In today’s society, polymer synthesis technology is developing rapidly, and materials such as plastics, rubber and synthetic fibers are widely used in daily life. However, all polymers have defects, due to its own composition by a chain of carbon and hydrogen atoms, resulting in compounds that are flammable, which can lead to the rapid spread of fire.
When a certain amount of flame retardant is added to the material, the flame retardant properties of the material will be improved accordingly, but often the mechanical or other properties of the material will be affected, and sometimes it will bring inconvenience to the processing. Therefore, in order to maintain the comprehensive performance of flame retardant composites, the comprehensive performance of flame retardants should be considered.
Magnesium hydroxide has many advantages as a flame retardant material:
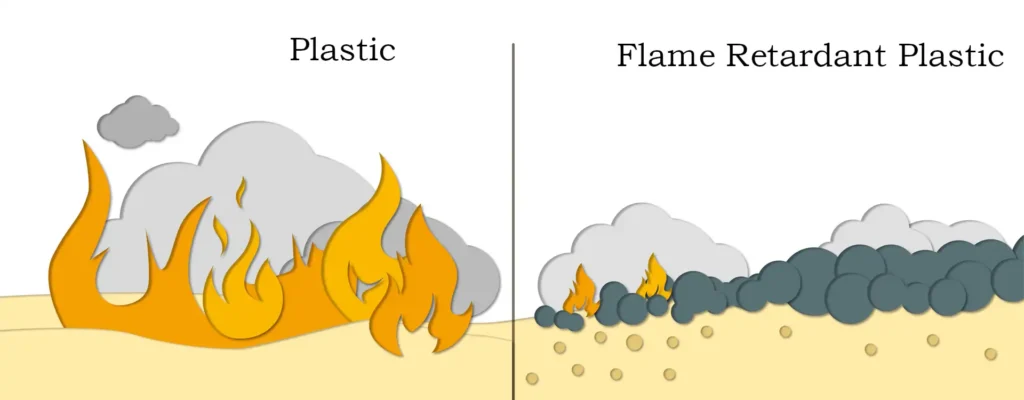
(1) Magnesium hydroxide has a high decomposition temperature and a higher ignition point than aluminum hydroxide, increasing the heating temperature of the polymer material;
(2) MgO generated after combustion and dehydration is a refractory material and is an alkaline oxide that absorbs acidic gases;
(3) Strong heat-absorbing capacity and high flame-retardant efficiency;
(4) Low cost and easy to process in different polymer materials.
In recent years, magnesium hydroxide as a kind of green flame retardant, the application amount is very large.
Preparation of magnesium hydroxide
Preparation of magnesium hydroxide most need to control two aspects: (1) filtration performance, if the magnesium hydroxide slurry settling performance is poor, it will affect the washing and separation operation process, resulting in magnesium hydroxide synthesis cycle is prolonged, and it will affect the yield of magnesium hydroxide; (2) control the morphology, because magnesium hydroxide with a regular morphology of the flame retardant effect is better, and therefore need to use the appropriate production methods and process conditions in order to achieve the Requirements.
The main production process of magnesium hydroxide has direct precipitation method, magnesium ore grinding method, magnesium oxide hydration method and so on.
Direct precipitation method
There are many methods for synthesizing magnesium hydroxide, among which the most used method is the precipitation method, which is easy to control the crystal morphology due to its low price and simplicity. In the precipitation method, mainly salt solutions are precipitated, usually with strong bases such as ammonia or sodium hydroxide. The most widely used magnesium salts are magnesium chloride, magnesium sulfate, and magnesium nitrate, and the organic magnesium salt magnesium acetate is also occasionally used.
The preparation of magnesium hydroxide by ammonia in the direct precipitation method is divided into one-step method and continuous precipitation method, and the continuous precipitation method realizes the recycling of resources, reduces the production cost, and ensures the quality of the product.
Hydrothermal method
Hydrothermal reaction can effectively control the shape and size of magnesium hydroxide, the nature of the product mainly depends on the type of precursor magnesium salt, solvent and the control of the reaction process temperature; the shape of the product mainly depends on the pH of the solution and the temperature of the reaction. The morphology of the synthesized magnesium hydroxide is nanofloral, acicular, flaky and spherical by adjusting the pH.
