Summary
The fire and wet processes commonly used by several representative copper oxide cobalt ore smelting enterprises in Katanga Province of the Democratic Republic of the Congo are introduced and reviewed. Among them, the country’s state-owned enterprises produce final products such as electric copper and electric cobalt, while the country’s Chinese-funded enterprises generally produce intermediate products or semi-finished products. Due to the lack of chemical reagents and raw and auxiliary materials for the smelting of copper oxide cobalt ore in the country, importing related reagents and materials has increased the production costs of enterprises.
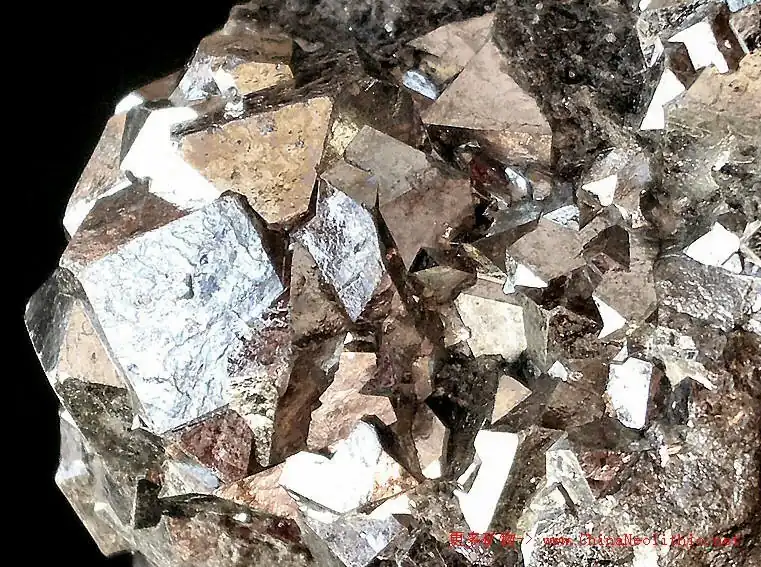
Overview
The Democratic Republic of the Congo is extremely rich in mineral and hydraulic resources and is rich in non-ferrous metals and rare metals. Mining is an important economic pillar. The country has high-grade copper oxide and cobalt mines buried underground, and its cobalt output ranks first in the world. Local companies usually use pyrotechnics and wet processes to process copper oxide cobalt ore. In 2011, the author inspected several representative copper oxide cobalt ore smelting companies in Katanga Province. This article will analyze these smelting processes and product forms. introduce. Likasi City in this province is located in the southeastern part of the Democratic Republic of the Congo, close to Zambia. The local copper-cobalt ore resources are very rich, including copper-cobalt oxide ore and copper-cobalt sulfide ore. Since the smelting process of copper-cobalt sulfide ore has not been investigated, this article only introduces the smelting process of copper-cobalt oxide ore. However, according to the information, the smelting of copper and cobalt sulfide ore adopts the boiling oxidation roasting process, roasting flue gas to produce acid, and the roasting slag follows the process route of smelting copper and cobalt sulfide ore.
In the Democratic Republic of the Congo, except for a few large and medium-sized companies that have mines, most small and medium-sized smelting companies do not have mines. Copper and cobalt raw materials come from purchase stations set up by companies. The acquired copper oxide ore (high copper, low cobalt,
Copper is priced, cobalt is not priced) The copper grade range is 8% to 40% and 6% to 45% respectively, and cobalt oxide ore (cobalt is high, cobalt is priced, copper is not priced) the cobalt grade range is 2% to 20%.
