Magnesium hydroxide is an inorganic additive flame retardant with outstanding smoke suppression and flame retardant properties. At the same time, the surface of magnesium hydroxide is highly polar and hydrophilic. When added directly to polymers, it has poor dispersion and compatibility. , affecting the processing performance of composite materials. In order to improve the compatibility and dispersion of magnesium hydroxide with polymers and change its “hydrophilic and oleophobic” surface properties, magnesium hydroxide must be surface modified.
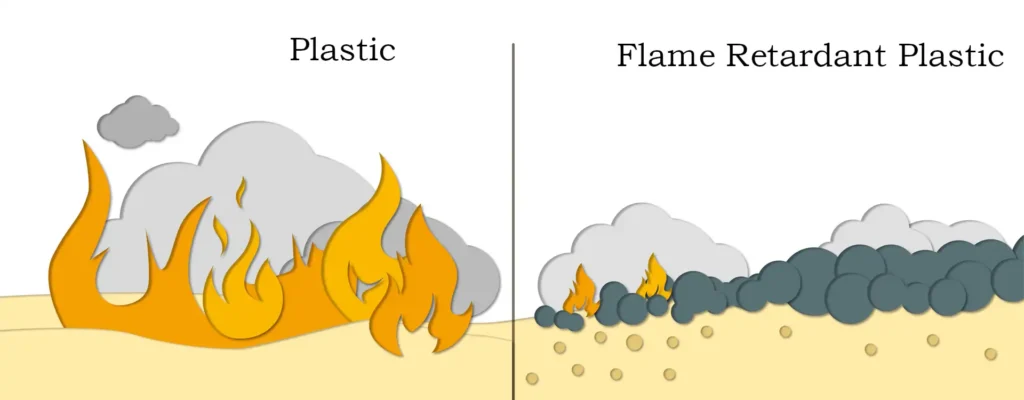
Magnesium hydroxide with special morphology, especially flakes and whiskers, when added to polymer materials, in addition to exerting flame retardant and smoke suppression effects, can also have other reinforcing effects due to its special morphology. This article uses composite modifiers to conduct wet surface modification research on magnesium hydroxide. Through single-factor experiments, various factors (stirring rate, time, temperature, modifier dosage, modifier type, modifier ratio, magnesium hydroxide slurry concentration, and feeding method) in the surface modification process of magnesium hydroxide were explored. , aging time, number of washings) on the modification effect.
And through orthogonal experiments, the optimal process conditions for the modification of magnesium hydroxide by composite modifiers were obtained. The conclusion is as follows: The optimal process conditions for Z1 type composite modifiers are: the dosage of surface modifier is 9%, The ingredient ratio of sodium oleate/sodium stearate/polyethylene glycol 6000 is 2:2:1, the modification temperature is 60°C, and the modification time is 100 minutes. The characterization results show that the modified magnesium hydroxide has good dispersion in paraffin. The infrared spectrum shows that the surface modifier molecules are chemically adsorbed on the surface of magnesium hydroxide. The SEM image shows that the agglomeration of modified magnesium hydroxide has been significantly improved. , water droplets showed an obvious “lotus leaf effect” on TLC thin layer chromatography plates paved with modified magnesium hydroxide.
At the same time, this article also conducted a preliminary exploration on the control of magnesium hydroxide crystal morphology. Under the conditions of supercritical state (T>31.1℃, P>7.38MPa), time 6h, polyethylene glycol 1000 as crystal control agent, and water as solvent, a base with a diameter of 1 to 5 μm and a length of 50 to 150 μm was prepared. Formula magnesium carbonate whiskers, after hydrothermal conversion, produced magnesium hydroxide whiskers with a diameter of 0.2 to 0.6 μm and a length of 2 to 8 μm; they were prepared using a microwave hydrothermal method at a microwave power of 400w, a temperature of 180°C, and a time of 80min. Magnesium hydroxide with regular hexagonal shape.