Abstract: Activated magnesium oxide was used to enrich nickel and cobalt by selective precipitation from sulfate media containing manganese and magnesium. The results show that the optimal precipitation conditions are: after slurrying, add two times the theoretical amount of activated magnesium oxide, reaction residence time of 6 h, precipitation temperature of 25 ℃. Under these conditions, the nickel and cobalt precipitation rates were 97.96% and 96.43%, respectively, and the contents of nickel, cobalt, manganese and magnesium oxide in the precipitates were 8.51%, 13.05%, 2.29% and 4.97%, respectively, and the average static free settling velocity of the slurry was 180 mm/min when 0.2 g of flocculent AN905 was added to each cubic meter of the slurry.
Study on Selective Precipitation of Nickel and Cobalt from Sulfate Medium with Active Magnesium Oxide
Abstract: Nickel and cobalt were selectively precipitated and enriched from Mn, Mg containing sulfate medium with active magnesium oxide. The results show that the optimum precipitation conditions include twice of theoretical dosage of active magnesium oxide, reaction time of 6 h, and precipitation temperature of 25 ℃. The results show that the optimum precipitation conditions include twice of theoretical dosage of active magnesium oxide, reaction time of 6 h, and precipitation temperature of 25 °C. The precipitation rate of nickel and cobalt is 97.96% and 96.43% respectively. The content of nickel, cobalt, manganese and magnesium oxide in the precipitate is 8.51%, and the content of cobalt and magnesium oxide in the precipitate is 8.51%. precipitate is 8.51%, 13.05%, 2.29%, and 4.97% respectively. The average static-state free settling velocity of slurry is 180 mm/min with the dosage of The average static-state free settling velocity of slurry is 180 mm/min with the dosage of flocculant AN905 of 0.2 g/m3 .
Key words: active magnesium oxide; precipitation; nickeliferous laterite; copper & cobalt oxide ore; nickel and cobalt selective precipitation
When nickel laterite ore or copper cobalt oxide ore is subjected to acid leaching[1-10] , nickel, cobalt, manganese and magnesium usually coexist in the solution during the process of solution purification and separation. The traditional methods of nickel and cobalt enrichment and separation in this solution are sulfide precipitation and neutralization precipitation[8-9] . Sulfidation precipitation method needs to control the precipitation pH during the precipitation process due to the use of alkaline precipitants such as H2 S, NaHS, Na2 S, NH4 HS and sodium dithiocarbamate (SDD), and the pH is too low there will be H2 S gas generated, which affects the operating environment, but the content of manganese and magnesium in the precipitate is high when the pH is too high, which will affect the purification and separation of the subsequent valuable metals, and the operating conditions are harsh, which is not conducive to the production of[11-14] . In the neutralization precipitation method, the traditional neutralizing agent usually adopts Na2 CO3 or NaOH with strong alkali, and the local over-alkali phenomenon usually occurs in the neutralization and precipitation process, which leads to the high content of manganese and magnesium in the enriched material; in addition, there is also the formation of hydroxide colloid in the precipitation process, which is not conducive to the separation of liquid and solid of precipitates[15-16] , and it also brings the impurity ions, such as Na+ , NH4+ , etc., to the post-precipitation fluid and brings the difficulties to the treatment of the post-precipitation fluid. The treatment of the precipitated liquid is difficult. In view of the above problems of sulfide precipitation and traditional neutralization precipitation method, this paper uses activated magnesium oxide as precipitating agent to selectively precipitate nickel and cobalt from sulfuric acid medium containing manganese and magnesium.
1 Experimental materials and methods
A low-grade oxidized copper-cobalt ore sulfuric acid leaching-extraction recovery of copper-oxidation and neutralization of iron and aluminum removal pH = 4.5 solution as raw materials, the main metal ion composition is (g / L): Ni 0.22, Co 0.36, Mn 4.15, Mg 3.45. precipitant used active magnesium oxide, containing MgO 94.48%.