1 Introduction to smelting process
1.1 Company A
Company A is a state-owned enterprise (including mines) in the Democratic Republic of the Congo. It started producing copper in 1929 and began producing cobalt in 1940. At present, wet processes are used to process copper oxide cobalt ore raw ore (containing 2.5% copper and 0.1% to 1% cobalt) and concentrate (containing 20% to 25% copper and 2% to 2.5% cobalt). There are electric copper and There are two production processes for electric cobalt. Electric copper production process: Copper oxide cobalt raw ore and concentrate are mixed in proportion. After the mixed concentrate is ball milled, copper and cobalt are leached step by step using sulfuric acid reduction. The leaching temperature is 60-80°C, the copper leaching time is 2 hours, and the cobalt leaching time is 6 hours; add The reducing agent sodium metabisulfite reduces trivalent cobalt to divalent cobalt for leaching. The leachate is filtered multiple times (mainly sand filtration) and then copper particles are added to precipitate selenium and sent to the copper electrowinning workshop to produce electric copper. Electric cobalt production process: The post-copper electroplating solution uses sulfidation, neutralization, and hydrolysis to remove impurities such as copper, iron, and nickel. Flocculants are widely used in the clarification process. The deimpurity solution is sent to the electric cobalt workshop to produce electric cobalt, and the electric cobalt melts water. After quenching, cobalt particles are obtained.
The total recovery rate of copper is 80%, and the total recovery rate of cobalt is 60%. Copper smelting consumes 3.5 t/t copper sulfuric acid; cobalt smelting consumes 8.5 t/t cobalt sulfuric acid and 10 t/t cobalt lime. The company’s annual output of electrical copper is about 10 kt, and its annual output of electrical cobalt is about 500 t. Except for the self-produced sulfuric acid (sulfuric acid, the same below) and lime milk, all the reagents used were imported from South Africa.
1.2 Company B
Company B is a Chinese-funded enterprise. It has two production systems that use the fire process and the wet process to process the copper oxide cobalt ore purchased from various places. The copper oxide ore with a copper grade of less than 15% enters the wet process system, and the cobalt grade is low. Enter the fire method system using 1% cobalt oxide ore.
The pyrotechnic process uses electric furnace reduction smelting to produce blister copper and copper-cobalt alloys. Copper oxide cobalt ore, flux limestone, and reducing agent coke are mixed and added to the electric furnace at a smelting temperature of 1,200°C to produce blister copper containing more than 92% copper, which is cast into blister copper blocks; molten electric furnace slag is produced and then fed into another electric furnace It is added with coke for reduction smelting to produce copper-cobalt alloy, with a smelting temperature of 1 400 ℃ (copper + cobalt ≥ 40%). The metallurgical principle is to control the amount of reducing agent coke and the smelting temperature to achieve the purpose of step-by-step reduction. Copper is first reduced in the first electric furnace, and then copper and cobalt are reduced in the second electric furnace. The annual output of blister copper and copper-cobalt alloy is approximately 10 kt and 2 kt respectively, and the products are sold to China.
Wet process: The copper oxide cobalt ore is ball-milled to 100 mesh, and the copper and cobalt are leached step by step using sulfuric acid and ferrous sulfide. The leaching liquids are combined and subjected to extraction and electrowinning to produce electrolytic copper. The raffinate is extracted regularly and is neutralized and initially removed from impurities. Take crude cobalt hydroxide. The electrolytic copper is sold locally, and the crude cobalt hydroxide is sold to China. The plant produces its own sulfuric acid, and except for lime, other chemical reagents are purchased from China.
1.3 Company C
Company C is a Chinese-funded enterprise that uses electric furnace reduction and smelting to process copper oxide cobalt ore to produce copper-cobalt alloy. Approximately 100 tons of oxidized copper and cobalt ore are processed daily, and 11 to 13 tons of copper-cobalt alloys are produced. This process uses limestone to make slag and pulverized coal to reduce. The alloy temperature is 1250 ℃ and the slag temperature is 1500~1600 ℃. In the rainy season, the concentrate has high moisture content and needs to be dried in an internally heated rotary kiln. Concentrates, limestone, and coal are lifted into the silo by grabs in the concentrate silo, unloaded to belts, and transported to 4 bins on the top of the furnace respectively; there is a belt under each bin to transport the three materials to the buried scraper. The material in the buried scraper then enters the two buried scrapers on the top of the furnace. Each buried scraper has several discharge openings. There is a material level rod on the top of the furnace to measure the slag level and alloy level. Both the slag and the copper-cobalt alloy are released by water quenching. The copper-cobalt alloy is sold to China and the slag is discarded.
