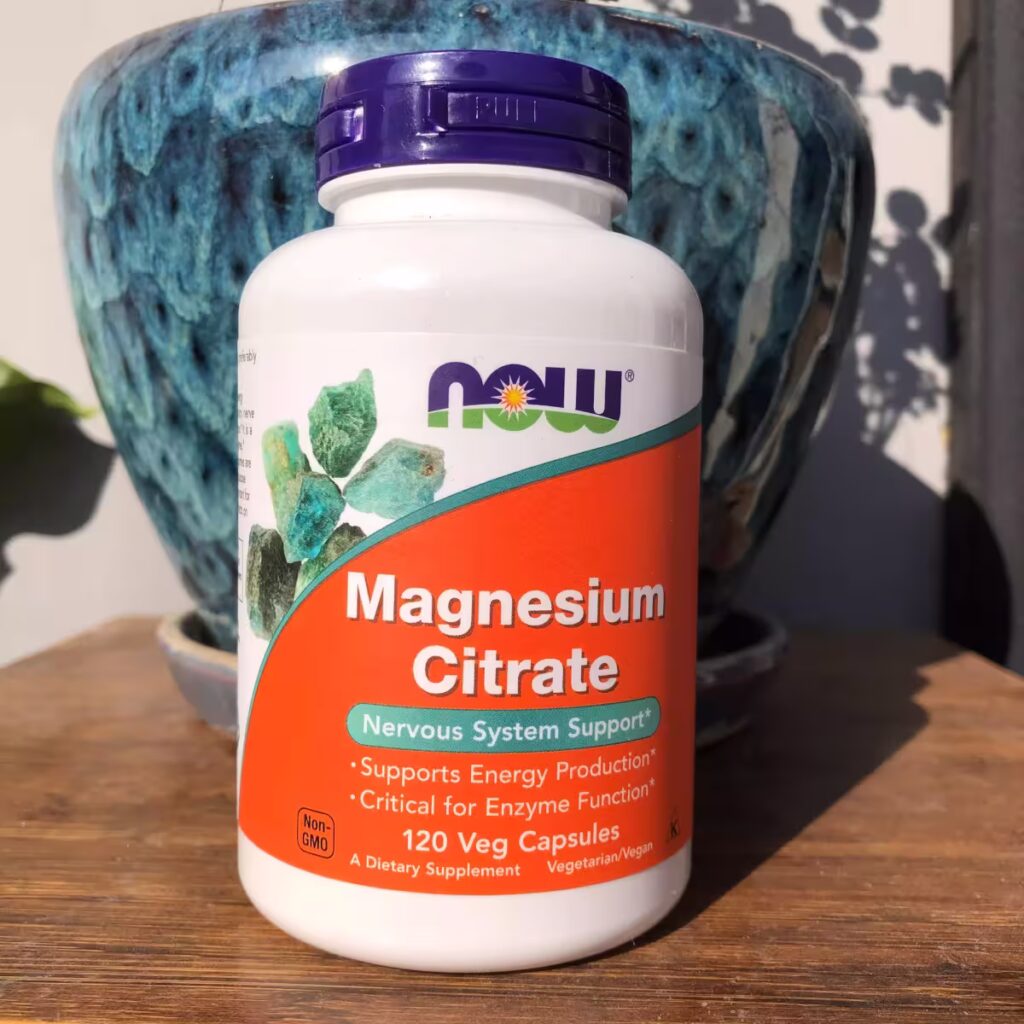
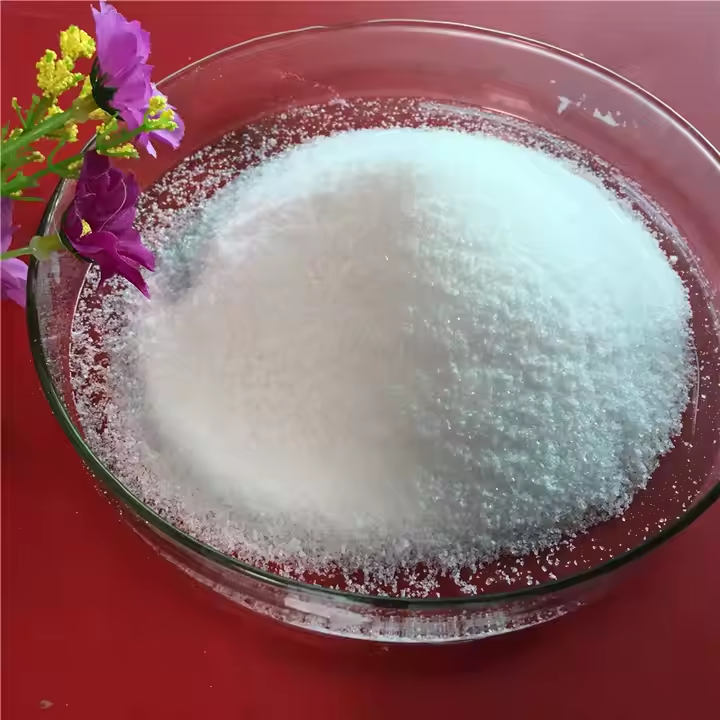
At present, magnesium citrate is produced in industry by reacting magnesium carbonate, magnesium oxide or magnesium hydroxide as raw materials with edible citric acid. The specific production method is: add citric acid to water to dissolve and filter, and start to add magnesium carbonate, magnesium oxide or magnesium hydroxide slurry when the temperature reaches 70°C after heating. During the reaction, the flow acceleration of the slurry is not controlled, and the pH value of the reaction solution is controlled between 5-8; after crystallization, washing and drying, the sieving is carried out according to the particle size requirements to obtain the finished magnesium citrate crystals. However, this method only controls the pH value of the reaction solution between 5-8, resulting in the reactants being doped in the obtained magnesium citrate crystals, and the content of magnesium citrate crystals is low. At present, the process of producing magnesium citrate is still immature, resulting in high energy consumption, large waste of resources and serious pollution. In addition, the prepared magnesium citrate contains a large amount of crystal water, which makes the product slightly soluble in water, and its use in the pharmaceutical and health care products industry is not conducive to human absorption. Therefore, there is an urgent need for a production method that can increase the content of magnesium citrate crystals.
