Abstract
A method for smelting fused magnesite using raw magnesite ore powder relates to a smelting method of fused magnesite, which solves the problems of high power consumption, magnesite ore and tailings used in the past to smelt fused magnesite. The problem of waste; the smelting method is as follows: (1) Use a crusher to process magnesite raw ore powder with a particle size of 0<x≤5mm into 0<x≤3mm, and take 1 ton of processed magnesite raw ore powder; (2 ) Add 35kg of binding agent, mix with a mixer, pressurize and form; (3) Process the magnesite particles obtained after pressure molding into magnesite blocks with a particle size of 5<x≤50mm, and then put them into the electric furnace Smelted in. The present invention utilizes magnesite ore and tailings powder to prepare fused magnesia. Since the magnesite raw ore is processed into small particles and powder, the structure is changed, and it is easier to decompose and melt when smelted in an electric furnace. Using this smelting method to produce fused magnesite reduces power consumption by 4% to 5% per ton, reduces electrode consumption by 5% to 10%, and increases output by 7% to 8% per shift, which has the advantages of energy conservation and environmental protection.
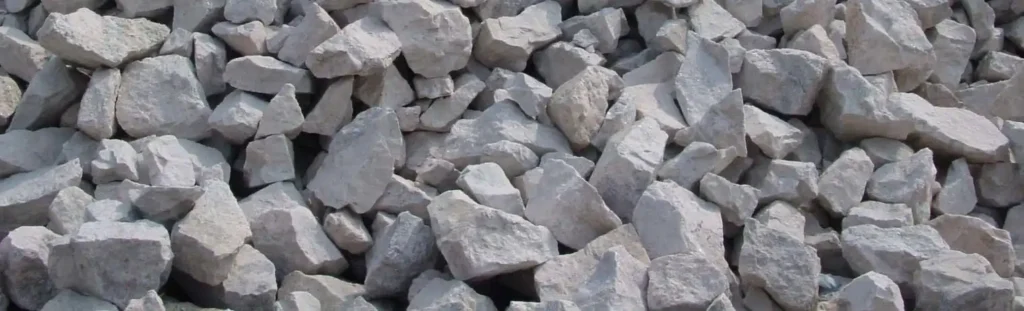
Description
Method for smelting fused magnesite using magnesite raw ore powder
Technical areas:
The invention relates to a method for preparing fused magnesia.
Background technique:
The current production of fused magnesia involves processing the raw magnesite ore into particles with a particle size of 5 to 40 mm, and then using an electric furnace for smelting and production. Due to the different origins of magnesite, the degree of decomposition is also different. Generally, an electric furnace with a capacity of 1,200 kVA is used. When smelting and producing fused magnesia, each ton of fused magnesia produced consumes 3700 to 3800 degrees of electricity and 65kg of electrodes. 7 to 8 tons of fused magnesia can be produced in 10 hours.
Contents of the invention:
In order to solve the above existing problems, the present invention provides a method for smelting fused magnesite using magnesite raw ore powder. Using this method to prepare fused magnesia reduces energy consumption, effectively utilizes previous waste, and is energy-saving and environmentally friendly. The method for smelting fused magnesia with magnesite raw ore powder, the steps are as follows:
(1) Use a crusher to process the magnesite raw ore powder with a particle size of 0<x≤5mm into a particle size of 0<x≤3mm, and take 1 ton of the processed magnesite raw ore powder;
(2) Add 35 kilograms of binding agent, mix with a mixer, then pressurize and shape. The binding agent is pulp with a viscosity of 145 mPa·s;
(3) Process the magnesite particles obtained after pressure molding into magnesite blocks with a particle size of 5<x≤50mm, and then put them into an electric furnace to smelt into fused magnesite.
Beneficial effects of the present invention: The present invention uses the mined and processed magnesite ore and tailings powder for reprocessing and smelting into fused magnesite, effectively utilizing the waste. Since the magnesite raw ore is processed into small particles and powder shape, with some changes in structure. When smelted in an electric furnace, it is easier to decompose and melt. Using this smelting method to produce fused magnesite, the power consumption per ton is 3500 to 3600 degrees. Using 60kg of electrodes, it can be produced in 10 hours. The production capacity is 7.5 to 8.5 tons of fused magnesia. The invention has the advantages of energy saving and environmental protection.
Detailed ways:
The method of smelting fused magnesia with magnesite raw ore powder, the steps are as follows:
(1) Use a crusher to process magnesite raw ore powder with a particle size of 0<x≤5mm into 0<x≤3mm, and take 1000kg of magnesite raw ore powder with a particle size of 0<x≤3mm;
(2) Add 35kg of binder. The binder is paper pulp, which is mixed with a mixer and then pressurized and shaped. The pulp is a pulp commonly used in the brick-making process in the refractory industry. The viscosity of the pulp is 145mPa·s at 20°C. Combination effect.
(3) Process the magnesite particles obtained after pressure molding into magnesite blocks with a particle size of 5<x≤50mm, and then put them into an electric furnace to smelt into fused magnesite.