C Enterprises purchase local copper oxide cobalt ores, which generally require a cobalt content of >4%, a slag containing cobalt and an annual average copper content of 0.2% to 0.4%, and a copper-cobalt alloy containing copper + cobalt of 30% to 40% and nickel of 3%. ~7%, iron 30% ~ 40%, SiO25% ~ 10%.
1.4 Company D
Company D is a Chinese-funded enterprise that uses wet process to process copper oxide cobalt ore (containing 5% to 10% copper and 2% to 5% cobalt). The ore is ball-milled to 100 mesh and put into the leaching tank, heated, and sulfuric acid and the reducing agent ferrous sulfate (made on-site by adding sulfuric acid and iron powder to the raffinate) are added for leaching. The leached copper and cobalt sulfate slurry is neutralized and acidified with calcium carbonate slurry. After dense separation, the underflow and clear liquid are obtained; the clear liquid is clarified and filtered for primary extraction, and the copper-rich liquid is obtained by back-extraction and fed into electrowinning to produce copper. The primary raffinate is combined with the underflow for stirring and washing. After solid-liquid separation, the leaching residue is produced and washed and then discharged; the filtrate is clarified and then subjected to secondary extraction. The secondary raffinate is neutralized with calcium carbonate slurry to adjust acidity and then densely separated, and the underflow is returned to stir and wash; while the clear liquid is heated under heating conditions and uses the neutralizing agent magnesium oxide for primary neutralization to precipitate cobalt and secondary neutralization. Cobalt is precipitated and crude cobalt hydroxide is produced as the final product. The neutralized liquid is treated and then discharged or partially recycled. The design of the electroplating workshop is simple. Plastic balls are placed in the electroplating tank to isolate the acid mist. A simple floor-standing crane is used to lift out the tank. The electroplated copper is soaked in a 90°C soaking tank and then removed and manually peeled. The company produces its own sulfuric acid, with an annual output of about 10kt of electrolytic copper. The total recovery rate of smelting copper is 95%, and the total recovery rate of cobalt is 88%.
1.5 Company E
Enterprise E is a Chinese-funded enterprise, and the copper oxide and cobalt ore it handles contains high copper (>10%) and low cobalt. First, the ore is ball-milled to 100 mesh, and the copper and cobalt are leached with sulfuric acid. The leaching liquid is directly sent to electroplating to produce electric copper. After electroplating, the liquid returns
The copper oxide cobalt ore is leached back; the copper-rich liquid obtained by extraction and back-extraction of the leaching residue washing water is sent to the electrolytic deposition tank to produce electric copper. No reducing agent is added during leaching, nor is it heated, so the concentration of leached cobalt is low. Finally, the cobalt is neutralized when the wastewater is discharged to obtain cobalt carbonate. The company’s annual output is approximately 3 kt of electrolytic copper and a small amount of cobalt carbonate.
2 Review of smelting process
1) Company A takes a long time to build and produce the plant. The copper and cobalt smelting process is mainly leaching + impurity removal + electroplating. The impurity removal in the leach liquid mostly uses neutralization and sulfidation, and solid-liquid separation and filtration basically uses sand filtration. Due to lengthy processes, outdated equipment, etc., the recovery rate of copper and cobalt smelting is low and the consumption of reagents such as sulfuric acid is high. Nowadays, in copper and cobalt smelting enterprises, the impurity removal of copper and cobalt leaching liquid basically adopts the extraction and stripping process of high-efficiency removal to purify and enrich the copper. The cobalt in the raffinate can also be purified and enriched by the extraction and stripping process, which can be used to produce electrical cobalt. For raw materials, solid-liquid separation is basically achieved using a filter press or thickener.
