Article Description
Sulfuric acid produced during Microbiologically Induced Corrosion (MIC) is responsible for the attack of metallic structures such as pumps, valves, ladders, etc. in most wastewater transport piping systems. Based on this problem, Prof. Anastasios Zouboulis’ team from the University of Aristotle published an article in the journal Construction Materials, in which seven magnesium hydroxide and one magnesium oxide materials were selected to be used as protective coatings on the surfaces of stainless steel and soft steel specimens, while the samples were subjected to an accelerated sulphuric acid spraying test, combining optical At the same time, during the accelerated sulfuric acid spraying test on the samples, optical observation, mass measurement and electrochemical impedance spectroscopy were combined to study the corrosion resistance of the samples, and the results of the study are of practical significance to significantly improve the corrosion resistance of the steel substrate in the sewage pipeline system.
Research Process
In this study, eight coating raw materials (seven of them were magnesium hydroxide powders with different specific surface areas and MgO contents; one was magnesium oxide powder. The eight raw materials (seven of them were magnesium hydroxide powders with different specific surface areas and MgO contents, and one was magnesium oxide powder, labeled C1 to C8) were applied on 4.8 cm × 1.5 cm × 0.2 cm stainless steel 316 and hot-rolled mild steel, and the coatings were made on steel substrates under different hydration times and hydration agent conditions (Fig. 1). 0.4 wt % of methyl cellulose and a common dispersant polymer were also added to enhance the adhesion of the coating on the surface of the steel specimen and to improve the dispersion stability, and processability of the coating. Finally, the authors applied the coatings to the steel substrate surface with a spatula, dried for 3 days, and then performed sulfuric acid spray tests (simulating the environment of sewage pipelines), as well as investigated the corrosion protection properties of the samples by a combination of optical observations, mass measurements, and electrochemical impedance spectroscopy.
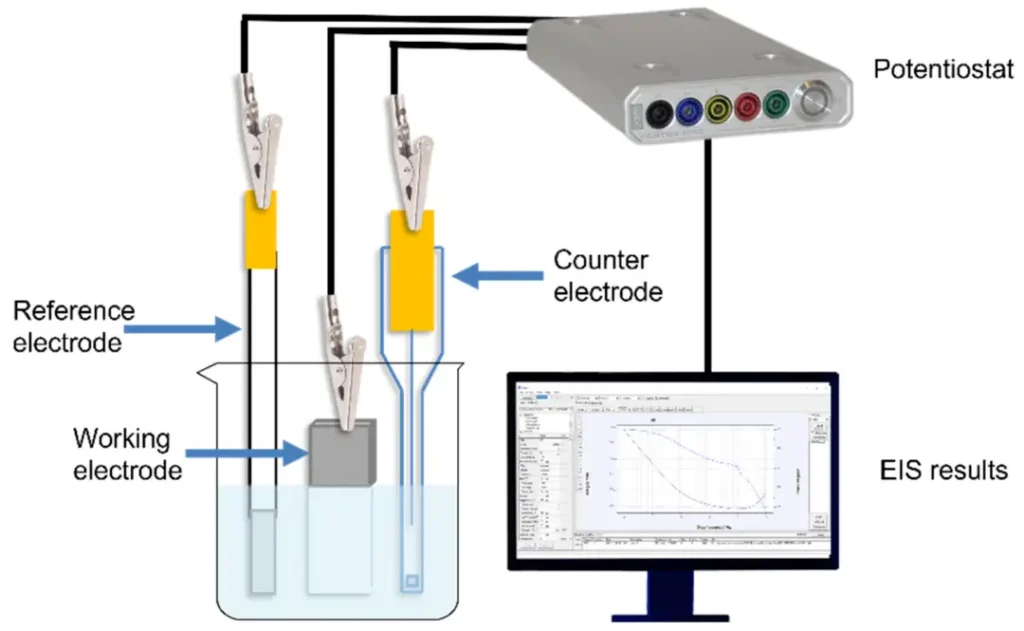
Results of the study
Figure 2 shows the optical observation images of soft steel samples with and without coatings after 4 days of sulfuric acid spray test, and the protective effect of coatings can be observed optically; Figure 3 shows the optical observation images of stainless steel samples with and without coatings after 4 days of sulfuric acid spray test. The results show that optical observation of the surface corrosion of coated and uncoated steel substrates can be used to visualize and compare the difference in corrosion of soft steel samples, but since stainless steel samples are not susceptible to corrosion themselves, the conclusions drawn from optical observation alone are not sufficiently reliable.
