Magnesium hydroxide is a new type of filling flame retardant. When it is heated and decomposed, it releases bound water and absorbs a large amount of latent heat to reduce the surface temperature of the component material it fills in the flame. It has the effect of inhibiting polymer decomposition and cooling the generated combustible gas.
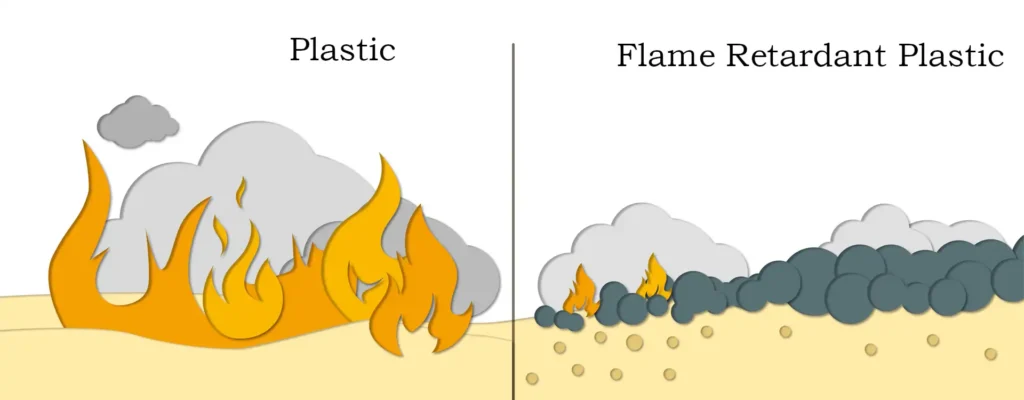
As a flame retardant material, magnesium hydroxide has many advantages:
(1) The decomposition temperature of magnesium hydroxide is high, and the ignition point is higher than that of aluminum hydroxide, which increases the heating temperature of polymer materials;
(2) MgO generated after combustion and dehydration is a refractory material and an alkaline oxide that can absorb acidic gases;
(3) It has strong heat absorption capacity and high flame retardant efficiency;
(4) It is low in cost and easy to process in different polymer materials.
In recent years, magnesium hydroxide has been widely used as a green and environmentally friendly flame retardant.
Preparation of magnesium hydroxide
There are two aspects that need to be controlled in the preparation of magnesium hydroxide:
(1) Filtration performance. If the magnesium hydroxide slurry has poor sedimentation performance, it will affect the washing and separation operation process, resulting in an extension of the magnesium hydroxide synthesis cycle and affecting the output of magnesium hydroxide;
(2) Control of morphology. Because magnesium hydroxide with a regular morphology has a better flame retardant effect, it is necessary to adopt appropriate production methods and process conditions to meet the requirements.
The main production processes of magnesium hydroxide include direct precipitation method, magnesium-containing ore grinding method, magnesium oxide hydration method, etc.
Direct precipitation method
There are many methods for synthesizing magnesium hydroxide at present. Among them, the precipitation method is used. Due to its low price and simple and easy operation, it is easy to control the crystal morphology. In the precipitation method, it is mainly salt solution precipitation, usually using strong alkali such as NH3·H2O or NaOH. The most widely used magnesium salts are MgCL2, magnesium sulfate and magnesium nitrate. Organic magnesium salts such as magnesium acetate are also occasionally used.
The ammonia method for preparing magnesium hydroxide in the direct precipitation method is divided into a one-step method and a continuous precipitation method. The continuous precipitation method realizes the recycling of resources, reduces production costs, and ensures product quality.
Hydrothermal method
The morphology and size of magnesium hydroxide can be effectively controlled by hydrothermal reaction. The properties of the product mainly depend on the type of precursor magnesium salt, the control of solvent and reaction process temperature; the morphology of the product mainly depends on the pH of the solution and the temperature of the reaction. By adjusting the pH, the morphology of magnesium hydroxide can be synthesized into nano-flowers, needles, flakes and spheres.
The advantage of hydrothermal synthesis is that magnesium hydroxide with a specific surface area greater than 100m2/g can be obtained. The disadvantage is that high temperature and high pressure are used in industry, which is costly.
Sonochemical synthesis method
The sonochemical method uses ultrasonic waves with a frequency range of 20kHz-10MHz to induce the formation and collapse of micelles, and produce active sites under high temperature and high pressure. Compared with traditional methods, this method occurs under extreme conditions, which can increase the reaction rate and generate small crystals with more uniform morphology. The characteristic of sonochemical synthesis is that materials of different structural types can be produced by changing the reaction medium.
Sol-gel method
The sol-gel method uses highly active metal compounds as precursors, liquid phase mixing, hydrolysis, condensation, and metal hydroxides. A stable transparent sol is formed, which slowly polymerizes after aging to form a network structure. During the reaction, the solvent is lost to form a gel. The gel is subsequently dried and sintered to prepare nanomaterials.
The reaction process of this method is that the precursor is dispersed and dissolved, hydrolyzed to form a monomer, polymerized, and a sol is formed. After drying and heat treatment, nano magnesium hydroxide materials are prepared.