Application
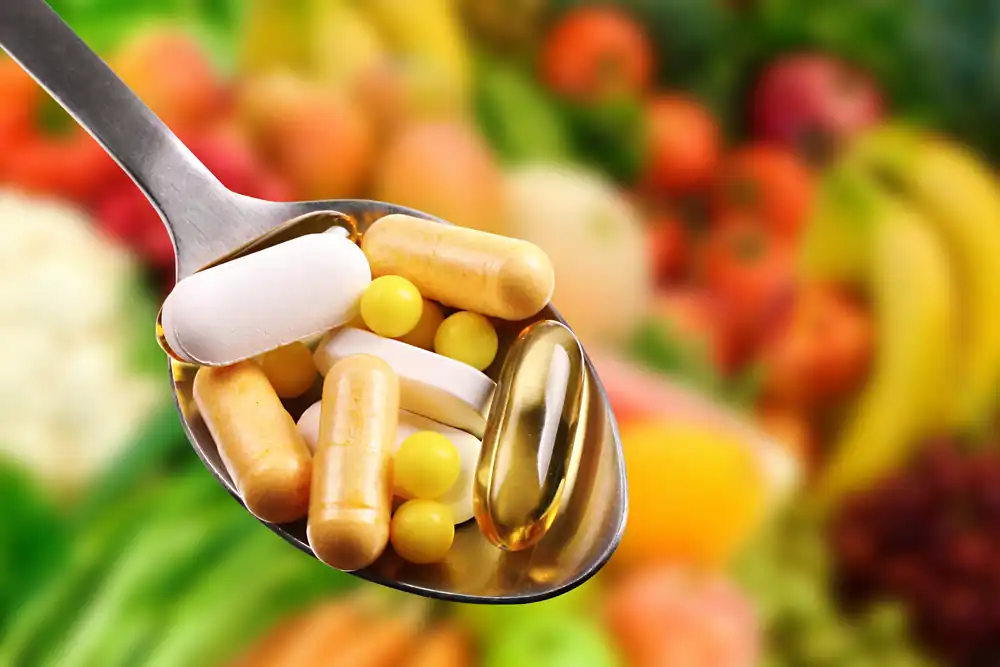
Magnesium citrate is composed of magnesium carbonate and citric acid. This is a chemical preparation with medicinal value, which contains up to 11% magnesium. For this reason, it is often used as a health supplement. Since the magnesium component is easily absorbed by the human body, it is an important source of magnesium nutrition. The most common medical use of magnesium citrate is as a saline laxative. Before any surgery, patients are given magnesium citrate to facilitate the emptying of the intestines. This is because it has a tendency to absorb tissue water, and after being injected into the intestines, it can absorb a large amount of water and excrete it from the body. In fact, it can also treat constipation and colon cancer, or diseases related to rectal cancer. In addition, magnesium citrate has the effect of preventing kidney stones. This paper has developed a feed additive for preventing urinary stones, which is composed of the following components by weight percentage: allopurinol 15-30%, lactase 35-50%, magnesium citrate 20-40%, ethacrynic acid 0.2-1%, and potassium canrenoate 0.5-3%. Added to daily feed, it has the effect of quickly dissolving urinary stones, preventing the formation of urinary stones, and promoting the discharge of stones.