The advantage of hydrothermal synthesis is that the specific surface area of magnesium hydroxide is greater than 100m2/g. The disadvantage is that high temperature and pressure are used industrially and the cost is high.
Acoustochemical synthesis
Acoustochemical methods use ultrasonic waves in the range of 20 kHz-10 MHz to initiate the formation and collapse of microcells and produce active sites at high temperature and pressure. Compared to conventional methods, this method occurs under extreme conditions and can greatly increase the rate of the reaction, producing small crystals with a more homogeneous morphology. Sonochemical synthesis is characterized by the fact that different structural types of materials can be produced by changing the reaction medium.
Sol-gel method
The sol-gel method involves mixing highly reactive metal compounds as precursors in the liquid phase, which are hydrolyzed and condensed to produce metal hydroxides. A stable, transparent sol is formed, which is slowly polymerized by aging to form a network structure and loses solvent during the reaction process to form a gel. The gel undergoes subsequent drying and sintering to prepare nanomaterials.
The process of reaction of this method is the precursor dispersion dissolution, hydrolysis to generate monomers, polymerization occurs, the generation of sol, after drying and heat treatment and other processes, the preparation of nano-magnesium hydroxide materials.
The use of magnesium hydroxide
Magnesium hydroxide has a wide range of uses, the flame retardant field and the environmental protection field are the main fields of magnesium hydroxide application. In addition, due to the high activity of magnesium hydroxide slurry, adsorption performance is good, convenient and controllable adjustment, magnesium hydroxide can be used as a neutralizing agent for acidic waste liquids and sulfur-rich oxides treatment, heavy metal removal, to improve the acidity of the soil, but also as an antacid agent used in pharmacy, fertilizer additives and so on.
Flame retardant applications
Magnesium hydroxide is an important halogen-free environmentally friendly green flame retardant, flame retardant mechanism for the generation of a stable coating layer of magnesium oxide and water vapor, flame retardant efficiency is low, in order to achieve a good flame retardant effect of its additive amount is generally as high as 50% to 60%, and at this time the mechanical properties of flame retardant composites and the processing of a serious decline in the performance of the material, and the method usually taken is the surface modification of magnesium hydroxide and magnesium hydroxide synergistic synergy. Flame retardant.
Magnesium hydroxide flame retardant can not only be used alone, but also with other synergistic agents used in combination, such as magnesium hydroxide / red phosphorus, magnesium hydroxide / zinc borate, magnesium hydroxide / carbon nanotubes and magnesium hydroxide / carbon black and so on. The synergistic flame retardant of magnesium hydroxide will not only obtain better flame retardant effect, but also reduce the amount of flame retardant, thus reducing the cost.
Application in the field of environmental protection
(1) Acid-containing wastewater treatment
The neutralization reaction speed of magnesium hydroxide is slow, and the particles produced after the neutralization reaction are large in size and settle quickly. Magnesium hydroxide in the treatment of acidic wastewater can realize the simplification of the operation process and the reduction of operation time, good controllability, and the reduction of treatment costs.
(2) Heavy metal removal
Due to the large specific surface area of magnesium hydroxide particles, it has strong adsorption capacity and can remove heavy metal ions such as Ni2+, Cd2+, Mn2+ and so on from industrial wastewater waste water which are harmful to the environment, and other heavy metal elements such as Mo, Co, Fe, W and V can also be removed by magnesium hydroxide, lightly burnt magnesium oxide or magnesium aluminum carbonate.
(3) Flue gas desulfurization
At present, the more mature desulfurization technology will be nearly 20 kinds, among them, magnesium hydroxide desulfurization technology is economical and practical, and has a good development prospect in the future. Magnesium hydroxide desulfurization process advantages include high desulfurization efficiency, low investment costs, low operating costs, high comprehensive benefits, reliable operation and does not produce secondary pollution.
Conclusion
Magnesium hydroxide as a flame retardant has excellent performance in various aspects, and its application will be more and more extensive. And magnesium hydroxide has the advantage of cheap price, which saves cost for factory production. The preparation of magnesium hydroxide by lightly burnt magnesium powder improves the added value of the product, realizes the effective utilization of resources, and can effectively enhance the competitiveness of enterprises in the market economy.