Hebei Messi Biology Co., Ltd. stated that a high-purity magnesium oxide sample was prepared by using light-burned dolomite powder as raw material, using the carbonization method, and adding sodium oxalate to remove calcium before pyrolysis of heavy magnesia water. By exploring the carbonization concentration (before carbonization The ratio of the mass of solids in the slurry to the mass of water), the influence of sodium oxalate dosage and aging time on the Ca2+ removal rate and Mg2+ loss rate, and the optimized process conditions are obtained:
When the carbonization concentration is 3g/L, the dosage of sodium oxalate is 6 times the theoretical dosage [based on n(Na2C2O4)/n(Ca2+) molar ratio], and the aging time is 6h, the magnesium oxide in the prepared high-purity magnesium oxide sample The content is 99.51%, the calcium oxide content is 0.17%, and the magnesium oxide recovery rate is 91.5%. X-ray diffractometer and scanning electron microscope were used to characterize the phase composition, particle size and morphological characteristics of the high-purity magnesium oxide sample. The results showed that the obtained magnesium oxide was in cubic crystal form; the average size of the magnesium oxide particles was 9 μm. It is evenly dispersed and has a regular spherical structure.
The specific preparation measures are as follows:
1) Use light-burned dolomite powder as raw material, adopt the carbonization method, digest, carbonize, and filter to obtain heavy magnesium water. Add sodium oxalate to heavy magnesium water to remove calcium, filter and pyrolyze to obtain high-purity basic magnesium carbonate. Calculate at 900°C for 1 hour to obtain high-purity magnesium oxide with a magnesium oxide content of 99.51% and a calcium oxide content of 0.17%. The recovery rate of magnesium oxide in the raw material is 91.5%. This experimental method solves the problem that it is difficult to effectively separate calcium and magnesium, and the amount of precipitant is small, and the extraction rate of magnesium oxide in the raw material is high.
2) The optimized process conditions for the calcium removal method by adding sodium oxalate to heavy magnesia water were determined: the carbonization concentration was 3g/L, the sodium oxalate dosage was 6 times the theoretical dosage, and the aging time was 6h. If the carbonization concentration increases, the removal rate of calcium from heavy magnesia water decreases; if the dosage of sodium oxalate increases and the aging time extends, the removal rate of calcium from heavy magnesium water first increases and then decreases.
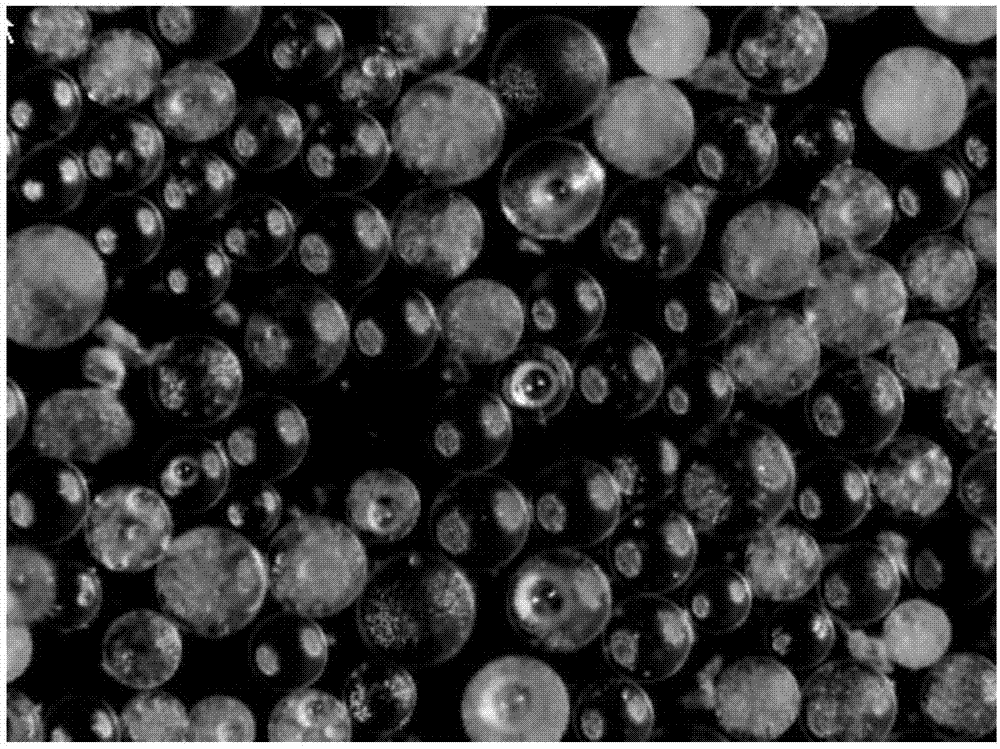
3) The magnesium oxide prepared by this method is in the cubic crystal form, with the shape of spherical particles, the particles are evenly dispersed, and the average size is 9 μm. The particle morphology is formed by the interlacing of flaky magnesium oxide with a thickness of less than 100 mm. Space spherical structure.