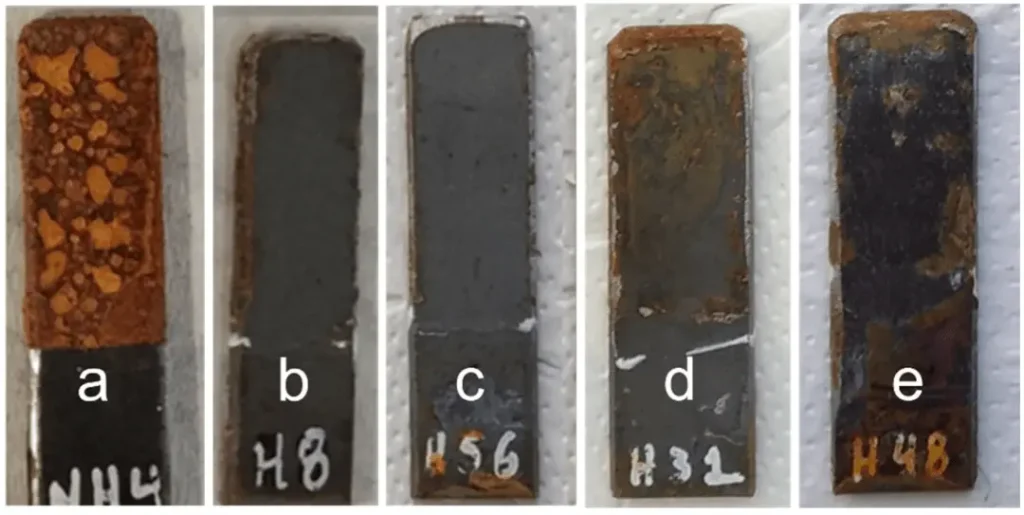
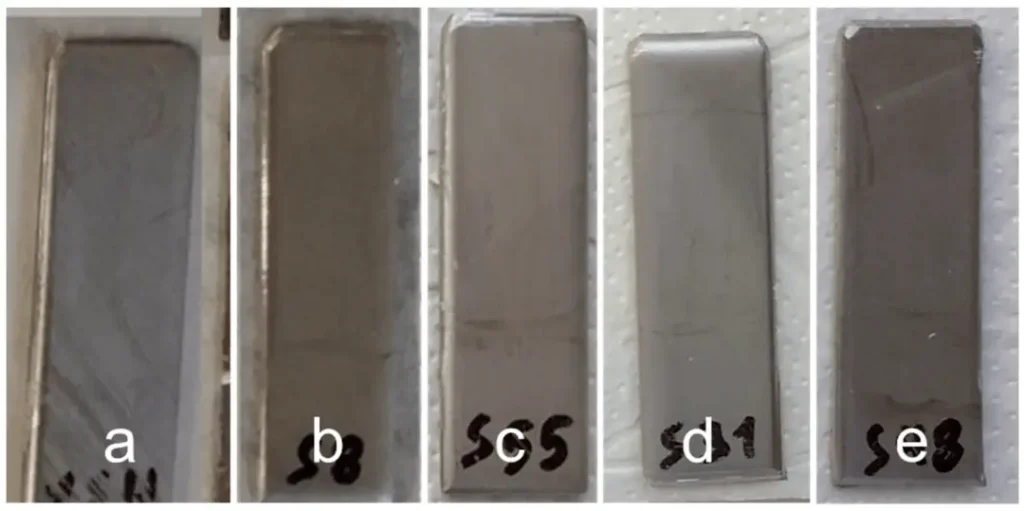
The difference in sample mass before and after the sulfuric acid spray test is an important indication of the degree of corrosion. As shown in Figure 4, the mass of the stainless steel samples remained constant before and after the sulfuric acid injection test, but this may indicate that the sulfuric acid is difficult to corrode both coated and uncoated stainless steel samples, and therefore it is not possible to distinguish the protective effect of the different coatings. However, in the soft steel samples (Figure 5), the mass of the samples varied considerably, with the mass of the uncoated samples decreasing by at least 1% relative to the initial value, and the mass of the soft steel samples remaining constant except for the C4 coating, suggesting that the C4 coating was less protective.