According to the 25 ℃ potential-pH equilibrium diagram of the aqueous solutions of nickel, cobalt, manganese and magnesium ions, when the initial mass concentration of nickel in the solution is 0.58 g/L, the pH of the beginning of the precipitation is 7.1, and the pH of the basic precipitation is 8.1; when the initial mass concentration of cobalt in the solution is 0.59 g/L, the pH of the beginning of the precipitation is 7.2, and the pH of the basic precipitation is 8.2; when the initial mass concentration of manganese in the solution is 5.5 g/L, the pH of the beginning of the precipitation is about 8.2, and the pH of the basic precipitation is 9.8 When the initial mass concentration of manganese in the solution is 5.5 g/L, the pH of the beginning of precipitation is about 8.2, and the pH of the basic precipitation is 9.8; when the initial mass concentration of magnesium in the solution is 2.4 g/L, the pH of the beginning of precipitation is about 9.5[17-19] . Therefore, according to the composition of the raw material solution used for the test, the initial separation of nickel and cobalt from manganese and magnesium in the solution can be carried out by using neutralization and precipitation.
Test method: take a certain volume of solution, heat to a set temperature, under strong stirring, slowly add a certain number of times the theoretical amount of activated magnesium oxide powder, and monitor the solution pH. after a certain time of reaction, filter, take the filtrate to analyze the content of manganese, nickel, cobalt in the solution, the filter cake is washed with water and then dried, and analyze the content of nickel, cobalt, manganese and magnesium in the precipitate.
The theoretical addition of active magnesium oxide is based on the amount of magnesium oxide needed for complete precipitation of nickel and cobalt, calculated by Eq:
m(MgO) = ((c(Ni)/58.69+c(Co)/58.93+c(Zn)/65.38)×40.3×V)/η
Where, m(MgO) is the theoretical amount of magnesium oxide required, g; c(Ni), c(Co), c(Zn) are the content of nickel, cobalt, and zinc in the solution, respectively, (g/L); V is the volume of the solution, L; and η is the content of magnesium oxide in the activated magnesium oxide.
2 Results and Discussion
2.1 The effect of the amount of active magnesium oxide added
Fixed conditions: reaction time 4 h, reaction temperature 60 ℃, direct addition of magnesium oxide powder, control of the addition rate by controlling the pH of the solution <8.0, the effect of the addition of active magnesium oxide powder on the precipitation is shown in Figure 1.
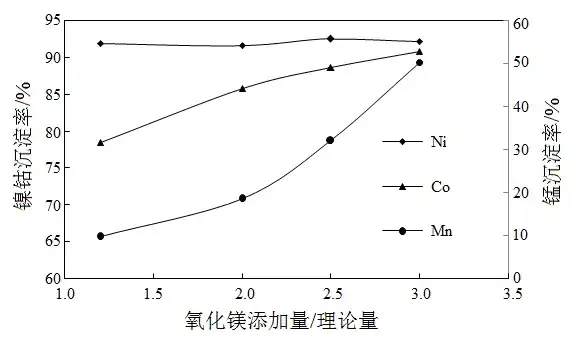
Fig.1 Effect of dosage of active magnesium oxide on precipitation
Figure 1 shows that the manganese precipitation rate in the solution increased significantly by increasing the addition amount of active magnesium oxide. In the magnesium oxide additive amount for the theoretical amount of 3 times, 60 ℃ conditions, nickel, cobalt precipitation rate is very high, but manganese precipitation rate is also as high as 50.23%. Therefore, the amount of magnesium oxide added in 2 times the theoretical amount can be controlled, the conditions, nickel, cobalt precipitation rate of 91.61% and 85.72%, respectively, manganese precipitation rate of 18.49%, but still on the high side, but also need to carry out other conditions to optimize.
2.2 Effect of the way of adding active magnesium oxide
In the test, it was found that when the active magnesium oxide powder was added to the solution, it first formed a small group floating on the liquid surface, and then slowly diffused into the solution after stirring for a period of time, which might affect the utilization efficiency of the magnesium oxide and cause local over-alkali phenomenon in the solution. Usually the addition of neutralizing agent is first slurry and then add, so as to avoid the powder neutralizing agent due to the role of surface tension leads to the neutralizing agent diffusion speed reduction and localized over-alkaline and lead to precipitates wrapped in the neutralizing agent, reduce the utilization rate of the neutralizing agent and other issues. The following two forms of adding active magnesium oxide slurry and powder test comparison.
Test conditions: reaction time 4 h, temperature 60 ℃, add 2 times the theoretical amount of active magnesium oxide. When the active magnesium oxide added in powder form, the composition of the liquid after precipitation is (g/L): Ni 0.017, Co 0.051, Mn 3.38, liquid meter precipitation rate (%): Ni 92.37, Co 85.72, Mn 18.49; when the active magnesium oxide slurry added, the composition of the liquid after precipitation is (g/L): Ni 0.007, Co 0.017, Mn 3.54, liquid meter precipitation rate (%): Ni 96.81, Co 95.23, Mn 14.83. It can be seen that the addition of activated magnesium oxide after slurries, nickel, cobalt precipitation rate has a greater increase, this is due to the slurries after the activated magnesium oxide in the reaction process of rapid diffusion of the results. Adding 2 times the theoretical amount of magnesium oxide after slurring, the precipitation rate of nickel and cobalt liquid meter was 96.81% and 95.23%, respectively.
2.3 Effect of temperature
Fixed conditions: 2 times the theoretical amount of magnesium oxide was added after slurrying, the reaction time was 4 h. The results of the effect of temperature on precipitation are shown in Figure 2.
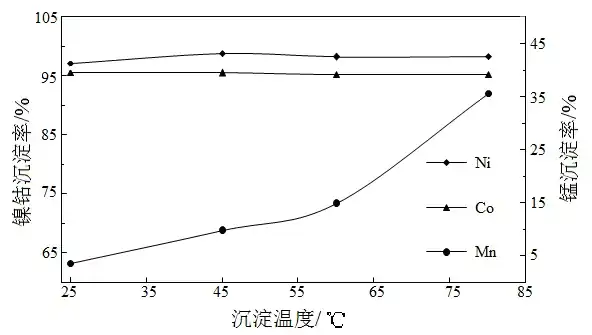
Fig.2 Effect of temperature on precipitation
As can be seen from Fig. 2, the precipitation rate of manganese in the solution increases rapidly with the increase of temperature, but the temperature does not have much effect on the precipitation rate of nickel and cobalt, so it is sufficient to use 25 ℃ precipitation at room temperature.
2.4 Effect of reaction time
Fixed conditions: 2 times the theoretical amount of magnesium oxide was added after slurrying, the precipitation temperature was 25 ℃, and the results of different reaction residence times are shown in Fig. 3.
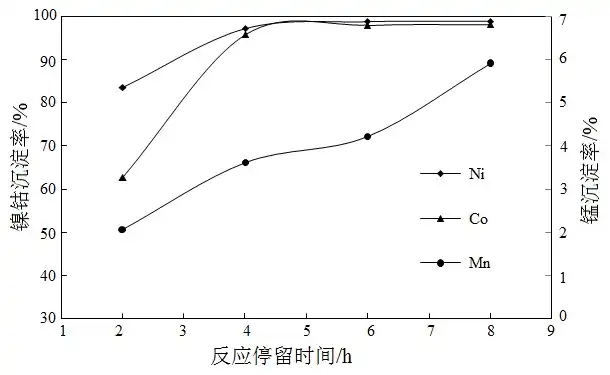
Fig.3 Effect of reactive time on precipitation
Figure 3 shows that the time for complete precipitation of nickel and cobalt is about 4 h and 6 h, respectively, and the manganese precipitation rate increases with the increase of precipitation time. For comprehensive consideration, the reaction residence time was chosen to be 6 h.