2) Company B uses the fire process to process the copper oxide cobalt ore with high copper and low cobalt. The cheap hydropower in the Democratic Republic of the Congo supports electric furnace smelting; while the copper oxide cobalt ore with low copper and high cobalt uses the wet process.
3) Company C’s oxidized copper-cobalt ore contains low copper and cobalt and is treated by fire process.
4) Company D’s oxidized copper-cobalt ore contains low copper and cobalt and is processed by wet process. This process is long, complete and classic. The copper is first pre-leached step by step, and then the on-site ferrous sulfate is added to leach the cobalt. The leached copper-cobalt slurry is heated when adding the calcium carbonate slurry; a second extraction is performed: the copper-rich liquid produced by the primary extraction and back-extraction is electrolytically To produce electrolytic copper, the primary raffinate and the leaching underflow are stirred and washed, and the clear liquid is subjected to secondary extraction; cobalt is enriched into the secondary raffinate, and magnesium oxide is added to the secondary raffinate for a second time to neutralize the precipitated cobalt. Crude cobalt hydroxide. Magnesium oxide is more expensive, but the characteristic of adding magnesium oxide is that it consumes a large amount of acid equivalent for neutralization. Magnesium does not precipitate when cobalt is precipitated, which reduces the impurity content in cobalt hydroxide and facilitates the subsequent purification process of crude cobalt hydroxide; neutralizers are Calcium carbonate (limestone) is used to grind the slurry; most of the washing water and slurry are returned to the previous process for treatment.
5) Enterprise E is a Chinese-funded enterprise. Since the copper oxide cobalt ore it processes contains high copper and low cobalt, it uses a wet process to process it. By controlling a certain liquid-to-solid ratio, it can obtain a leachate with a high concentration of copper sulfate, which can be directly Perform electroplating to produce electric copper containing 99.9% copper. Because copper oxide cobalt ore contains low cobalt, the main process only considers the recovery of copper and adopts a simple design. It does not use reduction heating leaching but uses room temperature stirring leaching, which eliminates the extraction process and reduces production costs.
3 Conclusion
1) There are generally two processes for smelting copper oxide cobalt ore, namely the fire process and the wet process. The pyrotechnic process is electric furnace reduction smelting to produce blister copper and copper-cobalt alloy, or only copper-cobalt alloy. If the copper oxide cobalt ore contains high copper and a small amount of cobalt, blister copper and copper-cobalt alloy can be produced. If the copper and cobalt content are not high, copper-cobalt alloy can be produced directly. The wet process is the reduction and leaching of copper and cobalt from copper oxide cobalt ore. The leachate treatment process depends on the concentration of copper.
If the concentration of copper is high, the leachate will be sent directly to the electrolytic deposition workshop to produce electrolytic copper. After electrolytic deposition, the liquid will oxidize and neutralize precipitated iron, and sodium carbonate will precipitate copper to produce basic copper carbonate. Sodium carbonate will neutralize precipitated cobalt to produce cobalt carbonate; If the concentration of copper is low, the leachate is sent to the extraction workshop to enrich the copper and then to the electrowinning workshop to produce electrical copper. The cobalt is not extracted, and is neutralized in the raffinate to recover cobalt semi-finished products in the form of crude cobalt hydroxide or cobalt carbonate.
2) State-owned enterprises in the Democratic Republic of the Congo produce final products such as electric copper and electric cobalt; while Chinese-funded enterprises generally produce intermediate products or semi-finished products to reduce investment and production costs as much as possible.
3) There is a lack of chemical reagents and raw and auxiliary materials required for smelting copper oxide cobalt ore in the Democratic Republic of the Congo. Companies generally produce their own sulfuric acid, and extractants, sodium carbonate, etc. must be imported from abroad, which increases production costs.