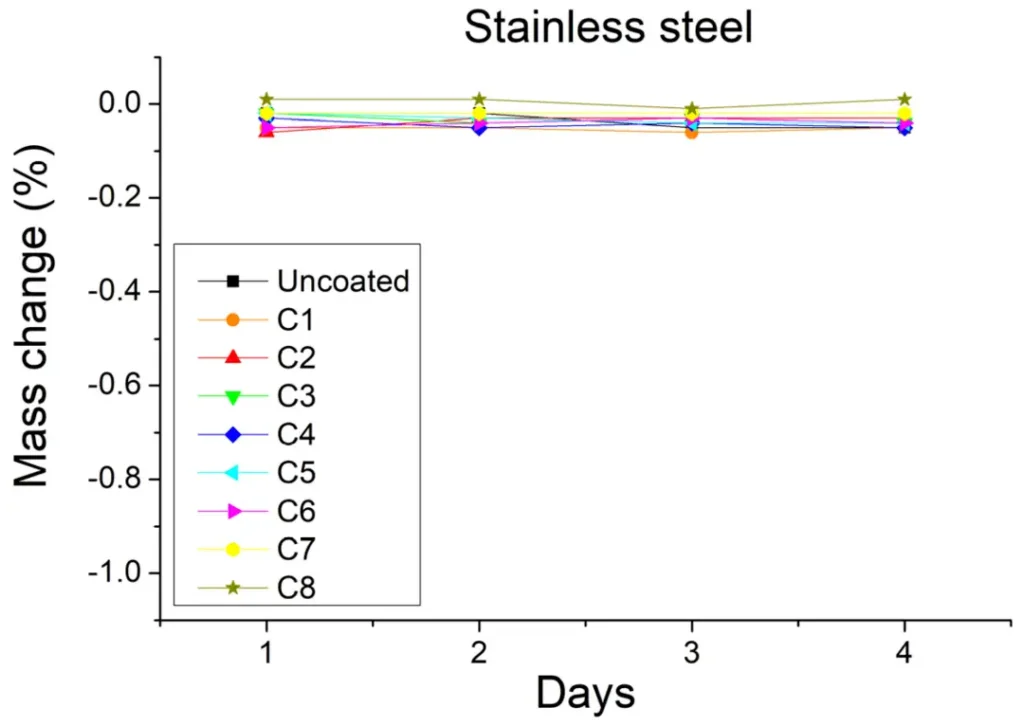
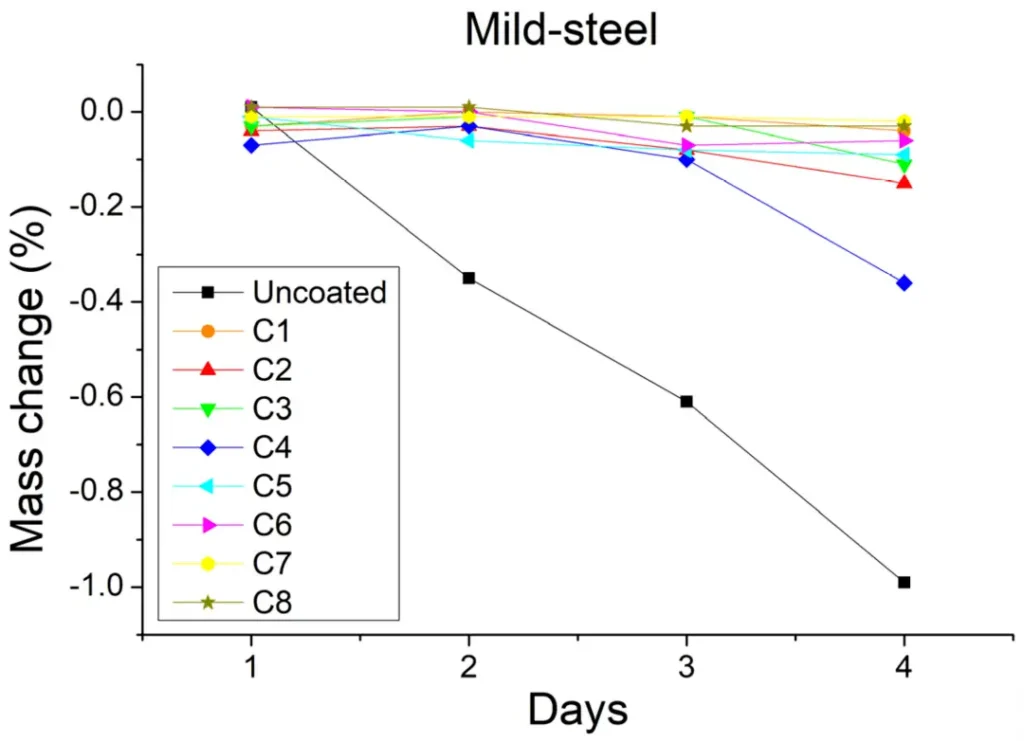
The authors also used electrochemical impedance spectroscopy tests to investigate the corrosion resistance of steel substrates with and without coatings. Figures 6 and 7 show the Bode plots for stainless steel and soft steel samples, respectively. The phase angle of the coated samples increases relative to the uncoated samples, indicating that the coatings have a protective effect on the steel matrix. The results show that the C6- and C7-coated samples have higher impedance modulus at lower frequencies and have higher corrosion resistance.
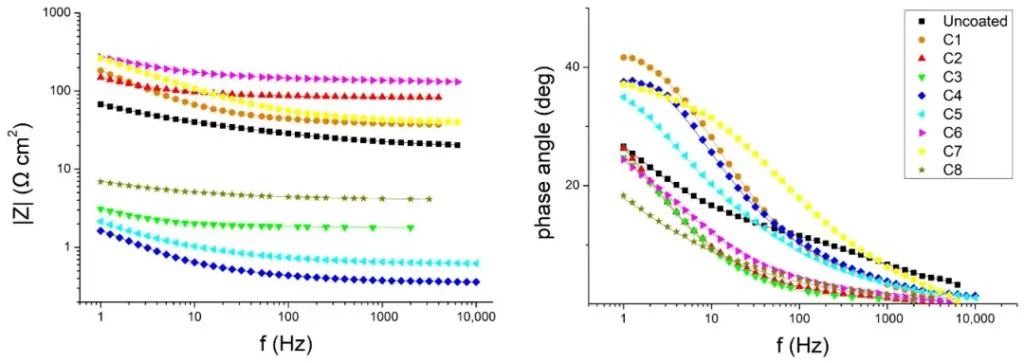
Conclusion
In the study, seven magnesium hydroxide and one magnesium oxide materials were used to prepare coatings on stainless steel and soft steel samples, respectively, and the sulfuric acid spray test was used to simulate the environment of wastewater conveyance pipelines to investigate the protective effects of different coatings on the steel substrate. The experimental results of optical observation and mass measurement illustrate that the stainless steel material has better corrosion protection, while the soft steel material has poorer corrosion protection; moreover, all the coatings, except the C4 coating, have better corrosion protection. The results of electrochemical impedance tests show that the C6 coating is the best coating that produces satisfactory results for both steels and protects the steel substrate better. Since the C6 coatings are mainly prepared using magnesium hydroxide powders with low specific surface area and small particle size, it shows that magnesium hydroxide powders with such characteristics can improve the corrosion protection of steel substrates substantially.