2.5 Comprehensive condition test
Combining the results of the above conditions test, the optimal conditions for selective precipitation of nickel and cobalt from the sulfate medium solution containing manganese and magnesium are as follows: adding 2 times the theoretical amount of activated magnesium oxide after slurrying, precipitation residence time of 6 h, and precipitation temperature of 25 ℃. When the solution composition is (g/L): Ni 0.22, Co 0.36, Mn 1.15, the above optimal conditions were used for the comprehensive condition test, the precipitation composition is (%): Ni 8.51, Co 13.05, Mn 2.29, MgO 4.97. The liquid-meter precipitation rates of nickel, cobalt and manganese were 97.96%, 96.43% and 4.22%, respectively.
The results of the comprehensive condition test show that the content of manganese and magnesium in the precipitation enrichment is low, which is favorable for the subsequent acid dissolution-purification-refining process of nickel and cobalt.
2.6 Sedimentation tests
Because the concentration of precipitated nickel and cobalt slurry is very low (0.28%), it is inconvenient to use direct filtration for liquid-solid separation, and it must be thickened before filtration. The following comprehensive test precipitated nickel, cobalt slurry is taken for the static settlement test to investigate the thickening performance of the slurry.
The true density of nickel and cobalt precipitation is 2.72 g/cm3 , and the density of the liquid after nickel and cobalt precipitation is 1.01 g/cm3 .
Static settlement test method: take 1 000 mL of comprehensive test nickel, cobalt precipitation slurry, pour it into the static concentration settlement tester, take 0.2 mL of AN905 flocculant with mass concentration of 0.1% to join the slurry, mix it sufficiently and then carry out the settlement test, record the height of the solid material settling at different time points and calculate its average settling speed, and the results of the test are shown in Fig. 4.
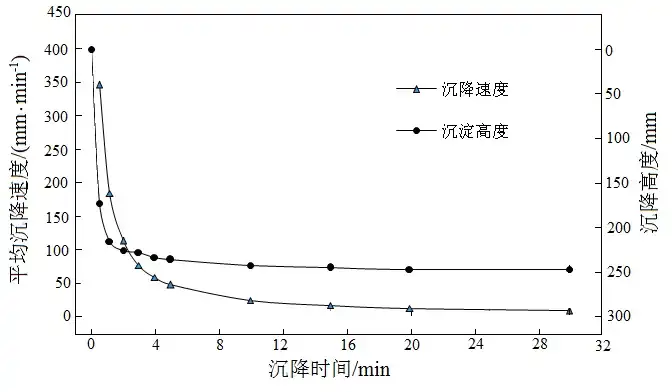
Fig.4 Results of static-state precipitation of slurry
The data in Fig. 4 show that the solid-phase settling rate is very fast after adding flocculant and mixing sufficiently. The maximum free settling rate of nickel and cobalt precipitation is 345 mm/min, and the average free settling rate is 180 mm/min. 1 min or so solid-phase settling is completed, and the slurry enters the compaction stage, and the static thick underflow concentration is 10%, and the thicker underflow slurry after thickening is conducive to the depth of filtration and dewatering.
3 Conclusion
(1) The optimal conditions for selective precipitation of nickel and cobalt enrichment from manganese and magnesium-containing sulfate media by activated magnesium oxide were as follows: 2 times the theoretical amount of activated magnesium oxide was added after slurrying, the reaction residence time was 6 h, and the precipitation temperature was 25 ℃. Under these conditions, the precipitation rates of nickel and cobalt liquid meter were 97.96% and 96.43%, and the contents of nickel, cobalt, manganese and magnesium oxide in the precipitates were 8.51%, 13.05%, 2.29% and 4.97%, respectively.
(2) After adding 0.2 g of AN905 flocculant to each cubic meter of nickel and cobalt precipitation slurry, the maximum free settling velocity of nickel and cobalt precipitation is 345 mm/min, and the average free settling velocity is 180 mm/min, which is fast in solid-phase settling and conducive to the subsequent liquid-solid separation.