raw material:
equipment:
Reactor
Scrubber
dryer
grinder
Screening machine
Process flow:
1. Ingredients
Add magnesium oxide and water to the reaction kettle in a certain proportion.
2. Reaction
Carbon dioxide is introduced and the temperature is controlled at 60-70°C. Magnesium carbonate and water are produced during the reaction. The reaction equation is as follows:
MgO + CO2 + H2O → MgCO3·xH2O
3. Washing
After the reaction is completed, water is added to wash the reaction product to remove impurities.
4. Drying
The washed magnesium carbonate is dried to remove moisture.
5. smash
The dried magnesium carbonate is pulverized to obtain fine powder.
6. Screening
Use a sieving machine to classify the fine powder by particle size to obtain the required magnesium carbonate for cosmetics.
Key points of the process:
Reaction temperature control: Excessive temperature will lead to the formation of impurities and affect the quality of magnesium carbonate.
Number of washings: Adequate washing can effectively remove impurities and improve the purity of magnesium carbonate.
Drying method: Use appropriate drying methods to avoid magnesium carbonate adsorbing moisture and affecting its performance.
Degree of crushing: The size of the particles affects the effectiveness of magnesium carbonate in cosmetics.
Impurity control: Strictly control the reaction raw materials and process parameters to avoid the introduction of impurities and ensure the safety of magnesium carbonate.
Finished product standards:
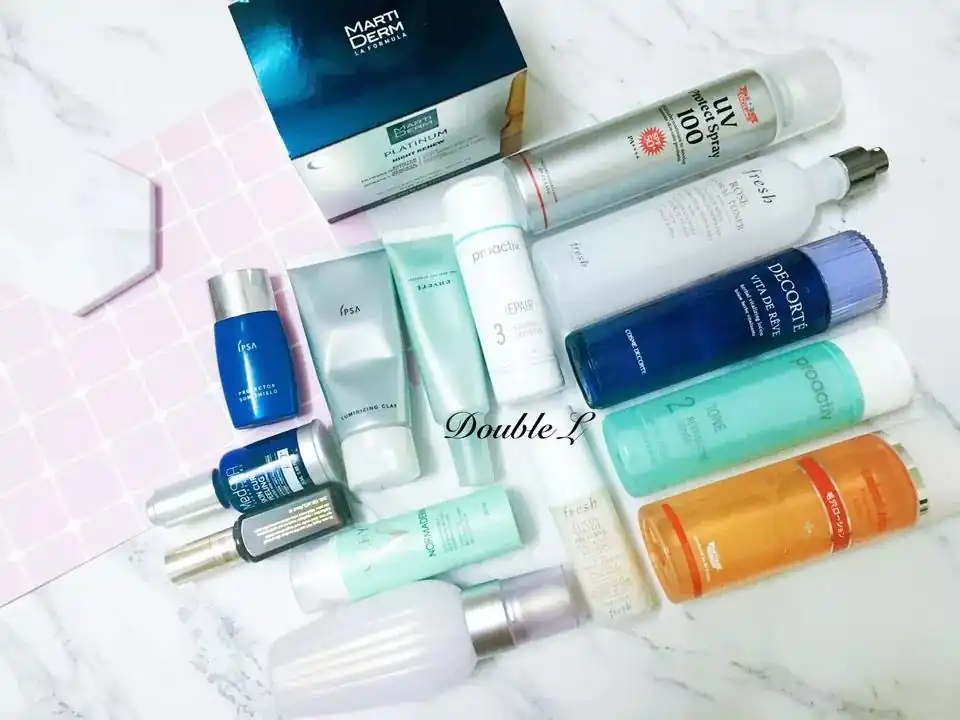
Magnesium carbonate for cosmetics should meet the following standards: