Magnesium oxide is a very common alkaline oxide and the main raw material for the production of magnesium hydroxide and magnesium metal. In the application of ceramic materials, magnesium oxide has a melting point as high as 2800°C and has some special and excellent properties. Therefore, it is also quite popular in the field of advanced ceramics. It can be directly sintered into magnesium oxide ceramics or used as an additive.
Magnesium oxide powder preparation
The preparation of magnesium oxide is divided into brine-ammonia precipitation method, dolomite carbonization method, magnesium salt thermal decomposition and rhombus ore thermal decomposition method, etc. In terms of preparation, the raw materials come from minerals or seawater. MgO is extracted from minerals or seawater. Most of them are first made into magnesium hydroxide or magnesium carbonate, and then decomposed into MgO by calcination. This MgO can be obtained through further chemical treatment or heat treatment to obtain high purity. For MgO, if high-purity MgO ceramics are required, additives cannot be added to promote sintering and grain growth. Instead, activation sintering is used, that is, Mg(OH)2 is calcined at an appropriate temperature to obtain a product with many properties. Active MgO with lattice defects is used to make sintered magnesium oxide ceramics.
Magnesium oxide ceramic
(1) MgO transparent ceramic
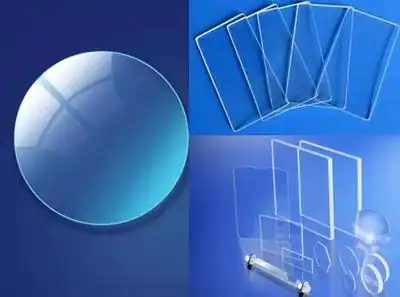
MgO transparent ceramic has good transparency and infrared light transmittance. It is an optical isotropic body with good alkali metal vapor corrosion resistance, high melting point, high thermal conductivity, small theoretical density, high insulation and High infrared transmittance and other advantages. It is widely used in the field of visible light and infrared light-transmitting materials, and its performance is better than that of alumina ceramics. It is a promising material.
Typical applications: It is an important material for preparing infrared windows and fairings of spacecraft and rocket missiles, high-temperature furnace infrared windows, high-temperature infrared optical devices, optical filters and optical detectors, high-pressure sodium lamp luminous tubes and infrared detector covers.
(2) MgO foam ceramics
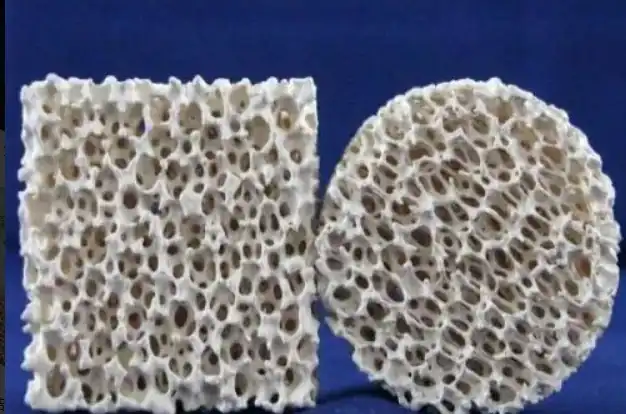
As a new type of ceramic functional material, foam ceramic material has been developed since the 1970s. MgO foam ceramic has a unique three-dimensional network skeleton structure, which gives it an opening rate of 60%-90%. It can effectively remove large debris and most tiny suspended inclusions in the molten metal, and has high fire resistance. strength, high porosity, low thermal conductivity, low manufacturing cost, simple preparation process, and good mechanical properties. In China, Li Wenxia and others from Peking University used magnesium oxide as aggregate and added an appropriate amount of ZrO2 to prepare a magnesium oxide partially stabilized zirconia foam ceramic filter. They have achieved good results in the production of nickel-based alloy single crystal wafers and filled the gap. Domestic technology gaps.
typical application:
a. Filter. The filter cake effect, adsorption effect and rectification effect are used to filter impurities in the magnesium alloy melt and improve the filtration efficiency.
b. Energy-saving insulation materials. It can be used as kiln lining and in the aerospace industry to insulate and protect aerospace equipment.
c. Sound-absorbing materials. According to research, its noise reduction coefficient is close to that of glass wool and has good application prospects.
d. Catalyst carrier material. With good adsorption capacity, it can be widely used as a carrier for automobile exhaust purifiers.
e. Food and pharmaceutical industry. It is used for the concentration, separation and refining of physiologically active substances such as enzymes, vaccines, nucleic acids, etc. in the pharmaceutical industry to ensure food safety.
(3) MgO series microwave dielectric ceramics
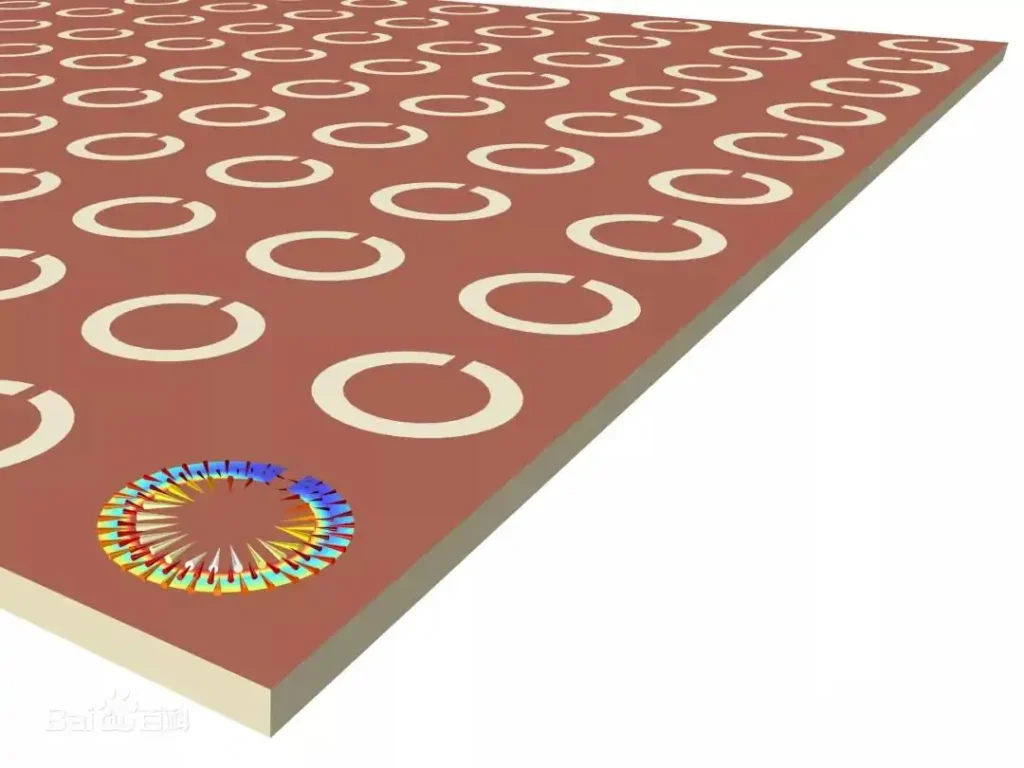
With the update and iteration of mobile communications and satellite communications technology, people have higher and higher requirements for communication frequency bands, making low dielectric and high Q ceramics a research hotspot. On the one hand, MgO ceramic itself has excellent dielectric properties (εr=9.1, tanδ<1.6×10-6) and is an ideal microwave dielectric substrate material for 5G communications.
MgTiO3-based microwave dielectric ceramics have an ilmenite structure of space group R3. This material has been studied and applied to ceramic capacitors and resonators due to its low tan δ and high-frequency thermal stability. In addition, MgTiO3 has the potential to be used in filters, communication antennas, radars, direct broadcast satellites and microwave frequency global positioning systems.
MgAl2O4 has a spinel-type structure with high hardness, high melting point, and high strength. Pure MgAl2O4 is transparent and can be used in transparent armor, infrared windows, radome and other fields. Not only that, MgAl2O4 also has the characteristics of low εr and can also be used as microwave dielectric ceramics. MgAl2O4 series ceramics prepared by microwave sintering have excellent comprehensive properties and can meet the requirements of various fields.
(4) MgO ceramic core type
Magnesium oxide has good high-temperature properties. When using magnesium oxide-based ceramic cores to footcast stainless steel castings, even if the pouring temperature is as high as 1650°C, the core material will not react with the alloy. The internal surface of the castings has high smoothness, and it is a weakly alkaline refractory material. It can be dissolved in organic acid solutions such as phosphoric acid and acetic acid, and is easy to remove the core. It does not produce thermal cracking defects. Currently, there is little research on magnesium-based ceramic core shapes, and it has a lot of room for development.