Ore method of preparing magnesium oxide process
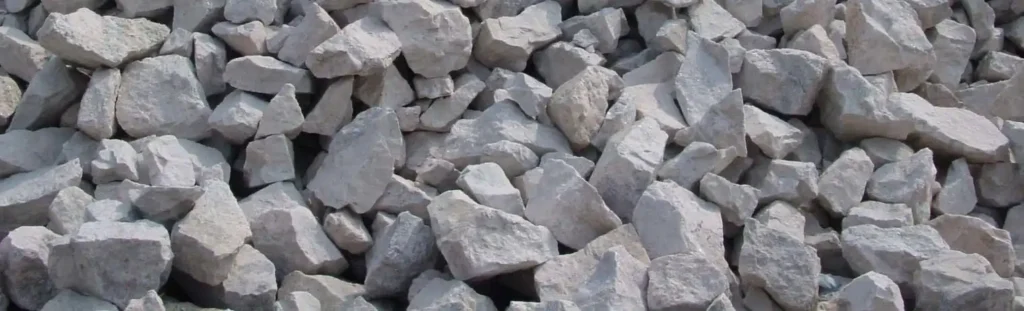
1 Direct calcination method
This method is to calcine magnesium salt or magnesite directly in high temperature to get magnesium oxide. Calcined under the condition of 450℃ for 3h basic magnesium carbonate pentahydrate and magnesium hydroxide, the magnesium oxide products with the average size of 9nm and 4.8nm were obtained respectively.
The reaction mechanism is as follows:
The direct calcination method is a simple process, does not require high equipment, and is easy to industrialize. However, the method is not easy to regulate the morphology of magnesium oxide.
2 Ammonium leaching method
This method is to react the product obtained after calcination of dolomite with ammonium salt solution, and after filtration, the filtrate will be reacted with NH3-H2O to obtain Mg(OH)2, and calcined Mg(OH)2 to obtain magnesium oxide.Huang et al. used the calcined dolomite as the magnesium source and ammonium sulphate as the leaching agent in the molar ratio of (NH4)2SO4 to MgO is 1.8∶1, the volume of distilled ammonia is 350mL, and the amount of calcined dolomite is 20 g. The method is simple and easy to control the morphology of magnesium oxide in industry. The magnesium leaching rate reached 96.81% under the condition of 20 g dosage. And the obtained Mg(OH)2 was calcined at 500~1000°C to produce magnesium oxide with particle size of 12.4~42.2 nm.
The reaction mechanism was:
Ammonium leaching method in the experimental process will produce ammonia, water recycling can be used to do the subsequent precipitation of magnesium precipitation step precipitant, can form a closed-loop process, recycling, the obtained magnesium oxide purity is also higher. But the choice of ammonium leaching agent is more expensive, the process is long.
3 Acid leaching method
The method is the magnesium ore crushed, immersed in sulfuric acid or HCL solution to produce MgSO4 or MgCl2, the use of precipitating agent to produce MgCO3 or Mg(OH)2 precipitation, calcined precipitate to get magnesium oxide. Commonly used precipitants are Na2CO3, NH3-H2O, (HN4)2CO3, NH4HCO3, and so on. Using serpentine as the magnesium source and sulfuric acid as the leaching agent, the leaching rate of magnesium was 98.40% when the particle size of the ore was 75 um, the concentration of sulfuric acid was 40%, the reaction temperature was 95°C, and the reaction time was 3h. Then NH4HCO3 was used as a precipitant to produce MgCO3,3H2O whiskers at a molar ratio of magnesium to ammonium carbonate of 1:2, an initial concentration of reactant C(Mg2+)=0.5 mol/L, a reaction temperature of 50 °C, a reaction time of 50 min, a reaction solution pH of 9.5, and an addition of the additive CXC-13 in an amount of 1% (mass fraction) of the total system, and the obtained The MgCO3,3H2O was calcined at 600°C for 2h to obtain magnesium oxide.
The reaction mechanism is as follows:
Acid leaching method is simple to operate, low equipment requirements, low cost, especially suitable for processing low-grade ores. But when acid leaching there will be a part of impurity ions into the solution, need to follow up on the leaching solution to remove impurities, improve product purity.
4 Carbonization method
The method is the calcined magnesium-containing ores to obtain the material, after digestion to generate Mg (OH) 2 suspension, and then carbonization, to produce Mg (HCO3) 2, pyrolysis to obtain basic magnesium carbonate, calcination to obtain magnesium oxide. Gan Yu et al. used dolomite as the magnesium source, and prepared high-purity MgO with 99.56% MgO content by digestion at a solid ratio of 10 mL/g, temperature of 60°C, stirring speed of 500 r/min, and reaction time of 1 h; carbonization at a liquid-solid ratio of 30 mL/g, temperature of 25°C, stirring speed of 600 r/min, CO2 admittance rate of 2 L/min, and carbonization time of 1 h; and pyrolysis at 90°C for 1 h. The MgO content of the MgO suspension was 99.56%, and the calcination yielded basic magnesium carbonate. MgO content of 99.56% was prepared.
The reaction mechanism is as follows:
Carbonization method is selective, not easy to corrode equipment, easy to control, simple process, stable product quality, and the CO2 used in this method is of low cost and wide source. The method is suitable for industrialized production and has great development prospects.