Preparation
Method 1: A method for producing magnesium citrate, which uses magnesium carbonate or magnesium oxide or magnesium hydroxide as a raw material to react with edible citric acid to obtain magnesium citrate, and then cools, crystallizes, washes with hot deionized water, and dries to obtain magnesium citrate.
The technical characteristics of the process for producing magnesium citrate of the present invention are: after magnesium carbonate or magnesium oxide or magnesium hydroxide is reacted with edible citric acid as a raw material, a dilute acetic acid solution is added to control the content of lead, and the specific implementation is as follows: a. Add citric acid into water to dissolve and filter, heat and warm When the temperature reaches 70℃, magnesium carbonate, magnesium oxide or magnesium hydroxide is gradually added, with a weight ratio of 0.55/0.29/0.41:1, and the pH value of the reaction solution is between 5-8; b. Add dilute acetic acid solution to control the lead content; c. After cooling, crystallization, washing and drying, sieve according to the particle size requirements to obtain the finished magnesium citrate crystal or powder. If granules are required, 3% maltodextrin can be soaked in warm water to form a paste, mixed with the powdered material, and then dried again through extrusion granulation to form granules.
Method 2: The production method of anhydrous magnesium citrate, which has a scientific and reasonable production process, is easy to control, reduces production costs, and the prepared anhydrous magnesium citrate is easily soluble in water, and can be made into tablets, granules, capsules, oral liquids and injections of easily soluble magnesium citrate, and can also be directly added to food and beverages for human absorption.
Its production process is as follows:
(1) Inject a certain volume of purified water into the reactor and start stirring;
(2) Add a calculated amount of clean citric acid, open the steam valve, and raise the temperature to about 70°C to fully dissolve the citric acid;
(3) Slowly add food-grade magnesium oxide calculated according to the chemical formula into the reactor;
(4) The reaction releases a large amount of heat, and the temperature is controlled not to exceed 90°C;
(5) After the feeding is completed, react for 3-4 hours to produce a large amount of white precipitate, and stir repeatedly;
(6) When the precipitate content reaches more than 50%, solid-liquid separation begins;
(7) After separation, dry at a low temperature of 70-80°C for about 5 hours to obtain magnesium citrate containing crystal water;
(8) Increase the drying temperature to 150°C and continue drying for about 60 hours to obtain anhydrous magnesium citrate;
(9) Sieve after cooling;
(10) Package to obtain the finished product.
Method 3: A method for producing low-lead granular magnesium citrate, which uses magnesium sulfate and sodium carbonate to prepare magnesium carbonate, and neutralizes it with food-grade citric acid to prepare magnesium citrate. The reaction principle is:
MgSO4+Na2CO3→MgCO3+Na2SO4
MgCO3+C6H8O7→Mg3(C6H8O7)2+CO2+H2O
Then, add dilute acetic acid solution to control the lead content. The specific steps are:
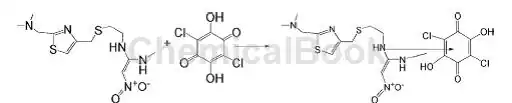
use magnesium sulfate and sodium carbonate as raw materials to first prepare magnesium carbonate, and then react magnesium carbonate with citric acid to prepare magnesium citrate.
The specific implementation is:
a. First dissolve magnesium sulfate (containing crystal water) in water, filter to remove impurities, and prepare magnesium sulfate solution (magnesium sulfate and water weight ratio is 1:0.8);
b. Perform double decomposition reaction on the prepared magnesium sulfate solution and sodium carbonate, and the weight ratio is (magnesium sulfate: sodium carbonate = 1:0.525) and then dehydrate and wash to obtain magnesium carbonate;
c. The magnesium carbonate, edible citric acid and water are prepared in the following weight ratio (magnesium carbonate: edible citric acid: water=1:1.67:2). First, citric acid is added into water, dissolved and filtered. When the heating temperature reaches 70°C, magnesium carbonate is gradually added, and the pH value of the reaction solution is between 5 and 8.
d. A dilute acetic acid solution is added to control the content of lead. f. After cooling, crystallization, washing with hot deionized water and drying, sieving is performed according to the particle size requirement. During sieving, 30-40% of tiny crystals or powders are obtained. In order to reduce powder pollution during use and meet the requirements of market particles, 3% maltodextrin is added into warm water to be soaked into a paste, mixed with the powdery material, and granulated and dried again to form particles.